December 2017 Vol. 72 No. 12
Features
Tips For Better Accuracy In Utility Plowing
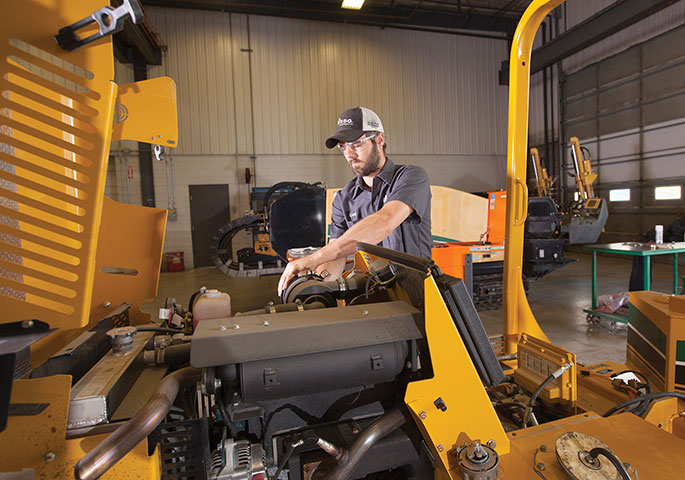
From upgrading existing services to installation of high-quality broadband, a vibratory plow is an in-demand piece of equipment. Utility installation projects, both rural and urban, can go quickly and smoothly with the help of this machine – when it’s operated correctly.
Failing to plan, forgoing maintenance and other simple missteps can be major hits to a plow’s accuracy. For optimum operation, focus on these five areas of best practices.
1. In the know
Efficient plow operation begins with knowing the area – both what’s above and below the surface. Smaller projects may not go through a full geological survey phase, in which case it’s even more crucial for the team to do its homework on the site.
It’s both smart and responsible to know what’s underground and map the plowing path accordingly. Not only will this prevent accidents and damage to existing utilities, avoiding underground obstructions will result in more accurate plowing and a better finished product.
Above-ground obstacles like telephone poles and boxes should also be noted and accounted for on the path. Plows aren’t agile machines that can turn on a dime. If an unexpected obstacle is encountered, the machine has to stop, reposition and alter its course, an interruption that costs precious time and delays, and can and should be avoided.
2. Made in the blade
The plow blade is a big key to optimal operation. It needs to be as wide as the line, whether cable, conduit, etc., going into the ground. That said, the wider the blade, the harder it pulls, so choose a blade that’s no wider than it needs to be.
On a similar note, certain blades pull better in certain ground conditions. Going back to knowing the area prior to starting the job is a great time to assess the soil and underground conditions to be sure the blade choice is appropriate.
A final tip is to always choose a blade with a leading edge in good condition, and the same goes for the toe. Dull tools decrease performance.
3. Proper operation
Any piece of equipment is only as good as its operator. A few best practices and simple tips can make a big difference in time savings and accuracy.
When using the up/down and swing functions, place the hydraulic control levers in float. This allows the plow to better follow the path of the machine, especially valuable in projects with several turns and hilly terrain.
To prevent wasted time and effort, never plow deeper than what’s specified. Not only is it wasteful, it’s unnecessary. Plus, any deviation from job specifications communicated by the project owner could have a negative impact on the company.
4. Maintenance matters
An unreliable plow or one that’s in poor condition can’t possibly operate at its best, making it important to follow the manufacturer’s recommendations for maintenance, and a few other tips too.
Prior to each day’s operation, do a quick visual inspection. Walk around the machine to check for issues. Oil and fuel leaks, cracked hoses or any visible signs of damage to the machine should be addressed immediately. Take time to check pins and bushings too.
Secure or replace pins as needed.should always be applied at the end of the day, when the machine is warm and more receptive to it – a habit to adopt when shutting down the plow for the day.
Finally, take advantage of the slow winter months to give the plow extra TLC. Whether done in-house or through a trusted, local equipment dealer, a thorough inspection annually is a great way to protect the equipment investment and ensure reliable operation in the upcoming year. RDO
Vermeer, for example, offers service and winter inspection programs, designed to address any issues from the tough working months, as well as prepare the machine for next season’s busy schedule.
5. Assessing the alternative
Sometimes the best way to efficient plow operation is to use other equipment.
Wait, what? That doesn’t sound right. It’s true though. Utility work, especially in rural areas, often requires different machines for specific needs. Knowledgeable operators identify this upfront and plan accordingly.
For example, most rural ditching projects cross over numerous county roads. Because plowing through the roads is not an option, a horizontal directional drill (HDD) can be brought in for that part of the project. This strategy works for a variety of other projects, from those that go under creeks and rivers, to those that cross major highways or busy interstates.
Similar to swapping in different pieces of equipment on the job site, a variety of attachments cater to different projects, soil conditions and other unique job-site factors.
Rocky soil and very hard underground conditions are common. In this case, it may not be necessary to switch from a plow to HDD machine. Instead, a trencher or rock saw/wheel attachment can tackle the job.
Also common with rocky soil is the use of a backhoe attachment. Rather than alter the path and drill around large rocks, the backhoe can dig up the obstruction and remove it from the equation.
From start to finish
Accurate vibratory plow operation is more than a few tips, it’s a full strategy. The strategy begins with a thorough understanding of the area and its characteristics, continues every day with best practices and maintenance, and doesn’t end until the job is completed – a day that will come much quicker by following these recommendations.
About the author: Mark Rieckhoff is sales manager for RDO Vermeer in Burnsville, MN.
Comments