May 2017 Vol. 72 No. 5
Features
Ramming In The Great White North: LTL Directional Drilling Conquers Cold Weather, Collapsed Culverts
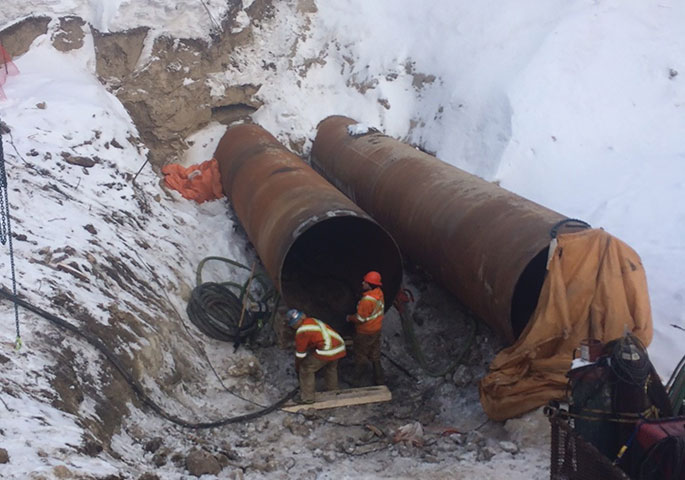
Culvert replacement can be a tricky proposition. The existing culvert is usually in bad shape to begin with. Add in weather, remote location and difficult site access, and now you have the makings of a project that only a few contractors can tackle successfully. LTL Directional Drilling, a division of LTL Group, Ontario, Canada, is one of those contractors.
The company was contracted to replace a pair of existing 60-inch by 100-foot corrugated metal pipe (CMP) culverts in Smooth Rock Falls, Ontario. The objective of the project was to ram a 72-inch steel casing over the existing 60-inch CMP culvert, then remove the culvert and leave the casing in place, and repeat the process for the other culvert. The objective proved easier said than done.
“We faced extreme challenges with the remote location and extreme cold weather. But those are the projects we excel at,” said LTL Directional Drilling Operations Manager Travis Kraag. “Our crews have the skills and the equipment to make these kinds of projects possible, despite the conditions.”
LTL utilized a 24-inch diameter Grundoram Taurus pneumatic pipe rammer from trenchless equipment manufacturer TT Technologies, Aurora, IL. “This project was full of challenges,” agreed Rick Melvin, TT Technologies’ pipe ramming specialist, “but LTL crews know what they’re doing with the modified extraction process. Having a powerful pipe rammer on the job helped as well.”
Company background
LTL Group has grown significantly over the past 10 years. The company has focused on larger, more specialized projects such as water intake installations and working with remote First Nations communities. LTL’s three core divisions work side-by-side providing clients with integrated, efficient and productive project outcomes.
Its contracting group provides municipal infrastructure services, along with sewer and water, marine construction, earth moving and more. LTL Environmental is highly skilled in demolition, dredging and site remediation services, to name a few. LTL Directional Drilling focuses on HDD services, along with other trenchless construction technologies.
For the culvert removal ramming project in Smooth Rock Falls, it was LTL Directional Drilling taking the lead.
Pneumatic pipe ramming continues to be utilized in a wide range of applications, both for primary pipe installation and as a method to help facilitate installation of other pipes or products. The advancement of pipe ramming continues to develop into new applications, through innovative ideas and techniques for achieving trenchless outcomes on projects with extraordinary requirements and restrictions.
While much attention has been placed on pipe ramming’s effectiveness for assisting directional drilling operations, the method has also been successfully used in a more standard configuration to facilitate the installation of drainage casings by ramming a larger diameter casing over an existing culvert.
“Any time you need to cross a road or railway with a large-diameter pipe, pneumatic pipe ramming is part of the conversation,” said Melvin. “The method is extremely capable in all kinds of soil conditions. It can be used as the primary installation method, or it can assist other methods like directional drilling or pilot tube boring machines.”
