July 2009 Vol. 64 No. 7
Features
Working Through Challenges, Clay Pipebursting Project Exceeds Expectations
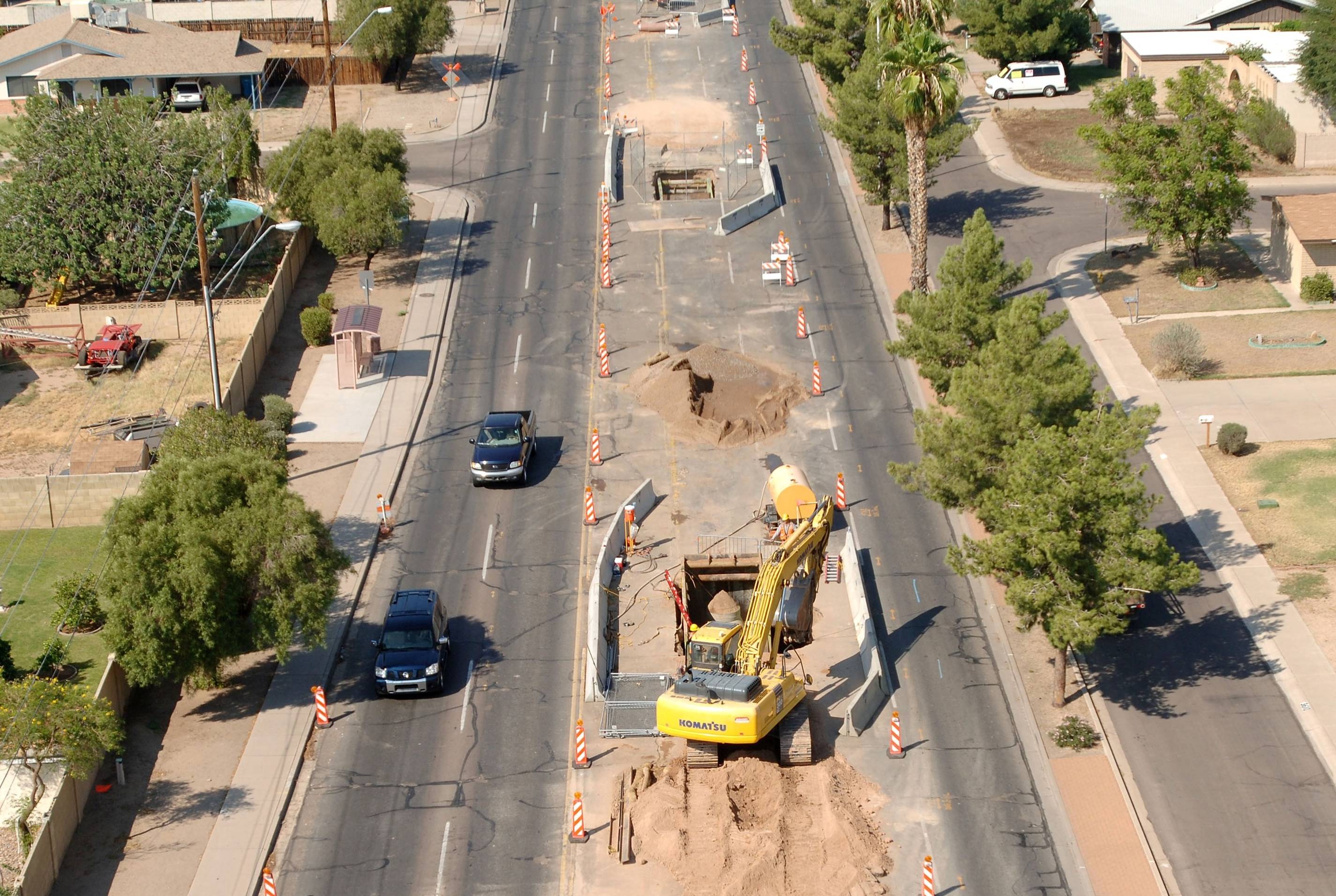
As are many American cities, Phoenix, AZ, is facing the need to make major improvements to its sanitary sewer system.
