September 2009 Vol. 64 No. 9
Features
Mobile Port Project Requires Massive Underground Electrical Installations
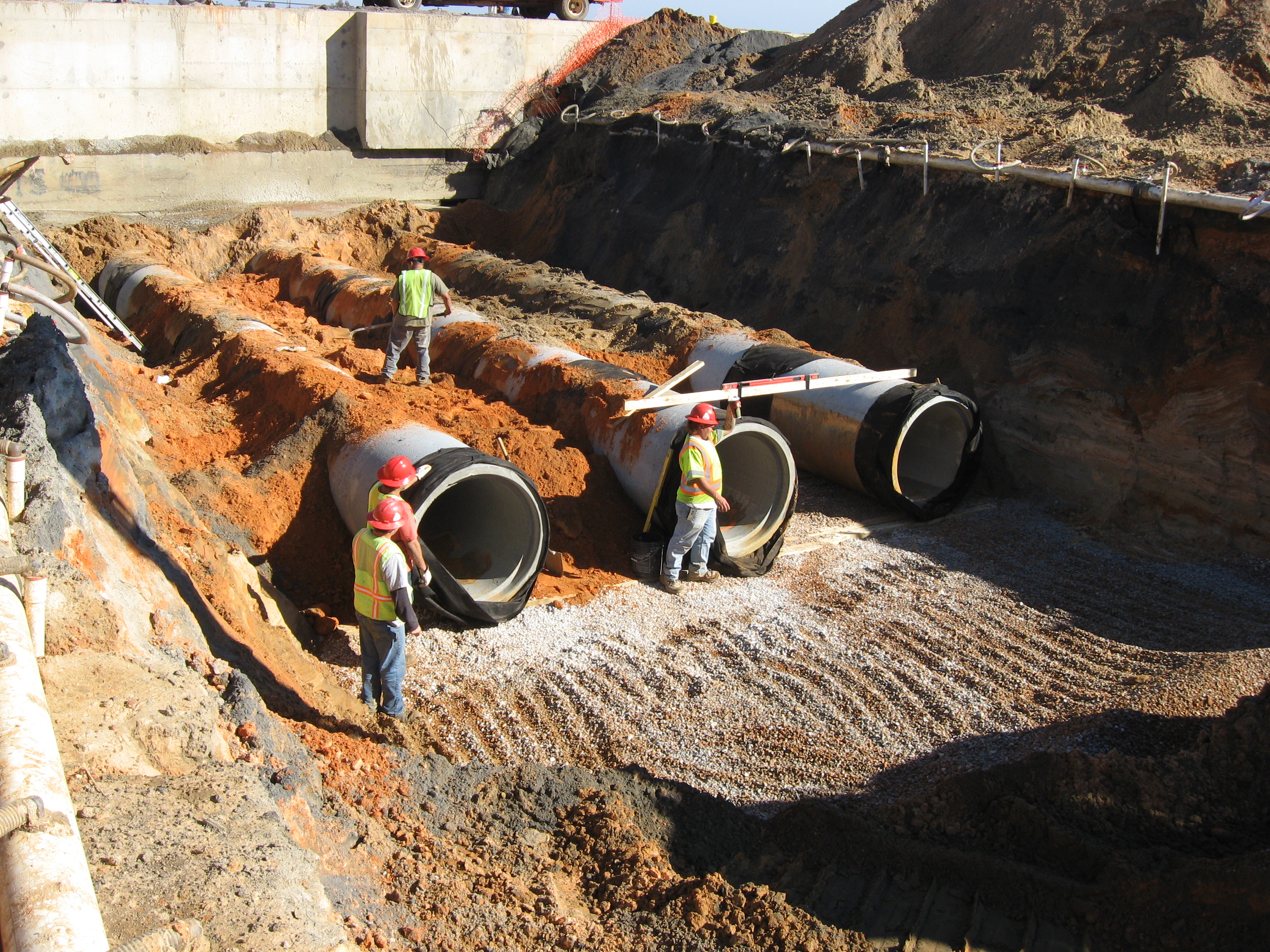
Shipping has played a key role in growth of Mobile, AL, since its establishment more than three centuries ago. Situated next to a deep bay that is well suited for a port and harbor, early settlers received goods carried by ships from Asia, Europe and other parts of the world.
