May 2009 Vol. 64 No. 5
Features
Complications On The Rio Grande
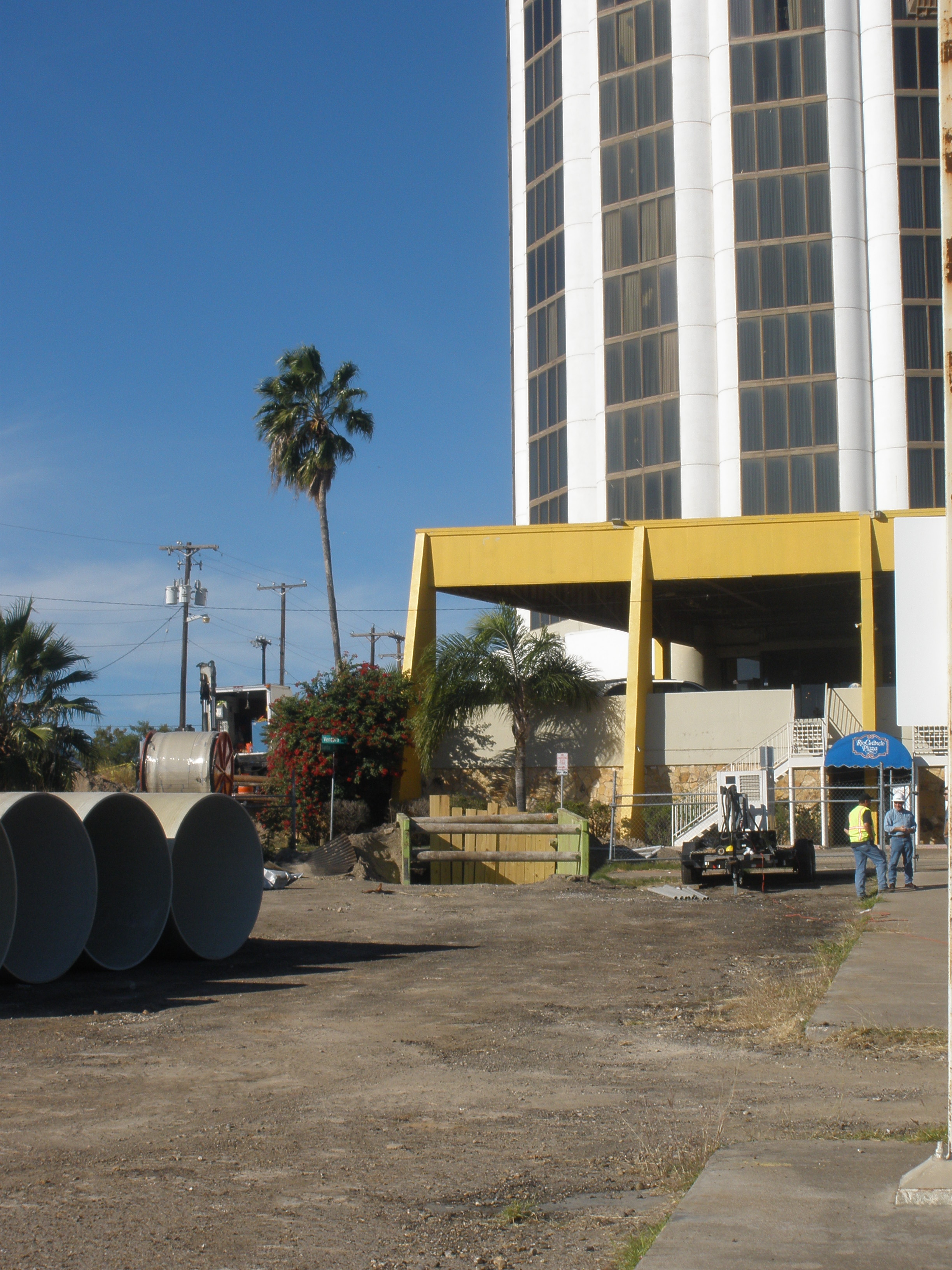
Repairing or replacing old, deteriorating utility infrastructure that has been buried in the ground for years and often directly beneath homes and businesses is a challenge that has become common for the nation’s utility providers.
