July 2018 No. 73 Vol. 7
Rehabilitation
Nuclear CIPP
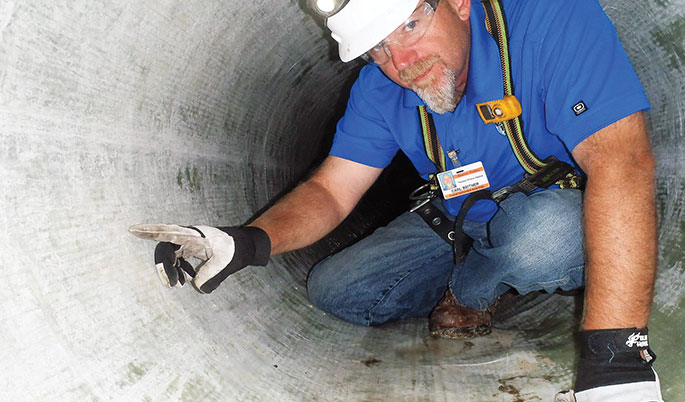
Patience, Safety, Security Paramount For Critical Plant Rehab Jobs
Most people are perfectly happy to stay away from any activity that could expose them to anything radioactive. We’ve driven past nuclear power plants, but few have ever entered their grounds or had the desire to do so.
However, Elite Pipeline Services has made pipeline inspections, rehabilitation and repair in nuclear power facilities an important part of its workload, and is recognized as an industry leader in this specialized field.
Elite has been serving the nuclear industry for more than 12 years, said General Manager Terry Bell.
Extensive underground piping
Bell explained that nuclear plants have extensive underground piping infrastructure that is critical to power generation and that all systems, regardless of purpose, are typically well-maintained and commonly evaluated.
The Nuclear Regulatory Commission (NRC) describes buried pipe as piping that is in contact with soil. Quoting the NRC, “At nuclear power plants, the buried piping systems are comparable to those used in other industries transporting a public water supply, and for oil and gas transmission.”
“Cooling water is the most common material transported in buried pipes,” Bell explained. Cooling water is generally taken from a lake or river and, except for a slight increase in temperature, is returned unchanged to the same body of water. Generally, this water contains only naturally occurring, background levels of radioactive materials. Some buried piping also transports smaller amounts of water that may contain slightly elevated levels of radioactive isotopes, usually tritium. Diesel fuel is the other commonly transported material.
“The NRC distinguishes between buried piping and other components beneath the surface because they are exposed to different environments; they corrode by different mechanisms, and they are protected from corrosion differently.”
Risks to buried piping Bell said preventive measures for corrosion and degradation are always front and center, and depending on the system, have NRC-mandated procedures.
“While buried piping is highly reliable,” he continued, “damage and corrosion can lead to leaks, which are often addressed with systems offline, unless the issue causes significant problems.
“In 2005, nuclear power facilities focused on a Buried Pipe Initiative (NEI 09-14) that took several years to investigate. Systems were found to be in much better shape than expected and, in fact, provided comfort that CP systems and program maintenance were working. When leaks do occur, they are often contained to ensure they do not create safety concerns for the plant or public . While some leaks do introduce slightly elevated levels of radiation into the ground water, they do not exceed regulatory limits.”
In selecting methods to address piping issues at nuclear facilities, Bell said engineers and decision makers always evaluate product data, history, performance, testing and references.
“Nuclear facilities are not testing grounds for new technologies,” Bell emphasized. “They value the input of industry providers and perform extensive research before allowing products in their systems. By the time a project is ready to be performed, plant engineers and program owners have performed their due diligence.”
As in other markets such municipal rehabilitation, using proven trenchless methods are commonplace. However, there are significant differences between municipal and nuclear work, and nuclear work proceeds at a much slower pace.
“Nuclear projects can range from several thousand feet to 50 feet, but all are equally important, Bell said. “Municipal work typically is high-volume and production-oriented, while nuclear is more low-volume, safety focused,” Bell said. “A contractor is often required to have backup equipment on standby because of the short repair windows and potential impact of equipment failure. It’s not uncommon to have three to five days for a repair.”
Nuclear plants constantly receive feedback from other facilities and place high value on the recommendation of others. What is or isn’t working? Has the contractor and/or product had past failure(s) and if so, why? Would the plant use the contractor or product again?”
“Contractors with a production mindset can find nuclear activity rather unnerving,” Bell said. “Nuclear contractors are selected for their excellent OE [operational experience], not speed. They are selected for nuclear familiarity and safety; for some, that can be a hard concept to grasp.”
Background clearance, badging
“It can be difficult staffing projects if employees aren’t nuclear capable,” Bell continued. “Plants require extensive background investigations and minor blemishes could be the basis for denial. Reference checks and in-depth reviews can be expected. A contractor who doesn’t have nuclear experience may find the entire experience overwhelming. Every contractor eventually will experience staffing complications, simply because of background or testing challenges. The 80/20 rule appropriately applies, with roughly 20 percent of the selected workforce gaining clearance.
