RAPID CITY, S.D. (AP) — Humans create tons of waste. They demand a lot of energy too. That, in essence, is what makes a South Dakota School of Mines & Technology project to convert waste products like cardboard, discarded food and agricultural refuse into methane gas for energy generation so exciting.
South Dakota Mines' Gas Cube Project Holds Big Potential

The Rapid City Journal reports that the Gas Cube, as the Mines’ students working on the project call it, currently rests in a portable, semitrailer-sized reactor. Funding for the program came in the form of a $4.8 million grant from the U.S. Air Force, $1.2 million of which is intended for the Gas Cube as the Air Force seeks ways to save money on waste handling and fuel costs at its remote bases across the world.
So, how does it work? Think of a cow’s stomach, said Jorge Gonzalez-Estrella, a post-doctoral research associate in the Chemical and Biological Engineering Department at Mines, in a news release from the school.
“Our reactor is in some ways a two-stomach cow,” he said. At the cube’s “mouth,” cardboard or food waste is grinded down and deposited into a chamber. In that chamber, microorganisms then break down the grinded waste into sugars followed by fermenting microbes that break down the sugars into smaller parts, called volatile fatty acids.
Next, in a vertical chamber or the cube’s “second stomach,” other microbes turn the volatile fatty acids into methane gas. Any leftover solids are then diverted into a third chamber for additional time for methane producing reactions. In the end, the methane produced from these processes can be piped out to run generators or other equipment needed to power a remote base.
The biggest challenge isn’t creating the methane, researchers say. Rather, it’s making the Gas Cube portable, user-friendly and scaling up its capabilities.
“Usually these things take up acres if they’re industrial. We put it in a 20-by-8-foot space,” said Jim Schultze, a chemical engineer who is helping construct the Gas Cube.
Though the Gas Cube is intended for use by the military, it has a large potential for application across other industries, Mines spokesman Charles Michael Ray notes, including being employed in disaster areas or refugee camps when waste-handling infrastructure is compromised or nonexistent.
It could even be used by local microbreweries, which often face restrictions on dumping their wastewater into municipal sewer systems.
But Dave Litzen, a chemical engineer and president of Litzen Process Consulting, Inc. — who is helping build and test the working prototype — was quick to add in the news release that for now, researchers’ minds aren’t muddled by the prospects of project development meetings over a free pint.
“I can’t think of a better first customer,” Litzen said, “than the Air Force.”
Related News
From Archive
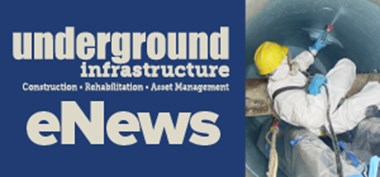
- OSHA cites Florida contractors for trench safety violations at sewer and excavation sites
- Biden-Harris administration invests $849 million in aging water infrastructure, drought resilience
- Texas contractor penalized by OSHA for repeated trench safety violations
- West Virginia approves $67 million for water, sewer projects
- Mark Boyer named 2025 MVP of underground infrastructure industry
Comments