May 2024 Vol. 79 No. 5
Features
Trenchers: Unsung hero of utility installation
By Amy Olsen
(UI) — Trenching, with its versatility and adaptability, remains a vital method for utility installation across various terrains and conditions. The wide array of trenching machines and attachments available today allows for efficient and effective utility installations, from small residential projects to large-scale industrial applications.
The ability to customize these machines to specific project requirements is a testament to trenching’s enduring relevance in the construction industry. As new technologies emerge and industry demands evolve, trenching continues to stand strong as a reliable solution for utility installation.
Today, trenchers are commonly utilized for long-distance installations in rural areas with fewer restoration requirements and are also commonly used for essential utility installations in residential and commercial settings. They are also employed for longer, more complex projects and prove effective and reliable for utility jobs in challenging rocky grounds.
Moreover, trenching is often the preferred method for installing new utilities in greenfield development projects, where existing underground infrastructure might be limited or non-existent.
Various trencher types, sizes
The term “trencher” refers to various types of dirt-digging machines. While some models are strictly built with a boom-and-chain, many can be outfitted with different attachments.
Trencher equipment varies in size, ranging from small 13-horsepower walk-behind models to massive 600-horsepower units. The larger models can cut a ditch 14 feet deep and 48 inches wide. Many models are also designed for different depths, widths and soil types, suitable for working and installing utilities.
Starting with smaller trenchers, pedestrian, walk-behind and walk-beside variants are excellent for installing small-diameter utilities at shallow depths. These machines are often used to lay fiber, water, irrigation and gas lines over short distances in residential neighborhoods.
“Small trenchers and vibratory plows excel at residential work,” said Nick Olsen, product manager at Vermeer. “They are the overlooked machines that deliver fiber to homes worldwide.
“And much of the industry prefers smaller tracked models that can fit through tight gates, while still having enough counterweight and stability for cutting a trench for lines to be laid. Vibratory plows are ideal for working in softer soil conditions. In comparison, combo units provide more versatility for contractors working in harder conditions or need to bury product deeper in the ground.”
“Ride-on tractors” is a term often used in the industry when discussing mid-sized utility trenchers; most machines in this category can interchange attachments. They usually work over longer distances in softer soil conditions like clay and loam. This category of trencher is often used for installing fiber, underground distribution electrical lines and connecting solar farms and wind turbines to the electrical grind.
Used for cutting deep and wide trenches in hard clay and rocky ground conditions, these impressive machines can help optimize crews’ production by installing large-diameter casing and HDPE pipe at deeper depths. This is often required for performing electrical connections on renewable energy projects, as well as pipeline work for oil and gas, water and sewer, and the hardening (undergrounding) of electrical distribution lines.
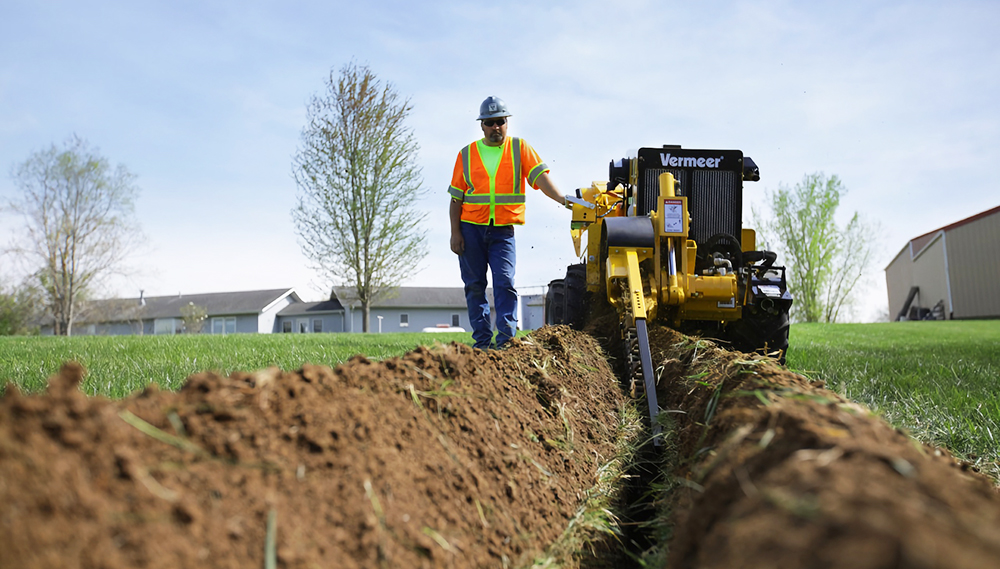
Selecting size, configuration
Small walk-behind and walk-beside trenchers can dig trenches up to 42 inches deep and 6 inches wide. Utility ride-on tractors with trencher attachments can dig twice as deep and wide. Large trenchers, with varying boom lengths and chain configurations, can reach depths of 15 feet and widths of 4 feet.
