June 2013, Vol. 68, No. 6
Features
Rain, Flood, Contaminated Soils Can’t Stop Gator Drilling
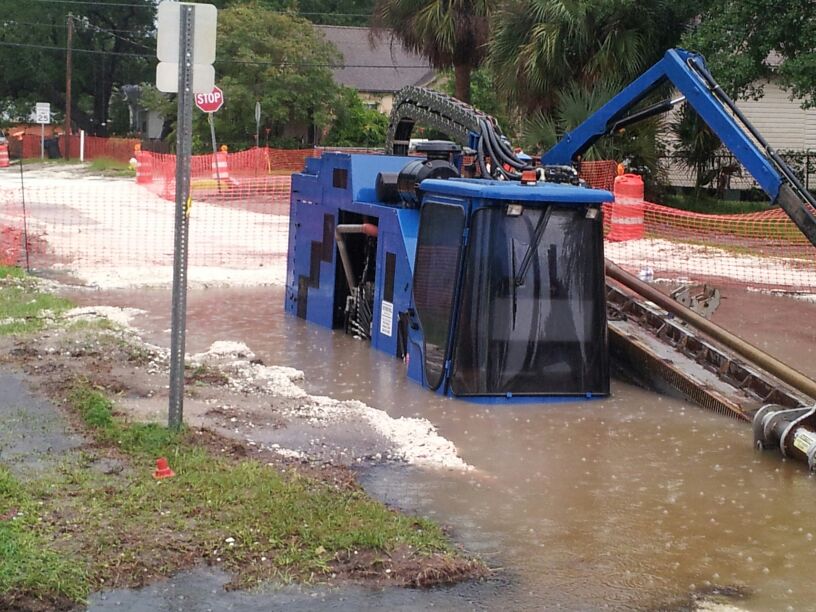
Horizontal directional drilling (HDD) continues to solve problems for utility owners and operators by completing difficult installations of underground infrastructure that many times can be addressed by no other method of construction.
Very often, environmental factors are involved in the decision to use directional drilling. A good example is a Florida project when the city of Pensacola faced the challenge of constructing storm water structures and relocating storm outflow lines which passed through a plume of contaminated soil related to a U.S. Environmental Protection Agency (EPA) Super Fund project. The contamination was left by a creosote plant that operated from 1902 to 1981 and released volatile organic compounds into the soil.
The outflow lines carry storm water into Pensacola Bay. The EPA prohibited the pipes from being buried by open-cut construction because of the high level of contaminated ground water. Excavation would require extensive groundwater de-watering of the contaminated area and no nearby treatment facility could accept such a high volume of pumped groundwater for treatment and disposal of contaminants. Pensacola City Engineer Derrik Owens discussed the feasibility of using directional drilling on the project with EPA and representatives of Pensacola contractor Gator Boing & Trenching Inc.
Ultimately HDD was chosen as the most viable option for installing the conveyance pipes because the process would result in lower volume of returns which could be quantified, containerized and disposed of properly.
Roads Inc. was prime contractor for the project. “Finding a good HDD subcontractor was key to building this project,” said Robby Williams, Roads vice president. “Gator Boring met all of the project specifications for HAZMAT certification, equipment requirements and gravity experience in on-grade gravity flow pipe installation experience.”
Tight tolerance
The project called for installing three, parallel, 26-inch diameters HDPE pipes with four feet of cover and two feet of separation between the pipes. The fall in grade of the pipes was precisely 0.28 percent.
“This was a very challenging situation that required us to apply technology that is not typically utilized for this type of application,” said the city’s Owens.
Gator Boring used a 160,000-pound pullback Universal HDD 160×240 drill model for the installations. Pilot holes were drilled with an 8.75 Radius HDD rock head through sandy clay.
“Because of the shallow elevation of the pipes, the drill unit was placed in a pit to launch the pilot bores,” said Eric Lyons, Gator vice president. “That made it easier to keep bends out of the pipe and hit the target. The bores terminated in a prefabricated junction box.”
A pit 20-feet wide, 30-feet long and three-feet deep was dug in the middle of a road and the drill unit lowered in and positioned for the first bore. The road is not usually heavily traveled, but it provides access to two event centers so construction had to be scheduled to mitigate impact during scheduled events.
All three bores were launched from the pit. Pilot holes were tracked and kept on grade using a DigiTrak Eclipse tracking system.
