September 2018 Vol. 73 No. 9
Features
Modern Solutions for Freeing Stuck Pipe
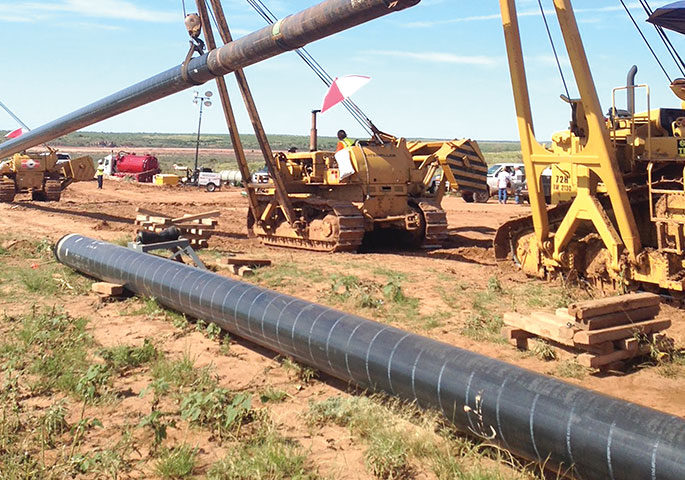
The business of horizontal drilling poses many risks, and unanticipated problems can cause completion deadlines to be missed or even prevent a job from being completed.
Having a drill string or product pipe stuck in the bore hole is something all drillers hope to avoid. Even though there are steps that help prevent this issue, pipe continues to get stuck, and many drillers today want to be prepared in case a stoppage does result from stuck downhole pipe.
“In today’s drilling market, drillers are being asked to complete longer shots with larger diameter casings that are stiffer and higher quality,” said Rick Melvin, TT Technologies national product specialist. “That makes achieving bends and the entire drilling process more difficult which, in turn, makes the potential for getting stuck much greater.”
There are a variety of reasons for drill pipe to become stuck or immobilized during a bore or product installation. Melvin said poor soil conditions can prevent returns from flowing out while performing the pilot bore, and solids left in the hole can cause the drill stem to lock up.
“Keyseating is another issue that can lock up a drill string,” he said. “As you’re reaming in softer soil material, your drill stems can sink down at the joint below the actual bore hole and get stuck. It happens as the bore path changes and if these pockets develop, it can cause the drill stem to become immobilized.
“Also, often excess cuttings left in the hole encapsulate the drill string and cause it to be stuck.
“Drilling under water or in loose-flowing soil conditions can cause hydrolock if external pressure being put on the product pipe from ground water, the drilling fluid and/or soil conditions exceed the drill rig’s pullback capability.”
Solutions
Often it takes a combination of methods that are most successful in freeing stuck pipe.
“When I’m talking to a contractor with a stuck drill string, the first thing I recommend is trying a wash-over pipe,” Melvin said. “It’s the cheapest, most readily available option and one that can be employed quickly. It is a steel casing with added carbide teeth that is drilled over the stuck drill pipe. While that is being done, massive amounts of fluid are pumped in to try and wash the cuttings and solids off the drill string. The process is limited by distance, drill capacity and flow.”
Another option is a “donut wash,” built like a figure eight.
“The pipe,” said Melvin, “has a head that rotates off a secondary drill string and the ‘donut’ head slips over the stuck drill pipe and follows the path of the string. Fluid is pumped down to wash away cuttings and free up the drill string.”
An approach to address product pipe stalled during installation is to use a block and tackle to attempt to pull the casing back a short distance to get things moving and reestablish the pull.
“Putting a pipe rammer on the back of a product pipe as a pullback assist,” Melvin said, “can re-energize that pipe and re-activate the drilling fluid that’s already down there and start things moving again. Connection between the rammer product pipe is made with a sleeve or ramming gear and then tapping on the back of the pipe.
“Another option is to attempt to add buoyancy back to the line. Sometimes water will get behind the pipe to the point where it’s actually floating. Add water to the pipe and usually put a rammer on the back of the pipe and let the water to settle.”
If nothing works, an attempt can be made to completely remove the pipe with a salvage operation, Melvin advised. Another pipe is attached to the struck pipe with a fabricated sleeve, and a winch can be used to assist the rammer. This may be enough to free the stuck pipe and remove it from the ground.
Being prepared
Frequently today, drilling contractors prepare themselves for the eventuality of getting stuck by bringing pipe rammers onsite with them. In fact, drilling contractors are pre-qualifying pipe rammers to be used on a project during the actual bidding process.
“By doing this upfront,” Melvin concluded, “and having everyone on the same page before the project begins, crews can react quickly and save time. By being ready, if pipe gets stuck at two in the morning, there’s no delay in getting a rammer. Reaction time is critical to getting the bore moving again.”
In its product line, TT Technologies offers Grundoram pipe rammers that can be configured to salvage product pipe, remove stuck drill stems, and assist drill units in product pullback. For assisting pullback, ram gear is standard and usually available in stock. For HDD pipe and drill stem extraction applications, Melvin said gear can be very specific, so often expanders and extractors require on-site fabrication.
FOR MORE INFORMATION:
TT Technologies, (800) 533-2078, tttechnologies.com
Comments