September 2018 Vol. 73 No. 9
Features
Evolution of Dual Pipe Makes Mid-Sized Rock Drilling Practical
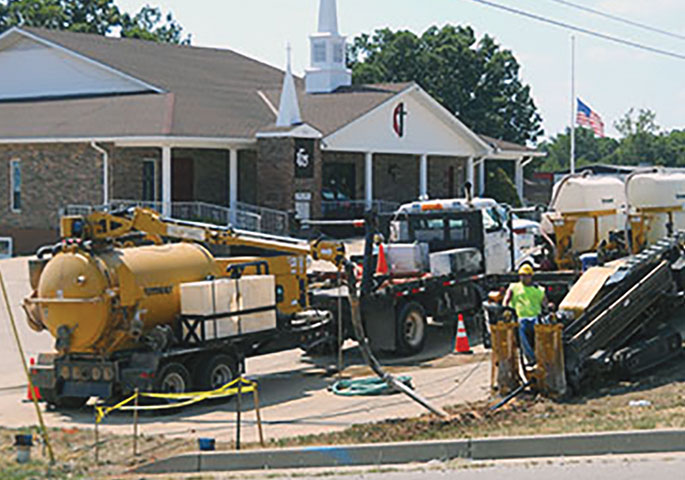
About a decade ago, residents and businesses in Branson, Mo, got access to gas service. Gas was a long time coming to this area.
Located in the Ozark Mountains of Southwest Missouri, the city is home to the popular Silver Dollar City resort and entertainment complex.
For years, several gas service providers said the rocky terrain made it too costly to construct the underground gas infrastructure necessary to serve the relatively small customer base. That changed with the availability of compact horizontal directional drilling (HDD) equipment that could effectively drill and be steered in hard rock formations.
First a 48-mile long transmission line was laid through the rugged Ozark mountains, and in 2010 multiple crews began installing underground gas lines to serve the community. Ultimately, about 85 percent of gas mains and services – approximately 80 miles of mains and 15,000 feet of service lines – were installed using HDD.
“The rock was as hard as we’ve ever encountered,” said one contractor who did much of the work. “I think without a doubt, Branson could never have had gas without the HDD equipment we and other contractors used.”
Rock solution
That equipment was Ditch Witch All Terrain (AT) models of various sizes equipped with a mechanical, dual-pipe drilling system, rather than using single drill pipe of conventional HDD equipment.
While drilling the pilot hole, an inner rod drives a rock bit and the outer pipe, with a slight bend, steers the downhole tool and provides rotary torque for the hole opener during backreaming. The setup is similar to that of a machine with a mud motor, except the bit is not powered by drilling fluid, eliminating the need for high-volumes of fluid and the accessory equipment to mix, circulate, clean and, ultimately, haul it away.
Indeed, one contractor who had just acquired an early AT model explained it to colleagues as having a “mechanical mud motor,” a somewhat inaccurate but descriptive explanation.
Manufacturers say the dual-pipe system provides significantly more horsepower to downhole tools than equipment using mud motors. Some call development of the dual-pipe system one of the major milestones in the evolution of directional drilling, enabling mid-size equipment to effectively and economically work through hard rock, allowing for the first time HDD to be used in developed areas built over rock.
The dual-pipe drilling system is not new. Ditch Witch introduced the first dual-pipe drive in 1995 on the 8/60 Jet Trac, a 27,000-pound pullback machine with a different look than other Jet Trac units of the time and a model designation inconsistent with the company’s other HDD machines. The drill carriage could be raised to enable vertical drilling, although little use was made of the capability.
While the 8/60 was ultimately dropped from the product line, engineers continued to make refinements to the dual-pipe system. In 2000, the first AT system was introduced. Since then, the dual-pipe drilling drive has continued to evolve, and AT machines have taken on an increasing share of HDD utility construction.
Convertible
Today two companies – Ditch Witch and Vermeer – offer mechanical dual-pipe HDD models. Each company’s dual-pipe units can be converted to a single-pipe system for drilling in softer soils.
“Dual-pipe technology changed the way customers and end-users thought about putting product in the ground, specifically hard ground,” said Cory Maker, Ditch Witch HDD product manager. “Previously, drilling in rock formations in residential areas was considered uneconomical because most rigs employing mud motors – then considered the only way to drill and steer in rock – were too large and required support equipment to operate in urban areas.
