January 2013, Vol. 68, No. 1
Features
Large Rig Market Profiles: Carving A Niche In Rock
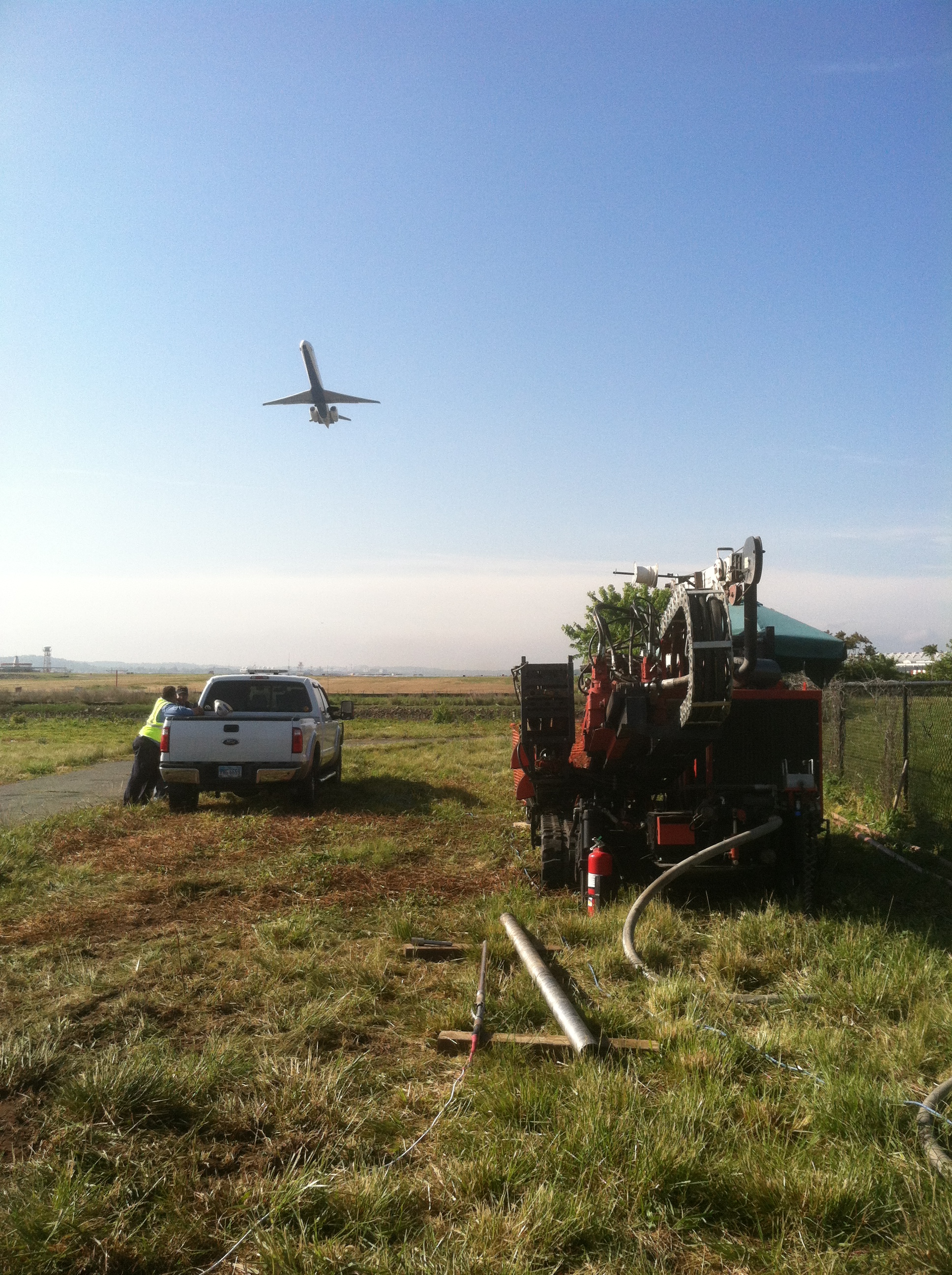
Editor’s Note: Large directional drilling, largely due to the strong shale oil and gas market, has experienced a major boom in popularity. This is the second article in an occasional series profiling the contractors tackling this rewarding – yet extremely challenging – large rig market.
Ohio-based H&H Enterprises is a directional drilling contractor specializing in making difficult installations, most of them in hard rock.
These days, much of the company’s work is in energy shale fields of the Northeastern United States, making road, river and stream crossings on segments of pipeline routes where open-cut construction is not feasible or practical, says Jason Hockran, H&H vice-president/owner.
H&H crews operate two American Auger drill units, each with 200,000-pounds of pullback, and one 90,000-pound machine rebuilt to custom specifications by Underground Professionals Inc.
“Ninety-nine percent of our drilling is in rock,” says Hockran. “By choice, we do very little dirt work. We have positioned ourselves in a niche market to do installations that are beyond the capabilities of many drillers. Contractors working in the Northeast U.S., where most of our projects are located, must understand and be prepared for difficult geological formations, or they will be in trouble.”
Established in 1994, H&H started out primarily doing directional drilling for telecommunications work using 24,000-pound pullback equipment. However, before the 2000 telecom bust, the company had made a transition to natural gas, water and sewer pipeline construction.
“We had two 60,000-pound machines and saw HDD beginning to be applied to the public utilities market, also including gas,” Hockran explains. “The change from telecom was more a business decision to expand to other areas, than anticipating the sudden drop in telecom construction. Our business model is to be adaptable and apply what we know to market demands and effectively manage and control our operations.”
The transition away from telecom and installing larger-diameter product put H&H in an excellent position to be a part of the construction boom in the energy shale fields in the Northeastern United States.
