June 2024 Vol. 79 No. 6
Features
Drilling under the LSU campus
By Jeff Griffin, Senior Editor
When the horizontal directional drill (HDD) technology for utility construction applications became practical, one of the primary benefits of using this trenchless technology is its ability to put pipe and cable under the ground and significantly reduce surface damage. That, in turn, reduces restoration costs.
The importance of minimizing surface damage still applies and a project on the Louisiana State University campus, in Baton Rouge, is a good example. The job included installation of two 1,600-foot segments of 42-inch diameter HDPE pipe by directional drilling. One was a chill water line, and the other was a return water line.
The overall scope of work for this project was to modernize the LSU chilled water supply and return process throughout the entire campus, said Donnie Braud, president of L.S. Womack Inc., the contractor responsible for underground construction on the project.
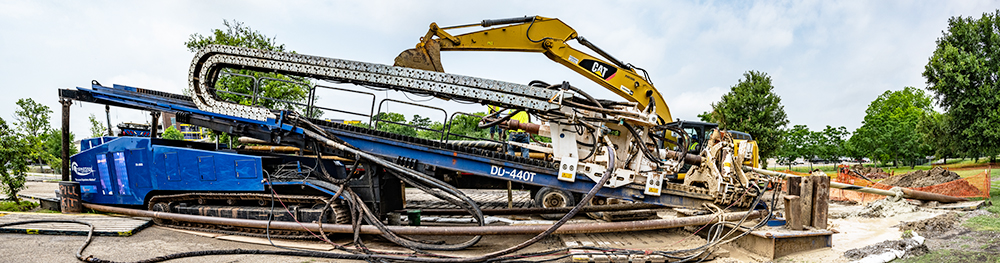
“Many construction disciplines from different companies contributed to the success of this project. “Commercial, electrical, mechanical, control and heavy civil construction companies are working together on different phases of the construction to complete the overall goal, which is to provide LSU with a new energy efficient utility system,” said Braud.
“That included updating and adding onto the existing chilled water supply plants, as well as increasing capacity of the underground supply and return transmission lines throughout the campus’s footprint.”
LSU was the project owner. Tiger Energy Partners (a Bernhard Energy & Johnson Controls joint venture) and CenTrio entered a 30-year partnership, in which Tiger Energy Partners will construct the new energy-efficient utility system for LSU’s main campus. Upon completion, CenTrio will manage the operation of the new facilities.
L.S. Womack was contracted to complete the underground piping installation for the overall initial modernization project. Spartan Directional installed the HDPE segments via HDD.
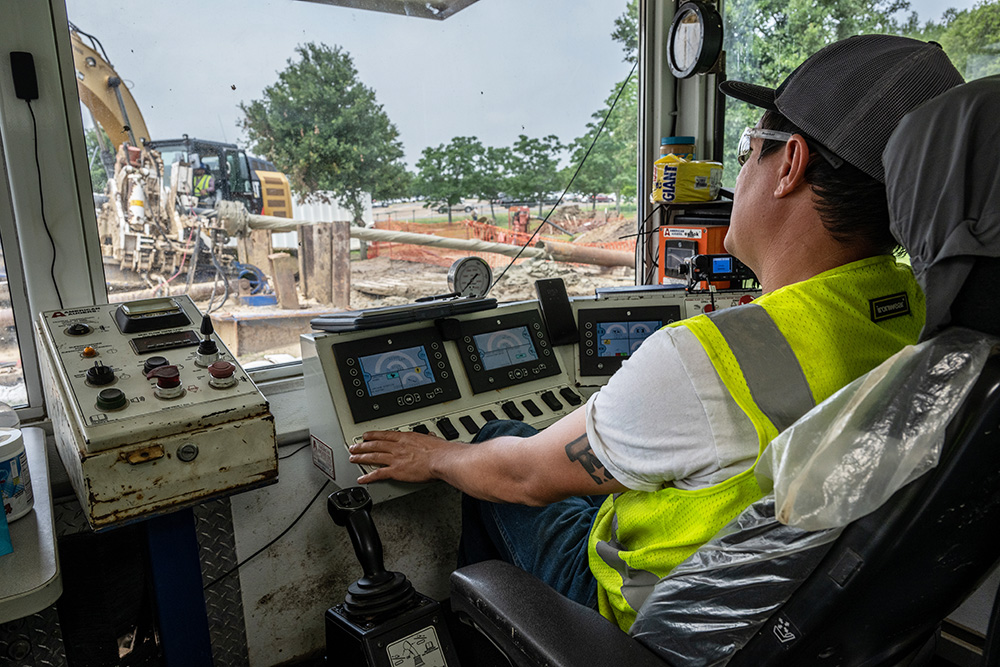
Enhancing water capacity
Braud said the project to increase the capacity of the main supply and return lines required the installation of two 42-inch HDPE pipes using HDD. Tiger Energy Partners contracted L.S. Womack to complete this scope of work due to its experience managing and completing bores of this magnitude. L.S. Womack has a long-standing relationship with Spartan Directional, the subcontractor to complete the two 1,600-foot drills of 42-inch HDPE SDR 9 pipe.