While these specifications are crucial for determining the appropriate size of trencher for a project, ground conditions also play a significant role.
“In challenging ground conditions, such as rocky terrains, a larger trencher that can produce more torque is necessary for effective ditch cutting,” Olsen explained. “More torque is also needed for digging deeper and wider ditches.
“However, high torque levels result in greater fuel consumption. Therefore, choosing the largest trencher model for every project is not always beneficial. Instead, opt for a trencher model that strikes a balance between productivity and operating efficiency.”
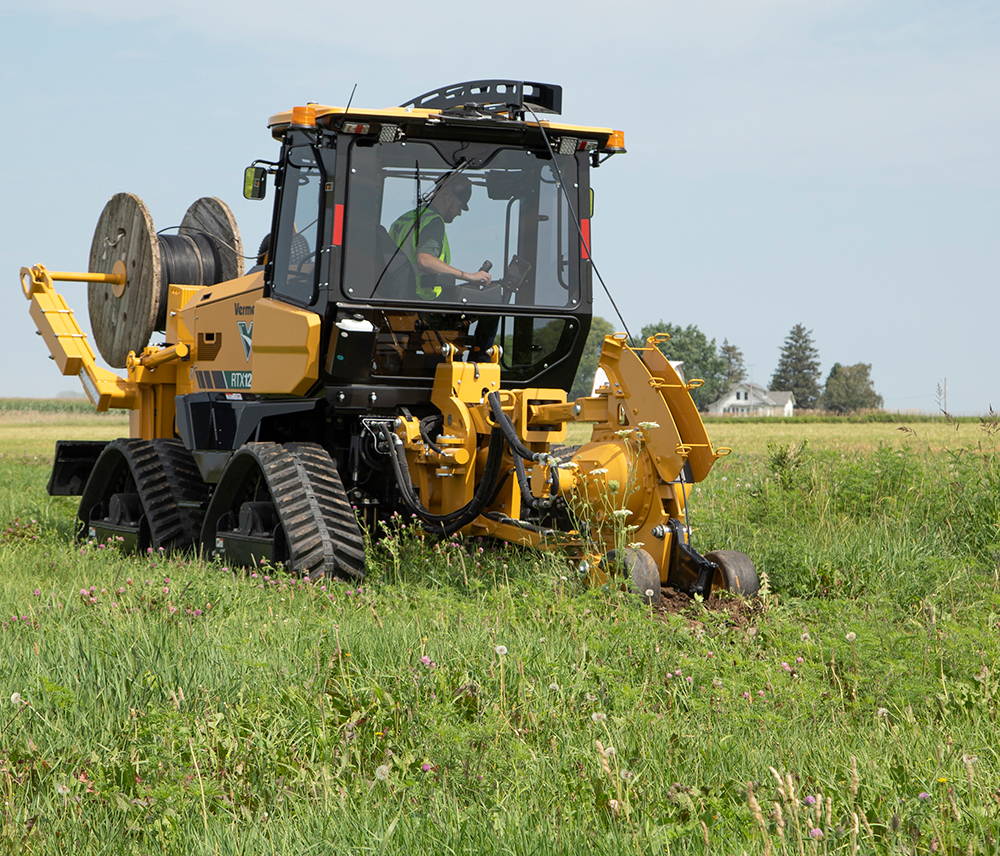
Attachments
As stated before, small trenchers are typically equipped with either a chain-and-boom trencher or a vibratory plow, and some units even come with both. Other accessories for these units include a backfill blade and a Porta Bore attachment, which is used for going under sidewalks and driveways.
