June 2020 Vol. 75 No. 6
Features
Pioneers of HDD Reflect on Hall of Fame Careers
Inaugural Inductees Melsheimer, Cherrington Inexorably Linked in HDD History
By Jeff Awalt, Executive Editor
It would be impossible to describe the advances in horizontal directional drilling during its early development in the 1960s and ’70s without addressing the pioneering work of Richard (Dick) Melsheimer and Martin Cherrington.
From a distance, the leapfrogging accomplishments of the two Californians may appear so closely intertwined as to suggest a carefully choreographed script, as each built upon the engineering feats of the other. Yet, a closer look reveals that nothing could be further from the truth.
In fact, Cherrington and Melsheimer spent most of their careers on opposite ends of the Golden State with unique professional paths, distinct personalities and entirely separate engineering agendas. When their accomplishments are viewed together, however, they tell a story of two maverick inventors who collectively laid out a path for an entire industry.
Dick Melsheimer
Compact Concepts Lay Groundwork for Modern HDD
Dick Melsheimer’s initial concept and experimentation with small directional equipment in Los Angeles paved the way for explosive growth in the small-rig market, powering the first telecom construction boom and laying the foundation for much of the today’s urban HDD activity.
The Los Angeles native was born into the underground construction business, following in the footsteps of his father, Fred, another industry pioneer who founded Melfred Borzall in 1946. Fred is credited with developing the slurry boring process. Dick built on his legacy of innovation after graduating from Cal Poly San Luis Obispo as a mechanical engineer.
After joining the family business in 1961, Dick and his brother, Ted, developed hydraulic-powered drill rigs and patented a self-propelled boring machine known as the Dynamole, which could bore and pull in more than 2,000 feet of polyethylene pipe per day. It marked a significant step forward in HDD development and a big improvement over the air motor-driven cut and bore method.
The air motor cut and bore process developed by Fred Melsheimer, while a definite leap forward when it came into use during the 1950s, was a labor-intensive and treacherous process, Dick recalled during an HDD Pioneers panel discussion at the 2020 Underground Technology Conference.
“That was the first power source for HD drilling, but we didn’t call it that in those days. We just called it horizontal boring,” Melsheimer said, describing a handheld, 3-horsepower motor that required two operators to power 20-foot lengths of drill rod.
“It was a dangerous tool,” he said. “You had a little fish-tailed bit that you’d use for drilling a 2-inch pipe hole, and if that sucker hit a rock or a root, the torque would go over, and if they weren’t holding onto the motor one guy could get a smashed jaw or a broken shoulder.”
Crews would dig a series of potholes in order to sight the drill rod and steer it along its path. “In those days we never knew of such a thing as a frack-out, because you had a pothole every 30 to 50 feet, and that’s where all the fluid went,” Melsheimer recalled. Laborers would dig the holes by hand, starting about an hour before the crew began drilling, “and they would just chase each other down the street.”
Melsheimer started putting in steel distribution lines for natural gas utilities in the Los Angeles area, but when Dupont introduced its Aldyl “A” polyethene pipe the 1960s, that lighter material set the stage for his next big advancement in HDD.
“Up to that time, when you had steel pipe and a handheld air motor, you could not physically pull the pipe back through. You pulled a cable through the hole and hooked that onto a winch to the trucks, and they’d pull the pipe back through the hole,” Melsheimer said. “When polyethylene came out, we came up with the idea of putting the swivel behind the reamer and pulling the pipe back at the same time.”
That meant stepping up from the 3-hp air motor to the 30-hp, diesel-powered hydraulic Dynamole machine, which made it possible to ream and pull the lighter PE pipe back through the hole at the same time, launching a new phase for the HDD industry.
The use of drilling fluids was rare in those early days, Melsheimer said, estimating that 95 percent of contractors working in the Los Angeles area used only water.
“We just went up to the homeowners and gave them five dollars or something, and we’d hook onto their water with a hose that ran out to the machine. If you got into clay, you’d squirt some dish soap in your drill rod and put the water on,” he said. “Years later, we made a portable bentonite mixing machine. You’d end up with half of a tank left of mud, and you’d just take it down to the corner where the storm drain was.”
As the city expanded, Melsheimer’s crews stayed busy running 1-inch conduit for street lighting. While the basic approach stayed the same, tractors with augers replaced hand-digging of potholes, and a two-man crew made fast work of it. From there, equipment kept getting more powerful, and HDD capabilities continued to improve.
“We were one of the first ones out there with Ditch Witch … and we had the first electric-over-hydraulic controls, where the guy didn’t actually hold onto the controls on the carriage, walking it up and down the track,” instead standing 20 feet away with joysticks,” he said.
Melsheimer described an early river crossing in New Zealand using an RD300 Radiodetection locating system as being “like the Model T era” compared with the “Tesla era” of today.
“It would normally give out an interrupted signal, and then when you stop at the 6 o’clock position, it would give you a solid tone. And that’s all it would give you – period,” he said, adding that the system used on the New Zealand project could locate down to 20 feet “after you cross your fingers and pray for it.
As crude as sighting was in the old days, Melsheimer said, the systems were accurate enough to drill about a foot off of a live gas main.
“It was just amazing how accurately (operators) would hold that thing,” he said. “There was a lot of hope and pray with this method because the rotation of it would normally cause it to climb and go to the right. The good ones who’d do the sighting would know how to aim it left and down.”
“Again, it was the Model T era, but it worked, and we got millions of feet of that polyethylene put in the ground in L.A.,” he said. “The beauty of it is that it only lasts 50 years. So, guess what has to be replaced.”