“Most of Elite Pipeline Services employees are what we term ‘nuclear capable’, so we’re able to support multiple projects across several facilities.”
Bell elaborates on some of the elements involved in working in nuclear facilities:
Planning nuclear piping rehabilitation. “It is necessary to have a plan ‘B’ and plan ‘C’,” he explained. “There can be no impulse decisions. A nuclear project could take hours, days or months of planning. Contractors must think through all aspects of ‘what ifs’ and plan accordingly. Nuclear program managers and project managers do an excellent job toward this end. Ultimately, they are responsible for a contractor’s action and work diligently to ensure collective success.”
Staging can be difficult. “Plant access for staging equipment and material is time consuming and often frustrating,” Bell continued. “Everything must be evaluated by security when entering a protected area (PA).When projects are in PAs, everything is searched and the process of transfer inside the plant can take days. Security schedules determine everything. Contractors must remain patient and understand they are a small part of a much bigger picture.”
Safety is paramount. “Working safely is not an option – it is a requirement,” emphasized Bell. “The nuke factor alone elevates safety to a level unseen by most. Contractors that operate unsafely will find themselves quickly escorted from the premises. There are no shortcuts to safety. All activity is closely monitored and for those unaware – smile – you’re under surveillance.”
Similar but different. “Once onsite and everything is staged, the steps to relining a pipe are basically the same as a municipal job,” Bell said. “However, installations at nuclear facilities are rarely straight runs – they vary with challenging configurations, pressures, temperatures, applications, etc. Access is complicated, and half the battle is contractor/plant coordination and planning. Contractors must deal with interferences, safety barriers, rules and more rules. Location and application are everything. This is not in any way the typical manhole-to-manhole lining.”
Elite’s CIPP services include pull-in-place ambient cure, air-inversion (steam cure), and pull-in-place UV cure (see sidebar for details on two of Elite’s many nuclear projects).
“Interest in UV cure,” Bell said, “has really gained momentum due to limited equipment, reefer and boiler equipment, controlled cure, and friendly material storage,” Bell said. “However, all methods have their place.”
Work during plant shutdowns
Work in nuclear power plants usually takes place during refueling outages, but also may be during times of full operation, said Bell. Plants usually operate on an 18- or 24-month cycle, meaning every 18 or 24 months, they must refuel, depending on the plant. Outages typically last between 20 and 30, days with contractor activity limited to three to five shifts, for 24-hour coverage. Refueling focuses on turbine and reactor maintenance, as well as an array of activities related to plant maintenance and operation.
“This is a critical time for repair and often extremely stressful for everyone involved,” Bell said. “All activity, regardless of purpose and type, is well-planned and -executed. Projects experiencing delay can become ‘critical path,’ which is never a great place to be. Projects can be in the PA OCA (owner controlled area) or RCA (radiological containment area); the location determines working hours, clearance requirements, plant oversight and level of security.”
Recent Projects
Two recent lining projects completed by Elite Pipeline Services at nuclear facilities document how a common trenchless method is benefiting the nuclear industry.
Emergency repair to a ruptured 8-inch diameter steel fire suppression pipe was Elite’s first pressure-rated UC CIPP application. Length of the lining was 40 feet, with a design pressure of 150 psi and operating pressure of 100 psi. The pipe was only 5- to 6-feet deep, but digging wasn’t an option due to underground interferences and location.
“Elite Pipeline’s immediate response included a 550-psi rated 4.3-mm UV repair that was expedited direct from Germany,” said Terry Bell, Elite general manager. “Before lining could be made, the pipe required CCTV investigation and extensive cleaning. The line had very heavy tuberculation that was removed after several passes of jetting. The pipe was successfully lined and treated with internal joint seal terminations. The plant was able to quickly reenergize the system shortly after the repair.”
A second project involved upgrading 250 linear feet of 36-inch corrugated metal (CMP) storm pipe. This project was in the protected area (PA), which elevates the level of security and scrutiny, and was being done to address engineering concerns regarding a future, above-ground diesel generator site. With the additional above-ground loading from a proposed diesel generator and building, engineers needed assurance the pipe below could accommodate needs without future failure. In this case, CIPP provided the comfort level.
“After extensive engineering evaluation and review, a 36-inch by12-mm UV CIPP liner was authorized,” Bell said. “Because installation was inside the PA, plant security traveled to the manufacturer’s facility to verify and secure liner crating for transport. All equipment arriving at the facility went through a rigorous inspection process and was staged with plant assistance.”
Access for installation was a 48-inch manhole with 24-inch opening (downstream) and 24-inch CMP vertical (upstream). Confined space entry was complicated by the eccentric configuration and multiple inlets that required water mitigation. Ground water inflow was a constant challenge.
“Inlet piping,” Bell continued, “required isolation and careful monitoring throughout the work.” The liner was successfully cured using UV light trains and was end-sealed.
FOR MORE INFORMATION:
Elite Pipeline Services,
(616) 726-8286 , elitepipeline.com
Comments