August 2023 Vol. 78 No. 8
Features
Tech lesson for Silicon Valley
Cratus brings leading pipe-bursting technology to Palo Alto, Calif.
Palo Alto, Calif., is considered the birthplace of Silicon Valley. The much-heralded area has been responsible for some of the most impactful technological advancements in history. But while technology of that sort amazes the general public, most would rather not consider the technology being used to update the infrastructure underground, specifically the sanitary sewer.
Trenchless technology has been one of the most important advancements in the underground construction industry and has changed the way utility contractors approach projects. For a recent sanitary sewer upgrade project in Palo Alto, it was trenchless pipe bursting that was making an impact.
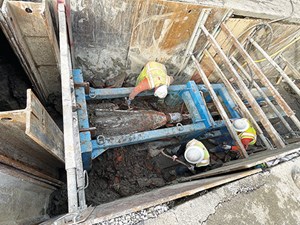
Utility contractor Cratus Inc, of San Francisco, Calif., was selected to take on the multi-facetted project. The job included replacement of approximately 10,000 feet of vitrified clay (VCP) sanitary sewer mains of varying diameter, along with replacement of 28 manholes and 150 existing city-owned sewer service laterals and cleanouts. The VCP was specified to be replaced with high-density polyethylene (HDPE), which made it a prime candidate for pipe bursting.
According to Liam Finnegan, president of Cratus, the company has a significant amount of pipe-bursting experience and was well-prepared for this type of project. “We focus on all utility work, underground sewer, water,” he said. “We don’t really do much else. We don’t do any concrete work. Sewer and water are what we primarily do. We’ve done quite a bit of pipe bursting.”
With the amount of pipe bursting slated for the project, high-production pneumatic bursting equipment was chosen for a majority of the project. Pipe-bursting specialist George Mallakis, from trenchless equipment manufacturer TT Technologies, Aurora, Ill., explained that pneumatic pipe bursting has been a workhorse in the industry since the 1980s.
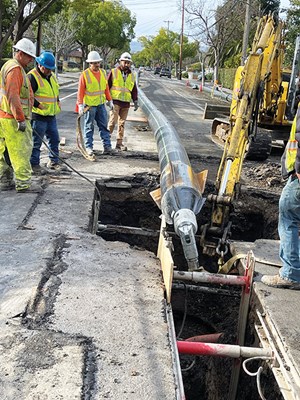
“Pneumatic pipe bursting really put the method on the map beginning over 40 years ago,” said Mallakis. “Contractors have been able to burst and replace literally thousands of miles of pipe with pneumatic pipe bursting. And it was a good option for this particular project.”
For the Palo Alto sanitary sewer replacement project, a reversible PCG180 pneumatic hammer, along with an RW10 10-ton constant-tension, variable speed Grundowinch and reversible boom, from TT Technologies was used.
Quality focused
Cratus is a high-quality utility contractor where safety is a top priority. The company emphasizes safety training, toolbox talks, observation programs and job hazard analyses to prevent incidents from even occurring. And it makes sure the right people are positioned to ensure safe operations.
“We operate with a superintendent and foremen and then inside that lead men in the crews, especially the pipe bursting,” said Finnegan. “There are lead men on the mainline pipe bursting then on the backend, we have lead men on paving and restoration backfill crews. We do toolbox meetings once a week. Our foremen go through a certain topic. We do the training as often as we need to keep everybody up to date if something changes.”.
The largest portion of the project was nearly 7,000 feet of 6- and 8-inch VCP to 8-inch HDPE, followed by smaller sections of 8-, 10- and 12-inch VCP to 10-inch HDPE, and 10-inch VCP to 12-inch HDPE.
“We fused all the HDPE pipe on site, for each run,” Finnegan commented. “There was very limited space to fuse some days. We had to make a separate fuse on the day of the pull, which delayed us. The city also has its own certification process for pipe fusing that we needed to go through.”
For most of the project, the mains ranged from 6 to 10 feet deep, with some sections as deep as 12 feet. Bursting runs averaged 350 feet with most running manhole to manhole. For traffic control, Cratus crews took the center lane of the roadway and pushed the traffic to each side.
