February 2023 Vol. 78 No. 2
Features
Reconstructing Utility Construction: How New Equipment Attachments Address an Infrastructure Crisis
By Lynn Marsh, Road Widener LLC
(UI) — Utility construction is a crucial piece of addressing the infrastructure crisis around the world. The origin of utilities may bring to mind grandiose stories like Thomas Edison failing 1,000 times in his pursuit to invent the lightbulb before succeeding.
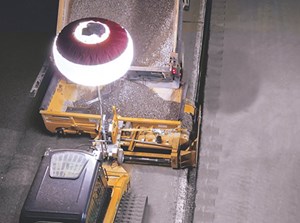
These ideas, while inspiring, are not something utility construction contractors have the time for today. In fact, contractors are being asked to accomplish more work on tighter deadlines, requiring peak efficiency.
Rising demand on infrastructure is steadily exceeding contractors’ capacity to maintain, let alone improve, utility construction. The global utility system construction market grew from $706.06 billion in 2021 to $770.11 billion in 2022 – compound annual growth rate (CAGR) of 9.1 percent. In 2026, the market is predicted to hit $951.7 billion.
It is evident that utility construction is on the rise, but limited budgets require re-evaluation of methods and efficiency to ensure the available funds can stretch far enough. With crews facing a growing backlog of jobs, contractors are looking for ways to get more done with the same amount of time and workers.
However, some worry that learning new technology may result in lost time. That’s where equipment attachments come into play.
Attachments provide a realistic, effective solution by utilizing equipment that contractors are already familiar with. By changing workflow, minimizing maintenance, lowering equipment cost, allowing for smarter labor and increasing ROI, these new attachments are changing the foundational methods of utility construction. Here’s how.
A New Method
Utility construction tasks, such as backfilling trenches, have typically been viewed as a four-step process. Materials are piled up, scraped into place, compacted, and then crews sweep and clean what remains.
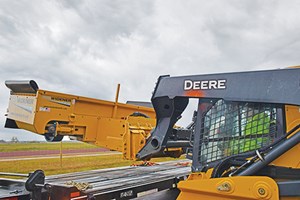
Although larger machines and added crew members can help complete projects, another way is to minimize the number of steps in the process, with the use of material placement attachments. Also reducing labor, these attachments provide safety and efficiency by easily maneuvering around obstacles such as power poles, signs and guardrails.
Material placement attachments take the complex four-step process using expensive equipment and simplify it. A single operator connects the skid steer, loader or other common host machine to the attachment and loads material into the hopper at the top. The operator drives alongside the road as material feeds down the hopper onto a conveyor that carries the material to the edge of the attachment, dispensing it through an adjustable width opening exactly where it’s needed.
Some attachments can even dispense up to 20 tons of aggregate in under 10 minutes, with all machine adjustments made by a single crewmember from inside the host machine via a remote control. To further increase the efficiency of material placement attachments, some manufacturers offer dual and single, left or right side, dispensing configurations to take on numerous projects around the world.
Streamlining the process saves money and makes money. Crews not only can do more work in a day but do more with their budget, by cutting out steps without adding more equipment or workers. And those savings continue into the future, with a drastically lower cost of ownership compared to self-propelled machines.
Traditional self-propelled machines see most of their maintenance downtime and costs from engine, transmission and associated parts repairs. However, attachment efficiency truly shines when considering these profits lost to maintenance.
In an effort to reduce maintenance, material placement attachments can connect to the engine and hydraulics of common, proven workhorses, like skid steers and loaders (wheel and tracked). If a host machine needs to be serviced, crews can quickly and easily hook up the attachment to another machine. Without an engine or transmission of their own to upkeep, these attachments have the power to reduce maintenance by up to 90 percent, with just a few grease fittings to look after.
When considering this type of equipment, look for manufacturers that offer an optional universal mounting plate and easy hydraulic connections for their attachments. Also, you want it to be able to connect to any host machine in a fleet.
An advantage of choosing an attachment with a compact design is less parts to keep track of, and fewer transportation requirements and job-site clutter. Another benefit is the ability to conveniently fit the attachments on the same trailer as the host machine, to be transported to and from job sites.
Reducing maintenance reduces downtime, ultimately providing crews with opportunities to take on more jobs and save money. Saving money during the process pays back an owner throughout the season, but what about out-the-door?
Savings from the get-go
Engines, transmissions and driveshafts. These high-maintenance parts are expensive, but necessary, for job sites. The addition of material placement attachments helps combat expenses by connecting low-cost, essentially maintenance-free hydraulic hookups to a host machine which then powers the attachment.
Cutting out the unnecessary parts slashes prices by up to 80 percent. It also allows contractors to invest in the host machines they know will support their fleet from multiple angles, not just the larger, self-propelled machines that see months of off-season.
And the host machine to power the attachment? These common machines cost pennies on the dollar when compared to dedicated, single-function construction equipment. Not to mention, most contractors probably have multiple machines that would excel as a host machine already in their fleet.
Overall, material placement attachments are low-maintenance and lower cost than self-propelled machines, but also provide savings by repurposing labor.
Remaking utility construction by utilizing attachments reduces unnecessary steps, lessens the amount of equipment needed and drastically lowers maintenance requirements. But crew members don’t await a similar fate. Contractors now have the freedom to assign these crew members to different tasks that benefit the job site, and in times when labor is scarce, this is a vital way to keep getting work done.
The freedom that efficiency provides allows contractors to put crews to work in areas they didn’t have the capacity to work in before and expand their utility construction operations. Contractors report up to 50 percent savings in labor, which could potentially double a crew’s work capacity when using attachments. In addition, labor savings can benefit crews from a safety perspective, as well.
It’s one thing for a machine to go down, but what about a crew member? Utility construction is a high-risk job on the best of days. Crowding numerous crew members around a project site to spread-out materials or make machine adjustments is an unnecessary risk.
However, utilizing attachments that cut out multiple steps in the process takes crewmembers out of harm’s way. Additionally, remote-controlled attachments allow the host machine operator to remain in the cab while adjusting dispensing speed and machine positioning.
The increasing demand for utility construction projects across the world and the limitations of traditional machinery are inspiring equipment innovations. Material placement attachments are proving to be assets not just in times of infrastructure crisis, but for creating a system of sustainable utility construction management.
ABOUT THE AUTHOR: Lynn Marsh is the president of Road Widener LLC and has 20 years of experience in the road construction industry.
Comments