July 2018 No. 73 Vol. 7
Rehabilitation
CIPL Project Sets World Record
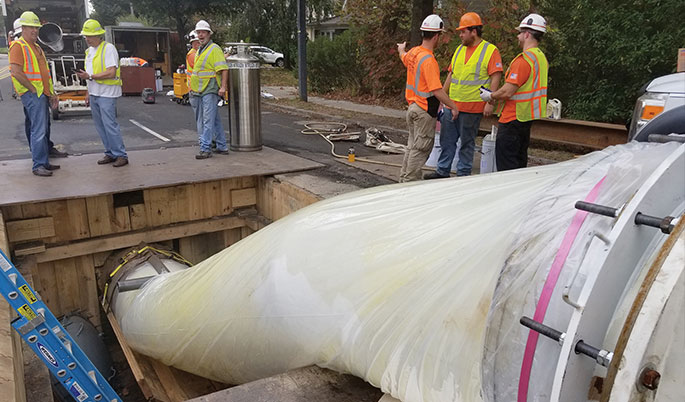
PSE&G’s 36-Inch Gas Main Renewal Reflects Growing Capabilities, Confidence
By Jeff Awalt, Executive Editor
The roughly half-mile stretch of South Orange Avenue framing the Seton Hall University campus is one of the busiest spots along New Jersey’s County Route 510, and some of its heaviest congestion is hidden beneath the freshly paved lanes that link Newark to the state’s scenic northwest.
When Public Service Electric & Gas (PSE&G) identified numerous joint leaks in an aging cast-iron gas main, the Newark-based utility faced the additional challenge of a crowded and complex substructure. Since its construction in the 1950s, the 36-inch, high-pressure main had become embedded in a maze of utilities, including water, telephone, electric, cable, storm drains and multiple sewer lines.
“A lot of short-term emergency repairs had been made to the pipe as it deteriorated over the years, and the mass of infrastructure that had built up around it left us with very few options for a long-term, permanent solution,” said George Ragula, distribution technology manager at PSE&G. “We had already identified 15 joint leaks along a 2,000-linear-foot section of this feeder main, so it was essential for us to develop a plan and take immediate action.”
Tapping its own deep experience and working in collaboration with Wenonah, N.J.-based Progressive Pipeline Management (PPM) and Karl Weiss Technologies of Berlin, Ragula and his PSE&G team completed a permanent renewal of the 36-inch main using trenchless methods and a cured-in-place liner (CIPL). The group overcame a series of challenges – both planned and unexpected – to set a new world record for the largest diameter gas main renewed with CIPL.
The project adds to a string of successful CIPL gas main renewals in ever-increasing sizes using the Karl Weiss Starline product. The growing track record for larger-diameter projects, combined with an influential university study on the lifespan of Starline liners, has sparked a long-awaited surge in demand for PPM, the exclusive North American licensee since 2002.
Absence of options
Along with all of the other structural limitations below South Orange Avenue, the presence of a 12-inch, low-pressure gas main running parallel to the 36-inch, high-pressure main added to the congestion, making it practically impossible to consider replacement of the cast iron pipe. Insertion of a smaller-diameter, higher-pressure plastic pipe within the host pipe also was ruled out as a viable option because PSE&G couldn’t afford to lose capacity on the critical feed.
PSE&G also considered excavating and encapsulating all of the leaking joints over a period of time, but concluded that this was not only impractical, but would have a major negative impact on traffic flow and the surrounding community. The utility had already identified 15 leaking joints and knew it eventually would have to repair all of the joints. With joints spaced at 18-foot intervals across the entire 2,000-foot stretch, the approach was deemed cost-prohibitive.
“We knew that re-laying it wouldn’t work because we couldn’t find a clear lane, and we concluded that there really was only one viable option that was cost-effective and offered minimal disruption, and that was trenchless renewal of the pipe using CIPL,” Ragula said.
PSE&G made the decision in June 2017 to proceed with CIPL renewal, using the adjacent low-pressure main as a relay to maintain service during low summer demand, but a detailed game plan was needed to ensure the project was finished before cold weather arrived.
