March 2013, Vol. 68 No. 3
Features
Under The Pond
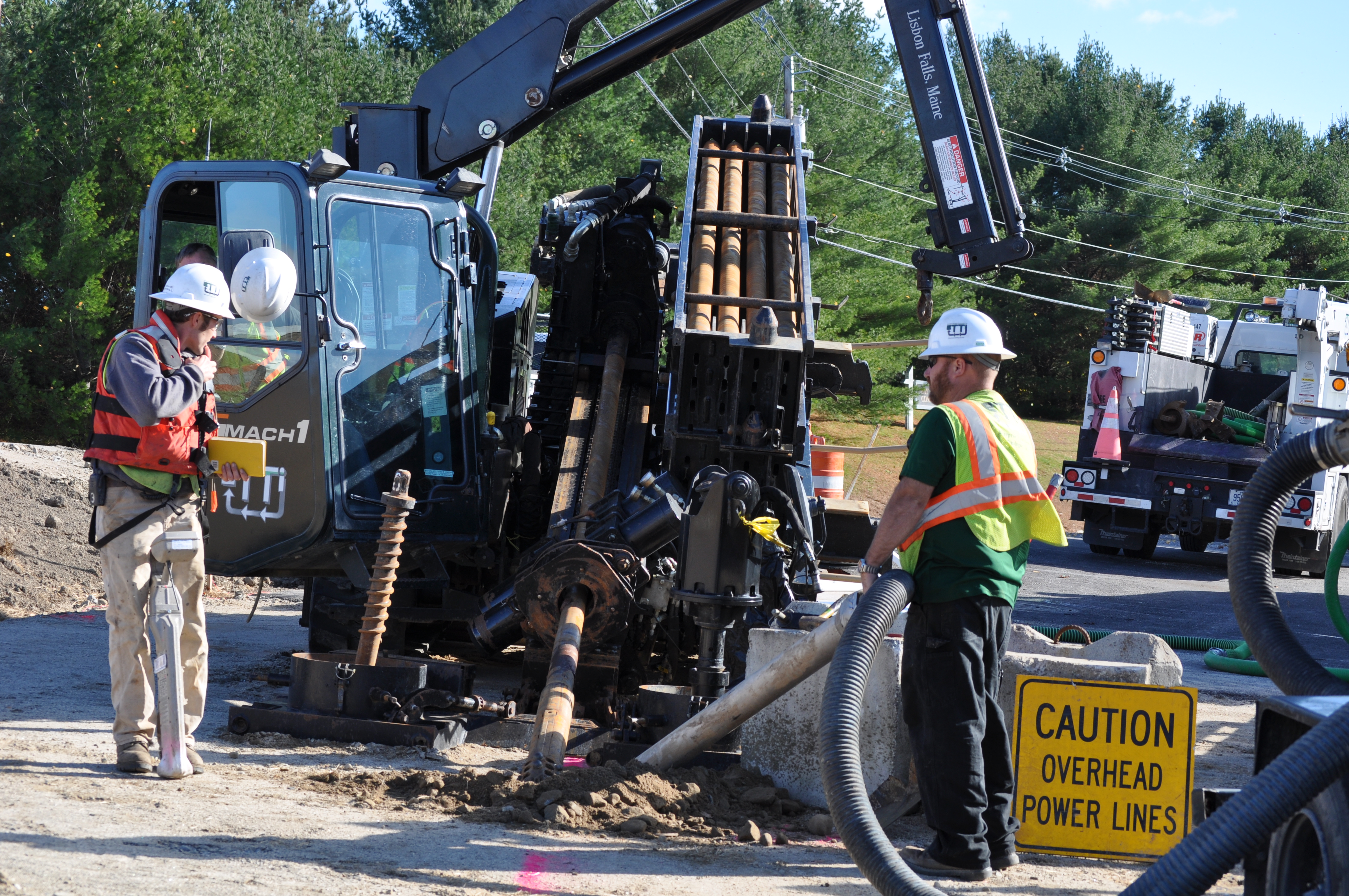
In a part of the country where rocky soils make underground construction difficult, Maine contractor Enterprise Trenchless Technologies, Inc. (ETTI) has built a solid reputation for successfully completing challenging horizontal directional drilling installations, many beneath bodies of water.
A recent project installed a 500-foot-long segment of 12-inch water main under Brandy Pond in the picturesque tourist town of Naples, nestled in western foothills of Maine. The job was a part of the Naples Causeway Restoration Project which included removal of an old draw bridge and constructing a new aesthetically-pleasing arched bridge. The water line was an important element of the restoration project because it connected the town’s fire suppression system, which previously was supplied by water from separate sources on each side of the causeway.
The project owner was the Town of Naples. Wyman & Simpson, Richmond, ME, was the prime contractor. Because the design of the new bridge could not accommodate suspending the water pipe from the bridge, it was necessary to take the pipe under the floor of the pond. Wyman & Simpson turned to ETTI to make the crossing by horizontal directional drilling.
