July 2016, Vol. 71 No. 7
Rehabilitation
Innovative Design Leads To Trenchless Solutions
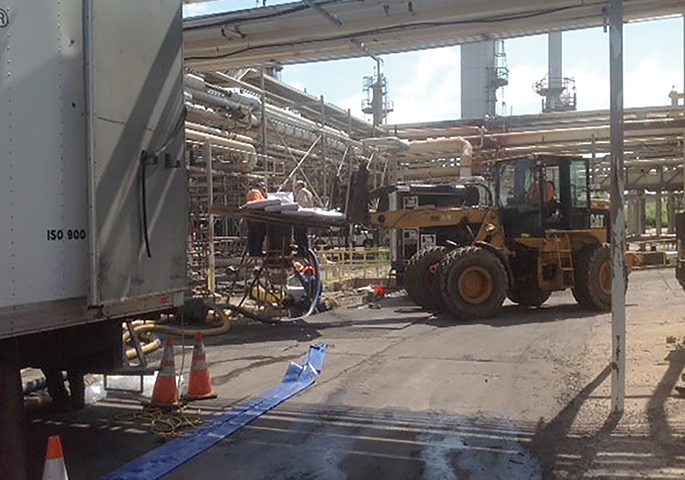
An “Impossible” Project Completed On-Budget, Ahead Of Schedule
Many sewer line replacement and rehabilitation projects could be classified “routine” because they are relatively straightforward with few complications.
Even so, no two projects are exactly alike, and most have challenges and issues that must be addressed. In some cases, problems may seem impossible to overcome.
An example in the “impossible” category was a project that replaced 6,700 feet of severely deteriorated sewer main running through an oil refinery operating 24 hours a day, seven days a week. Therefore, work had to be accomplished without halting or interrupting the refinery’s operations.
The more than one-mile-long section of pipe going through the Phillips 66 refinery is a critical element in the sewer system of Ponca City, OK, serving a drainage basin that includes 570 acres of mixed commercial and residential land, along with the Phillips 66 refinery office complex, research and development facilities and the refinery itself.
“The nearly 100-year-old section of vitrified clay pipe had been a continuing source of trouble for years,” said J. Bret Cabbiness, P.E., president of Cabbiness Engineering LLC, the project’s engineering firm. “It was a frequent source of backups. There were broken and missing pipe segments, and large amounts of groundwater inflow and infiltration (I&I). For decades, city leaders, refinery management and local citizens were frustrated that a sensible and affordable construction solution for this failing sewer line might not ever be designed.”
Ponca City Utility Authority called on Cabbiness Engineering to develop a feasible solution to replace the sewer line without interfering with the refinery’s operations. The $1.6 million project designed by the Cabbiness team was completed under budget and ahead of the six-month completion deadline.
Restrictions
As Cabbiness engineers began the design process, there were obvious restrictions to consider.
“One option not available was to request the Phillips 66 refinery to shut down and relocate refining units,” said Cabbiness. “With the added challenge of the project being located within an oil refinery operating at full capacity, the design had to take into account the refinery’s stringent safety requirements and operational restrictions that construction would encounter. [See sidebar for details.] This challenge required us to establish viable construction sequencing regarding the refinery’s around-the-clock operations.

“The project also brought the challenge of dealing with refinery equipment and refinery support components that had been constructed over the top and adjacent to the existing sewer main.”
A third design challenge was the rehabilitation of a portion of the existing sewer that crossed underneath multiple, highly active Burlington Northern Santa Fe (BNSF) Railroad tracks inside the refinery.
The first step in planning was to locate the existing manholes and identify connecting sewer mains. A survey was augmented by detailed drawings of refinery equipment, known pipelines and storage tanks, underground utilities and Phillips 66 monitored groundwater levels. A previous closed-circuit television inspection report provided by the refinery, and interviews with refinery staff and various Ponca City personnel, helped complete the project’s background information.
