June 2012, Vol. 67 No. 6
Features
Managing Burst Forces
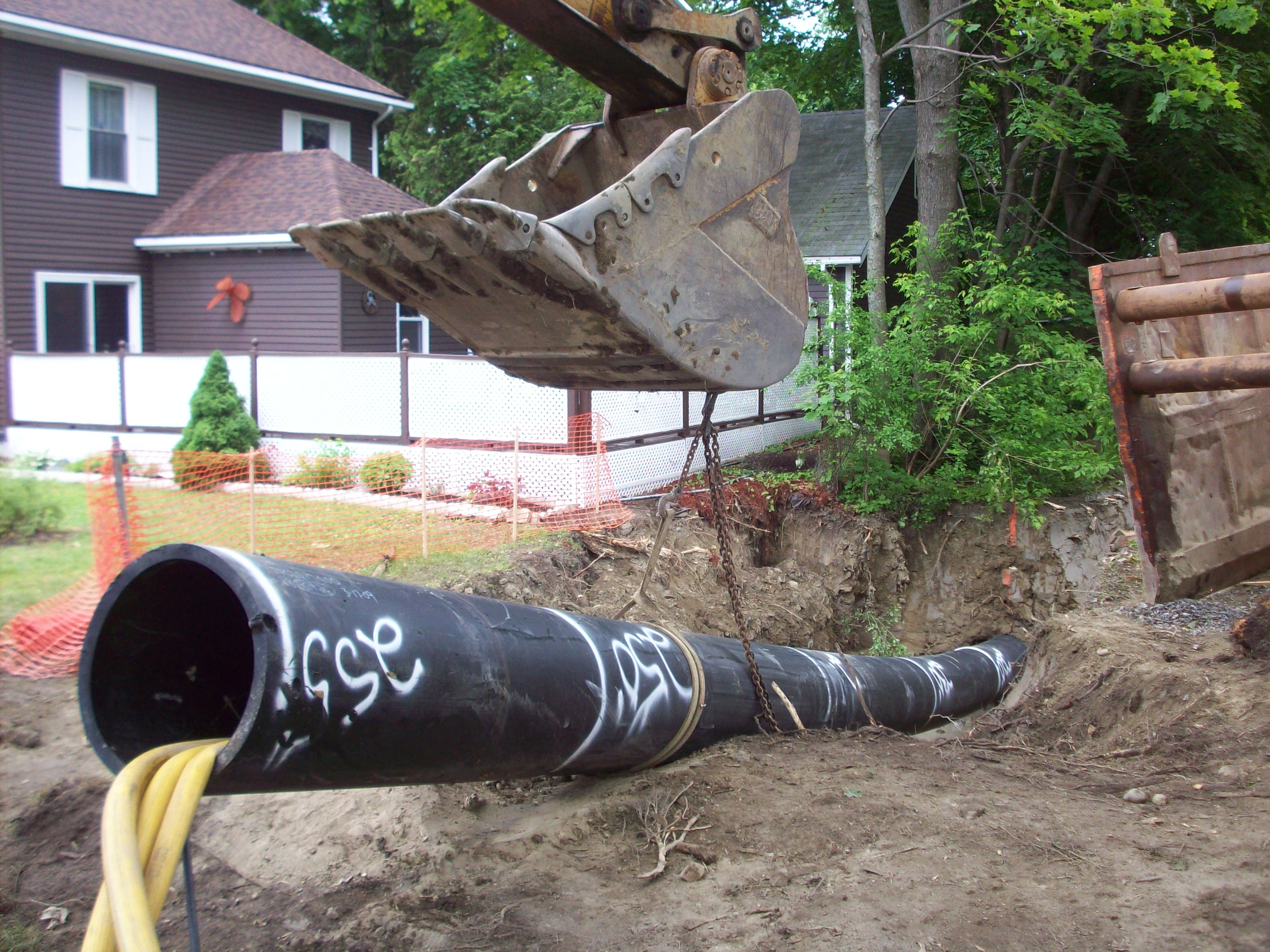
Pipe bursting is a reliable and proven method of replacement of deteriorated or under capacity utility lines. The IPBA has developed a recurring series of technical articles and this article is written with the understanding that the reader has an advanced knowledge of pipe bursting and risk management associated with a pipe bursting project.