Critical game planning
CIPL has been used for U.S. water main renewals since the 1970s, but the first gas application using Starline liners was in 1999. PSE&G was one of the initial adopters, and prior to setting the new record with its 36-inch project, was tied for a world-record, 30-inch gas main renewal. All that experience has taught Ragula the importance of advance planning, the need for long lead time and the value of working with a proven team.
“I was actually one of the people that was involved in bringing the Karl Weiss technology for gas to the United States 20 years ago, so I’ve got a long-standing relationship with them, and I believe it’s critical to work as an alliance and bring in all the experience and horsepower you can on a project of this magnitude,” Ragula said.
David Wickersham, CEO at PPM agreed, saying it’s one thing to go from an 8-inch main to a 12-inch main, and another thing entirely to go from a 30-inch to a 36-inch.
“You’re talking about tons of material, tons of adhesive, and it requires another class of heavier duty equipment. It took quite a bit of doing to ramp up to meet the demand for PSE&G on this 36-inch project, and we certainly took this challenge head on,” Wickersham said. “We were working closely with the patent holder and our supplier in Berlin, Karl Weiss, and with George’s team at PSE&G to make sure everyone was confident and prepared to get this done.”
Long lead times and careful planning to accurately determine quantities and dimensions are essential to starting and completing a major renewal project on time and within budget. A thoughtful approach to the sequence of work can also improve time- and cost-
efficiency.
In South Orange, onsite preparation began with abandonment of the 2,000-linear-foot (lf) section of the main to be lined. Before taking the 36-inch pipe out of service, two dead-ended lateral mains were installed. Excavations were made where lateral feeds were disconnected, and these were later used as lining excavations. The project team replaced deteriorated valves and made provisions for temporary relay feeds where valves were replaced. Before cleaning, CCTV inspection was run on each of the four planned project segments to confirm pipeline geometries, check for anomalies and assess internal condition.
A pig in grit
Ragula said lessons learned in previous renewal projects helped PSE&G solve problems in the planning stage before they happened – averting a potential failure of the liner material, for instance, by designing a reinforced patch to bridge a 4-inch tap hole in the pipe. But past experience has also taught the PSE&G team that there will always be unexpected challenges, and the record-setting 36-inch renewal project was no exception.
One notable example was a stranded grit problem that caught everyone by surprise.
Among the first steps in preparing the pipe for lining is to clean the interior with sandblasted grit and then use vacuum units to remove the grit. Earlier experience suggested that five vacuum units would provide plenty of power to remove residual grit and debris from each of the four segments after cleaning.
“We dealt with a stranded grit problem on our 30-inch job several years ago, and we learned that we had to put more vacuum power on the pipe as part of the cleaning process,” Ragula said. “We overdesigned that and really thought we had that problem licked, so we were just floored when we had about 150 feet of stranded grit inside one of the segments. That was totally unexpected.”
Two more vacuum sources and a special fitting were added to increase suction in segment 2 – the first of the four to be cleaned – but there were still piles of grit left behind after spending a day on it. A conventional pig was used, but failed to push the grit out. Finally, a custom pig was designed and fabricated with a tethered holdback and rollers to center the pig into the pipe and reduce the annular space. This increased the suction between the interior surface and the pig, which was slowly pulled against the airflow. It took another day, but by using the custom pig and monitoring with CCTV to confirm position and grit removal, the problem was solved.
Angle of attack
One of the biggest changes with a larger-diameter gas main renewal is in placement of the inversion cone. On smaller-diameter lining projects, the cone is placed in the entry pit, next to the host pipe.
To minimize excavation that would be required for the larger equipment on the 36-inch project, however, the inversion cone was placed above ground on the pressure drum, about 20-30 feet from the host pipe. Above-ground placement of the inversion cone makes it harder to optimize the entry angle and center the liner into the host pipe.