Flow monitoring of the existing sewer line upstream and downstream of the project’s boundaries was conducted to confirm average daily flows and peak sewage flows. This information shed light onto two significant elements that had to be considered in the project design: actual contributing flows from a fully developed drainage basin, and peak flows that included I & I of storm water and groundwater within the refinery’s property boundary.
During the development of the required Oklahoma Water Resource Board (OWRB) and Oklahoma Department of Environmental Quality (ODEQ) preliminary engineering report, the Cabbiness team quickly ruled out two design alternatives: direct burial of pipe below grade in an open trench, and construction of a bypass pump station.
“Direct burial of pipe in an open trench was ruled out because of the number of unknown, underground piping conflicts expected, and the possibility of impacting unknown, environmentally sensitive areas from nearly a century of refinery operations,” said Cabbiness. “Another factor was the escalated construction costs of these methods working within the refinery property.
“Although a new sewer lift station would address the city’s sewage flow, it would have left the refinery to combat the remaining problems of the existing sanitary sewer. Also, the initial capital cost and long-term maintenance costs of a sewage lift station further prohibited this option from being selected.”
Trenchless
Therefore, the project clearly called for trenchless construction.
“After evaluating design alternatives, an innovative, trenchless rehabilitation approach was developed that combined the use of pipe bursting and cured-in-place pipe (CIPP),” said Cabbiness.
Pipe bursting provided the best option to pull in a new pipe because of the number of offset joints, missing or broken pipe and pipe-protruding obstacles. Where access to the existing sanitary sewer line was limited by the proximity of existing refinery pipes or vibration-sensitive refinery equipment, CIPP was utilized.

Temporary bypass pumping was part of the overall construction plan, making a separate bypass system unnecessary.
Flow studies had found the existing sewer pipeline (ranging in size from 12 inches, 18 inches and 24 inches) to be slightly oversized for the expected average daily and peak flows.
“By pipe bursting a smaller outside diameter pipe inside the existing pipe’s larger diameter, the risk of a bursting head becoming stuck or hung up was virtually eliminated,” said Cabbiness. “Although the design reduced the new pipe’s interior diameter, the major improvement of the pipe’s coefficient of friction, along with the accepted reduction of sewage design flows, substantiated this innovative design. New pipe installed was in diameters of 12, 16 and 20 inches.”
While most of the project was accomplished by pipe bursting, CIPP was used in areas where underground vibration of pipe bursting posed the risk of damaging sensitive refinery equipment above the pipe.
Primary contractor Urban Contractors, Oklahoma City, performed the pipe bursting, as well as construction of new manholes and rehabilitation of existing manholes.
Due to the numerous, undocumented piping systems expected within the nearly 100-year-old refinery site, pipe bursting access pits were hydro-excavated by a refinery-approved subcontractor prior to the start of construction, allowing the project to stay on schedule. In three known instances, existing manholes had been buried by past refinery expansions and improvements. Several other manholes were located, but inaccessible for construction.
In addition to inaccessible manholes, other flow obstructions were found during the design process, including lightning protection grounding rods driven through the existing sewer, steel plate weirs constructed inside existing manholes, several pieces of broken pipe creating in-line blockages, protrusion of protective concrete caps into the pipe joints, protruding service connections, and a blind junction box.
Static bursts
With access to the sewer manholes, static pipe bursting provided the best result. This eliminated two major sources of groundwater infiltration and simplified the sewer system for future maintenance.
“The average length of pipe bursting was about 300 feet,” Cabbiness said. “In a few instances, we had pulls that extended to nearly 500 feet because of the manhole locations and existing refinery buildings, and other refinery equipment and refinery units.”
A 10-peson Urban Contractors crew made 14 bursting pulls on the project, using TT Technologies bursting equipment.
The project design required the pipe to withstand the fallout from hydrocarbon-impacted soils created by refinery operations in decades past. The pipe selected was SDR 19 HDPE DIP.
“The refinery had cleaned and mitigated most, if not all, of the areas adjacent to the existing sewer and the area was in good standing with ODEQ and the EPA,” Cabbiness said. “Hence, we worked closely with Phillips 66 and the regulatory agencies to ensure we followed necessary protocols and procedures if we encountered any hydrocarbon-impacted soils.”
