May 2018 Vol 73 No. 5
Rehabilitation
NASSCO Standard Bearer: Ed Kampbell, P.E.
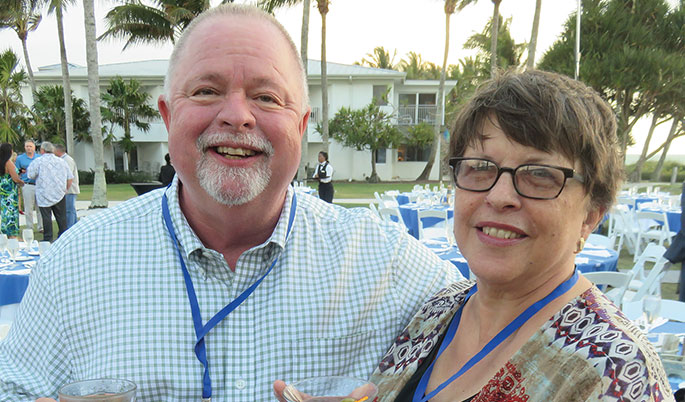
I’m a product of Little Rock, Ark. Even though the year was 1971 when I graduated from Little Rock Central High School, there was still some residual turmoil from when the school became integrated in 1957. After Arkansas Governor Orval Faubus surrounded the school with National Guard troops to prevent court-ordered racial integration, President Dwight D. Eisenhower sent 1,000 Army paratroopers to enforce the court order.
After high school, I got married and my wife Lynn and I spent our first seven years of marriage supporting each other through college. I worked first so she could earn her nursing degree; then she supported us while I got my Civil Engineering degree from the University of Arkansas. Graduating in 1977, my first consulting assignment was with McClelland Consulting Engineering where I worked in the water sector for five years while concurrently working to become a P.E. I was fortunate during this timeframe to design several new water and wastewater treatment facilities as well as modify and improve several others. It was a small office and my boss liked to load me up with work.
In 1983 I went to work for the Little Rock Wastewater Utility (LRWU) where, as the director of engineering, I was responsible for over 1,000 miles of sewer pipe with a given mission to transport and treat. In that position I served as the utility’s capital control officer presiding over a budget of $20 million annually. Unlike much of the industry at that time, we felt the need to be very proactive about the inspection and maintenance of our sewer lines. We invested in multiple CCTV trucks and ran them 16 hours every day, with our second shift crews working downtown in the evening hours to minimize disruption and improve productivity. Our goal was to inspect every pipe in our system at least once every five years. We also adopted a GIS mapping system to identify the conditions we were finding in layers and implemented a radio telemetry control system to our 44 pump stations to easily monitor our entire system in real-time.
CIPP
During those years, Insituform was just getting off the ground and I was an early adopter of this new technology called CIPP [cured-in-place pipe]. While at the city, I had a 10-inch diameter pipeline that was in desperate need of rehab, but it ran under a city block of buildings. That’s how I first became aware of CIPP as a solution to rehabilitate existing pipes without digging them up. Given our mission to transport and treat plus the challenging locations that needed renewal, I became a frequent employer of this fledgling technology over the next few years.
After two and a half years with the city, Insituform offered to train consulting engineers and municipalities in the use of their system. Given Insituform North America’s close proximity to Little Rock, I had the pleasure of working with Lynn Osborn and their entire R&D team, so I always kept abreast of the newest developments in CIPP technologies and was able to take that to the marketplace. Working under Bob Affholder’s company was a unique opportunity, as we were an aggressive team, constantly pushing the envelope. While the industry was cutting its teeth on 8 to 24-inch pipes, we were constantly raising the bar with respect to size.
This led to a noteworthy project involving the 60-inch diameter outfall sewer to Little Rock’s Adams Field Treatment Plant, which consisted of 6,000 linear feet of pipe that ran underneath a runway at the Little Rock Airport, as well as underneath a building where passengers checked in and were ticketed. It was discovered that the 40-foot deep pipe had two missing pieces. It was at least 30 feet below the water table, and it would take months to get the water down to a level where LRWU could make a point repair. The Airport Authority knew it had to be fixed immediately as it had created a huge hole beneath the ramp area where American Airlines jets parked at the gate!
The only solution LRWU felt it had at that time was to line the pipe using the CIPP technology. Further, because of the pipe’s location under the main runway, it was decided that one of the installs would have to be a single 2,100 linear foot length of 33mm thick CIPP. This brought Eric Woods, Insituform’s inventor, from England to observe the project because a CIPP installation of this scope, in both diameter and length, had never been done before. The logistics were also extremely complicated, including bringing the liner to the job site on two flat beds and using cranes to lift the ends off the transport vehicles and splicing them into one length in the field.
