Intersect HDD Gets Better with Experience
By Jeff Griffin, Senior Editor
An “intersect” project may be the most complex application in horizontal directional drilling (HDD).
Two pilot holes – one at each end of the projected bore path – meet somewhere in between to make a single pilot hole for pulling in the product. Each segment usually is long, and diameter of the pipe being installed is larger. The intersects’ point of connection may be under a river or larger body of water.
For the two bore paths to intersect takes meticulous planning and precise execution. While, today, an intersect project is not uncommon, not many contractors have the equipment and capabilities to undertake an intersect project and the challenges it presents.
Early days
The first successful pilot hole intersect was completed in 2003 by Michels Directional Crossings for a segment of Maritimes and Northeast Duke Energy Hub-Line Project in Boston. The Georges Island HDD crossing a was 5,174-foot-long, hard-rock, water-to-water crossing to install 30-inch diameter pipe.
Lengths of intersects and diameters of product installed have steadily increased in the years since the first intersect installation.
Underground Construction queried representatives from three veteran HDD contractors with several successful intersect projects on their resumes about this challenging method of underground construction.
Michels Directional Crossings, Jeffrey S. Mueller, vice president
Intersects have become common in the HDD industry and are used for a variety of reasons to minimize risk and increase productivity.
Various circumstances lead us to consider pilot hole intersects instead of single bore. The most obvious one is length. Depending on diameter of the pipe and the geological conditions, at a certain point even the most powerful rig would not have the horsepower needed to provide the thrust and rotary torque required to cross the entire span.
Other factors are the anticipated annular pressure of drilling fluid required to remove the cuttings, right-of-way considerations and time frames. If timing is tight, it theoretically takes less time for two rigs to drill from opposite sides of a project and meet in the middle than it would for one rig to complete the entire drill. Right-of-way restrictions determine where the product pipe is staged and assembled for pullback.
As with all HDD projects, accuracy and attention to details are critical to pilot-hole intersect projects. With two rigs drilling from opposite sides, tracking tools are important to ensure each rig stays on the predetermined alignment. Severe pilot-hole misalignment can cause tool failure, or the product pipe to become lodged due to inappropriate radii through the intersect transition.
Typically, a tangent section of the bore, rather than a mid-point, is selected as the location of an intersection. As technology has advanced in this industry over the past two decades, the point of intersect is not as critical or difficult a decision as it had been in the method’s infancy. The sophistication and skill of those involved in this industry have grown exponentially.
We use a variety of equipment, including surface guidance, magnetic survey instruments and gyroscopic tooling. For most drills, primary and secondary tracking systems are important. Many factors affect our decisions on the best methods and equipment for picking up signals, for and determining the precise position of the drill heads.
Downhole guidance sensors are utilized to align the drill paths, resulting in a successful intersect. Many intersects are completed underwater because HDD is typically done in conditions where traditional or open-cut installations would not be possible – and that is often under water or in other environmentally sensitive areas. The execution of the intersect does not vary based on what is above the location.
Currently Michels’ intersect project count is 206, with the number continuing to go up. The company’s longest HDD pilot-hole intersect HDD to date is the 13,247-foot installation of a 20-inch pipe under Lake Sakakawea and the Missouri River in North Dakota.
Mears Group, Neil Smith, senior vice president, engineering; and Steve Sommerfeld, steering technician manager
Primary factors to consider in determining whether a project could be best accomplished with an intersect include:
- Is it feasible?
- Does the geometric design of the crossing allow for a reasonable place to propose an intersection?
- Would an intersect sufficiently benefit the project?
- Do its benefits outweigh the additional cost incurred to accomplish it?
Generally, the situations appropriate for intersect pilot-hole drilling are crossings that are very long; where using intersect technology will alleviate potential problems concerning excessive annular pressures; where there are adverse geotechnical conditions at both the entry and exit points (often necessitating pre-installation of surface casings); and those with complicated geometries that would make it difficult to maintain directional control, or maintain adequate weight on the bit, with a single pilot drilling operation.
The intersect point is determined after evaluating the geometrical design of the crossing, as well as the subsurface ground formations to be encountered, for the most strategic location that provides the best chance of success. A straight section in the drill and a competent formation are both important considerations.