A big advantage for ride-on tractors is that they can be outfitted with multiple attachments, making them ideal for contractors who take on a variety of tasks. In addition to conventional chain-and-boom trenching attachments, many models can be easily adapted with a vibratory plow, microtrencher or rock-wheel for cutting trench. In addition, contractors can add an auger/boring attachment, backhoe, reel carriers and trench backfill blade attachment.
“For direct bury or small poly conduit in soft/loamy soil conditions, a vibratory plow is typically the fastest installation up to around 42 inches in depth,” Olsen said. "The product is usually installed in a single pass, and much less restoration work is required afterward.”
However, there are limits to how much a vibratory plow can do. Some plows can go deeper than 42 inches, but the soil conditions have to be ideal, and the size of the tractor required to pull that deep may make it a less efficient option at that point. Plows also have a more limited trench width than trenchers.
Chain-and-boom trenchers come in a broader range of sizes, adapt better to various applications, can dig deeper and handle a wider range of soil types than vibratory plows.
“While trenching will work in a greater range of environments and project types, the overall process takes longer than plowing,” Olsen said. “Trenching jobs require more restoration work after the product is in the ground, and contractors may need to bring in additional equipment to complete that portion of the job.”
Microtrenching is beneficial for fiber or small conduit jobs, as it can often be more cost-effective and time-efficient than horizontal directional drilling. A microtrencher is used to open a narrow and shallow trench in an asphalt roadway, usually in the seam between the asphalt road and concrete curb/apron. With many cities witnessing crowded underground rights-of-way, microtrenching allows contractors to help avoid other utilities, and future repairs to damaged lines can be easier to access.
Additionally, if a crew is working on rock, its productivity may increase by using a rock-wheel attachment to cut a trench.
Large trencher attachments
Large trenchers are renowned for their versatility. They can handle different types of excavation using rock-wheel and bucket-wheel attachments, which optimize digging in various ground conditions and product types.
Rock-wheel attachments often come into play in utility installation work in rocky terrains or when teams need to cut through concrete or asphalt.
“In solid rock, where smaller utility-sized rock wheels may struggle, it becomes necessary to upgrade to a rock-wheel attachment designed for use on larger, more powerful trenchers,” said Gregg Van Roekel, applications specialist, Vermeer.
Bucket-wheel attachments, on the other hand, are ideal for highly productive trenching in soft soil conditions.
“A bucket wheel features a series of buckets rotating in a circular motion to assist in moving more dirt from the trench,” Roekel added. “This trencher configuration is ideal for installing fiber, electrical lines, water and sewer pipes and tiling in agricultural applications.”
Further, a large trencher can be customized with different boom-length options and chain configurations to optimize trenching performance from one job to the next. Also, a loading conveyor can be added to many large trencher models on projects where new fill may be required, or a job site lacks adequate space for excavated material. This optional attachment allows the loading of excavated material directly into the back of a dump truck, eliminating the need for additional equipment.
While trenchless installation methods like horizontal directional drilling garner significant attention for their role in installing underground utilities, trenchers continue to play an indispensable part in the process. With a wide range of trencher models and ground-engaging attachments available to cater to different project requirements, trenching will continue to be the backbone of the underground utility market.
FOR MORE INFORMATION:
Vermeer Corp., (888) 837-6337
Comments