May 2022 Vol. 77 No. 5
Rehab Technology
Manhole Rehab Project – It’s Part of the Plan
Randy Gonzalez
The city of Eagle, Idaho, situated on the banks of the Boise River in the foothills of western Idaho, is home to nearly 30,000 people. The area, like much of the greater Boise region, has experienced significant population growth over the past 10-20 years (including a 50-percent increase since 2010), and that trend is expected to continue for years to come.
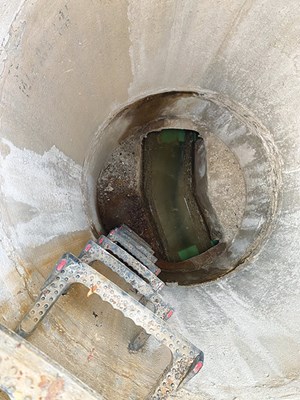
To keep up with the growth, the Eagle Sewer District – with a service area of roughly 35 square miles – has a proactive approach to ongoing maintenance. It includes a comprehensive program to help ensure its infrastructure will serve existing customers, as well as new customers well into the future.
Identifying problems
As part of the proactive maintenance plan, the district recognized the need to address a series of manholes on a neighborhood boulevard, that had experienced a significant amount of degradation and corrosion.
These seven manholes, along an 1,800-foot stretch of North Golden Crown Way, were part of a 24-inch trunk line that hooked into a nearby lift station. Given the levels of sewage running through this section of pipeline, the lift station was in a constant state of cycling on and off, leading to a continuous surging of sewage levels and bursts of turbulence in the stream.
The turbulence, in turn, caused heightened levels of hydrogen sulfide (H₂S) gases to be released, relentlessly exposing the vertical chimneys of the manhole structures to one of the primary causes of corrosion in any sanitary sewer system.
Like much of the Eagle Sewer District infrastructure, the manhole structures were built of concrete and put in place about 25 years ago. They had run the course of their anticipated useful life, especially given the extreme exposure to H₂S during that time. The district had two options to address the issue – replace the manhole chimney structures or engage in a rehab project.
Options
Replacing manhole chimney structures is a hugely disruptive and very costly project for any sewer district. Even though new polymer manholes were promising upwards of a 100-year life, they were also as much as two-to-three times as expensive per vertical foot as the cost of a rehabilitation solution. With the significant improvements of products and materials now available, and the improved lifespan of these solutions, the Eagle Sewer District decided to rehab the seven manholes on North Golden Crown Way.
One of its reliable vendors, Integrity Inspection Solutions (IIS) of Caldwell, Idaho, won the bid for the project. Familiar with working for the district and in the city of Eagle, the contractor contacted city hall to arrange traffic control and began to mobilize its team to get the project underway in August 2021.
The scope of work for IIS was a comprehensive rehab of the seven-manhole chimney structures. At an average depth of 10 to 11 feet, the project was comprised of 80 vertical feet of manhole risers, with a five-foot circumference of each structure. With the proximity of the city of Eagle to the Boise River, and the corresponding high-groundwater table, four of the seven risers were experiencing infiltration and inflow; the team used a hydrophobic pressure grout to address this issue.
The next step was some build back work on all the risers. Integrity chose a high-early-strength patching material to fill any voids in the concrete. As part of the surface prep, the contractor also cut a keyway at the top of the chimneys, below the grade rings, and a termination key at the spring line – versus doing a monolithic down to the flow line – using a grinder to “notch” the concrete.
This would help ensure a good solid termination point at the edge of the coatings solution, and reduce the possibility of undercutting, corrosion, disbondment or peeling of the coating. Once the build back and keyways were completed, the final step in preparing the surface was pressure washing all seven of the risers, with a 5,000-psi rotary tip.
When considering a coatings solution for a manhole rehab project, one option is polyurethane. But in this type of environment, it would be difficult, time-consuming and expensive to dry the concrete enough for it to take a typical polyurethane coating. There was also too-much residual moisture in the substrate to apply the polyurethane without extensive surface prep.
As a result, an ultra-high-build epoxy coating was chosen – Raven 405 from PPG Raven Lining Systems. The 100-percent solids, zero-volatile, organic-compounds, chemically resistant epoxy was an ideal solution for the manhole structures. It could be applied on a saturated surface-dry (SSD) substrate, saving a significant amount of time.
Raven 405 epoxy was applied direct-to-host, without a primer, at 150-mil dry-film thickness (DFT). The pressure washing done beforehand created the required surface profile for the epoxy to both chemically and mechanically adhere to the concrete risers.
In some rehab applications, an epoxy coating may seem an excessive, expensive, and premium solution that isn’t needed. But with an environment with such high exposure to extreme levels of H₂S, the epoxy was critical to providing a long, useful life for the manhole risers – “as good as new,” for most any sanitary sewer infrastructure application.
48 hours
Once the film was dry (approximately four to five hours), a final step was a comprehensive holiday test in the seven chimneys, following ASTM and NACE industry standards. The tests, using specialized, high-voltage equipment, ensured there were no inconsistencies or imperfections in the 150-mil DFT surface of the epoxy coating, such as discontinuities, pinholes, holidays and voids.
Holiday tests are particularly important when applying anti-corrosive coatings, as undetected holidays leave the underlying substrate (concrete, masonry, metal) susceptible to corrosion at those locations.
From start to finish, the IIS team took 48 hours to get the job done. It was a quick and efficient project, made possible by the knowledge and expertise of the team, but also by the time-saving features of the 405 epoxy. With the ability to apply the coating on an SSD substrate, and the brief window from time of application to holiday tests, it proved an effective solution as part of a long-term, ongoing maintenance plan for any sanitary sewer district. •
ABOUT THE AUTHOR: Randy Gonzalez is the West Region Technical Manager for PPG PMC Raven Lining Systems. He can be reached at 760-685-7784, or at gonzalezr@ravenlining.com.
FOR MORE INFORMATION:
Integrity Inspection Solutions, (208) 442-4470, iispipeline.com
Raven Lining Systems, (800) 321-0906, ravenlining.com
Comments