Ramming tools, in general, are capable of installing 4- through 147-inch-diameter pipe and steel casings. Ramming can be used for horizontal, vertical and even angled applications. It is often used under roads, like the Ontario project, and rail lines.
“Some installation methods can jeopardize the integrity of roads or rail lines because they remove soil from underneath to allow for the new pipe installation,” Melvin explained. “Pipe ramming’s ability to install various-sized casings without putting the topside structures in danger makes it a very attractive option. Pipe ramming works in difficult soil conditions.
Boulders and rocks, as large as the casing itself, can be consumed as the casing moves through the soil, and can be removed after the installation is complete. For LTL’s project, the objective was to swallow an entire collapsed culvert and then remove it.”
Culvert removal, replacement
LTL Directional Drilling needed to replace corrugated metal pipe culverts that were collapsing under Highway 634 north of Smooth Rock Falls, Ontario. The exiting culvert facilitated flow and overflow from a small stream from one side of the highway to the other. LTL Directional Drilling was contracted by the Ontario Ministry of Transportation to remove and replace the collapsing CMP culverts through pipe ramming.
“The access to the site was very difficult,” said Kraag. “We had to build almost 300 feet of road down a steep embankment, through 3 to 4 feet of frost and frozen ground. Of course, we were working alongside the highway in order to access the exiting culverts and get set up for ramming operations. Our goal was to encase the existing culverts with new 72-inch steel casings. Once in place, we could remove the collapsed culverts and the new casings would serve as the new culverts.”
After experiencing total rejection at 50 feet on two separate attempts with existing gear, LTL brought in the 24-inch-diameter Grundoram Taurus pipe rammer. Compounding the difficulty of the project were the extreme cold temperatures. In order to counteract the effects of the 40-degree-below-zero weather, forced air heaters ran 24-hours-a-day to get equipment in proper running condition. Crews also ran heaters inside of the casings to keep the ground condition as favorable as possible.
“Cold temperatures in this part of the world can make even the easiest of tasks difficult. But you prepare for it. You put the things in place that need to be in place in order to compensate for the conditions and get the project done,” Kraag added.
Before the 24-inch-diameter pipe ramming tool arrived on the job site, crews welded another 40 feet of pipe onto each of the partially installed casings. Weld time for each casing section was approximately three hours. Once in place, this would be enough casing to complete the project.
Prior to attaching the new ramming tool, the spoil and culvert pipe were removed from the partially installed casings. With the 24-inch ramming tool onsite, crews connected it to the 72-inch diameter casing with standard ramming gear from the equipment manufacturer. A 60-inch pipe ramming adapter made the connection to the tool. The 60-inch-diameter pipe ramming adapter was then connected to the 72-inch casing through a series of tapered locking ram cones. An excavator was used to cradle the pipe ramming tool.
“Standard ramming gear is now available for casings as large as 120 inches in diameter. Having standard ramming gear for all those sizes of pipe makes everything a little easier for the people in the field pushing in casing,” said Melvin. “It reduces the amount of field fabrication significantly and ensures the most efficient transfer of power from the pipe rammer to the casing. That’s essential to successful ramming projects.”
Two air compressors, one 1600 CFM and one 900 CFM, were used to power the rammer. Once everything was in place, ramming began on the first partially installed casing. The 24-inch hammer was able get the casing moving again at a rate of about 1 foot every two minutes until the casing was installed completely. The process was repeated on the next casing. Crews rammed 20-foot casing segments until they completely consumed the existing collapsed culvert. The collapsed CMP culverts and spoil were removed and the new casings were left in place to function as new culverts.
“Cold weather can mess with a project, but Travis and his crew really overcame tough conditions on the culvert replacement job,” Melvin concluded. “That was a tough situation. In the end, LTL came through.”
FOR MORE INFORMATION:
LTL Group, (807) 623-3600, ltlgroup.ca
TT Technologies, (800) 533-2078, tttechnologies.com
Comments