Martin Cherrington
Big, Bold Projects Prove HDD’s Value in New Markets
While Dick Melsheimer’s work in L.A. focused primarily on compact applications, Martin Cherrington was thinking big in Northern California with the development of large rigs and visions of environmentally friendly river crossings.
Before pioneering the development of horizontal directional drilling in Sacramento and making headlines with first-of-their-kind HDD river crossings, Martin Cherrington gained broad experience working on dams, tunnels, pipelines, telephone and power cable projects with his father, a construction industry contractor.
Always looking for a better and faster way to get things done, Cherrington’s willingness to leap into new technologies led to plenty of successes but didn’t always prove to be the best career move, as he told a crowd that gathered to honor the HDD pioneer at the 2020 Underground Construction Technology International Conference & Exhibition.
Cherrington was working as foreman of a project to lay telephone cables in Los Angeles the first time he witnessed how effectively drilling technology could be used to place cables and conduits underground.
“I was already on my job, open-cutting with backhoes, and it was the biggest mess you’ve ever seen. Then across the street came in Irish Construction Company, and they were using this pothole drilling method,” Cherrington said. “They came in a couple of weeks after me, and they left a couple of weeks before I did.”
It wasn’t just that the process was faster, but it also was less disruptive, allowing residents to come and go from their driveways with no impact on work schedules. After finishing the L.A. project and returning to his employer’s home base of Sacramento, Cherrington was so enamored with the new process that he went out and charged a Chicago Pneumatic air motor to the company’s account.
“The one thing I forgot to do was to have a work order or an acquisition sheet. I didn’t tell the company, the bookkeeper or anyone that I was going to spend $900 and this was back in the early ’60s. The first thing I knew I had my pink slip,” he said. The short-term setback led to a groundbreaking future in HDD.
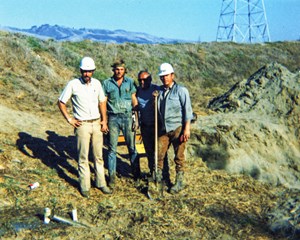
In 1964, Cherrington built his first drill rig and started Titan Contractors, specializing in utility road boring. His fledgling company benefited from a growth spurt in Sacramento, the state capitol, as well as a national beautification effort spearheaded by President Lyndon Johnson’s wife, Lady Bird, who sought to rid America’s neighborhoods of unsightly utility poles and cables. Sacramento County decreed that all utilities be placed underground, and Titan had to build a fleet of rigs to keep up with demand after contracting with the Sacramento Municipal Utility District to install underground cables throughout its service area.
Over the years, Cherrington amassed 27 patents related to horizontal directional drilling, drawing widespread recognition and helping to gain acceptance of HDD with his first river crossing, a 500-foot crossing under the Pajaro River of a 4-inch gas line for Pacific Gas & Electric. Despite the success of that project, however, he found that many were not ready to make the leap to horizontal drilling.
“At the very beginning of the contracting when we were drilling under rivers, it was a long space between getting jobs,” Cherrington said.
“Not everyone was interesting in doing this drilling. These pipeline owners and their engineers weren’t going to jeopardize their pensions for some newfangled idea of putting a pipe under a river,” he said.
He also faced a steep learning curve during those early years, drawing on the expertise of oil industry directional drillers while pioneering HDD methods “without any blueprints” for how to do any of it.
Northern California was a constant challenge of varying and unpredictable drilling conditions.
“We didn’t have the fine grain or orchard-type ground material or formations. We had hard pan that kind of reminded you a little bit of limestone. You could see these layers, kind of like a layer of hotcakes out there. And Sacramento was made up of that because it’s a flooded area, and it was coming down the mountains, so some of it was very hard and some was very soft,” he said, describing sparks flying as crews drilled through the layers.
Because of the conditions in the region, bentonite was in early use for HDD applications. Fortunately, because of oil drilling in the area, bentonite was readily available.
Although each job benefited from the learning of the last, there were some rough spots along the way. For instance, Cherrington recounted a story of an early attempt on that first river crossing after hiring an oilfield driller who brought out a heavy drill motor and bit.
“The bottom hole assembly never did come up. It just went straight down,” he said. “That driller we contracted who had all the tooling came to me and said, ‘Son, I think you’re drilling a dry hole here.’
“I thought that was just the end of the world,” Cherrington said. “But we finished the project with some of the utility equipment that we had. Then, on the next project, we had some input from (Smith Tool division) Dynadrill. That job was pretty successful using these tools.”
From that point on, Cherrington realized that much of the technological know-how that could be learned and applied to HDD could be adapted from the deep experience of the oil and gas industry. One of his early major successes was a 2,000-foot crossing under Louisiana’s Atchafalaya River of a 10-inch chemical line for Union Carbide. It was an arduous process with a single-shot system that had been in use since 1929, averaging 30 feet a day.
“The problem is, when you go out there 1,000 to 1,500 feet, it was hard to pump it,” he said describing the old Dowell cementing pumps and Halliburton trucks at work before Sperry Sun came up with the steering tool in the late 1970s that’s still in use today.
“Those pump trucks were really working, and the wire line was dragging down – and sometimes it wouldn’t make it. Just remembering it now – horrible memories,” he said.
He described a gradually improving evolution of equipment through the 1980s–90s, with cable rigs of up to 750,000 to 1 million pounds, followed by a series of rack-and-pinion rigs.
“Cable rigs had their place,” he said. “I’m glad those days are gone.” •
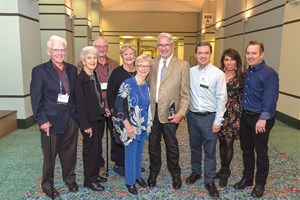
Comments