October 2016 Vol. 71 No. 10
Features
Importance Of Compact Track Loaders Undercarriages
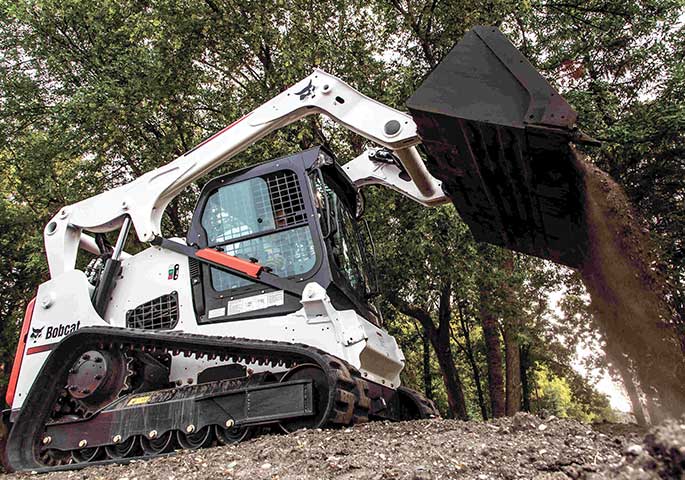
When was the last time you worked on a construction site and didn’t see a compact track loader? The popularity of compact track loaders has dramatically increased since its inception in the mid-’90s. In fact, today, these machines account for nearly 20 percent of all financed equipment in number of units, according to Equipment Data Associates.
Compact track loader benefits such as their powerful pushing, digging and lifting performance; exceptional traction; minimal ground disturbance; increased flotation and attachment versatility, have made them popular in construction. In addition, the loader’s tracked undercarriage enables contractors to work more efficiently in wet or soft soil conditions, adding weeks of production to a schedule that would have otherwise been lost to unsuitable ground conditions.
For utility contractors, it’s important to understand compact track loader benefits, advantages of rubber track undercarriages, track patterns and types, and the importance of proper undercarriage maintenance.
Understanding undercarriages
One of the hardest-working parts of a compact track loader is its undercarriage, so it is important to understand undercarriage track systems and how they can be successful in a variety of conditions. Compact track loader manufacturers offer the following undercarriage types.
A fully-enclosed, solid-mount undercarriage is driven by two powerful direct-drive hydrostatic motors, which include internal tapered roller bearings to help carry heavy load stresses.
Dual-flange front idlers ride on the rubber track’s roller way, helping absorb shock and reduce wear on the inside of the track. The undercarriage is also equipped with single-flange idlers located on the rear of the machine to help minimize de-tracking. Idlers and rollers are permanently sealed and lubricated, requiring no routine maintenance.
A solid-mount undercarriage provides the traction necessary to work in soft conditions. Its design stabilizes the loader and work group, making it the best type of undercarriage for leveling or grading applications. The undercarriage provides a consistent tractive effort to improve pushing power, produces a more level grade than other track systems and permits higher tipping loads for improved performance when carrying materials.
In addition, a horizontally mounted tension cylinder opens up room in the undercarriage for easier cleanout. The undercarriage is sloped on both sides to shed material such as sand, dirt, mud and debris better than previous designs. Additionally, raised cutouts between the rollers allow for easier cleaning.
A fully-enclosed roller suspension undercarriage provides a smoother ride on hard surfaces or long-travel applications than a solid-mount undercarriage. The undercarriages are made of tough, forged steel components, similar to tracks used on bulldozers, which offer increased traction, improved ride and the potential to extend track life.
This system offers better shedding of mud and debris than other systems, saving valuable time during cleanout and maintenance. It incorporates dual flange front idlers, wide rollers and mono-leaf springs for smoother action. The extra weight of the track system increases traction to provide more pushing force as well.
Choosing track pattern, type
Depending on the application and project needs, compact track loaders can be equipped with a variety of rubber tracks. Custom-made C-pattern rubber tracks provide the best combination between flotation and traction. The main components of the rubber tracks are internal steel cables similar to steel-belted radial tires, which provide for a strong base. These cables do not stretch, minimizing the need to check track tension.
In addition, a variety of tread patterns can accommodate various applications:
- Block Pattern delivers a comfortable ride on hard surfaces and provides minimal ground disturbance due to its staggered tread pattern
- Multi-Bar Lug offers a smoother ride than traditional lug patterns and has excellent traction with a greater number of tread lugs per foot
- Non-marking reduces the risks of damage to delicate surfaces, especially when traveling over grass or finished concrete.
- Wide tracks work well when lower ground pressure and flotation are desired, while narrow tracks add increased ground pressure, traction and pushing force.
Undercarriage maintenance
If the undercarriage is not routinely inspected and maintained, it can easily cost operators valuable time and money, as well as potentially decrease the track’s lifespan.
A full undercarriage inspection should be completed to keep maintenance to a minimum. Look for excessive or uneven wear, as well as damaged or missing components. If the machine is being used in harsh applications, the undercarriage may need to be inspected more frequently.
During a routine inspection, the tracks should be checked to see if any components look out of place. If so, this could indicate a loose track pad or possibly a broken track pin. In addition, the rollers, idlers and drive motors should be examined for oil leakage. These oil leaks could indicate a failed seal, which could lead to major failure in the rollers, idlers or track drive motors
It is also important to tailor the track to the job and maintain proper track tension to decrease track wear. As a general rule, when operators are operating in soft, muddy conditions, it is recommended to run the tracks slightly looser.
As always, certain job-site tasks can create more wear on tracks and undercarriages than other applications, so it is important to adhere to the manufacturer’s recommended operating procedures.
Here are two tips to help minimize track and undercarriage wear:
- Make gradual turns: Sharp turns or pivoting
the machine can lead to accelerated wear and increase the potential for de-tracking or damage to established surfaces such as lawns. - Avoid harsh environments: Rough asphalt or concrete or other abrasive materials can cause damage to rubber tracks.
Understanding the advantages of a rubber track undercarriage, track patterns and types and the importance of proper undercarriage maintenance can help operators add more workdays and potentially open up new applications to further its utilization.
ABOUT THE AUTHOR: Jason Archbold is the marketing manager for Bobcat Company, a compact equipment division of Doosan Bobcat Inc. Archbold has nearly 20 years of marketing and analytics experience in several industries, including construction, engineering and electrical/industrial supply. Bobcat Company, headquartered in West Fargo, ND, is a worldwide leader in the manufacturing and distribution of compact equipment.
Comments