Indeed, site conditions often make it impossible to make excavations to install new pipe, leaving rehabilitation the only construction option. Fortunately over the past decade, technologies have advanced to the point that rehabilitation often is the most cost effective method of construction, regardless of surface conditions.
The population of Laredo has grown steadily over the past decades, more than doubling between 1969 and 1990 and reaching more than 217,000 by 2008. One result of this growth has been a strain on the city’s storm sewer system, requiring significant improvements. Commercial and residential developments, and in some cases encroachments to storm water easements, has complicated the problem.
A recent project to rehabilitate approximately 1,100 feet of 120 inch outside diameter corrugated metal pipe (CMP) storm sewer trunk line is an excellent example of how trenchless rehabilitation technologies can be utilized. On this project, there also were potential environmental issues because a portion of the site had once been a landfill. Therefore, it was important to limit excavation during construction, and trenchless methods allowed that to be accomplished.
The rehabilitation process reduced the size of the pipe from 114 inches inside diameter to 78 inches, while maintaining capacity due to improved flow characteristics of the structural liners.
“The CMP storm sewer was constructed more than 30 years ago and serves an extensive drainage system through an older section of the city of Laredo near the Gateway to Americas International Bridge which is one of the city’s five international bridges to Mexico,” said Temple Williamson, P.E., CFM, project engineer, Lockwood, Andrews & Newnam Inc. (LAN), engineering firm for the job.
“The project,” he explained, “addresses many utility and environmental issues among which is crossing a former landfill area where the existing storm sewer has a cover depth of more than 20 feet below the surface along certain sections of the project. The existing storm sewer line also transverses densely compacted residential and commercial areas including the Rio Grande Plaza Hotel, a Laredo landmark, before the line outfalls into the Rio Grande River. Additionally, numerous public facilities would be impacted by any open cut construction.”
Fix, don’t replace
A preliminary analysis, said Williamson, determined that the most cost effective solution would be to rehabilitate the existing line rather than removing and replacing it.
“The project,” he continued, “presented several challenges, including installing a structural liner in the existing line and the use of trenchless construction methods for rehabilitation which included sliplining fiberglass reinforced plastic (FRP) and spiral wound high density polyethylene (HDPE).”
The project required a special outfall design at the Rio Grande in order to comply with U.S. Department of Homeland Security (DHS) requirements. Special provisions were incorporated into the project to address these concerns and minimize impact to local residents and retail businesses.
Ultimately, the decision was made to use two different sliplining methods to rehabilitate the old pipe. General contractor was Huff & Mitchell, Inc., Cypress, TX. Glen Crawford was project manager. Boring & Tunneling Company of America (BorTunCo), was the contractor for sliplining.
Construction was scheduled to begin on the lower section with sliplining of approximately 300 feet of Flowtite glass fiber reinforced thermosetting polymer mortar pipe (FRP). Because the area is in a flood plain of the Rio Grande River, work was scheduled to begin after the end of normal “wet” season, which had been dryer than usual. FRP pipe was chose for the lower segment because it was anticipated the 20 foot sections of pipe could be installed very quickly in case rain did come.
Although the area had been dry preceding the projected starting date of construction, heavy rains came about the time work started, delaying the project from the beginning.
Wet woes
About the time water in the river began to recede, more water came unexpectedly. The Mexican government owed the United States water that it had borrowed during previous drought periods, explained Williamson. With the approval of the International Boundary and Water Commission (IBWC), Mexico released water from dams upstream of the project, and water remained at a level too high to permit construction.
“We considered a coffer dam, but it was determined that would require too much time,” said Williamson. “But the water did drop, and we resumed work. The FRP section was cleaned quickly by BorTunCo and 4 inch PVC runners were attached to the host pipe on each side at the 5 o’clock and 7 o’clock positions. This facilitated pushing the 20 foot joints the entire length of the lower section of the project by hand.”
