June 2023 Vol. 78 No. 6
Features
GPR: From glaciers to conduits, digs deeper so you don’t have to
Blake Bacho | GPRS
(UI) — The casual observer would think Trey Merrell just stinks at mowing the lawn.
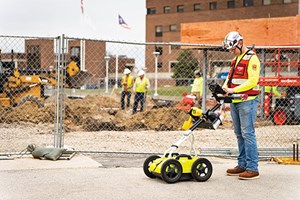
Pushing a red-and-black, four-wheeled cart that resembled a lawn mower, he was walking in the correct, methodical grid pattern that normally pressures neighbors into doing their own yardwork. But the telltale sound of whirring blades was absent, and the grass remained unspoiled.
That’s because it wasn’t a lawn mower that Merrell guided across the Ford Motor Company’s sprawling Research & Engineering Center campus. The cart was a GSSI UtilityScan ground penetrating radar (GPR) unit he was using to investigate the labyrinth of infrastructure buried beneath the historic facility in Dearborn, Mich.
“We’ve done a bunch of work here,” said Merrell, a project manager at Toledo-based Ground Penetrating Radar Systems (GPRS). “Ford is making a huge, generational investment in [this] campus. This is the property that Henry Ford built towards the end of his life and that his kids ran as their headquarters for research and development.”
Merrell and his coworkers have been with Ford every step of the way as the latter has undergone a years-long transformation of its historic Dearborn R&D campus.
GPRS specializes in infrastructure visualization. Its nationwide team of technicians – called project managers – offer a suite of services that include utility locating, concrete scanning, video pipe inspection, leak detection, 3D laser scanning, and mapping and modeling.
GPRS has conducted utility locating and concrete scanning at the Ford site – both services that rely primarily on GPR technology. This non-destructive detection and imaging tool identifies subsurface elements, either underground or within a surface, such as concrete. GPR can detect both metallic and non-metallic objects, meaning that it can find all types of buried utilities.
GPR works by sending a radio signal into a structure or underground and reading the “bounce” of that radio wave off any material it encounters. These bounces are displayed as hyperbolas on the GPR’s display. An experienced technician can then interpret this reading to determine the type of material located and its precise location.
The ability to accurately map underground or encased infrastructure allows construction and excavation professionals to plan groundbreaking and other destructive activities more efficiently. By knowing where not to dig, cut or core, these professionals eliminate the risks associated with striking buried utilities or severing structural components, such as rebar or post-tension cables.
It’s not uncommon for GPRS to be called to a site to conduct a single area locate or concrete scan, only for the scope of the project to expand as the contractor realizes the potential of the company’s services.
Merrell and the GPRS team have conducted hundreds of these scans at the Ford site, investigating both below the earth and within concrete structures. Over the time on the project, GPR technology has seen improvements that allow Merrell and his team members to provide a clearer image of the property’s infrastructure today than they could have even just a few years ago.
The UtilityScan unit Merrell has used much of the time on the Ford campus is being phased out of GPRS’ arsenal in favor of the ImpulseRadar PinPointR GPR Scanner. With its dual-channel operation and internal global positioning system (GPS), the PinPointR can accurately locate items both shallow and deep in the earth in a single pass over the surface. This improves locating efficiency and decision making.
“I think the ImpulseRadar is the next big thing,” Merrell said. “It uses multiple frequencies simultaneously. It has good resolution deep, but then you can toggle over, and you can get great resolution shallow. It’s just an incredible piece of equipment.”
Whether it’s the UtilityScan or the ImpulseRadar, modern GPR barely resembles the equipment GPRS project managers used when the company was founded in 2001. And that equipment is lightyears ahead of the GPR units of even a decade prior. Yet, while this ever-evolving technology reigns supreme as the premier choice for utility locating and concrete scanning, its origins are far removed from the construction industry that relies on it so heavily today.
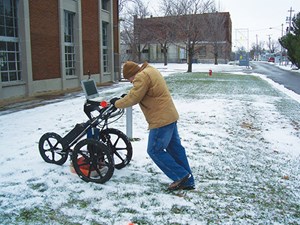
Decades of development
GPR technology is older than one might expect.
Dr. Andrew Kozlowski of the New York State Museum traces its origins back to the early 1930s, when it was developed to measure the thickness of glaciers.
It would be another 30 years, however, before the technology’s capabilities were explored in earnest.
“The hardware and software made tremendous technological advances in the 1960s, 1970s and finally became affordable in the mid-1980s,” Dr. Kozlowski wrote.
In 1972, a GPR unit called ALSE (Apollo Lunar Sounder Experiment) was carried by the Apollo 17 capsule as it orbited the moon. ALSE operated on three radio wavelengths – 5, 15 and 150 Mhz – and radar data of the moon was recorded on 70-millimeter photographic film. The data ALSE collected provided profiles of the lunar surface and subsurface.
As with any technology, GPR’s capabilities only expanded once the equipment became widely available. Still, at the dawn of the new millennium, the construction and excavation industries had yet to truly realize its potential for eliminating subsurface damage.
At this point, underground utilities were primarily located based on the as-built drawings created when the lines were installed. As any construction professional will tell you, those drawings should really be called “as-intended” because they are rarely an accurate representation of what’s underground.
