July 2018 No. 73 Vol. 7
Features
DCA/AGA Conduct 5th Annual Workshop Panels Highlight Wide Range of Topics
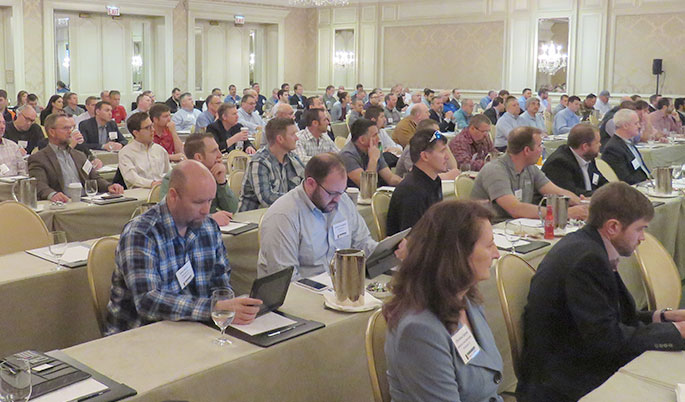
The Distribution Contractors Association (DCA) and the American Gas Association (AGA) recently hosted the 5th Annual DCA/CGA Workshop in Chicago. This two-day event is aimed at increasing communication and cooperation between natural gas utilities and the contractors who build the pipeline infrastructure for them. The workshop reflects the strong and still-growing relationship between the DCA and AGA, and addressed a wide range of industry issues and efforts– some ongoing and others relatively new to both associations.
The first day was kicked off by staff members from the Pipeline and Hazardous Materials Safety Administration (PHMSA) describing its vision and main end-goal as being “the most innovative transportation safety organization in the world.” While that may sound ambitious, PHMSA has a long and successful track record of working with industry to provide an effective, risk-based approach to regulating some 2.7 million miles of pipeline. Recognizing that more than 2.2 million miles, or 80 percent, of that is distribution, it’s little wonder that PHMSA is a regular at these workshops.
PHMSA explained the principles behind a risk-based regulatory approach: the administration establishes minimum safety standards and enforces them with a focus on safety performance. Pipeline operators hold the responsibility of understanding and managing risks associated with their unique systems, and dedicating resources to address those risks. When industry and government work in good faith with these concepts in mind, pipeline safety and program effectiveness can be achieved at the highest levels
After describing pending rules that impact the gas distribution sector, PHMSA addressed the administration’s take on pipeline Safety Management Systems (SMS). These systems include a “Plan-Do-Check-Act” cycle of determining the steps that need to be taken, implementing those steps, periodically reviewing them and making changes or improvements, if necessary. It allows the pipeline industry to progress from a reactive to proactive, and even predictive, approach to safety.
PHMSA’s Voluntary Information Sharing Working Group is developing a secure system that encourages collection and analysis of pipeline integrity and risk assessment information to improve pipeline safety in all sectors, including distribution. According to PHMSA, this effort aligns well with pipeline SMS by sharing best practices and lessons learned, engaging all stakeholders, and striving for continuous improvement.
AGA celebrates 100-year anniversary
An AGA representative provided the lay of the land at AGA, which has served the gas distribution industry for a century. The organization continues to invest significant resources to increase safety and efficiency in the distribution sector. AGA has widened its messages well beyond encouraging reasonable and risk-based regulations and is making a point to describe the many benefits that come with natural gas, such as its abundance and affordability, and declining trends of natural gas leaks and methane emissions.
AGA maintains a strong role in the Center for Energy Workforce Development (CEWD), of which DCA is now a member. Efforts to recruit and retain workers have expanded to engaging women and veterans, and providing scholarships.
As the industry continues to replace antiquated cast iron and bare steel lines, 41 states have implemented cost-recovery mechanisms to facilitate the process, which remains a focal point of the Distribution Integrity Management Program overseen by PHMSA. AGA is also pilot testing pipeline SMS and will be releasing its own SMS guidance document while the association continues to host SMS workshops.
Panels address wide-ranging topics
As always, the “meat and potatoes” of the DCA/AGA Workshop included several panel discussions that gave attendees a better awareness of some of the leading issues being tackled by industry associations and corporations.
PHMSA’s presentation made it clear that pipeline SMS is currently a hot topic in all sectors of the pipeline industry. DCA, AGA and several other national associations representing different facets of the pipeline industry plan to collaborate in an effort to promote pipeline SMS. The panel, moderated by a representative of the American Petroleum Institute (API) overseeing API Recommended Practice 1173 which addresses pipeline SMS, included a DCA contractor and gas utility representative with extensive experience in implementing SMS concepts in their respective companies.
