March 2010 Vol. 65 No. 3
Features
HDD Culvert Cleaning Proves Effective
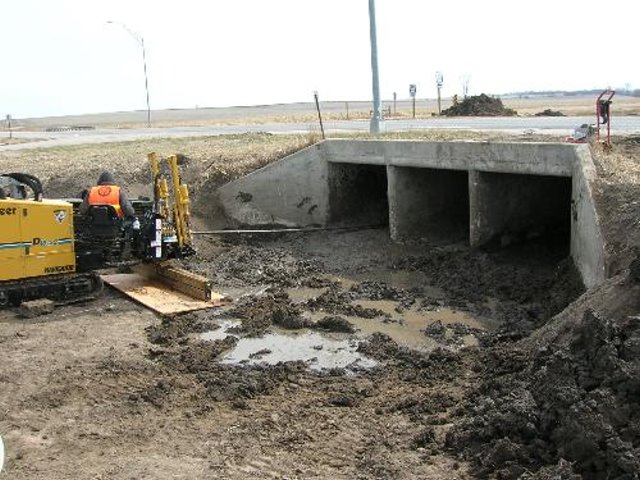
Most travelers are unaware of the complexity of engineering and constructing modern highways and streets, and many of the most critical elements that make a roadway safe and able to withstand heavy traffic for years into the future are not readily apparent.
Culverts play a vital role by carrying water under sections of roadways to prevent flooding during periods of heavy rainfall and reduce erosion of soil formations beneath and around the road’s surface.
Most culverts are relatively short in length, but often are buried quite deep. They are of various sizes and shapes, including round, elliptical and box configurations of steel, HDPE and PVC pipes and box shaped structures of concrete. But whatever the shape and material used, culverts are an integral part of a highway’s road/drainage interface.
Critical to culvert performance is keeping them free of blockages. Access often is a challenge and excavating the roadway to clear obstructions is a disruptive and costly solution. Therefore, culvert cleaning is an often neglected aspect of highway maintenance.
Bob Harr, founder and owner of Harr Technologies, Kasilof, AK, believes many culverts in the United States never have been cleaned which has resulted in damages to the structures themselves, as well as roads, ditches and other property, and can potentially cause serious injuries.
“One of the main reasons cities and highway and transportation departments have not properly maintained culverts is due to the lack of efficient and effective culvert cleaning methods,” says Harr. “Open cutting a road, jetter trucks, backhoes and cables, are methods used to clean culverts and each method has shortcomings.”
Harr has developed special downhole tools and a method of employing horizontal directional drilling (HDD) equipment for accessing and cleaning culverts that, he says, can access and clean the structures faster and at less costs than conventional methods. Harr holds patents for the downhole tools and method of using them. The Harr cleaning procedures are in use in the United States and other parts of the world, but many transportation officials responsible for maintaining culverts remain unfamiliar with the benefits.
High-profile job
To date, the system’s trenchless culvert showcase project has been on Alaska’s James Dalton Highway. The road has received wide attention from the television program, Ice Road Truckers, on the History Channel.
Basic components of Harr’s culvert cleaning system are:
• A standard HDD unit capable of meeting requirements and handling a culvert cleaning project;
• Barrel reamer to loosen and remove heavy material located in the culvert;
• Push bucket designed to push material out the far end of the culvert; It can also function as a scoop to remove material one bucket at a time;
• Pull bucket for pulling material back to the entry end of the culvert; and
• Brush for fine cleaning the culvert.
Harr said the system offers many benefits. In addition to trenchless access to the culvert, speed and efficiency head the list of advantages.
For comparison, Harr cleaned two parallel 220 foot culverts, one using his system, the other with a jetter truck.
“We cleaned the first pipe with a jetter, completing the job in 6½ hours using 1,200 gallons of water,” Harr says. “Next we used our HDD method, finishing in 40 minutes and used only 110 gallons of water.”
Reduced water requirements is a significant advantage, says Harr.
“For example,” he says, “a 60 foot culvert with a diameter of 24 inches that is 100 percent full of debris can be cleaned with our system using between 100 to 250 gallons of water. With our process, water is pumped through the HDD drill stem to the culvert cleaning tools and volume and pressure are controlled by the drill operator.”
Control
Harr says his system also provides better control of spoil than other methods.
The HDD operator controls movement of debris in the culvert. Controlled thrust and pullback allow as much or as little debris to be removed as required, allowing the spoil to be shoveled, loaded or vacuumed as it is taken from the culvert. The ability to either push or pull debris from either end also is a significant benefit unique to the Harr system.
Finally, downhole tools are built of mild steel to lessen the risk of damage to the interior of the culvert and the direction and rotation of the tool can be precisely controlled by the drill operator, who can stop immediately if a difficult blockage is encountered or when the tool passes into a void.
