February 2021 Vol. 76 No. 2
Rehab Technology
First Look: Robots Tackle Underground Pipe Repair
Repairing underground water pipes can be a deadly job. As an industrial accident in 1984 in Idaho illustrated, workers above ground can sometimes be at risk, too.
The Oneida Power Plant disaster claimed the lives of four men when a pipe burst in a power plant. They were knocked unconscious by a sudden blast of water, then drowned after they were swept into the freezing Bear River.
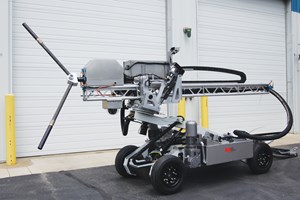
More than 3,000 cubic feet of water per second was released, washing the men, a maintenance shop and even vehicles into the water. The crew had finished routine maintenance on a turbine generator and opened a valve controlling the water flow from penstock to the turbine. The valve malfunctioned, causing a “water hammer” – a powerful surge of water – to develop, rupturing the 12-foot diameter penstock. A faulty weld made on the penstock joint about 35 years before the disaster led to the rupture.
While the men were above ground when the accident occurred, it pinpoints the inherent dangers working on water, sewer and other underground pipes. In 2017, a worker in Arlington, Ill., died in a sewer lining project. That same year, five men were killed in Colorado when a flash fire engulfed a platform inside the penstock where they were performing maintenance work. The workers used handheld radio to communicate with co-workers and emergency responders for 45 minutes before succumbing to smoke inhalation.
The dangerous work being performed by workers in underground pipes is still done mostly through manual labor. Robots, however, are beginning to take on that dangerous assignment.
Remote Orbital Installations LLC (ROI) and Big Sky Engineering, in Wisconsin, have developed a faster and safer alternative for pipeline rehabilitation and repair. A robotic unit, which the companies call the “Crawler,” can both surface-blast and line medium-to-large-diameter pipe internally. Penstocks, like the ones involved in the Colorado tragedy at Cabin Creek, are large-diameter pipes at hydro-electric installations that transfer water from mountain lakes down to generating turbines at a lower elevation.
The Crawler could be used in many different applications, avoiding tragedies, such as those that occurred in Colorado and Illinois. “This equipment could basically be used in any pipe or similar structure that needs repair,’’ said Mike Kronz, an engineer who helped design the unit for ROI/Big Sky.
A look inside
The Crawler travels within pipes of varying length to clean the penstock with powerful blasting. The unit then completes the process by re-lining the pipe with epoxy, which prevents corrosion that can lead to leaks.
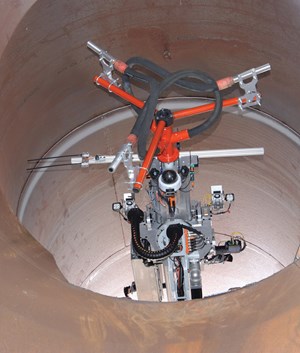
The unit is controlled by a person in a “command center,” which is actually a modified shipping container. “There are all kinds of feedback that can be read in the command center,’’ Kronz said.
An umbilical cord attached to the Crawler allows for remote operation 2,000 feet from the command center.
The Crawler’s blasting rate in a 10-foot penstock is about 500 to 600 square feet per hour, and travels about 15.1 feet per hour. During the internal lining process, the unit travels at about 150 feet per hour. For contractors, the lining material cost is about $200 per minute. In a project for BC Hydro’s Bridge River facility in Canada, the Crawler moved through 5,679 feet of penstock.
The primary advantage of the Crawler is it minimizes the amount of time workers spend inside the pipe structures, thereby reducing the risk that was inherent in the Cabin Creek tragedy.
“This not only reduces the amount of manual labor, but it also is quicker, safer and performs the work more consistently,” Kronz said.
Durable
In designing the automated unit, the ROI/Big Sky developers needed to identify equipment that would stand up to the stress of the task and the grimy environment. “It’s a dirty, rugged environment with a lot of dust and abrasive material,” said Paul Garvoille, who also worked on the machine’s design.
The designers selected components from igus, a Germany-based manufacturer of motion plastics. The company runs its North American operations out of Providence, R.I.
The Crawler includes energy chains from igus, which are used to guide power to moving parts of machines or structures. Also referred to as a power chain or cable carrier, the chains supply energy and data to mobile consumer equipment. They can be installed in large products, such as offshore oil rigs, all the way down to minimally sized robots.
While some energy chains can be made of metal, they require maintenance. The weight of machine components has led to the use of more lightweight components, such as plastic. The tech-up, cost-down
igus energy chains require no maintenance, resist dirt and can reduce installation costs by 88 percent.
In the Crawler, an energy chain allows the wheel width to be adjusted as it moves within the penstock. Diameters vary from 5 to 1.5 to 13 meters, and the automated unit is adjusted through the umbilical cord that is controlled by the command center operator.
Energy chains are also used to manage and protect electrical cables going from the lower control cabinets to the upper cabinets. They are used in the main boom raise, which allows the boom to extend and contract as it works within the pipe.
There are also servo motor cables that direct boom movement and in the 1,640-foot umbilical cord that contains power and control cables, along with fiber optic cables. A grease-free slewing ring bearing allows the boom to pivot from side to side without the worry of future maintenance.
Infrastructure challenge
Besides safety, the Crawler offers one other primary advantage for communities and businesses. The devices work more quickly, efficiently and safely than manual labor.
There is also no question that it meets necessary needs. The world’s infrastructure is crumbling. Whether it is the United States, Canada, Europe or elsewhere, there are plenty of projects that require rehabilitation and restoration. In December, for instance, the United Kingdom government authorized spending €400 million (about $478 million) to invest in Northern Ireland’s infrastructure.
The World Economic Forum’s gloomy forecast from 2019 said the world was facing a $15-trillion gap between projected investment and the amount needed to provide adequate global infrastructure by 2040.
The Crawler will help reduce labor costs on projects. “Similar to any automation project, it’s going to reduce the amount of manual labor required,’’ Kronz said. “The work will also be more consistent. Just not cosmetically superior. It’s going to be far superior to somebody working overhead and dangling within the pipe.”
And safety? Robots can be rebuilt if an accident occurs. Human lives cannot be restored. There is no price tag for the loss
of human life.
“Any tunnels that are being built are going to need rehab over time,” Garvoille said. “It’s not limited to water or liquid applications. It could be used in any tunnel that is being built.”
FOR MORE INFORMATION:
Remote Orbital Installations, (608) 845-0360, roi360.com
Big Sky Engineering, (608) 848-9898, bigskyeng.com
igus, (800) 521-2747, igus.com
DAN THOMPSON is the energy chain industry manager for igus, N.A.
Comments