September 2018 Vol. 73 No. 9
Features
Mud Motors Remain Effective Tool for HDD Hard Rock Drilling
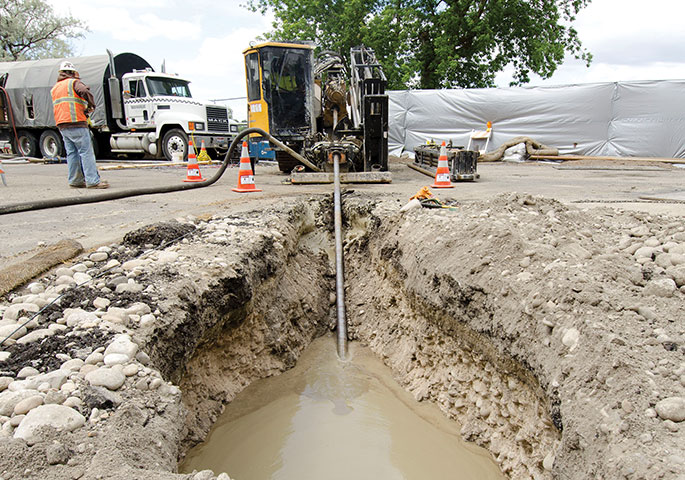
Underground Construction magazine has covered the evolution of horizontal directional drilling (HDD) since the first compact drill rigs made their appearance on utility job sites in the early ‘90s.
The magazine publishes reports about HDD projects and products of interest to the industry, and over the years many have been about difficult projects drilling in rock.
It may be easy to overlook, but long before HDD was being used for utility construction, big HDD rigs were making long, deep pipeline water crossings, many of them boring through hard rock.
The first long HDD pipeline water crossing using horizontal directional drilling was in the ‘70s, said Dan Sharpe, vice president of Sharewell HDD, a leading supplier of HDD downhole drilling tools, guidance systems and services.
Mud motors powered the cutting action of this equipment. Using a proven technology from oil field drilling, almost 50 years ago enterprising contractors adapted mud motors to horizontal directional drilling.
Today, mud motors remain a primary method of HDD rock drilling while mechanical dual-pipe systems, which enable mid-size drill units drilling in rock on urban utility construction job sites, have certainly made a growing impact as well. (See related article)
Motor details
The mud motor is powered by drilling fluid flow pressure to turn the drill bit. Basic components of today’s HDD mud motor are a rotor and stationary stator. A downhole mud motor typically has a 2-degree bend, set back 2 or 3 feet from the drill bit. To drill a straight path, every component of the tool rotates. To change direction, the mud motor turns the bit only. The angle of the bend is positioned to change the desired direction of the pilot hole, and drilling forward resumes.
Drilling with mud motors requires large volumes of drilling fluid and equipment to mix, circulate, clean and recirculate the mud mix. It also requires bits and backreamers appropriate for soil conditions, including hard rock, and sophisticated tracking and guidance systems.
Properly planned and executed, large rigs today make bores of thousands of feet to install large-diameter pipes.
It was in the ‘70s, Sharpe said, when it was recognized that with mud motor technology used in the oil industry, it was possible to guide a borehole to a predetermined target on the opposite side of a river or canal. This was done using a downhole motor for drilling and magnetic single shot guidance. A single joint was drilled, and a magnetic compass and plumb bob assembly was pumped down the drill string to land within a non-magnetic drill collar above the motor. A survey was taken and the instrument was withdrawn from the pipe. The single shot film was developed, and the results calculated and plotted on the drilling plan.
Evolution of all equipment involved in making installations with mud motor equipment has brought many improvements.
Sharp said when the wireline steering tool was developed and obtained, the time required to drill a pilot hole was significantly reduced and resulted in wide acceptance in the larger rig pipeline market. Adding roll and pitch, deeper depths, reducing local interference to the signal and dynamic transmission of position information were significant steps forward.
“My first experience with rock drilling was in the early ‘80s,” said Ron Halderman, Mears Group director of HDD. “Back then we were using the ‘wash pipe’ method – steering with a small inner string of NX wireline pipe (later upgraded to 2 7/8-inch drill pipe) and periodically ‘washing’ over this relatively weak string with 5-inch drill pipe. We used a low power Dyna-Drill motor and a PDC (diamond) bit. We also used a specially made hollow and expensive PDC wash pipe bit. Our reamers were also PDC.
“We generally had little success in rock harder than 8,000 psi UCS. In the early ‘90s, I was convinced by Frank McKenney of Smith International [now vice president of business development at Sharewell] to try their large 6-inch motor mounted directly on the end of the 5-inch drill pipe – there was no inner string.
“I was hesitant, so he did it all for free. It worked well and that completely changed my view of hard rock drilling.”
Effective
According to Sharpe, mud motors remain a basic tool for HDD rock drilling because they work. A mud-motor equipped HDD rig with proper downhole tools and necessary support equipment can cut and be steered through rock of any hardness.
Sharpe doesn’t expect the role of the HDD rock-drilling role of mud motors to change. Mid-size dual-pipe mechanical drill rigs have filled the need to drill in rock for shorter shots and small-diameter product, but he doesn’t expect to see mechanical system rock drilling technology to be introduced on larger equipment.
Halderman said there is no rock hardness level today that is a barrier to HDD.
“All rock can be drilled and opened successfully,” he said. “However, drilling in very hard rock is still for the big contractors who can and will take the risk. I would advise smaller contractors to be very careful in taking on rock jobs unless they are familiar with the particular formations where work will be done.
“I attribute successes to the combined efforts of contractors who can work out of the box and suppliers who understand the HDD business.”
Finally, Halderman added, it is important for magazines like Underground Construction to showcase new thoughts and innovations.
“That’s how we all learn to do a better job,” he said.
Comments