“LSU’s main campus is home to many historic oak trees that must be preserved during this underground construction process,” Braud continued. “The routing of the pipe also had to be in close proximity to existing structures and many high-traffic areas throughout campus.
“In order to minimize the disruption to campus activities, HDD was chosen for the installation of the two lines that would have required a much larger construction footprint if conventional mechanical excavation methods were utilized.”
Spartan Directional Manager Boyd Simon, P.E. said the two bores of 1,600 feet were made with an American Augers DD-440 which has a pullback rating of 440,000 pounds. A Brownline guidance system was used to guide the bore path and an American Augers MCD 1000 cleaning system was utilized. Bentonite was used to help remove cuttings and keep the cut hole open.
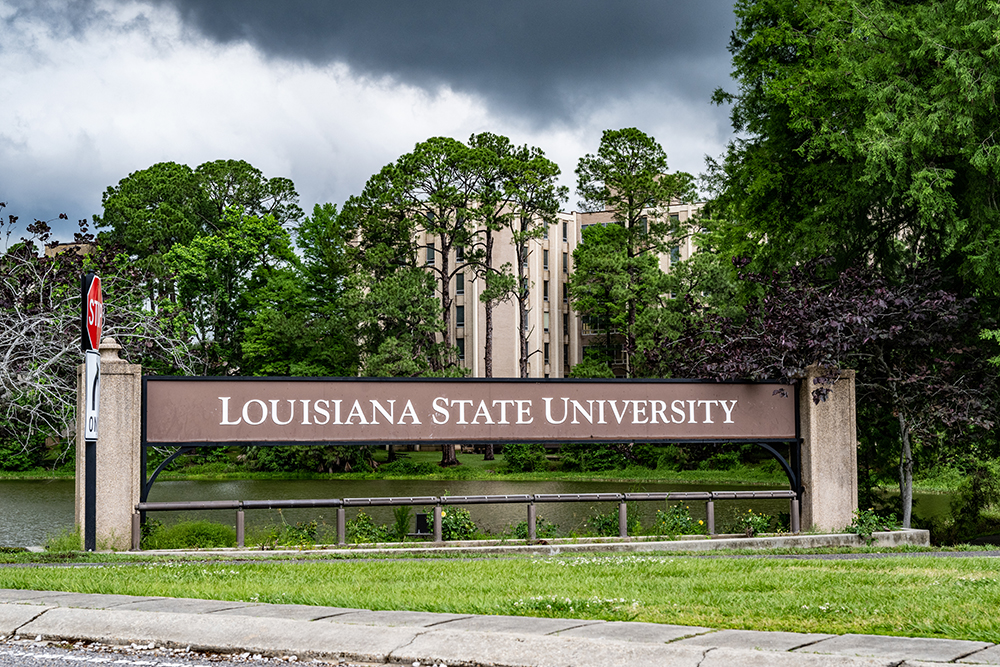
Support equipment included Komatsu 220 excavators, a forklift, super sucker vacuum trucks, two tanker trucks, four 6-inch Godwin pumps to move drilling fluid around, and dump trucks for solid removal.
