June 2009 Vol. 64 No. 6
Features
Centralizer Increases Production Rates, Extends Life Of Other Tools
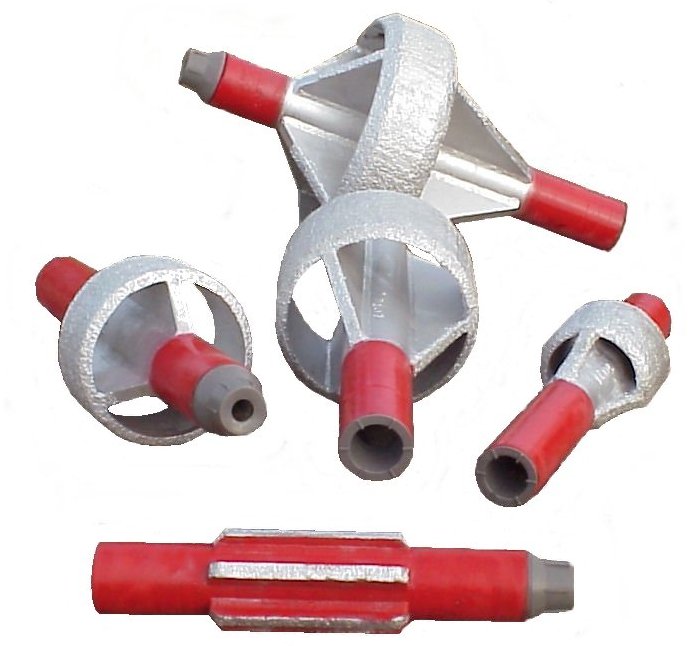
Downhole tools are critical components of the horizontal directional drilling (HDD) process—no project can be completed without them. The wrong tools for soil conditions can result in excessive equipment wear and slow production—or even make it impossible to complete a job.
Drilling heads and bits, backreamers, couplings, drill pipe and other downhole tools comprise a highly competitive market with pros and cons of various products discussed and debated. However, one sometimes overlooked is the centralizer. When added to the bottom hole assembly and used correctly, a centralizer provides several benefits that lower the overall cost per foot of an installation.
“The centralizer is a tool that is overlooked in many bottom hole assembly designs,” believes Danny Crumpton, technical sales manager for Inrock, a supplier of centralizers and other HDD products and services. “The fact is, this tool is one of the most important for keeping cost per foot at its lowest.”
Crumpton said centralizers are designed specifically for HDD applications.
“Centralization in front of the hole opening assembly symmetrically aligns cutters in the center of the pilot hole against the rock face, ensuring the cutters evenly engage the pilot bore as drilling progresses, providing a smooth round bore hole,” said Crumpton. “The proper use of centralizers increases hole opening production rates and extends the life of cutters and hole opener bodies.”
Contractor observations
Many failures in reamer bodies such as broken legs that attach the cone to the reamer body and loss of cones in the hole, can be attributed to not properly centralizing downhole tooling, believes Keith Whitaker, president/owner of Trans America Underground Ltd., Flower Mound, TX.
“One thing that is very important,” Whitaker pointed out, “is getting the correct diameter of centralizer down hole. If it is not the right size for the material being cut it can act as a wedge and build up material in front of it. Tool design will help eliminate such buildup issues.”
Boyd Simon, division manager for Ranger Field Services, Broussard, LA, says his HDD crews use centralizers any time they drill in rocky conditions.
“A centralizer keeps the downhole cutting tool from wobbling or bouncing around the hole,” he says. “A centralizer reduces the chance of tool damage in such conditions and keeps cones and cutters constantly cutting to create a circle shaped hole, not one that is egg shaped because the tool moves around.
“Stabilizing the tool is not as critical in the gumbo we encounter in Louisiana, but when we’re in rock, we use a stabilizer for backreaming every time we pass through the hole.”
Crumpton said centralizers generally are available in sizes ranging from 9 3/8 to 60 inches. He said that some manufacturers use oil field designed centralizers.
“Some HDD designs,” he continued, “have three or four legs to support the outer centralizer ring, usually containing jet nozzles to keep the tool clean of debris that sometimes can clog the area between the ring and the body. Bladed centralizers can work in hard rock, but not soft soils. Generally, most centralizers are similar in design, some with jets, some with a larger diameter ring thickness, others using inserts or a combination of both.”
Tilt-a-whirl
Crumpton compares a hole opener’s performance without a centralizer to “tilt a whirl” rides once popular at fairs and carnivals.
“The hole opener will bounce from one side to the other side of the bore hole,” he said. “This causes the cutters to always be skidding, making them become drag cutters.
“With the hole opener being slammed into the sides of the bore, it will always keep the cutters from being evenly and properly loaded. Due to the weight of the drill string, the hole opener will always be tilted away from the centerline of the bore causing a wobble as the tool is rotated. This wobble effect will not allow the weight to be transferred from the tooth insert to the rock efficiently. The rock will not be fractured as it should be. The effect of not centralizing includes premature and extreme body wear, shortened bearing life, broken inserts and poor bore hole geometry. The rate of penetration will not be as good as it could be. The efficiency of production will be lower.”
By centralizing the reamer body, Crumpton said the reamer stays more stationary while rotating and will help align the reamer with the face it is cutting by reducing the weight of drill string which can pull down. The wobble effect also is reduced.
Another benefit of centralization is reducing the chance of “tear drop” holes, that can occur when a series of passes are made that cut lower in the formation because the tool has no centralizing support.
Crumpton equates effective use of centralizers to an art.
“In some instances, centralizing in front and behind the hole opener is recommended,” he said. “Experienced drillers develop an understanding of what a job requires. During push reaming, centralizing behind the hole opener will help with weight on bit and tool life. Not centralizing will cost money due to the premature wearing out of the cutters and tooling. New tools have to be rented or purchased and there will be freight added to that. The tool will need to be repaired if it is a rental tool. Centralization will not protect a hole opener 100 percent, but it will allow the tool a chance to achieve its maximum potential.”
FOR MORE INFORMATION:
Inrock, (713) 690-5600, www.inrock.com
Comments