In the July 2011 article titled :Geotechnical Conditions And How They Relate To Pipe Bursting, we discussed the three forces that must be overcome to ensure a successful pipe bursting project. Those forces for both static and pneumatic pipe bursting are:
• The force required to “split” or “burst” the existing pipe, plus;
• The force required to expand the existing soil to accommodate the new pipe, plus;
• The “drag” or friction that is being caused by the soil relaxing back on the outside of the newly installed pipe as it is pulled in place; therefore
• Burst + Expand + Drag = Total force required.
This article will focus on managing the “drag” or friction on the pipe and some of the lessons learned by IPBA members. In many pipe bursting designs the length of the pipe that is to be installed is determined by the anticipated combination of the three burst forces. By limiting the amount of drag that is placed on the pipe, the installation lengths can increase. This increases productivity and reduces impact and cost. Although there is no “rule,” it is generally accepted that lubrication is used on pipe bursting projects where the new pipe size is larger than +/- 15-inches and for lengths where the anticipated pipe drag may approach safe pulling limits.
Lubrication mixtures can be used in two ways to reduce or manage the effects of drag. By lubricating the pipe as it is installed the friction is reduced, and by stabilizing the hole it is kept in the expansion state for a longer period of time prior to relaxing back onto the pipe. A common mistake made is to use a basic bentonite mix for all installations regardless of pipe size, type, geotechnical conditions or groundwater levels. Lubrication design should be just that – a design as to what it is going to do and how the ground will react to it.
There is a basic formula to calculate the volume of lubrication required. By taking the inner diameter of the existing pipe and subtracting it from the outside diameter of the expander head, you are able to easily calculate the annular volume that will follow the burst head through the ground as it pulls the new pipe in place. Once that volume is calculated, potential fluid loss can be calculated based on type of soil and experience from a given geotechnical area. In some soils, a 1:1 ratio is used and in others a 2:1. Once volume in gallons per foot is determined, it can be multiplied by the total length of a burst to give a total volume in gallons for the burst which will need to be prepared and ready prior to installation.
Designing the mix
Once the volume is determined, the design of the mix must be planned. One of the most critical aspects of any lubrication mix is the makeup water which in many cases is pre-treated with soda ash or another additive. It is not common for salt water from coastal areas to be used in lubrication mixes; however, there are additives available that can be used with salt water. Based on soil conditions, the mix is made in most cases with a bentonite base and additives used to maximize the effects of the lube. The additives for unconsolidated soils, gravel, large cobbles and reactive clays will have contrasting materials which will affect the viscosity and ability of the lubrication to keep the hole stabilized. (See photo at head of article.)
In the field, a simple mud pump, mud mixer and supply system is attached to the new pipe just behind the expander head which injects the lube as the pipe is pulled in place.
One important factor to keep in mind is that, in many cases, some of the lubrication will flow to the insertion and/or receiving pit and may need to be vacuumed and removed from the site. Unlike with HDD where the majority of the lubrication is removed from the site, pipe bursting typically only requires enough lube to reduce friction as it is a one pass process. Disposal of the lubrication should be planned in advance and although the materials are safe for environmentally sensitive areas and drinking water applications, many people unfamiliar with the process will simply not understand that the material is not hazardous.
Many of the leading suppliers of “mud” offer schools which can train key personnel on how to design, mix, manage and confirm the quality of the mix in the field which will greatly increase the chances of successful and profitable projects. Manage your project and don’t let it manage you, good luck and happy bursting!
Coming in July: Tips from the field — how to make burst day a success.
FOR MORE INFORMATION:
IPBA (NASSCO), (410) 486-3500, www.nassco.org
Comments