At the beginning of the 21st Century, Mobile was ranked as one of the 10 busiest ports in the United States. With the opening in late 2008 of the Mobile Container Terminal (MCT), the port’s capacity to handle containerized cargo increased substantially.
“The opening of the Mobile Container Terminal makes the Port of Mobile very competitive with neighboring Gulf ports,” says Brian Clark, the facility’s director. “The significant increase in capacity has encouraged additional steamship lines to add Mobile to their rotations.”
The MCT’s two giant cranes dominate the Mobile waterfront. Each is 240 feet high and 90 feet wide with a 150 foot long boom, and the capability of reaching across the width of 18 containers on board a vessel and are classified as Post Panamax ship to shore cranes, meaning they are capable of unloading or loading containers from ships too large to pass through the Panama Canal.
As are most cranes of this size, MCT’s cranes are powered by electricity for efficiency and because it is significantly “greener” than diesel power which releases carbon into the atmosphere.
Prime general contractor for construction of the $90 million project was R.B. Baker Construction Inc., Garden City, GA.
Any facility the size of MCT’s requires large volumes of dependable electrical power, but with the two cranes depending on electrical power for operation, it makes the performance of the electrical system even more critical. The electrical contractor was Bagby & Russell Electric Company Inc., Mobile.
“All electrical components of the terminal are underground,” said Albert Hensley, Bagby & Russell vice president and project manager. “No component of the electrical infrastructure is above ground. All power loops are redundant, with two loops for each feed. If one feeder develops problems for whatever reason, there is another complete loop for back up, and the result is no interruption of normal services.”
Electrical installation
Electrical construction included electrical duct banks, vaults, distribution substations, 25kv facility power and 15kv crane power with a redundant power system for each crane, and high mast and perimeter lighting.
Vaults, duct banks and feeders in the underground system are like spokes from the hub of a wheel going out from the center to various locations and substations, said Hensley.
The project was designed to be completed in phases, beginning with underground work, followed by substations, cable pulling, termination and installation of lighting.
“To support the fully grounded installation, all distribution cable was placed underground in 42 miles of PVC conduit,” Hensley said. “The electrical engineer made the decision to use Schedule 40 PVC glue joint pipe in the specs for the high durability and the wall thickness to be able to handle the friction of the wires being pulled. At just over 2,000 feet, the crane feeders were the longest.”
Conduit duct banks were installed first so site paving could take place.
“All conduits were installed in open trench,” said Doug Beasley, project manager, R.B. Baker Construction. “Seven excavators were in operation at one time, including two Volvo 330s, and one each Volvo 290, Volvo 460, Caterpillar 325, Komatsu 200 and Komatsu 300.”
Trench depths ranged from four to 25 feet with water a continuing problem.
“Because the terminal is within arm’s reach of Mobile Bay,” Beasley explained, “water was encountered in any cut beyond three to four feet in depth. For water issues, we used well pumping systems, thousands of feet of sock pipe and multiple trash pumps.”
Special PVC
One hundred percent of the Cantex conduit installed was four and five inch diameter Schedule 40 PVC pipe in 20 foot sections. All electrical duct banks were stacked in PVC chair supports with rebar cage surrounding the entire duct bank totally encased in 3,000 psi red dye concrete.
“The project,” Beasley said, “required a lot of coordination with owner supplied materials, including the cranes which were shipped from overseas and had to be transferred to the wharf for operations. The first stage was to install power to the cranes and next, power to the buildings. The facility included new administration and maintenance buildings which were not part of our contract, and that required a lot of coordination.”
RJ Baggett Inc., Mobile, was the subcontractor that performed all excavating and concrete operations associated with the electrical work and other areas of the site, including all concrete pads for the substations, reefer areas, inbound and outbound gates and K rail barriers.