Rapid population growth, recent mandates from the state environmental quality department and aging portions of infrastructure have resulted in portions of the city’s wastewater collection system being near or above capacity.
Because sewer system capacity deficiencies could have a negative impact on the area’s economy, the Phoenix Sanitary Sewer Relief and Replacement Program was established to address these and other issues.
One recently completed improvement was a pipebursting project using vitrified clay (VCP) jacking pipe that included replacing 3,938 feet of existing 12 inch VCP with 18 inch VCP, replacing 2,525 feet of 15 inch VCP with 18 inch VCP, and replacing 720 feet of 12 inch VCP with 15 inch VCP. The existing sewer line’s capacity had been exceeded due to growth in the service area.
“To our knowledge, this represents the most significant upsizing and maximum drive length ever completed in the United States using the static pull bursting method with replacement segmental pipe,” said C.J. Haas, P.E., resident engineer, Project Engineering Consultants Ltd., engineers for the project.
The utility corridor encompassing the existing line was congested with other utilities making open cut construction challenging, Haas added. The existing pipe was bedded in a soft, dry silty sand material and installed in a trench with widths ranging from three to 5 feet, depending on pipe depths which ranged from 10 to 20 feet. Other utilities were adjacent to the pipe.
Open-cut alternatives
The goal of planners, Haas continued, was to consider alternatives that would minimize the conventional open cut construction headaches such as impeding traffic, impacting local business and customers, and ultimately provide a solution less costly and disruptive. Trenchless pipebursting was ultimately chosen to upsize capacity deficient pipes without trenching.
“Pipebursting has been used in the Phoenix area in the past,” said Haas, “and while clay pipe had been used as replacement pipe years ago, most recent pipebursting jobs were done with pneumatic heads and HDPE pipe. Static bursting is different, and some of the depths on this project were at the edge of what we had experienced.”
The use of pipebursting provided a relatively small job site footprint, and Haas said utilizing segmented pipe eliminated the need for a long lay down area on the project site that would be required with welded pipe.
“This is highly beneficial in high traffic urban settings as long strings of welded pipe would have inhibited traffic flow and driveway access before and during the bursting operation,” he said. “As a result, traffic was not impacted as much during the pipebursting operation.”
Kiewit Western was the contractor for this phase of the work with a GMP (guaranteed maximum price) of $5.3 million.
All existing utilities in the pipe zone were identified and marked on plans including fiber optics conduits and electric duct banks which were potholed and surveyed, waterlines, telephone conduits, natural gas lines, storm drain connectors and sewer lines. Potholing of electrical utilities was performed during design. In addition to potholing, soil borings were collected every 150 to 200 feet along the pipe’s route.
“Soil boring data is very important for pipe bursting and bore and jack projects to determine feasibility,” Haas said. “Soil classification, size and density are of particular importance.”
Before pipebursting could begin, two 12 inch HDPE bypass lines – one strictly a backup – were constructed to carry sewage flow during construction. When driveways were encountered, the bypass pipe was trenched under and paved over to allow property owners to have full access at all times. Existing pipe was cleaned and inspected by closed circuit television (CCTV) to ensure there were no severe alignment problems or sags. Also, CCTV was used to locate all existing service laterals which were intercepted, monitored during the operation, and connected into the sewer bypass system which ran adjacent to the pipe being burst.
VCP
Based on previous experience with a number of pipe line materials, the city of Phoenix preferred the use of VCP, Haas said. The Mission Clay No Dig jacking pipe used on the project uses resilient gasket material and stainless steel collars at each low profile compression joint to provide a leak free system. A chipboard compression ring distributes jacking forces from one section of pipe to the next.
Haas said because of the strain on the pipe joint during the installation process, the decision was made to use a double fin elastomer gasket with a five inch width, 13 gauge (0.09) inch stainless steel collar over the standard for 18-inch pipe which utilizes single fin elastomer gasket coupled by a 4½ inch width, 16 gauge (0.06 inch) stainless steel collar.
