September 2012, Vol. 67 No. 9
Features
Energy Growth Fuels Large HDD Rig Boom
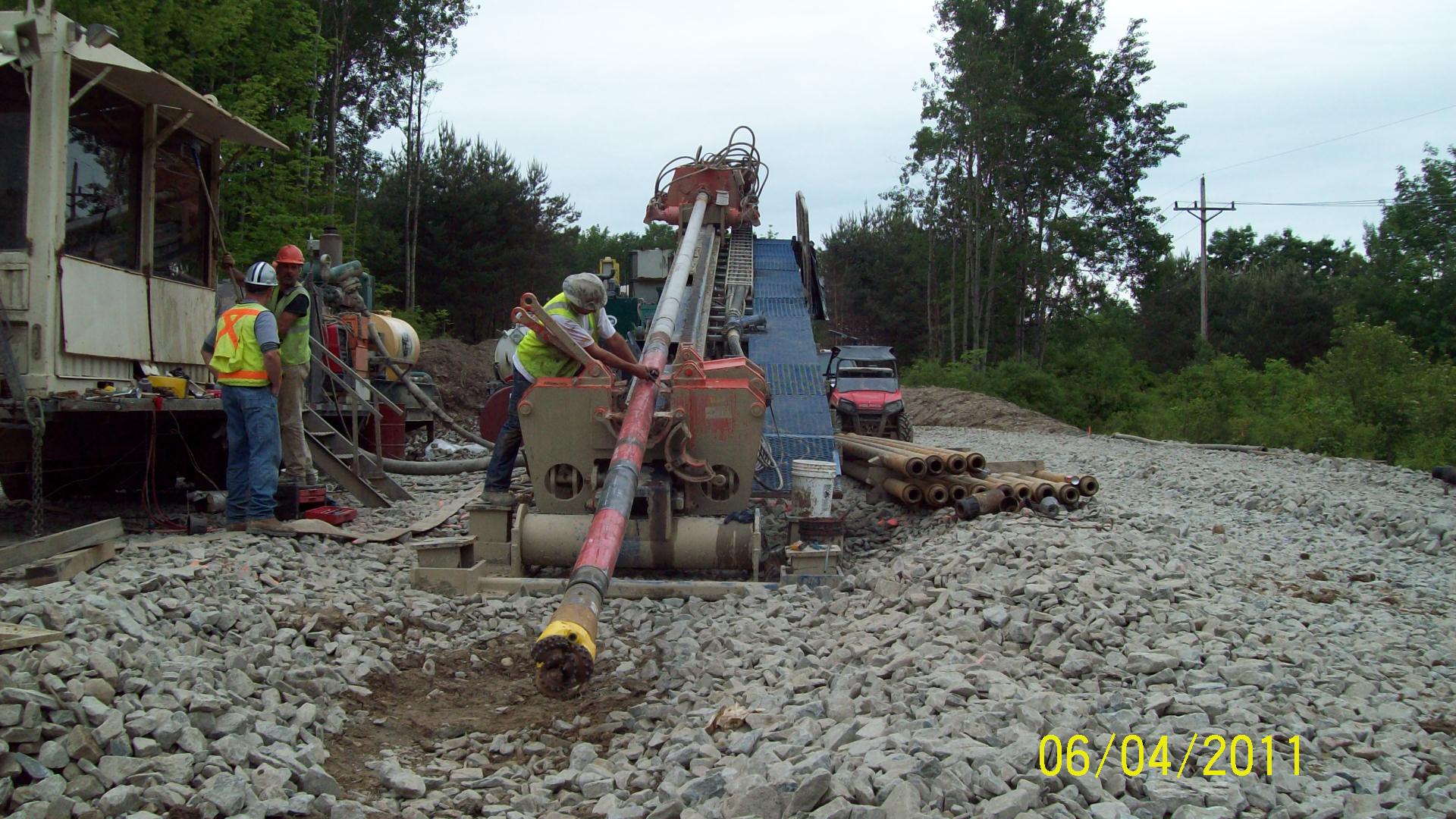
Horizontal directional drilling (HDD) as it relates to utility construction usually is dated from the late 1980s when the first compact drill units became commercially available.