“After underground work was complete, multiple crews of electricians worked simultaneously on other portions of the project,” Hensley said. “Each substation was lifted from a delivery truck by a crane and placed on the concrete pad and anchored to the pad.
To help keep the excavation phase on schedule, the 29 vaults were placed underground and prefabbed 20 foot sections of PVC conduits were stubbed into the vaults and connected to the duct banks. GPS readings were taken of the vault locations because the vaults were eventually completely covered by the concrete. Later the GPS readings were used to locate the underground vaults, and concrete saws were used to cut through the paving to access manholes.
Electricians were provided confined space entry training before working in the underground vaults and also had to be instructed and certified to operate motorized lull fork trucks used to move materials throughout the project site. Training included lockout and tag out procedures.
High mast lights consisted of 19 sectional metal poles, 120 feet tall; 2 sectional metal poles 100 feet tall and 21 sectional metal poles 60 feet tall. Fixtures are 1,000 watts each 10 for each of the 120 and 100 foot poles and two each for the 60 foot poles. Total wattage for the high mast poles is 252,000 watts.
“Installation of the light poles is routine for contractors experienced in this work,” said Hensley. “It is simply assembling sections of the poles, standing them upright with a truck crane, securing them to pole bases, and making terminations.”
For a project of this magnitude, Hensley said work proceeded smoothly, and unexpected events were handled without causing a delay in completion.
Unexpected interruption
The work schedule was interrupted just over a month before the target completion date when an oil spill on the Mississippi River closed operations at the Port of New Orleans. The two Mobile cranes were powered up early to accommodate a ship rerouted from New Orleans. Areas in the construction zone were secured and containers offloaded at MCT in order to keep the delivery of imported goods on schedule. The overall project work schedule was changed to 10 hour days, six days a week.
After the Port of New Orleans reopened, the original construction schedule was resumed, and the interruption did not delay the facility’s grand opening ceremonies.
The high mast lighting was needed for the ceremonies, but the completion of the substation to power them originally was scheduled in Phase 2. Bagby & Russell devised a reconfiguration of the substation feeders and moved forward to power up the lighting substations for the grand opening.
R.B. Baker also installed a storm drainage system that includes 13,716 lineal feet of storm drainage reinforced concrete pipe (RCP) in diameters of 12, 15, 18, 24, 30, 36, 42, 48, 60 and 84 inches. Beasley said 99.9 percent of the drainage pipe was at a 50 percent slope. Two outfalls discharge into the Gulf of Mexico – one 84 inches in diameter through a bulkhead, the other a triple 42 inch outfall. In addition, 4,960 linear feet of trench drain was installed.
“R.B. Baker topped off the 95 acre site with 403,000 square yards of 6 inch soil cement with 110,000 square yards of 15½ inch and 293,000 square yards of 8 inch roller compacted concrete (RCC),” Beasley added.
The Mobile Container Terminal is a public private partnership between the Alabama State Port Authority and Mobile Container Terminal LLC, a joint venture between APM Terminals North America and Terminal Link, a subsidiary of CMA CGM, a leading global container shipping carrier based in France. The facility is operated by Mobile Container Terminal.
Founded in 1920, Bagby & Russell is a full service electrical contractor serving Alabama, Florida, Mississippi and the Louisiana Gulf Coast. Bagby & Russell typically self performs 100 percent of all phases of electrical installations.
R.B. Baker Construction Inc. is a heavy-highway general contractor engaged in construction of highways, landfills, site development and other related construction projects for both public and private sectors. The company operates primarily in the southeastern United States.
RJ Baggett Inc. is a general contractor specializing in industrial buildings and warehouses.
FOR MORE INFORMATION:
Cantex, (817) 215-7000, www.cantexinc.com
Bagby & Russell Electric Company, (251) 344-5987, www.bagrus.com
R.B. Baker Construction Inc., (912) 964-6513, www.rbbaker.com
RJ Baggett Inc., (251) 473-3290, www.rjbaggett.com
Caterpillar, (309) 675-1000, www.cat.com
Komatsu, (847) 970-4100, www.komatsuamerica.com
Volvo, (825) 650-2043, www.volvo.com
Comments