December 2023 Vol. 78 No.11
Features
PM completes large-diameter spray pipe rehab
Project Completed Ahead of Schedule Despite Challenges, Obstacles
By Corinna Hunt, Contributing Editor
(UI) — When PM Construction began a project in mid-March 2023 to rehabilitate two sewer pipes beneath the service road at Beltway 8 and Memorial, in Houston, the company had a November deadline. Working 24 hours a day, every day of the week, the project wrapped up in July – more than three months ahead of schedule.
“We’ve done it in the past,” Justin Mouton said of the 24/7 schedule. “It just all kind of depends. With this project, we had a hard cutoff date of November because we all know Thanksgiving and the holiday season, and it being right there by City Centre and all the shopping areas … that’s when it really gets busy over there.”
Mouton is business development manager for Puris. PM Construction, which is based in Pasadena and services Texas, Louisiana, Oklahoma, Mississippi, and Arkansas, is under the Puris umbrella.
“We do pipe bursting, we do CIPP and we do geopolymer spray,” Mouton said of PM Construction. “We’re one of the few contractors out there that does all three trenchless pipe rehabs.”
Two pipe rehabilitation methods were considered for this job. The original scope for the CityCentre project involved a cast-in-place polyethylene liner.
“Once we started looking at the project and talking about it with the city of Houston and TxDOT, they were not going to approve the traffic control plans because it’s a super sensitive area,” Mouton said.
Geopolymer
Instead, the decision was made to spray a GeoTree geopolymer material called EcoCast, which involved a smaller footprint.
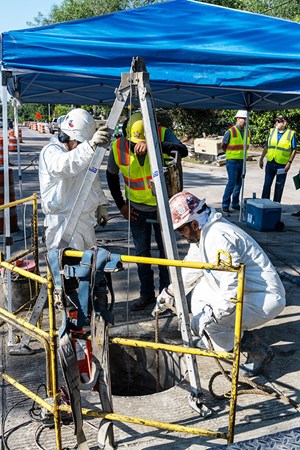
“That’s the beauty of geopolymer: entry through the manholes in order to rehab the lines,” PM Project Manager Jack Simmons said.
Both CIPP and geopolymer are great solutions, and the former is actually quicker, Mouton said. But it would have required tearing up the road in order to open up the manholes enough to fit the liner through, and it still likely would have involved working around the clock at times, he said.
Even though the project footprint ended up being smaller with the use of the geopolymer spray, an extensive amount of traffic control was still utilized, including two police flaggers. PM Construction began work on the southbound side of the service road, and once that was completed, crews moved to the northbound side to repeat the work on a smaller section of pipe.
“We did a 54-inch spin cast lining with the geopolymer and that was 5,129 feet, and then the 36-inch geopolymer spin cast was 516 feet,” Simmons said. “We had to spray up to a thickness of 1.75 inches for the 54-inch, and 1.25 inches for the 36-inch.”
Throughout, each line had to be tested for compressive strength and thickness to ensure the solution was meeting the city’s needs and requirements, posing a small challenge.
“The thickness tests were done manually, with a gauge,” he explained. “The city would send a lab tech down into the manhole to measure – after we’ve sprayed, while it’s still wet – and found it was hitting 1.75 inches.
“Then, for the compressive strength test, they basically take a sample of the mix we’re using for the spray,” Simmons continued. “The lab techs test each manhole section by taking a sample and casting it into cylinders, basically. Then they take them to the lab and do a compressive strength test with all their breaking equipment.”
Tests had to be done three times, which took time. Another challenge came from a delay caused by having to repair a void discovered at one of the manholes.
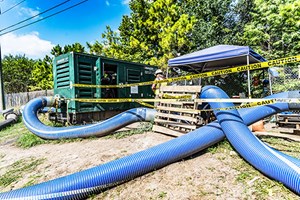
Unexpected void
“When the crew went down into the manhole, you could see through it into this giant void. They described it like a cavern,” Simmons said of the crew members who made the discovery.
