September 2011, Vol. 66 No. 9
Features
Ergonomics Play Major Role With Equipment Productivity
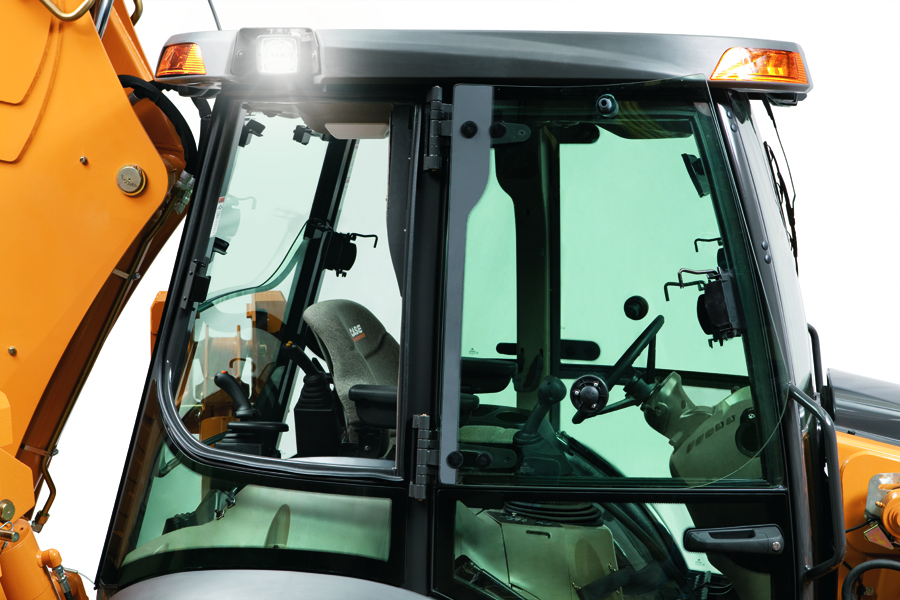
Manufacturers of construction equipment today are committed to “good” ergonomics, and they actively promote ergonomic features of their products in sales and advertising efforts.
Sales personnel and sales literature often identify specific ergonomic features and explain their benefits; other products simply are labeled “ergonomically friendly”, a description that can seem as ubiquitous relating to equipment as “all natural” is to foods.
Broadly defined, ergonomics is “the science of work,” says Prof. Alan Hedge, PhD, CPE, director of the Human Factors and Ergonomics Laboratory at Cornell University.
“For construction equipment,” Hedge explains, “ergonomic considerations involve studying what a machine will be expected to do and the places where it will work in order to design a machine that takes into account the physical and mental abilities of people who will operate it, in order to maximize the equipment operator’s comfort, health and productivity.”
In the past, Hedge says, designers of equipment followed an “outside-in” (OI) approach to design with placement of controls and the operator’s station one of the last considerations. The OI approach, he says, emphasizes engineering convenience over operator comfort, often resulting in design compromises regarding the operator work station or compartment, controls and displays.
Ergonomic design reverses this process by taking an “inside-out” (IO) approach. Designers begin with the operator compartment or work station. Controls and displays are designed for the needs of the operator — then designers work out to develop the form of the machine or vehicle.
Better approach
“The result of an IO approach,” says Hedge, “is equipment that is built around the operator’s needs in terms of anthropometric dimensions, task requirements and comfort. The goal of the IO approach is to maximize operator comfort by minimizing discomfort and accident risks, while at the same time maximizing productivity by optimizing task-cycle times, paralleling functions and maximizing vehicle usability by designing for ease of use, reduction of training time and facilitating skilled operation.”
Critical areas for ergonomic design include:
• Operator compartment or station;
• Design and placement of controls;
• Design and visibility of displays; and
• System integration to ensure all design elements must fit together.
“Ergonomic input into the design process starts with a careful and systematic analysis of equipment requirements, considers the functions to be performed, and the form of the design elements that might best achieve those functions,” says Hedge.
