May 2017 Vol. 72 No. 5
Features
Coach Turned Auger Boring Contractor Has Plays To Save Time, Resources
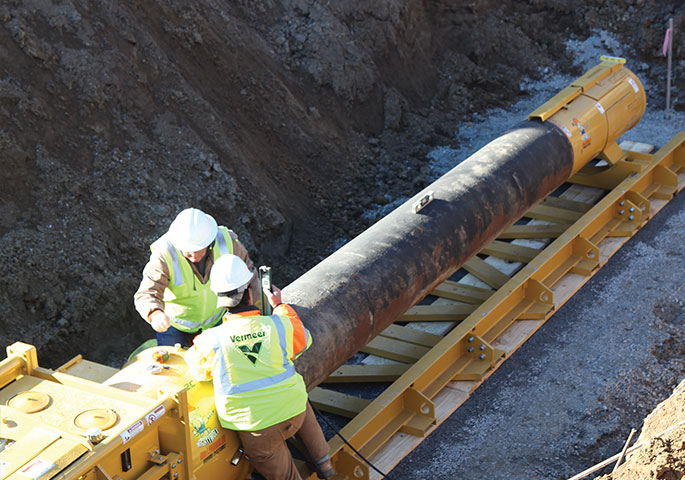
Basketball and auger boring are two completely unrelated topics unless Mike Boyd has a say in it. At the end of a lengthy career of coaching basketball, he knew he’d miss the excitement and strategy he left on the court. He took that dedication and applied it to his new contracting company, Three Point Construction. Founded in 2004 and located in Mechanicsville, MD, the company specializes in directional boring, trenching and auger boring projects.
Boyd usually has fewer employees than a basketball team’s starting lineup. He prefers it that way, though. By staying small, he eliminates the need for a foreman, and Boyd himself can be on-site for every job Three Point Construction takes on.
“When I started my own company, I knew I had to differentiate myself from my competitors,” said Boyd. “I decided that I’d be on-site for every job. No other bore contractor in this area has that level of hands-on ownership.”
Full-court press
Boyd refused to be one of those owners who only receive a call when there’s a problem. He wanted to be on-site to recognize the small hiccups early, and to fend off full-fledged disasters. He decided to put on some gloves and get back in the field. From gravity sewers and water main installations to utility relocations, Boyd is there to oversee the work. He said his presence on the job site creates some undeniable advantages.
“It gives the client a level of comfort knowing that I’m there,” he explained. “I can relay information to the client that I witnessed firsthand.”
In addition to an increased level of trust from his clients, Boyd said his hands-on style has had an impact on the company’s productivity level. He estimates his crew can double the installation of the standard operation without breaking a sweat.
“With 36-inch casings, the general rule of thumb (for auger boring) is about 40 feet a day around here,” Boyd explained. “My crew can do 80 to 100 feet on a normal day. It’s nothing special. I know that’s strictly because I’m there pushing them the whole time.”
How quickly he can complete a job isn’t a matter of pride for Boyd. It comes down to the accountability he feels for every project he accepts and an eagerness to complete each job on budget, on schedule and on grade. Then, it’s on to the next.
“If I did a job that normally takes two weeks in five working days, that’s all to the black,” he pointed out. “Instead of incurring all that expected labor and overhead, I’m just going to turn around and move on to the next job.”
Steering clear
Boyd recalled one project in particular when he had to bring his A-game. The town of La Plata needed to install a 10-inch gravity sewer at the National Guard Armory. The 220-foot auger bore needed to be approximately 20 feet deep. Boyd remembered ideal ground conditions — southern Maryland red clay that was stiff and firm, perfect for a steerable bore.
Even with optimal ground conditions, a few project specifications made this bore especially challenging. The percent of grade was only 0 .5 percent, and Charles County Public Works insists all installations must be perfectly on-grade.
“There couldn’t be any dips, valleys or bends to the left or right,” said Boyd. “The casing had to be straight, so we had to take our time with it. We couldn’t just throw it underground.”
A telephone pole right in the middle of the bore path made it so there was about a three-by-three-foot window on the receiving end that they had to hit from over 200 feet away.
The stringent grade requirements combined with the narrow receiving window made having a reliable and responsive steering apparatus extremely important. Since it was a 10-inch sewer, Boyd considered using a 36-inch casing, which would have given the crew a bit more room for the casing to go off-grade. Calling on the strategy skills from his coaching days, Boyd had a play he knew would save time and money on the project — the McLaughlin ON-Target auger boring steering system.
“The nice thing about the ON-Target system is that you know a lot sooner if you have a problem and if you need to adjust,” said Boyd. “It reacts quicker, so you won’t have those dips and valleys.”
The ON-Target system allowed Boyd to reduce the casing size from 36 to 24 inches.
“I convinced Public Works we could get the job done with a smaller casing,” said Boyd. “Obviously, 24-inch casing is a lot cheaper than 36-inch.”
The system allowed the crew to reduce its production time, as well. Boyd had quoted two weeks to complete the project, and his crew completed it in five days.
He mentioned one other benefit of the system. “It’s a lot easier to get paid when the casing ends up where it’s supposed to be,” he laughed.
End of push and pray
As horizontal direction drilling (HDD) continues to dominate the market, Boyd knows he has found a niche. He’s the last remaining auger boring contractor in his area. Others have moved to HDD or packed up shop all together.
“I wouldn’t say auger boring work has declined,” Boyd said, “but it’s not being utilized as much as it could be.”
Boyd is determined to employ the auger boring machine in circumstances where the application makes sense – which he believes is most of the time.
“Auger boring is still asked for specifically by a lot of government agencies because they trust the accuracy of the installation method,” he stressed.
Boyd’s been in the market a long time and knows that cost-effectiveness is key to a successful business. Moderate steel prices always help with that, but getting jobs done right the first time is the best way to guarantee survival in this business.
“The days of pushing and praying that the casing goes to the right spot are just over,” Boyd said. “There’s no room for those kinds of errors anymore. The ‘just get close’ mentality doesn’t cut it. It’s worth taking the extra precaution of using one of these steering heads and you take all that out of the equation.”
You can bet Boyd will be onsite for every job, making sure his crew is taking those precautionary steps to ensure the bore is right on target.
FOR MORE INFORMATION:
Three Point Construction
(301) 472-4040, threepointconstruction.com
McLaughlin
(800) 435-9340, mclaughlinunderground.com
Comments