Guidance technology used depends on the particulars of each situation. We have utilized conventional magnetic guidance tools, gyroscopic tools and a combination of both to accomplish numerous intersects.
A serious risk is that a “dogleg” can occur at the intersect point, which will be detrimental to the reaming and ultimately to the product installation phase of the HDD process. Care needs to be taken to ensure holes are merged together gradually, so they don’t exceed radial design limitations of the product pipe to be installed.
Depending on the type of guidance system selected for the project, once the relational difference between the two opposing pilot holes has been determined, one string is extracted while the other is advanced towards the intersect position. It’s important to steer the advancing string at a merge rate that does not allow it to enter the existing hole at an unacceptable deflection deviation. Once the intersection is accomplished, radius calculations of the merge into the existing hole are analyzed for acceptable tolerances, and the strings are advanced/retracted to pilot hole completion.
Location for the product preparation side is normally determined by available space and right-of-way restrictions. Once the intersection is completed, the reaming rig and pull rig location can be situated at either end, depending on the particulars of each individual site.
To date, Mears has completed 29 HDD intersects. The longest is a 7,400-foot-long crossing for 130V underground pipe/cable crossing the Elizabeth River in Norfolk, Va.
Hard Rock Directional Drilling, Cory Baker, general manager
When applied correctly, the intersect method is one of the greatest tools in the HDD industry. It’s primarily considered because of length and concerns about inadvertent fluid return (IR).
An intersect may be needed to build the section of the exit curve on very long bores when it’s necessary to steer to build the angle in the exit curve, and push at the bit is lost preventing it gaining angle. Therefore, it helps to set up a rig at the exit end to drill the exit curve so the main rig on the entry can follow the exit rig up the exit curve.
The intersect method also helps prevent inadvertent returns. A fracture analysis is used to determine the maximum pressure the soil can handle. Then the drilling contractor can calculate the anticipated annular pressure the soil can handle for the pilot hole. If the pressure goes higher than the maximum allowable – which is a safety factor of two – then an intersect rig is needed to reduce the annular pressure downhole. This is one of the best methods in the industry to reduce IRs.
Before planning an intersect, geo cores should be completed to help decide where to make the intersect. Planning also requires a review of the entire crossing to identify what downhole tools will be used for the soil conditions.
Guidance technology is determined by each crossing’s requirement. Hard Rock has completed intersects with all types of systems and combinations. If the intersect is under a body of water, a system with radar is great – it all depends on the job.
What does not change in all intersect projects is the entry and exit rig. The larger rig will always be at the entry side, so it can complete the reaming and pulling operations. The side with the space to lay out product determines which side is which.
Hard Rock has completed many intersects over the years. The longest to date is 11,265 feet of 10-inch pipe under Clear Lake at Kemah, Texas. Drill rigs of 1 million and 330,000 pounds of pullback were used.
FOR MORE INFORMATION:
Michels Corporation, (920) 924-4300, www.michels.us
Mears Group, (281) 448-2488, mears.net
Hard Rock, 210-403-2086, http://hardrockhdd.com
Related News
From Archive
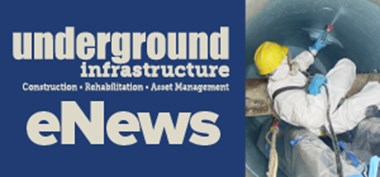
- Trench collapse kills one construction worker in Houston, Texas
- Intrepid Fiber breaks ground on fiber optic network in Superior, Colo.
- Excavator collides with I-95 overpass in Henrico, Va., causing multi-vehicle crash
- Shrewsbury, Mass., expands sewer inspections and cleaning efforts
- Construction worker killed in trench collapse near Prosperity, S.C.
- Final construction phase kicks off for Indianapolis deep rock tunnel
- Texas contractor penalized by OSHA for repeated trench safety violations
- Trench collapse kills one construction worker in Houston, Texas
- WES tunnel boring machine retrieved from Oregon river after seven-month project
- Illinois overhauls Peoples Gas pipeline program, mandates focus on high-risk pipes
Comments