The pneumatic bursting system was ideal for this project. “The straight barrel tool worked well bursting manhole to manhole,” Mallakis pointed out. “Straight barrel bursting tools, like the 7-inch diameter PCG 180, use a front expander.
“This is a different configuration than your standard rear expander system. The front expander adds versatility to this style of tool; when entering manholes you do not want to remove and replace. The straight barrel tools can be reversed automatically with a lever located on the in-line lubricator.
“So, once you complete a bursting run and enter the manhole, the winch cable can be detached from the tool and be reversed out through the newly installed pipe. This is extremely helpful when bursting into a manhole from a pit. Removing the tool through the manhole is usually not possible because of space limitations but reversing it out to the launch pit solves that problem.”
For pneumatic pipe bursting, the bursting tool is guided through the existing pipe with a constant-tension, variable-speed winch.
“The winch is specifically designed for pipe-bursting and other underground construction applications,” Mallakis explained. “The constant-tension, variable-speed aspect allows the winch to adjust for conditions that affect line speed during the pipe bursting operations, providing for constant and consistent pulling force.
“Cratus also has one of our specially designed reversible booms on this project, which creates more space to detach the tool from the winch cable and back itself out,” Mallakis added. “The Cratus crews were very efficient and productive.”
Navigating around utilities
While the bursting runs went smoothly on the Palo Alto project, getting to the point where bursting could begin proved challenging and contributed to some long days on the work site.
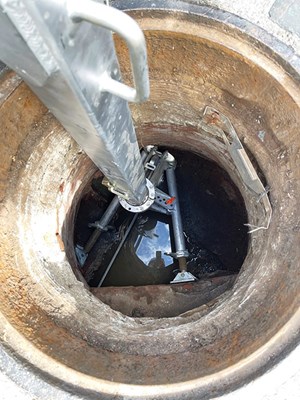
“One of the biggest issues with the project was the number of adjacent utilities,” Finnegan observed. “We had to excavate quite a bit because Palo Alto has many utilities that are underground – all the electrical lines in the area and basically everything else. They don’t have many poles in that city or overhead utilities of any kind. So, we had a lot of potholes. That was probably the most challenging part, crossing so many utilities.
“Then, by the time you do an active bypass on that system – 6-inch hoses on 6-inch pump – put in temporary piping, get the new pipe into position, get down, get it shackled down and get moving, I don’t know what time in the day we started pulling, but in the end, it’s an 12-hour day.”
For a 700-foot section of 15-inch VCP to 18-inch HDPE, the Cratus crew utilized a different approach to pipe bursting.
“For the larger-diameter pipe we brought in a static pipe bursting system, the Grundoburst 1250G,” Mallakis said. “This gave Cratus the opportunity to expand its pipe-bursting resume and, with the proximity of both businesses and homes at that location, the static operation is much quieter than the larger pneumatic hammer. We also used special tooling that helped with connecting and disconnecting in a highly efficient manner.”
For the static bursting process, instead of a winch guiding a pneumatic tool through the host pipe to break it apart, a hydraulically powered bursting unit uses static pull force to pull quick lock rods and the expander through the host pipe, while pulling in the new pipe at the same time.
“Static pipe bursting is very versatile and popular because you have the ability to pipe burst a wide range of existing pipe materials and install diverse new product pipe materials in addition to HDPE,” Mallakis said. “Pneumatic pipe bursting is still a high-production method and widely used, especially in gravity sewer, but static pipe bursting has become a more common alternative, especially in water and pressure pipes.”
Finnegan added, “That was our first time using the Grundoburst static rod system. We wanted to use it in the past but didn’t have a suitable project. We only did one pull. It was more like a test for us. I liked it. Once you get the pipe ready to go and if you have long runs, that machine is a beast, you know what I mean? That’s how I would describe it. But it was very smooth.”
Project success was due to “Cratus’ ability to plan well and bring the best people and equipment to the job,” said Mallakis. “The city of Palo Alto and their residents benefit from pipe bursting being specified and used instead of traditional open cut replacement through lower costs, less disruption and lower carbon emissions to get the job done."
FOR MORE INFORMATION:
Cratus Inc., (415) 939-2840, cratusinc.com
TT Technologies, (800) 533-2078, tttechnologies.com
Comments