Equipment design is an iterative process, he continues. That is, it involves repeating a process with each repetition or iteration becoming the starting point for the next iteration.
“At each stage,” he explains, “the impact of introducing a new design feature or making any design modification to an existing feature needs to be reviewed in light of these ergonomic analysis requirements, and the impact of the changes on the operator and the whole vehicle as a system. When undertaken in this way, ergonomic design and analysis involves more than simply commenting on an existing design.”
For buyers and users of equipment, ergonomic analysis involves carefully considering the requirements of all parties involved in the purchasing and operation of the vehicle.
“A comprehensive ergonomic analysis,” concludes Hedge, “can often reveal new marketing opportunities and equipment features that can help to differentiate a machine from the competition so that it truly stands out from the crowd.”
The types of underground construction equipment in widest use today incorporated many of the ergonomic factors discussed by Hedge. Three leading manufacturers discuss ergonomics and ergonomic features of their products.
Excavation equipment
Case Construction Equipment, Tim O’Brien, marketing manager: The Case concept of ergonomics includes features that reduce operator fatigue and stress by enhancing operator comfort, safety and productivity.
The newest loader-backhoes have floor-to-ceiling windows that provide superior visibility. Near-quarter windows provide easy communication to the back of the machine and improve cross-ventilation comfort. A side lighting package helps illuminate the entire perimeter of the machine, greatly enhancing operator and job-site safety, and boosting productivity. New models include comfortable, adjustable operator seats and ergonomically placed controls along with all-season heating and air conditioning systems for increased operator comfort. At 72 decibels, the cabs are also among the industry’s quietest.
The newest compact and full-size excavators incorporate many of the same features. Compact machine cabs are larger with large front and rear windows and a slide-up front window for improved air flow and to facilitate communications with workers near the machine.
Full-size excavator cabs are larger, have improved noise reduction, and vibration refinements in the cab’s reinforced tubular structures. A rearview camera expands the operator’s visibility, air conditioning performance is improved and the standard air-suspension seat is available with optional 10 memory recall settings.
Trenchers, vibratory plows
Ditch Witch, Richard Levings, senior product manager: Despite advances in trenchless construction technologies, trenchers and vibrator plows remain fast, efficient methods of installing underground cable, pipe, duct and conduit.
The Ditch Witch conception of ergonomics as it applies to trenchers, vibratory plows, and other products is consideration of how an operator interacts with the equipment to do its intended job.
We have worked hard to make operation intuitive so that someone with little or no experience can quickly learn to operate equipment effectively. Color-coded controls are a good example. From the early days through now, the rental industry has been an important market for compact trenchers, and with many rental customers novices at using the equipment, we recognized the importance of making controls easy to understand and use. We devote a lot of engineering to make a product’s operator interface simple and intuitive.
Until a few years ago, small walk-along models had no steering control — the operator wrestled them into position in order to change the path of the trench. Power steering was introduced to walk-along models which simplifies operation and greatly reduces operator fatigue.
As trenchers and plows evolved from mechanical to hydraulic drive, the machines became easier to use because they no longer had a clutch, gears to shift and other levers to learn. A pedal controls forward and reverse motion.
On riding models, operator stations are designed for comfort and convenience with controls and gauges positioned for ease of use and gauges easy to see and read. The operator can have one hand on the wheel, the other to set and adjust depth and digging chain speeds, making adjustments as soil conditions change. Today’s machines are much easier to run. Larger models have enclosed cabs.
“Good” ergonomics helps an equipment operator be more productive and be less tired at the end of the day.
Vermeer, Jon Kuyers, product manager for utility products: Ergonomics specifically has to do with the operator’s function and control of the equipment. This means controls and the operator station should be designed to be intuitive and easy to use without stress. The goal is operator comfort, whether it is reducing the amount of repetitive operations or making the overall controls more comfortable, it needs to be easy for the operator to perform.