“Directional drilling was the only feasible option to get the water line across the water,” said Scott Kelly, ETTI president.
Water crossing challenges
Water crossings always involve complications and the Naples job was no exception. Using a wireline system to track the bore path while beneath bodies of water adds cost to the job. Employing conventional walk-over trackers usually requires crew members to move along the bore path in a boat.
ETTI used a Ditch Witch JT8020 drill unit with 80,000 pounds of pullback to make the installation, setting up on the east side of the causeway in the parking lot of a marina which had ample space for the drill unit, fluid system and support equipment. The drill rig was positioned for the surface launch about 200 feet from the water’s edge.
Starting the pilot bore was delayed a day by rough waters — too choppy for the ETTI crew of two to take out their small boat to operate the handheld tracking receiver as it followed the path of the bore head. Depth readings also would be taken at various points.
Kelly said boat traffic also could cause potential complications.
“We use a guide rope stretched across the water to keep the boat on course above the path of the bore,” Kelly explained. “If another boat crossing under the causeway hit the rope, it would delay the project and potentially do damage to our boat.” ETTI’s solution was to put a team member on top of the newly-constructed bridge with a two-way radio to keep watch for boat traffic. When a boat approached, the guide rope was detached and lifted out of the boat’s path.
Another challenge was fusing 500 feet of HDPE pipe along busy Route 302 while keeping traffic flowing and businesses accessible to customers.
To avoid interference with normal activities, ETTI used two fusing crews on the side of Route 302 opposite the businesses. Two McElroy TrackStar 412 fusing machines fused the pipe.
Moving pipe
After the string of pipe was assembled, it weighed approximately 10,000 pounds, Kelly said. Personnel of Wyman & Simpson and excavating contractor R.J. Grondin & Sons helped move the pipe string across the street in front of businesses and positioned for the pullback.
“The challenge here,” Kelly said, “was to move the pipe without damaging it and to delay traffic as little as possible. To prevent disturbing a bank and newly-completed landscaping, the crews used their equipment to lift the pipe off the ground and support it during the install, leaving room for vehicles to use both the entrance and exit to businesses.”
Fusing required four hours with another hour to position and lift the pipe.
The pilot bore was completed in about five hours through sandy clay using an 11-inch Railhead bit. Bore depth under the floor of Brandy Pond was approximately 31 feet. The exit point was in a parking area on the west side of the causeway in front of a residence so access was not difficult but still tight with all of the necessary machinery.
Two backreaming passes were made with an 11-inch rock wing reamer with pipe pulled in behind the reamer on the second pass. Backreaming and pipe pull in took about 12 hours.
Once the pipe was in place, ETTI personnel installed MJ adapter kits on both ends of the HDPE pipe so that the crews from Wyman & Simpson could make their final connections with mechanical joint ductile iron pipe.
Ahead of schedule
Start to finish, the HDD installation took two and a half days.
The JT8020 drill unit is powered by a 275-horsepower liquid-cooled diesel engine. In addition to 80,000 pounds of pullback force, the machine develops 10,000 foot pounds of torque and spindle speeds to 210 rpm. For its power, the machine is relatively compact in size, and its rubber tracks enable it to travel over various surfaces, including paving, landscaped areas and rough terrain.
Tracking from the boat was done with a Ditch Witch 752 electronic guidance system. Fluid was pumped by a truck-mounted Ditch Witch FM50 fluid system. Mud from the slurry pits was removed with a Ditch Witch FX60 vacuum excavator and a commercial vacuum supplied by the Ted Berry Co.
The water line was laid in late October 2012. The original project is completed as designed and ahead of schedule, but additional work requested by the Town of Naples and Maine Department of Transportation continues. Additions include a half mile of roadway construction, installation of a fire suppression system along the entire length of the project, construction of a scenic vista overlooking Long Lake and Mount Washington, and construction of a terraced granite amphitheater. All work is scheduled for completion in the spring of 2013, still ahead of schedule for the completion of the original project.
Established in 1995, ETTI is based in Lisbon Falls, ME, and specializes in trenchless utility construction by horizontal directional drilling. Clients include gas, communications, power and water and sewer utilities along with general contractors. In addition, ETTI also installs geothermal heating/cooling systems. The company currently owns three HDD units, ranging in size from 30,000 to 80,000 pounds pullback, drilling fluid mixing systems, excavators and vacuum excavators, a variety of support equipment and vehicles to transport equipment and personnel.
FOR MORE INFO:
ETTI, (207) 353-5000, www.hdd-etti.com
Ditch Witch, (800) 654-6481, www.ditchwitch.com
McElroy Manufacturing, (918) 836-8611, www.mcelroy.com
Railhead, (888) 313-7455, http://railhead.com
Wyman & Simpson, (207) 737-4471, www.wymansimpsoninc.com
R.J. Grondin & Sons, (800) 287-1147, http://grondinconstruction.com
Comments