Pipe was fused in predetermined staging areas outside the active refinery units and was pulled to the construction area with special permission and coordination from the refinery staff.
Insituform was the subcontractor for CIPP segments. The specified liner had a special CIPP resin that is inert to hydrocarbons. CIPP runs were from manhole to manhole, and lining was cured with standard hot water procedures.
“Completing the sewer rehabilitation project within the established six-month construction period was critical to the refinery’s continuous 24-hours a day, seven days a week operation,” Cabbiness emphasized.
Beating the deadline
“As it worked out,” he continued, “Urban Contractors finished nearly two months ahead of schedule. A majority of the credit for early completion goes to the contractor’s construction crews and management, city and refinery on-site field representative, and our design team’s field representatives, all working together for the common good of the project.
“The elimination of I&I by trenchless construction decreased the actual sewage flow in the sewer main, reduced the amount of wastewater being treated at the city’s wastewater treatment plant and saved the Phillips 66 refinery approximately $254,000 a year in sewage treatment costs, as well as the cost to replace all the lost water from the fire water storage ponds from their deep underground wells.
“Moreover, the project eliminated the city’s upstream sewer main backups in the entire drainage basin. This not only saved the city money, but also brought relief to residents who had been continuously impacted. Truly, it was a win-win-win situation for the residents, the refinery and the city of Ponca City.”
Following completion of the project, Dr. Hong Fu, director of Ponca City environmental services, praised the program.
“Many people in our community, the Phillips 66 Refinery staff and even our own city government had for years believed there was no viable or financially feasible solution to this important and much-needed project.
“Not only were the various trenchless rehabilitation designs meticulously analyzed, but both the project budget and construction schedule were held completely intact as planned and never compromised. All of this was realized by the Cabbiness Engineering team regularly visiting the job site to offer innovative design and construction solutions, and to help coordinate any necessary field changes as they were discovered,” Fu said.
“The city of Ponca City is pleased to have had Cabbiness Engineering as our engineer of record for this project, providing the much needed vision and engineering expertise to solve this once thought un-solvable problem.”
Safety On A Challenging Construction Site
With a public sewer line traversing an oil refinery’s highly secure and sensitive private property, planning engineers and construction personnel faced out-of-the ordinary job-site challenges.
“Safety was paramount for the construction crews, inspection staff and Phillips 66 employees,” said J. Bret Cabbiness, P.E., president of Cabbiness Engineering LLC.
Cabbiness proposed to the Phillips 66 refinery management and Ponca City leadership that all those involved in the project adopt the refinery’s construction safety policies, operational procedures and accepted refinery construction practices.
“The refinery’s construction safety policies,” Cabbiness said, “are more stringent than normal municipal projects for obvious reasons. We felt as a design team, we had to respect the unique construction environment and do everything possible to ensure that everyone came home safely every night after work.”
All project personnel, including the engineering design team, owner representatives and construction contractors were required to complete site-specific Phillips 66 safety training and conform to special, personal-protective equipment requirements while on site.
“No exceptions regarding safety would be allowed,” he said. “Any incident of non-compliance would subject that person to immediate expulsion from the project.
“Prior to submitting bids, all construction contractors were pre-qualified by documenting that they had the proper safety training, construction experience and expertise, as well as having all necessary construction equipment to provide the safest work possible.”
Other project requirements included a separate, on-site safety coordinator and project manager to ensure all of the safety protocols were followed and that daily refinery construction permitting procedures were completed to ensure that all refinery unit operators were aware of construction activities and personnel that were on site.
“The project was completed without any safety violations or safety instances,” said Cabbiness.
FOR MORE INFORMATION:
Cabbiness Engineering,
405-310-6435, www.cabbinessengineering.com
Urban Contractors,
405-478-5370, Urbancontr@aol.com
TT Technologies,
(800) 533-2078, www.tttechnologies.com
Insituform,
(800) 234-2992, www.insituform.com
Comments