After the liner was cured and the ends cut flush, the team discovered a slight crescent-shaped piece at the entry end that was dis-bonded at the end point where the liner entered the host pipe. The minor issue was repaired on each of the four segments using epoxy and a mechanical retention band, which was used to hold the liner in place while the local epoxy repair cured.
These same liner entry angles also increased chafing from the retention belt, causing minor leaks on the exposed portion of the liner outside of the host pipe. At a few points along the liner, excessive friction between the belt and liner caused chafing and minor leaks. To prevent this liner chafe issue for segments 2-to-4, PSE&G switched to a four-inch belt and doubled the lubrication.
“I think the issue with the retention belt chafing the liner was primarily related to the sharp angles involved with our placement of the inversion cone above ground,” Regula said. “In hindsight, it probably would have been better to make the holes longer and perhaps spend more time lining up the inversion cone with the pipe entry point. By excavating down a little bit farther, I think the inversion cone could drop down into a little slot trench to reduce that angle of attack.”
Bolting into action
Most of the challenges – small or large, planned or not – had minimal impact on schedule. As an issue was being resolved, work was re-sequenced to maintain progress. But as the project neared completion and the scheduled in-gas date was looming, one of the tail bolts failed and tore a hole in the liner. This prevented the team from maintaining pressure and completing the liner installation, creating a serious threat to the project schedule with colder temperatures expected soon.
After carefully retracting the liner from the main, the PSE&G team considered its limited options. One was to gas-in the entire 2,000-lf section of 36-inch main while allowing the leaks to continue in the unfinished segment 2. Another option would be to relay that segment until trying to line it again in the spring. Those measures were avoided, however, when Karl Weiss agreed to manufacture an emergency replacement liner – manufacturing it, clearing customs and delivering it to South Orange in only two-and-a-half weeks.
The PSE&G team modified its design with additional tail bolts and worked nonstop to install the liner within 24 hours after it had been delivered. PSE&G gassed-in the lined main on Nov. 20, as winter weather was approaching.
Rising U.S. tide for Starline
Wickersham started PPM about 15 years ago after acquiring it from a Philadelphia company and coordinating the license agreement for Starline CIPL with Karl Weiss. In those days, a “large-diameter” project was a 12-inch pipe. Successful completion of 16- and 20-inch renewals were key milestones, but demand grew slowly.
“It has really come on in the last decade, and all the testing that’s been done on the product has helped us find a sweet spot for large-diameter cast iron in the past five years,” Wickersham said.
Most notably, the Starline liner underwent 10 years and $14-million worth of testing with the federal government’s Pipelines & Hazardous Materials Safety Administration (PHMSA), Cornell University, and NYSEARCH. This independent testing, in live pressurized pipe, determined a 100-plus year’s lifespan for the product. Although PHMSA did not take any action at the federal level, it indicated that it would not oppose decisions by state regulators to allow use of the liner technology as a replacement, versus taking out cast iron. Massachusetts, New York and Pennsylvania have already made this determination, which could make it significantly less expensive for utilities to use liner as
replacement.
“It’s an important change, because it allows gas utilities in those states to line the pipe now and consider it a composite pipe, so the gas utility can capitalize that cost, maybe with rate case relief, rather than considering it as a maintenance cost,” Wickersham said.
“From National Grid’s perspective alone, one study we have heard about was that if they were to remove and replace all of their cast iron, it would cost them about $6 billion over the next 10-to-15 years,” he added. “So this technology certainly has a place in their strategy to handle their cast iron reduction mandates at substantially lower cost.”
Responding to the growing demand, PPM has new equipment arriving soon that will enable it to handle CIPL gas main renewals up to 42 inches. That’s welcome news for Ragula, who has no plans to rest after PSE&G’s world-
record, 36-inch CIPL gas main renewal.
“I’m looking to do a 42-inch, and then I’m looking to do 48,” Ragula said. “I always want to try something bigger and better, and our team is ready for another challenge.”
FOR MORE INFORMATION:
Progressive Pipeline Management, (855) 246-6344,
progressivepipe.com
Karl Weiss,
+49 (0)30 809700-0,
karl-weiss.com
Comments