The size was about 12 by 20 feet, and another company had to be called in to fill the void with cellular grouting – “a very light concrete” – before the crew could safely get inside the pipe to work.
The same manhole had corroded itself, so it was also necessary to rehabilitate that for future sustainability as well.
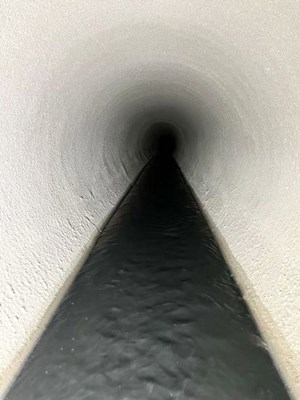
“Any issue that came up, we’d quickly turn it around and got back on track very fast,” Simmons stressed.
One crew worked a 12-hour day shift, and another crew worked a 12-hour night shift. Because the project involved sewer pipelines, a bypass was necessary, and so was a bypass watch – all working at the same time as both crews.
“In order to spray these lines, you have to have bypass on, which means the bypass is running 24/7,” Simmons said. “So, it also meant that we were constantly watching the bypass and running those 24/7, which can be a costly expense.
“But it was beneficial in the fact that we managed to get the project done so far in front of schedule and managed to open the road back up for the public which, of course, was the biggest concern and issue for TxDOT in the first place.”
Throughout the project, PM ran 10-inch, 6-inch and 4-inch bypass pumps with the main ones being 10-inch. There were also two backups: one to kick in, in case the other failed, and a standby unit.
Using a truck with a compressor, hooked up to a hopper with the cement and the water, and then hooked up to hoses, they were able to spray pipeline interiors up to 500 feet at a time. Hose length is what hinders the distance. “Five hundred feet is the most that we like to push,” Mouton pointed out.
Bad condition
The original pipe was badly deteriorated. Some of the rebar even poked through. In this case, the host pipe was only used as a host form.

“This product was designed to be fully structural, so we essentially use the host pipe,” Mouton said. “We spray our product, and then once the product is in place, the host pipe can deteriorate away. Our product will then be in place and be a fully structural pipe.”
It will have a design life of 50-plus years, according to the Army Corps of Engineers.
The overall work of the rehabilitation project began March 17 and concluded July 8, well in advance of the November deadline – even when a new challenge arose, requiring some additional time.
“We actually went back on July 24 to perform a point repair,” Simmons said. “We ran into an issue towards the end of the job, where part of the pipe was basically dislodged. So, we did an 8-foot point repair on the 54-inch line, which was quite a big undertaking. That spanned from July 24 to August 4, and now the job is completely finished.”
The dislodging occurred on the northbound side and could have happened for a number of reasons, including unsettled bedding or the ground moving with vibrations, groundwater, the weight of the pipe, the weight of the load on top of it.
“They wanted us to make a proper repair,” Simmons said of the city. “That involved a 15-foot-long saw cut along the frontage road. We actually had to close down a huge part of the frontage road for two weeks.
“We did a saw cut 20 feet long, excavated the site and removed a giant 54-inch concrete pipe in order to make a concrete pipe replacement. Once the point repair was made, we went down into the pipe and performed a geospray for the rehabilitation work.”
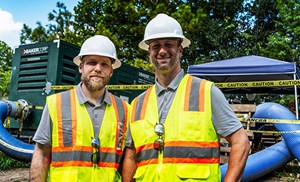
The total cost of the project was about $4.5 million. Pleased with the outcome, the city awarded Puris a similar pipe rehabilitation contract in the Briar Forest neighborhood – for which work would not be done around the clock.
“The city was extremely happy with everything,” Mouton said. “They were very impressed with us finishing early … so much that they’re giving us this new project not far from there. I would suspect we’re going to have more work coming from Houston.”
Comments