Energy pipeline construction in the Northeast is more complicated than in other parts of the country, Hockran observes.
“Directional drilling plays a more significant role in pipeline construction in the Northeast more than in other areas,” he says. “In the Midwest, for example, most pipeline construction is in open country where big trenchers can go for miles without stopping. The Northeast is very different: regulations are very strict about where trenching is permitted and when it is prohibited. All road crossings have to be drilled or auger bored, and the geography creates a demand for HDD; auger boring sometimes is complicated because of changes in elevations. HDD simply is the only way many segments can be completed.”
Hockran says H&H jobs in the energy shale typically involve making two or three bores in a five to 10 mile segment of a pipeline route. The drill unit is set up on the low side of a road or river, drills under the obstacle and up the side of a hill or mountain where excavation can resume. Drills often are to depths of 50 to 150-feet, too deep for walkover trackers. Mud motors are used to go through shale and other rock, and wireline systems are used to guide the bore path.
A recent project southwest of Pittsburgh, PA, to install a segment of 16-inch diameter steel gas transmission pipe is typical of H&H energy projects. An American Augers DD220 with a mud motor was used to drill through solid shale and sandstone.
“The bore was 1,700 feet long under wetlands, a creek and up to an exit on the side of a mountain where it tied into pipe in a trench,” says Hockran. “The 8 3/4-inch pilot hole was enlarged in two passes with 20- and 26-inch hole-openers. Average depth below the surface was 60 feet. It took 10 days to complete the pilot hole. While drilling was under way, pipe was assembled along the right-of-way.”
Hockran says that in H&H’s experience, mud motors and conventional hole openers consistently work very well in rock found in the Northeastern U.S.
“We believe it is best for companies to purchase mud motors that drill in rock most of the time. We own and operate Adtech motors, but at times rent as needed,” he says. “We use a ParaTrack II magnetic tracking system from Prime Horizontal; we own and operate our own steering equipment.”
For rock drilling without a mud motor, Hockran considers the two primary options: conventional heads with TCI inserts and air hammers.
“Conventional TCI drill heads are effective in rock formations of less than 15,000 psi,” says Hockran. “Harder rock decreases the ability to steer effectively and reduces production. These drill heads are excellent for gravel and unconsolidated rock formations as they will not wear out as quickly as a standard ‘dirt’ drill head.
“Air hammers are increasingly becoming a more popular alternative in the HDD rock drilling market. They are very effective for drilling plus-or-minus 6-inch pilot holes in hard rock more than 15,000 psi. In certain very hard rock exceeding 25,000 psi., an air hammer will be more effective and efficient than a mud motor. A limitation with air hammers is that steering is not very effective in unconsolidated formations, and it is sometimes difficult to keep the drilled hole clean. However hole-opening capabilities of hammers are very limited and in our experience are less efficient and effective than traditional hole openers that operate with fluid.”
Hockran emphasizes that effectiveness of the various methods depends of project conditions and that no single tool or method is suited for every type of rock drilling.
While projects in energy shale currently dominate H&H’s workload, Hockran makes clear the company’s versatility is important and bids for new work are not limited to the energy field.
An impressive non-energy project in 2012 was crossing the Potomac River and boring under adjacent wetlands in Washington, D.C.
“The eight-inch diameter pilot bore under the river was 5,000 feet long to install fiber optic cable,” Hockran says. “We set up the 210,000-pound pullback DD210 drill about 200-feet from the bank of the river, drilled down and then under the river bed. The depth was about 100 feet below the river bottom. The project owners didn’t want to take any chance that the cable could be disturbed by dredging or any other activity that might occur.”
Crossing rivers with pipe and cable in this area almost always are made by HDD, Hockran added. State departments of transportation limit suspending cables and pipes from bridges, and excavation typically is not an option.
“The river crossing was a ‘drill-and-leave’ job with drill pipe left in place to be duct for the cable,” says Hockran. “Therefore, no pullback was necessary.
Two drills were made in wetlands to the river with the Underground Professionals 90,000-pound SS-90 machine. Pilot holes were seven-inches in diameter and enlarged by an 18-inch hole opener. Depths under the wetlands reached 50 feet. Multiple bundles of four-inch HDPE pipe were installed to accommodate various fiber optic communications lines. Subsurface conditions were sandy silt formations with some rock. Mud motors were used on all bores.
H&H has remained successful throughout up-and-down business cycles and is quick to adjust to market changes. One of the keys to being adaptable and proactive to market changes is quality employees, Hockran believes.
“One of our greatest employee partners is Operations Manager Scott Kilgore,” Hockran says. “Scott has been with H&H for almost eight years, and his personal, relatable and professionally-responsible approach to customer and project relationships are crucial for our continued success. It is through quality individuals like Scott and our other professional employee partners that we continue to succeed.”
Hockran says company management and employees strive to be a business that is lean and adaptable.
“Workloads ebb and flow and our range of experience helps us when slow times come,” Hockran says. “As demand for our services has grown, we have allocated capital to be able to meet demands, and we don’t compromise our principles for maintaining quality work consistent with the high standards we set for ourselves.
“Proper planning and contingency plans are the most important steps in minimizing mistakes or unknown obstacles for successfully completing a project. The number one thing that keeps us in business is quality relationships with our customers, and those are built and sustained over time.”
H&H Enterprises is based in Andover, OH and maintains a branch in Bemus Point, NY.
FOR MORE INFO:
H & H Enterprises Inc., (440) 293-8911, www.handhent.com
American Augers, (800) 324-4930, www.americanaugers.com
Underground Professionals Inc., (419) 282-6400, http://undergroundprofessionals.com
Prime Horizontal, (570) 675-0901, www.prime-horizontal.com
Comments