“We collected all drilling fluid returns with our 3,000 gallon LMT vac truck and a 3,000 gallon Vac King tanker and disposed of it under the direction of the EPA,” Lyons said. “Coordination with the Superfund site manager determined timing, entry locations, disposal locations and flow rates and volumes. When fluid disposal was complete, equipment was decontaminated.”
Minimal reaming
Pipe was laid out in a vacant lot and fused with a McElroy T900 machine. Each pipe string was then positioned in the road for pullback after each pilot hole was completed. Because grade was critical, holes were not backreamed prior to product installation. One reaming pass was made with an in-house reamer and pipe pulled in behind it.
The first pipe was installed over a four-day period. The second installation took longer – almost five days.
Then the weather brought an unpleasant surprise: heavy rains caused flash flooding and water in the starting pit rose to within inches of vital engine components of the Universal drill rig. Waters receded the following day, and the rig was up and running again on the final 400-foot bore. The third installation also required five days.
Start to finish, the HDD portion of the project took just over four weeks. Once pipe was in the ground, the prime contractor made connections.
In addition to 160,000 pounds of pullback, the Universal 160×240 drill rig used on the project develops maximum torque of 23,800 foot pounds of torque and has maximum spindle torque of 160 rpm. It is powered by a 350-horsepower turbo diesel engine and has double rack and pinion drive and onboard crane.
The Eclipse tracking system displays drill head location and locate points in real-time. It is well suited for on-grade installations, said Lyons.
“In spite of the challenging nature and accuracy requirements of the bores,” he explained, “Gator Boring felt that the bore was well within the capabilities of DigiTrak Eclipse locating system. Sewer grade (0.1% pitch resolution) transmitters are a standard feature and Gator Boring employed the locating feature called target steering to maintain proper separation between the three installed pipes.”
Initially, a MGS wireline method was considered for the project. “However,” Lyons explained, “there were too many limitations for this type of guidance. The walkover system allowed the elevation to be field verified at random locations at the directional foreman’s request.”
Experience in on-grade drilling and having previously worked in contaminated soils were factors that contributed to Gator’s successfully completing the Pensacola job.
“We’ve been boring to grade since 2001,” said Lyons. “At that time, tracking equipment was not very accurate or user friendly and we often used a laser level. Today we use the Eclipse F2 and F5 and have our own proprietary program that lets us check top elevation and determine what the depth and pitch reading should be to maintain grade.”
HAZMAT benefits
Gator has maintained a HAZMAT certified crew since 2008. The company is one of a few drilling contractors currently installing horizontal remediation by directional drilling.
In the early 1990s, many in the industry believed HDD-installed remediation wells offered several advantages over the vertical wells sunk through plumes of contamination to remediate underground soils, and was perceived by some to be a new market with great potential for HDD specialists. However, a boom in HDD remediation work never occurred.
“Remediation work is a small part of our business,” said Lyons. “We often work with engineers explaining what the method can and can’t do, and we do two or three jobs a year. However, once personnel have completed the 40-hour HAZMAT training certification, it makes sense for them to do the annual eight-hour training so we are prepared for jobs that require a HAZMAT crew.”
Gator Boring is a third-generation, family owned company that specializes in directional drilling primarily for water, sewer and natural gas construction. The company operates on a national basis with recent projects completed in Florida, Alabama, Mississippi, Louisiana, Arkansas, Georgia, Virginia and Tennessee.
The company currently operates the Universal 160×240, Universal 60×70 and a Universal 24×40; a Vermeer DD-330×500 and a Ditch Witch JT920.
This equipment provides the capability of making directional drilling installations from service lines to river crossings of several thousand feet of HDPE, ductile iron, steel, PVC and PFPVC duct and pipe from one-half inch to 48-inches in diameter.
In addition to HDD operations, Gator provides auger boring, pipe fusion and utility mapping services.
Looking back at the Pensacola project, Lyons said building the project for the community and working with other contractors and suppliers was a “great experience.”
Concluded Pensacola’s Derrik Owens: “This was a successful project that benefits everyone.”
FOR MORE INFO:
Gator Boring & Trenching, (877) 64GATOR, http://gatorboring.com
Digital Control Inc., (800) 288-3610, www.digital-control.com
Universal HDD, (847)955 0050, http://unihdd.com/
Ditch Witch, (800) 654-6481, www.ditchwitch.com
Vermeer Corp., (888) 837-6337, www.vermeer.com
Radius HDD Tools, (800) 892-9114, www.radiushdd.com
McElroy Manufacturing, (918) 836-8611, www.mcelroy.com
Comments