Subsurface conditions were clay. Surface conditions included parking lots, roadways, sidewalks, buildings and mature oak trees along the entire path of the drill. Paths of the pilot bores crossed multiple utilities.
“It was a very confined area that was highly populated with students and everyday college activities,” Simon said. “The major issues on this project were pre-existing utilities, the shallowness depth for an HDD of this size and how close the 42-inch pipes needed to be – 15 feet apart at the same depth at entry point and exit points. There were multiple compound curves in the bore paths.”
Spartan completed the pilot hole for the first drill in eight days. The second HDD bore was completed much faster, taking only two days.
L.S. Womack mobilized pipe to the job site and strung it out in two sections, fusing them together the day before each pull back. A section of one street was closed for the weekend to avoid as much school traffic as possible and the product pipe was laid on rollers in the road to support a continuous string of pipe.
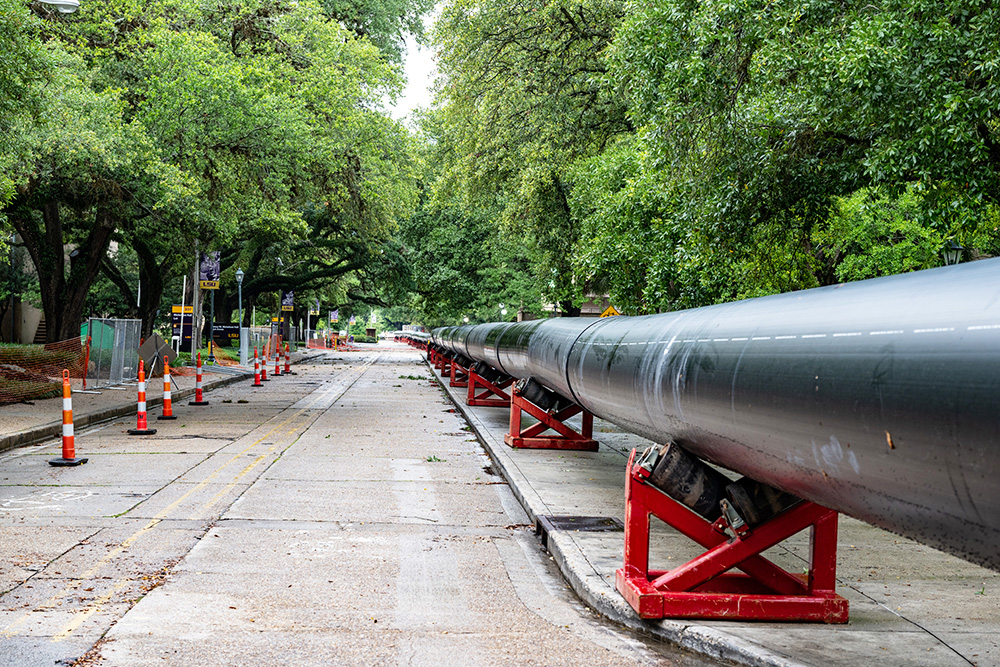
Completion
Spartan completed the pullback for the first bore in 11 hours and the second bore in eight hours.
Challenges on the LSU project included the high volume of vehicle and foot traffic. “It was important to make the public aware of the hazards associated with the project that people are not normally used to having to look for,” said Simon.
“Due to the location of the drill, we couldn’t completely block off the entire drill path, so we had to make sure any hazards were clearly marked, and alternate paths were available for people to get around for everyday college activities,” he pointed out.
“This project updated the existing outdated and overextended facilities throughout campus and supplied an energy efficient system that will provide LSU with a significant cost savings per year in the management and operations of their energy utility system,” concluded Braud.
FOR MORE INFORMATION:
Spartan Directional, (337) 837-4HDD (4433), spartandirectional.com
American Augers, (419) 869-7107, americanaugers.com
Brownline, (281) 391 5800, drillguide.com/en
Comments