September 2016, Vol. 71 No. 9
Features
Keeping HDD Equipment In Top Operating Condition
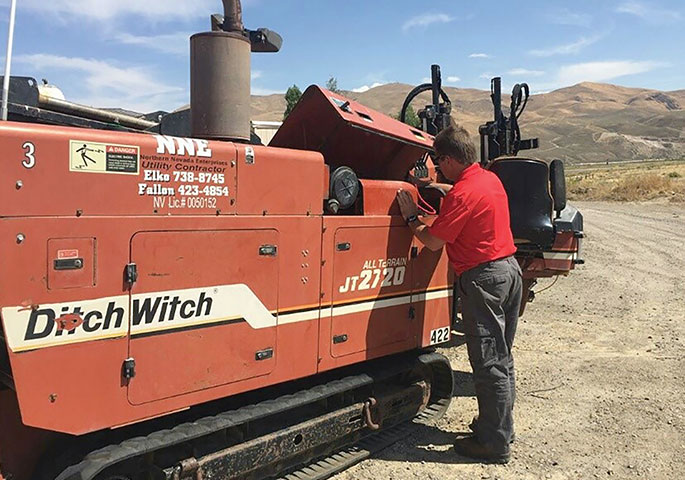
By Jeff Griffin, Senior Editor
A key to being a successful horizontal directional drilling (HDD) contractor is finishing every project to specifications on or ahead of schedule.
To achieve that, drilling equipment must perform efficiently throughout the project without breaking down. Downtime is costly and a contractor repeatedly forced to halt work due to equipment issues not only risks missing completion dates, but can lose future business because of a reputation of unreliability.
Keeping equipment in top working condition reduces the risk of downtime, but that can be easier said than done. A machine may move immediately from a finished job to another project. On projects where equipment is working long hours every day, being “too busy” to stop long enough to perform scheduled maintenances can lead to serious problems.
The ways contractors make sure their equipment stays in good working condition varies greatly. Many large contractors have their own shops and mechanics including a formalized policy and maintenance procedures. Smaller companies may rely on individual crew members responsible for preventive maintenance. However, no matter the size of the company, the number of drill units it operates, and how maintenance is managed, the goal is the same: keep drill units drilling and pulling back product.
NNE Construction
NNE Construction, Elko, NV, has a comprehensive program for maintaining drill rigs.
“Before each project, our rigs are taken to the shop and inspected by our mechanics and also inspected by the operator,” said Sam Ballard, NNE supervisor. “Any problems are addressed at that time – before the drill leaves the yard.
“We have a scheduled periodic maintenance program that allows our mechanics to request a time for the rigs to be serviced based on the recommended hours of operation. Items checked are table slide pads, shuttle arm pads and grips, vice teeth, track tension, chain tension, belts, hoses and overall general condition of the machine.”
Each machine is put through basic operations to check functionality and then is sent to a job.
During operation, the condition of drill pipe and tooling is inspected before each use or at the time each connection is made. Rods with excessive wear are removed from the string until they can be further inspected.
“Every morning the drills are given a regular safety and maintenance check before operation,” Ballard continued. “This includes everything from fluid checks to safety equipment and operational lockouts to prevent accidental machine damage or harm to personnel due to equipment failure. Details are recorded daily on an inspection form and turned in for review by our maintenance manager and mechanics.
“Regular lubrication also takes place at this time. Many of the sites and locations we work at require these checks, and that copies of inspection records be available upon request. It is in our company’s best interest, and the safety and security of our employees, that these checks are completed so that work can be done effectively and efficiently with the utmost concern for safety,
followed by productivity.”
Anyone on a job has the authority to take a machine out of service for safety concerns, Ballard said. Functionality issues are covered by the operator and the mechanics with management to warrant shutting down a project for repairs or maintenance. In most cases, these decisions are made based upon recommendations of the operator.
“When a job is completed,” Ballard said, “machines are returned to the yard and washed, inspected, lubricated and the necessary repairs are made. If a rig has been idle for a period of time, before it goes out, the fluids and filters are checked and changed, if necessary, prior to its use.”
Ballard said these practices have extended the productivity of the company’s directional drilling equipment.