HDD units with pullback forces ranging from 7,000 to 100,000 pounds have been used in culvert cleaning projects, depending on job requirements.
“A smaller barrel reamer is the first tool into the culvert that checks integrity of the culvert and loosens soils for removal,” says Harr. “Next, a pull or push bucket is used to remove debris. Whether it is removed from the access or exit point, often depends on requirements to preserve wetlands or stream flows.”
A box structure cleaning tool is used for removing large volumes of material. When cleaning is completed, spoil removed is spread over the job site area or loaded and trucked away, depending on individual job requirements.
“We have developed more than 290 varieties of cleaning tools,” says Harr “Some soils need water to help remove debris from the drainage structure. But there are jobs where use of water is prohibited, and our system can work without water which keeps the site cleaner and limits cross contamination during rehabilitation. Of course, jetters use water for cleaning and cannot be used in such situations.”
Most culverts in the United States are 24 to 36 inches in diameter, Harr said.
“Lengths,” he continues, “range from typical 40 foot road crossings to four lane highways which are 200 feet. In good weather, a 36 inch diameter culvert, 40-foot long can be cleaned in about 40 minutes. However, we have completed several jobs that were 2,500 feet long.”
Market need
Harr believes there is a great, largely untapped need for the culvert cleaning system. Compared to conventional cleaning methods, Harr said one of the greatest benefits of using the system is the reduction of costs relating to construction of detours, traffic control, restoration of job sites when construction is complete, especially in environmentally sensitive areas, and permitting.
An agreement has been reached with the Robbins Company to manufacture Harr downhole tools and sell the products in Alaska, Harr says. Previously Vermeer distributors sold the products which helped the cleaning process gain exposure and recognition as a viable alternative to convention culvert cleaning procedures.
In other areas, qualified contractors may apply for a license to use the Harr system and purchase downhole tools from authorized distributors.
Harr says culvert cleaning with the Harr system is not suited for every contractor.
“We recognize that only qualified contractors with the proper training should undertake culvert cleaning services with the Harr system,” he explains. “The licensing requirement assures project owners the contractor is qualified to perform the work. In other markets, improper use of HDD technology has had a negative impact on the technology, and we want to avoid that.”
Harr is enthusiastic about the future. “Our research documents indicate there are hundreds of thousands of culverts in the United States that need immediate cleaning,” he says. “Our system provides a new application for HDD equipment that can safely and quickly restore culverts and save tax payers millions of dollars.”
Developing A New Method Of Culvert Cleaning
With experience in various types of construction including mining and pipelines, Bob Harr, now owner of Harr Technologies, Kasilof, AK, was operating a construction company specializing in underground telecommunications power construction in the late 1990s.
As the telecom building boom slowed, Harr began investigating other markets they could serve, especially any which could benefit from using horizontal directional drilling technology.
Alert to new opportunities, one day Harr, living in Colorado at the time, observed a crew cutting a road to reach a culvert buried under the road to remove obstructions that had stopped the flow of water. The work was slow and difficult, interrupted the flow of traffic, and it would require street repairs after the culvert was cleared.
Further investigation by Harr revealed that clogged culverts were a problem nationwide. Many culvert failures, he found, were attributed to inadequate or often no maintenance. He learned, also, that methods used to clean culverts were not effective in many situations. At short time later, Harr had become a self educated expert in culvert maintenance and cleaning.
It became clear to Harr that HDD provided a way to access blockages in culverts, and he began developing specialized downhole tools that could clear blockages and remove the debris in less time than conventional methods. The new tools and the method of using them were extensively tested and improved. He began calling on highway department and railroad officials to present information about his new culvert cleaning process. Harr has called on the DOT in every state explaining the system and its benefits and urging that it be approved for use.
Harr became a member of the American Railway Engineering and Maintenance of Way Association (AREMA) and the Transportation Research Board (TRB). He was invited to make a presentation at a meeting of the American Association of Highway and Transportation Officials (AASHTO).
Following that meeting, an AASHTO representative from Alaska invited Harr to that state to evaluate culvert problems there. He recognized an opportunity to develop trenchless culvert technology in extremely challenging soil and weather conditions.
Meeting with engineers, Harr began taking on culvert cleaning projects from large primary contractors. After his system proved effective in cleaning culverts with diameters to four feet and at distances exceeding 200 feet, the Alaska State Engineer asked Harr whether his system could address a collapsed section of the James Dalton Highway. That led to Ice Road Trucker highway project, completed November 2009.
FOR MORE INFORMATION:
Harr Technologies LLC, (907) 262-6710, www.harrtech.com
Comments