“The development made it possible for contractors to purchase smaller machines to work more efficiently on compact and hard-rock job sites.”
Vermeer Trenchless Product Manager Tod Michael said dual-rod machines fit a broad range of ground conditions, from loamy soils to relatively hard rock, including 25,000 psi compressive strength or harder.
“Compared to other rock drilling equipment,” he said, “dual-pipe machines have the ease of operation similar to single pipe models.”
The current Vermeer dual-pipe model is the 40,000-pound-
pullback D40x55DR S3.
Differences
Underground Construction asked representatives of both companies what sets their dual-pipe rock drilling equipment apart.
Vermeer’s Michael said the D40x55DR S3 carries 500 feet of drill rod onboard, which allows for longer bores without the need for manually adding rod. It also has a range of tooling options: the dual-rod head, dirt tooling and air hammers for drilling harder rock. And its basic components include a dual-rod head capable of running several bit types developed for various ground conditions.
“Vermeer has been drilling rock with a number of methods for many years,” said Michael. Our first dual-rod machine was introduced to the market in 2012. Our machine rod exchange and vise design were developed to help reduce rod exchange time and complexity.”
Michael said several questions need to be addressed before drilling in rock, including:
- What is the rock type and its compressive strength?
- How abrasive is the rock to be drilled?
- Is the rock solid, layered, cobble, gravel, etc.?
- How much loamy soil will be drilled before or after rock formations?
- What are the lengths of bores?
- What is the required bore geometry?
- Can bore geometry be changed to match drilling conditions, if necessary?
Ditch Witch’s AT40 features new innovations that separate the system from others.
“The advanced drilling system provides 33 percent more torque than competitive units,” Maker said. “Its patented connection provides a more reliable connection for optimized performance and steering.
“A patented, steering-offset design eliminates the need for a universal CV joint which reduces fatigue in the shaft and allows a two-degree bend for more effective and responsive steering in hard-rock conditions.
“With a standard 70-gallon-per-minute, 1,100-psi mud pump [an optional 110-gmp, 900-psi mud pump is available], the AT40 provides increased fluid flow from the mud pump to the swivel, for more downhole flow capabilities.”
Using 15-foot-length drill pipe, AT40 can carry 360 feet of drill pipe for reduced cycle times. The machine includes a patent-pending reversible pipe box for added job-site versatility.
Maker added that the advanced AT system also has an enhanced RockMaster housing for reduced maintenance and improved longevity. A modular design makes the housing adaptable to two different sizes of drill bit using regular API connection.
The housing has an industry-exclusive, double-layer seal with high-capacity bearings, as well, for increased downhole life. This doubles service -time intervals when compared to previous models.
The current AT lineup ranges from 30,000 to 100,000 pounds of pullback.
Installing Gas, Communications in Rocky Conditions
G&W Construction Co. Inc., Moorehead, Ky., provides directional drilling services to the gas, water, sewer, electric and communications industries, and specializes in rock drilling.
“Most of our directional drilling is for gas and communications,” said Darrel R. Alderman, president. “We have eight Vermeer drilling rigs ranging from 24,000 to 100,000 pounds pullback. Most of our rock drilling is done with our D50x55DR, which has the dual-rod rock drilling system. We also have mud motors and air hammers for other drill rigs.”
Alderman said planning is the key when drilling in rock.
“Profile the bores to make sure bends do not exceed drill or product specifications, and select the right drill rig for the project,” he advised. “Corners can’t be cut in this kind of work, and proper tooling selection for ground conditions is a key in successful rock boring.”
Deploying Fiber Through Rock
The value of mechanical dual-pipe HDD technology is demonstrated on the job.
Ditch Witch Product Manager Cory Maker describes how a JT30 all-terrain model (forerunner of the AT30) was used on a fiber deployment job by Oregon contractor West Pacific Drilling.
“Conditions underground were extreme, with nearly 80 percent of the project being hard rock,” he said. “Fractured rock also was scattered throughout the job site.
“On this portion of the backbone work, a Ditch Witch JT30 was used. Dual-pipe, all-terrain technology helped to productively make installations through the tough ground and decrease the amount of fluid often needed for rock drilling. Less fluid volume helped reduce environmental impact, fluid waste and site cleanup, which helped us complete the work in a tight timeframe.”
Comments