As directional drilling proved its value for installing underground power and communications cable and small-diameter water and natural gas pipe, sales of directional drills increased steadily — 1,415 units sold in 1995, 2,371 in 1998 and peaking in 2000 with 3,990 drill rigs sold, most of them with 100,000 pounds of pullback or less with the greatest number in the 30,000- to 50,000-pound pullback range.
However, the roots of the HDD industry date back to the 1960s, and the first successful HDD machines were big ones for pipeline construction. These machines borrowed and adapted established oil field technology to make horizontal bores that could be directionally guided. It is generally agreed the first HDD river crossing was in 1971 when a drill unit developed by industry pioneer Martin Cherrington bored under the Pajaro River near Watsonville in Northern California.
As HDD markets expanded during the 90s, work included many projects that required big rigs, and American Augers and Vermeer marketed models that could make long, deep bores to install large-diameter product in amazingly-difficult conditions.
It is generally accepted that now is a boom time for big rig directional drilling as pipeline companies specify HDD in situations where open-cut construction is difficult or impossible. A relatively small group of HDD contractors with the experience and equipment to meet these challenges routinely complete HDD installations that a dozen years ago would have been considered impossible.
Shale driving market
Much of the newer energy projects developed in the United States are in shale fields, including Bakken in North Dakota and Montana, Eagle Ford in South Texas and the Marcellus shale play in the northeast. HDD is being widely used on Marcellus projects because much of the construction is in developed areas, and there also are environmental considerations and restrictions affecting excavation.
This report is the first in a series and will focus on projects completed by Utility Services Authority LLC (USA), Belleville, MI.
Directional drilling in Marcellus shale involves many challenges, observes Chris Lamb, USA general manager. On many projects, accessing the drill site is difficult.
“Many bores are in rural mountainous areas,” Lamb said. “The distance between a bore’s entry and exit may only be 1,000 to 3,000 linear feet, but it takes an hour to get from one end to the other. Matted roads up to a mile long are often required to gain truck access to the drill sites.”
Marcellus shale with multi-layered strata and multiple fractured formations vary in depth with hardness ranging in compressive strengths of 10,000 to 30,000 psi, he said.
“Fractured formations complicate production and increase chances of frac-outs,” he continued. “Steering through multiple layers with drastically different hardnesses is difficult and creates situations where the pilot wants to follow the path of least resistance, making it difficult to hold radius. These formations require careful downhole tool management, including inspecting drill strings and downhole tools for abrasive wear and tracking hours on tools to minimize the potential for failures during construction.”
Elevation changes pose steering challenges, Lamb added, and create mud management issues and increase the risk of frac-outs.
“Frac-outs,” he said, “can occur as far as 500 feet left or right of the drill alignment, requiring large areas to be monitored for inadvertent returns (IRs). The HDD crossings are usually under and/or near creeks and rivers that have been slowly cutting through the different layers of rock along the face of the terrain. There are seams of sediment in between layers of rock that allow the drill fluid to travel through the strata for long distances. Therefore, the drilling fluid can reach the surface at the areas where the erosion has exposed the layers along the edge of the river.”
Drill sites in wetland areas raise environmental issues, and construction and related activities have a high public profile because of controversies about natural gas collection issues.
USA’s work on HDD crossings ends with completion of pipe installation. Typically the mainline contractor welds sections of pipe together into a string for the HDD contractor to pull in and makes final connections to the mainline to complete the project.
Projects
Several recent USA projects illustrate the complexities of HDD installations in energy shale.
Project 1: Installing 1,920 linear feet of 16-inch steel pipe under low-level terrain and crossing a river.
Elevation changes: 320 vertical feet entry to exit; 420 vertical feet, bottom to exit.