The bursting equipment was a TT Technologies Grundoburst 2500G static bursting machine with a pulling capability of up to 315 tons. The machine utilizes Quicklock rods between the machine and the expander, sized for the pipe being installed. For this project, rods were connected to a special 24 inch outside diameter expander sized for the 18-inch VCP. The expander had an internal socket arrangement for the lead piece of VCP to butt against.
Launch and receiving pits were constructed at new manhole locations at intervals of approximately 400 feet. Trench boxes were used to stabilize the walls of the pits to provide a safe working environment and allow ample room for equipment and pipe. The bursting equipment could easily be rotated 180 degrees in the launching pit to launch bursting pipe from the opposite direction.
Summary
A technical paper prepared by Project Engineering Consultants, the city of Phoenix Water Services Department, National Clay Pipe Institute and TT Technologies, states:
“The bursting equipment for this project was designed and assembled for the specific purpose of bursting the existing VCP and towing in the new non restrained joint jacking VCP. Because the pipe sections are compression fit joints, a bursting system was built to push each pipe joint “home” as well as to keep the column of assembled pipe sections in compression during bursting. A ride-along hydrostatic machine (cylinder pack) attached to bursting rods inside the new pipe sections kept the column of assembled pipe segments in compression as the bursting progresses. The pipe sections were lowered into the pit and the pipe joints were pushed home with the cylinder pack via pressure plate. The cylinder pack provided 40 tons of force to keep the assembled pipe segments in compression and rods in tension as the bursting head is pulled toward the static pipebursting machine. As the bursting head is pulled forward, fracturing the existing VCP and expanding the fragments into the surrounding backfill, the rear cylinder pack pressure plate keeps the assembled pipe sections in compression,” the summary states.
“As the pull progressed, additional rods were added, followed by the pipe sections which were slipped over the rods. A cylinder rack with three pressure plates was then employed and pinned to the rods. Next, the plate was hydraulically energized to serve two functions: to push the newly added pipe joint fully into place, and hold the entire jacking pipe train in compression as the pipe bursting expander was pulled forward by the 2500G machine.
“In one portion of the installation, alignment problems were encountered with an existing 40 year old, six-inch water main composed of asbestos cement pipe (ACP) which meandered adjacent to the sewer alignment. The ACP water main began breaking at multiple locations apparently due to pipe movement caused from soil displacement during the pipe bursting operation. The city decided to relocate the entire portion of the ACP waterline which was within six feet of the existing sewer pipe. The decision to relocate this existing water line would have been the same if an open cut construction method was elected over pipebursting. There were no other major conflicts with utilities and no service disruptions during construction, and all utilities that were in pit areas were supported and maintained at all times during construction.
“Production rates were affected by unknown conditions such as a cementitious cap, dry dense soil conditions adjacent to the existing trench, and the existing sewer pipe alignments.”
Fast turnaround
Haas said the project was completed in nine months, including all pipebursting and one jack and bore segment.
“Production via pipebursting exceeded everyone’s expectations,” he said. “The contractor estimated that the project would have taken at least 12 months to complete if it had been open cut. Static pull segmented pipebursting technology using clay jacking pipe proved to be very successful and cost effective for upsizing a capacity deficient sewer.”
In addition to actual construction cost savings, pipebursting on the project did not interrupt sewer services which were maintained by bypass pumping operations. Pavement removal and replacement costs were reduced by approximately two thirds as only the bursting and receiving pit excavations required pavement removal and replacement which reduced disruption of traffic and inconvenience to local residents and businesses.
FOR MORE INFORMATION:
Project Engineering Consultants (PEC): 602-906-1901, www.pecaz.com
TT Technologies, (800) 533-2078, www.tttechnologies.com
National Clay Pipe Institute, (262) 248 9094, www.ncpi.org.
Mission Clay No-Dig Pipe, (210) 863-3350, www.no-dig-pipe.com
Kiewit Western, (303)979-9330, www.kiewit.com
Comments