For scanning concrete, the only option that existed prior to GPR was X-Ray. This was a costly, time-consuming and dangerous tool, as all or most of a site needed to be cleared to protect workers from accidental irradiation during a scan.
GPRS President and CEO, Matt Aston, is considered a pioneer in bringing GPR to the construction industry. It started in 2001 when he happened upon an advertisement for GPR rental while flipping through a magazine. He was well-versed in the risks associated with cutting or coring concrete – his father owned a concrete company – and had seen utility lines and other subsurface objects accidentally damaged during construction projects.
Aston seized the opportunity to bring GPR technology to the construction industry. And GPRS was born.
Concrete scanning was GPRS’ first service line, and GPR was the primary tool used for the task. Unlike X-Ray scanning, GPR requires access to only one side of a slab or structure. Also, unlike X-Ray, GPR emits no harmful radiation and requires no prior set-up.
GPR’s final advantage over X-Ray? It keeps evolving.
Continued progress
Every iteration of GPR has been lighter, faster and more user-friendly than its predecessor.
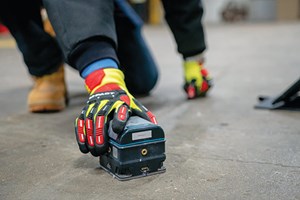
GPRS Contract Locating Manager John Kessinger was one of the company’s earliest employees. He started in 2002 as a project manager, and he can still vividly remember being in the field conducting utility locates and concrete scans.
What he recalls most is that the GPR scanners of his day were unwieldy and heavy. While similar in size to today’s carts, the original units were constructed with traditional metals, rather than lightweight carbon fiber. Their acid batteries were much heavier than the lithium-ion cells that power today’s scanners, and their displays were thicker and less user-friendly than modern touchscreens.
The improvements in GPR technology are even more obvious when you compare the concrete scanning units used by Kessinger’s era to today’s devices.
In 2005, Kessinger was called to Jackson, Mississippi, to scan precast concrete walls to verify the location of reinforcing steel as part of construction of a new Bass Pro Shops store. Today, this would be a straightforward job accomplished in a couple of hours, thanks to the mobility of the handheld Proceq GP8800 GPR Scanner, GPRS’ current scanner of choice for investigating concrete.
It was a little more complicated for Kessinger who, more than 20 years ago, used the top-of-the-line GSSI SIR-20 system, which had to be physically connected to a Panasonic Toughbook computer. Including its cart, the system weighed close to 100 pounds.
“I remember just having cords, having all this equipment, the setup,” Kessinger said. “It really wasn’t as conducive as today where we have small antennas that really don’t have the cables and cords.
“The job was done, it was a successful job, but it was just hard on the body a little bit to do the scanning.”
Limitations
Every tool has its limitations, whether you’re talking about something as simple as a hammer or as sophisticated as ground penetrating radar.
Soil type plays a huge factor when using GPR for utility locating. Highly conductive soils, such as clay, are harder for GPR to penetrate. However, modern GPR units, like the ImpulseRadar, are less inhibited by this problem, due to their dual-channel operation. This allows for one-pass locates at both high and low frequencies to scan both shallow and deep into the soil.
Moisture also plays havoc on GPR’s effectiveness. Freshly cured concrete still has a lot of moisture inside and is, therefore, more difficult for GPR to penetrate than older, dryer concrete.
GPR can still be useful in situations where it is hindered by its limitations.
Back at the Ford Research & Engineering Center, Merrell has been called out to help the contractor locate the main utility connection points on the property. The pipes in question are believed to be transite, or asbestos-cement (AC) pipes, that are buried 9 feet below the ground. It is next to impossible to detect them with GPR or EM locating, so instead, an excavator is potholing for them, digging where the lines are supposed to be to verify their location.
Merrell’s job is to use GPR to find all the infrastructure around these connection points if he can’t locate the points themselves. This way, the excavator knows which spots to avoid.
“They will have us out and they’ll have like 30 locations at a time where they need, essentially, a 30x30 [foot] utility locate performed,” Merrell explained. “They have us locate everything around the pipe they are looking for, so they don’t damage any of it when they go through and pothole to locate those lines.”
GPR continues to prove its worth as Ford inches closer to the finish line of the multi-million-dollar project. If the excavator were to sever a single power line while searching for the transite pipes, it could be fatally electrocuted. The best-case scenario for a strike is that the contractor will be looking at a costly repair job and hours of downtime as the line is fixed.
“If I can spot the utility they’re looking for, then I can save them a boatload of money on each pothole,” Merrell said. “If I can’t spot the utility, they need to know what other utilities are in there, so they don’t bump them and make a mess of it.”
Despite its limitations, GPR continues to prove its usefulness as the most reliable and versatile infrastructure visualization technology. Developed nearly a century ago to measure the thickness of ice, it has evolved to become an indispensable tool of the construction industry.
“There’s just nothing that has come along that one: can gather the amount of data that GPR can, and two: can cover the surface area,” Kessinger said.
“GPR being on wheels when utility locating means you know you can scan back and forth,” he added. “It’s like you’re mowing the grass. I think its ability to cover that amount of surface area, to make it feasible to scan a large area, is what’s mainly contributed to GPR staying around as a technology.”
FOR MORE INFORMATION:
GPRS, gp-radar.com
GSSI, (603) 836-9663, geophysical.com
Comments