As luck would have it, the project didn’t go perfectly at first. The outside temperature soared to 106 degreesF and the resin became too warm due to the slowness of the wet-out process and it began to kick off. Those were the early days, so we didn’t have the static mixers we have now to continually initiate and pump the resin into the waiting tube; the resin was delivered in 55-gallon drums that we refrigerated at a warehouse near the airport, added the catalyst and then brought to the job site. Despite throwing dry ice and trying to save the installation, we had to cut our losses, re-group and then try again. The second time was a charm. The weather cooled down and the installation was completed without a hitch. The subsequent installs also went well.
New direction
After my time at Insituform I went on to work for Advanced Drainage Systems, a company that manufactures corrugated polyethylene pipe, a product which won the American Society of Engineer’s “Most Innovative New Product” award for their HC pipe. I was a product development team member. I would spend eight years with ADC and moved from Little Rock to Columbus, Ohio, where its headquarters was located. We did some amazing things from an engineering perspective. I worked with design engineers in over 42 countries during this timeframe. I designed a 36-inch diameter pipe for a depth of bury of approximately 1,000 feet, designed pipes in South America that saw a 100-degree F temperature change daily in an above ground trench, and eight hydroelectric plants in the jungles of Costa Rica.
After Advanced Drainage Systems I went to work for CSR Hydro Conduit, an installer of CIPP and U-Liner as their general manager in Hilliard, Ohio. I started with just one installation crew and grew that business to seven crews in 30 months. The Hilliard operation was the only one that installed both the fold-and-form HDPE and CIPP. We installed liners in 26 states. Because the Hilliard operation had the CIPP wet out facility, we served the entire CSR Hydro Conduit company with CIPP materials and installation expertise. Utilizing my knowledge of processing fold-n-form HDPE with steam, together with other members of the National Liner CIPP system, I drove the development of curing CIPP with steam rather than hot water.
In 2001, I got a call from Jerry Reynolds, the owner of Inliner Technologies, a technology provider of CIPP liners, about going to work for them. There was still much awareness to be gained for the CIPP process in the United States at that time, so I took the job. While there I developed a patent on CIPP curing that is based on a time versus temperature relationship of the curing process when curing with steam. Inliner’s support of the R&D process allowed me to show, through a series of experiments, that when using steam in the manner that we were, one could predict with reasonable certainty that the exotherm would move from the A end to the B end of the process, and that the temperature seen at the B end could be used to establish the minimum time required for a thorough curing of the liner. This allowed us to avoid the nasty surprises of lifts (or non-hardened spots).
After Reynolds, I started my own engineering firm to support the trenchless industry. The first three or four years my primary clients were Applied Felts, a manufacturer of felt and glass-reinforced liners, and National Liner, a company that supports CIPP contractors across the United States and Canada by providing liners, materials and technical support.
My experience goes way beyond CIPP, however. I was also very interested in exploring cementitious lining of manholes. AP/M Permaform, a manhole rehabilitation company, wanted to expand their offerings through the exploration of cementitious lining of larger diameter pipes. My firm was contracted to produce a design methodology they could take to the engineering community to demonstrate the required wall thickness for this technology. This, along with the subsequent second generation of the design of these rigid liner materials, have been well accepted by the engineering community.
This acceptance has led to my placement on a design solution team with Dr. Mohammad Najafi, director of CUIRE at the University of Texas, Arlington. CUIRE won a 24-month study to produce a standardized methodology for cementitious liners for AASHTO. I am also chairman of the task group for ASCE charged with producing a new Manual of Practice on how to design flexible liners. I have served periodically as an expert witness for the underground infrastructure industry.
NASSCO involvement
As you can see, I am very involved in many areas, but that involvement parallels my very first exposure to NASSCO, which was back in 1999. My boss asked me to become a NASSCO member, but he also told me that if he was going to invest the money in membership dues, I needed to be an extremely active member. I took that to heart and have been deeply involved ever since by participating on various committees, becoming an ITCP-CIPP trainer, and advising on special projects, when called upon to do so. I also was honored to serve as NASSCO president in 2009.
Everything NASSCO does goes back to setting standards. I personally am a proponent of NASSCO performance standards over vendor-supplied standards because many of those that come from manufacturers read like recipes. They don’t always lend themselves to a smooth execution by a contractor in the field. The documents need to recognize the realities of what happens between the engineer who shares what he or she learned in the design phase, to the contractor’s performance. They need to be built around real-world, achievable results.
When Norm Sirna and Ernie Alexander founded NASSCO more than 40 years ago, it was all about reaching engineers and getting those standardized documents in place so the work could be done both properly and profitably. My hope for NASSCO is that it continues to grow in its ability to communicate with and train the next generation of engineers to understand our business environment and the importance of setting standards for the assessment, maintenance and rehabilitation of underground infrastructure.
Comments