September 2015 Vol. 70 No. 9
Features
Record Setting Houston Ship Channel Crossing
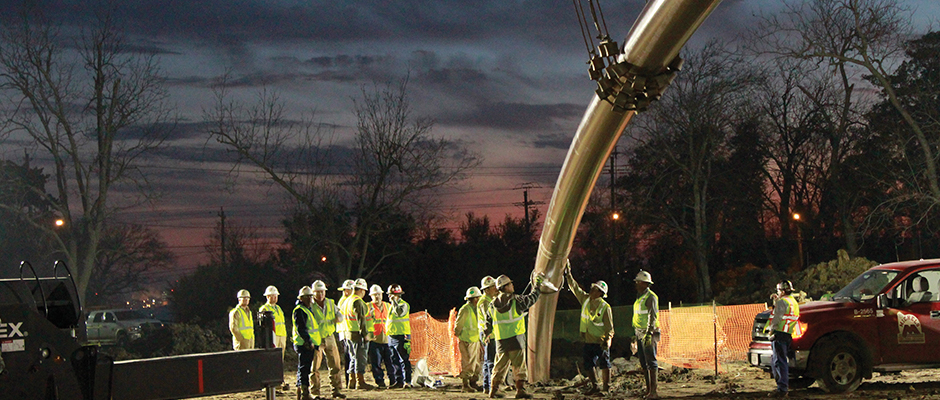
by Greg Goral, design engineer, Michels Directional Crossings; and
Donald Mueller, assistant operations manager, Michels Directional Crossings
The 50-mile-long Houston Ship Channel is regarded as a modern marvel of civil engineering. So is the 2.6-mile-long cable-stayed Fred Hartman Bridge that spans it.
In February, another construction project joined those esteemed ranks of major achievements in modern day construction – and the record books – when Michels Directional Crossings, a division of Michels Corporation, one of the world’s leading horizontal directional drilling (HDD) contractors, completed HDD reaming and record-setting pullback installation of an 18-inch steel pipeline for Phillips 66 under the Houston Ship Channel.
Although Michels has completed longer, smaller-diameter crossings, the combination of size, length, location, swelling soils and congestion of existing pipelines, severely reducing the right-of-way, made this crossing one of the more difficult and technically challenging crossings ever undertaken in the trenchless industry. The 12,459-foot HDD project (approximately 2.4 miles) established yet another world record by Michels for its
diameter, as the pipeline spanned an unimaginable length beneath the banks of the ship channel from LaPorte to Baytown, TX.
Troy Construction was hired by Phillips 66 to provide the necessary support to Michels’ HDD operations. Its crews prepared two work-site footprints to accommodate a drill rig on each side of the canal so that intricate pilot-hole intersect operations could be successfully performed. This operation required each drill rig to simultaneously drill toward one another from both land-based locations until the pilot holes could intersect at a predetermined location near the middle of the crossing. Troy also assisted in supporting the HDD operations by providing product line string-out, testing, coating, welding, pullback pipe handling and coordination responsibilities on the Phillips 66 project. A 15-member Michels team managed all aspects of the HDD crossing installation.
The technically challenging HDD project brings the pipeline from a greenspace north of Scott Bay in Baytown to Kinder Morgan Energy Partners’ Battleground Oil Specialty Terminal Company (BOSTCO) in LaPorte.
Most practical solution
Building the pipeline by trenchless construction under the Houston Ship Channel proved to be the most feasible and timely method as attempting to install the pipeline by conventional means would have entailed disrupting one of the United States’ busiest seaports. Each year it provides passage to more than 8,300 ships carrying more than 2 million containers and is the main conduit for ocean-going vessels between Houston-area terminals and the Gulf of Mexico for domestic and international destinations. The channel also serves an ever-increasing volume of inland barge traffic, and even a minor disruption could certainly impact profits on the water.
Phillips 66 chose the designed corridor across the ship channel because it was the most direct route to connect the two terminals. By comparison, traveling by motor vehicle between the two points requires a passage of about 11 miles, including a trek across the 2.6-mile Fred Hartman Bridge. The bridge took eight years to build; Michels successfully pulled the 2.4-mile-long string of pipe into place in less than three days.