An example is a walk-behind trencher, which in the past was very difficult to maneuver — operators had to physically push their bodies into the machine to make it move. It wasn’t very comfortable. We improved the ergonomics of the machine by re-engineering the system to make it steerable with its handlebars without unnecessary physical effort. Most manufacturers now offer steerable walk-behind trenchers. Newer technologies offer steering capabilities without complexity or additional cost which makes these machines simpler and easier to operate. Also, there has been overall improvement in controls.
For riding trenchers, we have tried to improve the ergonomics by offering rotating operator platforms. These platforms pivot to allow for expanded visibility. The operator can see while he’s trenching without looking over his shoulder. Also control stations have improved by providing an open operating platform and utilizing electronic controls minimizing the amount of controls to engage.
However, the biggest improvement to both walk-behind and riding trenchers and vibratory plows is the transition from mechanical to hydrostatic drive systems, and it has significantly affected equipment ergonomics.
For walk-behind trenchers, it has improved controllability while providing steerable platforms that are simple to operate without the need for physical force, greatly simplifying operation.
For ride-on trenchers, new electronic controls can do much of the operator’s work. For example, a push of a button can replace a complicated shifting procedure. Open operator platforms and reduced sound level continue to be refined and improved.
Improvements in ergonomics should not be limited to looking at designs of levers and other manual controls to operate machinery. Vermeer has developed an electronic control system that troubleshoots difficult and problematic situations for the operator. Once the computer senses that the trencher is on rock, for instance, the machine will stop and back up the chain in order to get around the obstruction. This is a definite improvement in ergonomics because instead of handling many different levers and controls to get the machine out of a difficult spot, the system does the work for the operator.
Ergonomically designed equipment makes operators more productive. The work is less labor intensive, so they can get more done during a work shift. Overall, a more productive crew gets more work done in the course of a month or year, which improves the profit margin.
Horizontal directional drills
Ditch Witch, Richard Levings: When the first small horizontal directional drill (HDD) models designed for utility construction came out in the late 1980s, they brought a completely new technology. Those early machines were very primitive compared to today’s models, and they were very labor intensive.
One of the first models had control levers on the drill’s carriage. As a joint of pipe went into the ground, the operator walked along with the carriage, then walked back with it to add another length of pipe. Pipe makeup during drilling and breakout during pullback was done by hand. Crew members anchored the drill by physically driving stakes into the ground.
Equipment evolved rapidly. Operator stations had seats and controls that were arranged to be easy to access and use. By the mid-1990s, HDD machines were available with automated pipe makeup and breakout and stake down. Larger models had on-board cranes to handle pipe racks.
Advances in tracking systems improved pilot bore accuracy and remote displays became available for the driller’s station, showing drill head clock position and other information gathered by the walk-over receiver.
Much attention has been given to designs of operators’ stations and making control functions more intuitive. As the HDD market has matured the operator interfaces have followed suit. Operators spend many hours seated. To reduce fatigue, control levers, switches and gauges have all been positioned strategically to allow the operator to be very productive and comfortable. Many functions have been merged into single controls to allow the operator to reduce the movement needed to function with the systems. Hydraulically operated pipe loaders, vise wrench functions and pipe thread lubrication are processor-controlled to reduce the number of steps an operator must go through to cycle pipe. Cruise control functions have been developed to reduce operator fatigue during long time consuming backreaming operations. System status gauges are now positioned in the line of sight to keep the operator from having to reposition their body to monitor how the unit is performing.
The final product of HDD drilling systems is a long ways from being complete. The industry will continue to see ergonomic improvements that will reduce the human effort to ensure safe and productive installations of underground infrastructure.
FOR MORE INFO:
Case Construction, (262) 636-6772, www.casece.com
Ditch Witch, (800) 654-6481, www.ditchwitch.com
Vermeer Corp., (888) 837-6337, www.vermeer.com
Comments