All FRP was installed from one insertion pit in one week and then grouting operation began.
“Due to the large annular space, a special grout technique was borrowed from large diameter tunneling experience,” Williamson said. “This technique used gravel to fill the void on each side of the liner holding it in place and then using grout to complete the operation.” Williamson added that the ease and speed of insertion and grouting helped assure the project’s success by relieving concerns about another unexpected rise in the level of the Rio Grande.
For the upper portion of the project, approximately 800 feet of Sekisui RibLoc spiral wound HDPE liner was used. This segment of host pipe had more than 25 feet of cover.
A continuous strip of highly stiff, low-weight plastic liner was spirally wound into the host pipe by the hydraulically self running winding machine that interlocks the strips of the liner as it advances forward, forming the structural liner. The winding machine rotates around a frame that bends the steel reinforcement which is built into liner. After the host pipe has been lined, the winding machine is disassembled and removed through the access pit. With this process, an exit pit is not needed.
“The spiral wound pipe process provided the ability to slipline the pipe’s difficult vertical transitions and horizontal bends and transitions without the use of fittings,” explained Williamson. “In addition, the use of spiral wound pipe reduced the number of access shafts that would have been necessary with other methods of construction, allowing the hotel in the project area to remain open.”
Mega-void complication
During construction of the upper segment, “a large 20 by 20 by 15 foot void was discovered above the host pipe,” he said. “It was caused by erosion of a 60 inch CMP connected to the host pipe from above by a vertical 90 degree bend. The lower section of the 60 inch pipe had completely corroded away, allowing the storm water to erode the bedding around the pipe and creating the giant void.”
The void was near the hotel under a street intersection which could have potentially caused a catastrophic collapse of the street above.
“The intersection was immediately closed and the pavement was removed to fill the void and replace the lateral based on a design developed by LAN’s engineering team,” said Williamson. “Lining of the host pipe was completed to keep the pipe structurally secure while the void was filled with backfill and the lateral replaced.”
The void repair required about two weeks.
Relining of both segments was completed in approximately six months and in spite of the early delays, the unanticipated void repair and other complications, work was completed on time and within the contract amount.
Reflecting on the project’s importance, city of Laredo Director of Environmental Services Riazul Mia, P.E., CFM, said: “The goal of the project was to preserve service of the storm sewer system and to prevent a catastrophic failure of the existing trunk line. The use of the trenchless rehabilitation for the section of storm sewer minimized impact of the construction phase to the surrounding area and resulted in a timely and cost saving delivery.
“Additionally, the material properties for the fiberglass and spiral wound PVC pipes that were used provided for structural support and maintained capacity of the existing storm sewer with a reduced diameter.”
As Laredo’s infrastructure programs continue, LAN has been awarded a contract to design a 42-inch storm sewer, which includes rehabilitation of a 24-inch segment with illegal connections to the sanitary sewer system. Construction is planned to begin in the fall of 2009.
Lockwood, Andrews & Newnam is a national engineering firm offering planning, engineering, and program management services. As a subsidiary of Leo A. Daly, one of the largest planning, architecture, engineering and interior design firms in the United States, LAN has access to the expertise of more than 1,100 professionals in 25 offices in 21 cities worldwide.
Huff & Mitchell specialize in water and sewer utility construction.
Established in 1948, Boring & Tunneling Company of America is experienced in all types of tunneling and boring methods serving a wide range of clients throughout the United States and internationally.
FOR MORE INFORMATION:
Lockwood, Andrews & Newnam (LAN) Inc., (713) 266-6900, www.lan-inc.com
Sekisui SPR Americas, (678) 510-1820, www.sekisuispr.com
Boring & Tunneling Company (BorTunCo), (713) 799-1200, www.bortunco.com
Huff & Mitchell, (281) 304-9100
Comments