The comprehensive planning and preparation for this monstrous project took much longer – about two years as design and permitting were of primary importance. Michels strives to provide safe, efficient and dependable HDD construction services but when attempting something that has never before been done, crews have come to expect the unexpected and the outcome can be anything but predictable. With exceptional projects like this one, nothing is left to chance.
Careful planning, deployment of the most sophisticated equipment, tools and mobilization of highly-qualified professionals guarantees that the best attempt can be made for a project of this magnitude. It is only through the crew’s years of experience and dedication along with critical coordination and assistance from Phillips 66 and Troy Construction that the many day-to-day challenges presented by the unknowns on this project were safely and efficiently overcome.
Taming the ground conditions by adapting appropriate drilling parameters for the constantly changing conditions was paramount in the successful completion of the pilot hole, which had several critical brushes with failure. Phillips 66’s rapid response to facilitate 24-hour operations when the drill string torque became nearly unmanageable was a key factor in the timely completion of the pilot hole. Michels carefully employed critical drilling techniques and specialized fluid which not only allowed the pilot hole to intersect precisely on the ends near the middle of the crossing, but that also achieved full drilling fluid circulation nearly 100 percent of the time, which had previously never before been accomplished at these distances and in these ground conditions.
Due to the length and large number of pre-existing utilities already consuming available ROW space along the alignment, pilot hole intersect was the preferred method of choice for drilling. It allowed for the establishment of entry and exit points as well as more precise guidance and control in these critically volatile and congested areas. Combined, those factors allowed for a safer installation. Pilot hole intersect also alleviated concerns regarding the use of HDD construction and potential for inadvertent returns under a major waterway.
Guidance
Gyros along with other high-tech alternative steering tools were used on each of Michels’ 1.2-million-pound drill rigs to help guide critical steering along the alignment, which dipped to 170-feet below water surface of the 101-year-old Houston Ship Channel. The main channel has a maximum depth of 45 feet and a width of 530 feet. Successful completion of the pilot hole took roughly two weeks.
Once the pilot-hole intersect was completed, Michels crews meticulously coordinated reaming and swabbing activities between two drill rigs connected by a single string of drill stem almost 2½-miles apart from each other that operated continuously for 24-hours a day, seven days per week for nearly two weeks. Then, through close communication, detailed planning and careful orchestration, the expert teams of personnel from Troy Construction, Phillips 66 and Michels were able to align the 18-inch pipe string with the HDD exit, connect to the HDD pulling assembly and successfully complete the monumental pullback while overcoming three intermediate shut downs for necessary tie-in welds over a continuous 36-hour period. The ability of the persistent Phillips 66 right-of-way professionals to quickly gain access for the additional work space required to limit the shut downs to only three tie-in welds was paramount in the success of the pullback installation. The pull loads continued to increase with each of the shut downs and may have otherwise increased beyond a manageable force, had additional tie-in welds been necessary, as originally planned during pipe pullback operations.
Initially, plans called for the 18-inch product line strings to be staged in nine sections, but it was ultimately reduced to four sections (3-tie in welds) at the suggestion of Michels and the Phillips 66 ROW professionals. The green space provided an adequate laydown area for the strings and did not impede traffic or emergency services.
The massive HDD alignment traversed through various geological conditions, including sands, silts, swelling clays and marine sediments. The alignment consisted mainly of swelling clays and sands, which ranged from loose to dense.
The steel pipe string weighed 93.5 pounds per foot for total steel pipe weight of more than 1.16 million pounds. Michels’ 1.2 million-pound drill rig, dubbed Hercules, was up to the challenge of pulling back the massive string of coated steel pipe.
Drilling fluid management was critical on the project. Circulation needed to be properly maintained to allow installation, but minimize risk of inadvertent returns. Controlling buoyancy was also important.
FOR MORE INFO:
Michels Corporation, (920) 924-4300, michels.us
Troy Construction, (281) 437-8214, troyconstruction.com
Comments