United Rentals Provides Tips to Keep Equipment Running Smoothly During Summer
Summer heat can be physically stressful not just for construction workers but also for equipment. Increased temperatures, along with longer work days, intensify the wear and tear on construction equipment. United Rentals, Inc. shared tips on maintenance best practices to help keep excavators, trucks, loaders and other equipment running smoothly and productively on worksites.
“Keeping equipment running requires an organized approach of daily and long-term maintenance activities that emphasize operating life and safety,” said Bret Kasubke, director of customer equipment solutions at United Rentals. “Contractors need to adapt equipment maintenance to the seasons. Tailoring actions to the specialized needs of equipment during the summer can help contractors protect workers and maximize productivity during this peak construction period.”
Daily Inspection Tips
Daily inspections are an essential element of effective maintenance programs. During summertime, contractors should especially look for these issues.
Coolant and oil. In summer, engines get hot and thirsty. Daily maintenance checks should ensure the machine has the proper coolant level, coolant/water ratio and oil levels recommended by the manufacturer. Radiators must run totally full to prevent oxygen from entering the cooling system.
Grease. Hot temperatures reduce the adhesive properties of grease, so use thicker grease. Consult the equipment manual to find what type of grease is best for the machine, where to grease and how often. Keep in mind grease can get “squeezed out” during heavy operations like earthmoving or drilling. When dust and silt mix with grease, it increases wear and tear on the equipment, so clean equipment regularly.
Belts and hoses. Discolored hoses and loose belts offer the first hint of overheating, so be sure to inspect them.
Hydraulic system and air filters. During an equipment walk-around, check for signs of possible hydraulic leaks, excess oil and grease, leaks around seals and loose bolts. Also give the air filters a look-over.
Tires. Hot conditions weaken tires and may cause a blowout. Check tire pressure regularly. Tire pressure increases with the temperature, which can lead to over-inflation. On the flip side, an underinflated tire heats up more quickly.
Be sure to check the brakes. Steamy summers can cause the loss of brake friction because the brake components cannot absorb the additional heat.
Cooling system. Summer working conditions require maximum airflow through the oil cooler. Check that the radiators, and inlets and outlets of the cooling system are free of debris. Accumulated dust that cakes can clog a cooling system, so use compressed air daily to clean it.
Scheduled Maintenance Tips
Along with conducting daily inspections, contractors should set a schedule for a deeper maintenance routine. Whether working with excavators, wheeled or skid steer loaders or other equipment, scheduled maintenance routines need to cover hydraulic and engine oil levels, transmission oil, radiator coolant, tire treads, battery, brakes and many other check-list items.
Make sure the coolant matches the manufacturer’s specifications. Older equipment may use a silica-based coolant. Newer equipment usually includes a tag near the coolant filler that indicates the use of an organic acid technology (OAT) coolant. Anti-freeze used in summer must have a higher boiling point to prevent cooling water from boiling.
Clean and check seals, filters and breathers because dry, windy summer days can push dust and contaminants into equipment systems. Check the transmission, pistons, bearings and major assemblies for signs of wear or lubricant build-up.
Many times, manufacturers specify the replacement of parts at certain intervals for equipment used in hot environments. Use software calendaring tools to schedule maintenance and use a log to document part replacements as well as lubrication and repairs.
Maintenance is part of an even larger fleet management strategy. Outsourcing to an equipment maintenance service provider that specializes in equipment repair and service in the field and onsite can protect a contractor’s equipment investment. These services safeguard employees by helping ensure equipment is expertly inspected, maintained and repaired. They can help contractors address ANSI, OSHA and CSA requirements.
“Maintaining equipment fleet is not easy. Working with an equipment maintenance service provider allows contractors to set up a proactive, automated program of preventive maintenance and inspections customized to their specific needs. An effective maintenance program positions contractors to extract maximum value from their fleet,” said Kasubke.
Related News
From Archive
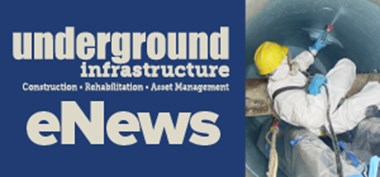
- Trench collapse kills one construction worker in Houston, Texas
- Intrepid Fiber breaks ground on fiber optic network in Superior, Colo.
- Excavator collides with I-95 overpass in Henrico, Va., causing multi-vehicle crash
- Shrewsbury, Mass., expands sewer inspections and cleaning efforts
- Construction worker killed in trench collapse near Prosperity, S.C.
- Final construction phase kicks off for Indianapolis deep rock tunnel
- Texas contractor penalized by OSHA for repeated trench safety violations
- Trench collapse kills one construction worker in Houston, Texas
- WES tunnel boring machine retrieved from Oregon river after seven-month project
- Illinois overhauls Peoples Gas pipeline program, mandates focus on high-risk pipes
Comments