Drill rig: Vermeer D330x500 developing 330,000 pounds of pullback.
Downhole tools: 9 7/8-inch TCI bit for pilot hole; 24-inch TCI hole openers for backreaming.
Guidance: The pilot hole was guided by a Tensor wireline tool and TruTracker surface grid system.
Comments: Said Lamb: “This crossing was exceptionally challenging due to a weak and open formation that drilling mud followed for over 500-feet horizontally and surfaced at the edge of a creek bed. We tripped out of the hole several times to insure the hole was clean and ended up using loss circulation material (LCMs) to reduce the volume of fluid lost horizontally.”
Project 2: Road and creek crossing to install 1,760 feet of 16-inch steel pipe.
Elevation changes: Entry to exit, 100 vertical feet; bottom to exit, 250 vertical feet.
Drill rig: Vermeer D330x500 developing 330,000 pounds of pullback.
Downhole tools: 9 7/8-inch TCI bit for pilot hole; 24-inch TCI hole openers for backreaming.
Guidance: The pilot hole was guided by a Tensor wireline tool with TruTracker surface grid system.
Comments: “The job was in a mountainous region subject to drastic fluctuations in weather due to proximity of the Atlantic coast,” Lamb said. “The set-up phase occurred during flooding caused by a hurricane and it affected fluid management and IR monitoring. The HDD installation was in the reaming stage during the flood, and there was an active IR in the dry part of the creek bed. The flooding required us to cease work operations for a week until the stream returned to its normal level.”
Project 3: Railroad and creek crossing to install 1,800 linear feet of 24-inch steel pipe. Five-hundred feet of the bore path contained cobble and boulders.
Elevation changes: Entry to exit, 45 vertical feet; bottom to exit, 130 vertical feet.
Drill rigs: Vermeer D330x500 developing 330,000 pounds of pullback.
Downhole tools: 9 7/8-inch TCI bit for pilot hole; 24- and 36-inch hole openers.
Guidance: The pilot hole was guided by a Tensor wireline tool with TruTracker surface grid system.
Comments: To successfully complete the bore on schedule, work operations ran 24-hour work days, seven days a week, Lamb said. “Due to the cobble and gravel and flowing underground water, it was necessary to maintain a continuous flow of drilling mud to lower the potential for IRs and cave in of the hole. We moved the rig pipe-side to pull ream from entry to exit to carry the gravel out the short side of the hole. Staffing and equipment issues were created by having four crews committed to the same project. From a business perspective, there is a risk factor in allocating so many resources to a single revenue source.”
Project 4: Crossing stream and state road in an environmentally-sensitive area to install 3,220 linear feet of 24-inch steel pipe.
Elevation changes: Entry to exit, 300 vertical feet; bottom to exit, 500 vertical feet.
Drill rigs: Vermeer D330x500 developing 330,000 pounds of pullback and American Augers DD210T with 220,000 pounds of pullback.
Downhole tools: 9 7/8-inch TCI bit for pilot hole; 24- and 36-inch TCI hole openers for backreaming.
Guidance: The pilot hole was guided by a Tensor wireline tool with TruTracker surface grid system.
Comments: “A pipe side rig was used to ream from the low side to the high side of the bore path to avoid push reaming and keep the right amount of force on the face of the rock with the cutter.” Lamb said. “With 300 feet vertical elevation from entry to exit, there was 1,000 feet of hole above the entry elevation. With that much dry hole, it always is difficult to clean the hole because mud outruns the cuttings. Soil boring proximity to alignment created an IR situation. This project also required four crews to operate 24-hours a day, seven days a week, bringing the same concerns regarding staffing and allocated of resources described on the previous project.”
FOR MORE INFO:
American Augers, (800) 324-4930, www.americanaugers.com
Vermeer Corp., (888) 837-6337, www.vermeer.com
TruTracker — Sharewell HDD, (281) 288-2560, http://www.sharewellhdd.com/
Comments