“Our newest machine is a 2003 model and still runs with minimal downtime and repairs,” he said. “Many of our machines have very high hours and require regular maintenance and upkeep just as new ones will. This is the benefit of good maintenance, careful experienced operation and quality products. In spite of the age and hours on our machines, it also helps us to maintain a good reputation on a project because our equipment is capable of completing tasks with minimal breakdowns and repairs.”
NNE is experienced in underground and aerial fiber optic, microwave and cellular construction including, but not limited to, horizontal directional boring, excavation, land development, tower, electrical and IT work. The company operates in several western states. NNE operates directional drills ranging from 17,000 to 70,000 pounds of pullback.
Alltech Directional Drilling
Alltech Directional Drilling Inc., Happy Valley, OR, makes sure its HDD equipment is ready to go to a new job by thoroughly checking it on completion of a project and replacing worn parts and making necessary repairs, said Michael Thomas, president.
Routinely checked are track tension; all oils are checked and if any are at the limit on hours, they are replaced; carriage rollers are checked and adjusted; the saver sub is checked for wear; vice jaws are checked for wear; all electronics are checked to make sure they are functioning correctly; and the drill is completely washed and cleaned.
On the final pull of a job, all collars and roll pins are checked for cracks and wear. Safety checks also are part of the inspection, including the electric strike alert and limit switches.
Inspections are made in the shop or in the field, depending on circumstances.
“The project foreman has the responsibility for maintaining condition of drilling equipment,” Thomas said. “On the site, the foreman, operator and I as the company owner have the authority to take a machine out of service.
“When a machine moves from one job site directly to another, our strict policy is we go through the complete checklist before it can be put in operation. That includes cleaning. Cleaning equipment is a top priority with me because it allows us to notice problems such as oil leaks, cracks, etc.”
Alltech is a family-owned business experienced in all phases of trenchless and open-cut construction with a primary focus on telecommunications. Most of the company’s work is in western states, but Alltech HDD crews currently are installing fiber optic cable in Texas in the Dallas-Fort Worth metroplex. Alltech uses 30,000-pound pullback HDD equipment.
Jackson Creek Enterprises
Jackson Creek Enterprises, Allerton, IA, operates drill rigs ranging from 7,000 to 24,000 pounds of pullback.
“We don’t have a formal equipment maintenance program, but our policy is that every drill unit be in work-ready condition at all times,” said owner David Wampler. “All our employees understand that having the equipment work ready is important to getting the job done. We believe in the old saying: ‘Take care of the equipment and the equipment will take care of you.’”
That means all fluids and filters are changed at manufacturers recommended intervals. All daily maintenance is done at the end of the shift when the machine is warm so it will be ready for the next day.
“Winterizing machines and pumps is done every day from November through March, and sometimes earlier,” said Wampler. “We do this regardless of daily temperature forecasts. It is cheap insurance for those times that the weatherman is wrong.
“Drill rod maintenance is critical to overall success. This means limiting oversteering the drill rod, using good thread compound every time a joint is connected, and keeping the drive chuck greased and in good condition. A bad or worn drive chuck can ruin every rod in the drill string. Replacing it at the first signs of wear can greatly increase the life of the drill rods.”
“Cleanliness is next to Godliness” applies to equipment, too, said Wampler.
“Drilling fluids and excess rod grease are washed off daily utilizing the power washer on the vac truck,” he continued. “We always have several weeks in the shop during the winter months where we give all of our equipment a thorough cleaning, buffing and waxing. Not only does it protect the paint from fading, it looks better on the job site and increases the equipment trade-in value. Almost all of our projects are in residential areas. Having nice looking equipment and keeping the job site cleaned up, including sweeping the streets and sidewalks, goes a long way in reducing complaints.”
Jackson Creek personnel are experienced with the underground utility installation of water, sewer, gas, electric, fiber optics and cable television. In addition to utility applications of directional drilling, the company has the expertise necessary to successfully complete environmental and soil remediation projects.
FOR MORE INFORMATION:
NNE Construction,
(775) 738-8745, nneconstruction.com
Alltech Solutions Inc.,
(506) 8589432, alltechsolutions.ca
Jackson Creek Enterprises,
(641) 873-6500, jackson-creek.com
Comments