A local distribution company (LDC) representative made it clear that “operators cannot be successful without contractor participation.” This operator is currently working with several other LDCs and conducting a pilot project to gauge their own effectiveness. The systematic SMS approach was described as a very big effort and requires a complete shift in approaches to pipeline safety -from compliance with a safety “checklist,” to striving for continuous improvement with buy-in from senior management.
The LDC representative also said that operators need to engage with their contractors, and contractors have to share “what keeps you up at night” with their LDC customers.
The DCA contractor on this panel, who has maintained a certified SMS for several years, agreed that increased cooperation will only improve SMS programs for both operators and contractors. Conducting a full gap analysis with API RP 1173 was “eye opening,” he said, and underscored the importance of striving for continual improvement. It was also noted that while PHMSA has insisted it is not looking to regulate or require SMS, the more the industry can demonstrate a commitment to SMS, the more likely it can avoid prescriptive SMS requirements.
As contractors are now being encouraged to develop and implement their own SMS programs, the panel was asked if there should be concerns about conflicting provisions between SMS maintained by operators and contractors. While this will be something to think about, it demonstrates the need for contractors to work with operators on a template that can be agreed on by both pipeline operators and the contractors who work for them.
Damage prevention tech, OQ
Last year, PHMSA released a congressionally mandated study on improving existing damage prevention programs through technological improvements and practices. Many DCA and AGA members contributed significant material and perspective for consideration during the study’s development.
This panel started out with a presentation from the lead staffer at PHMSA responsible for overseeing the development of the study and discussion about how best to promote their use in the gas distribution construction industry. PHMSA’s remarks included key findings of the study and what stakeholders should do with them. While PHMSA is not looking to require use of these technologies, the agency encourages their use.
The importance of preventing and mitigating cross bores was underscored several times in the PHMSA study, including the need for municipal governments to belong to their respective One-Call Center, and accurately locate and mark sewer mains and laterals
The issue of operator qualification (OQ) was the main focus during the first DCA/AGA Workshop in 2014 and the issue has been discussed at every workshop since. Over the past several years, DCA established a task force comprised of contractors, gas associations, OQ service providers and industry experts to investigate whether and how the industry can improve the OQ process, and provide more consistency in compliance with operator OQ programs. Because leaders of the DCA OQ Integrity Program (OQIP) are now looking to initiate a pilot program in several states, and participation from both operators and regulators is a must, this panel was very timely.
According to an OQ service provider (and an active member of the OQIP) on the panel, a primary driver of OQIP is the pending rule in PHMSA that will adjust OQ regulations to likely include new training provisions and requirements related to program effectiveness. However, where the pipeline safety regulations are the minimum standards, OQIP will “raise the bar.”
The OQ Integrity Coalition addressed the people, process and program validation elements that would need to be included in an OQIP, based on expectations of operators and regulators. The goal is to establish a program that delivers a more-consistent OQ process and ensures regulatory compliance, exceeds minimum requirements, focuses on core competencies, ensures program effectiveness, and provides verifiable audits and records.
Addressing the many workforce capacity challenges may result in an added benefit of the OQIP process. Credentials for trainers, proctors, evaluators and auditors are currently based on the B31Q standard. OQIP would include specific requirements related to testing (allowance of true/false questions, testing time limits, minimum passing scores, etc.), and provide a detailed description of core competencies.
A pilot program conducted in several states will test whether an updated approach to OQ compliance can elevate the integrity of OQ program, while increasing consistency and providing a set of standardized processes. The panel discussion was followed by an extensive Q&A period where the audience expressed positive feedback and the coalition described significant interest among several operators and representatives from the National Association of Pipeline Safety in pilot testing OQIP over the next few years.
Evaluation of pipeline inspection
Because pipeline inspection requirements are constantly changing in different parts of the country, this panel addressed sensitive issues and challenges during the inspection process by both in-house and third-party inspectors. Regardless of who the inspector is or where he/she came from, there is a need for qualified, extensively experienced inspectors. The panel, which included a third-party inspector and a gas utility representative, agreed that while technology is playing an increasing role in today’s pipeline inspections, the need for effective and experienced inspection personnel remains.
The panel evaluated the traditional inspection process, and if and how the use of third-party inspectors can be improved. A third-party inspector on the panel described the need for a “smart” inspector platform and “smart” tools to support that platform. This inspector was clear that the goal should be to “raise the performance and reliability of the average inspector” through thorough identification and selection, training, motivational incentives and inspection technologies. inspectors face workforce capacity issues and the constant search for talent. One solution to is recruiting older workers ,who may not perform pipeline work, but can inspect the work of others. Experienced inspectors also need to be provided, and embrace, contemporary “smart” technologies. Comparing “people versus technology” was described as a false choice.
Preventing, mitigating IR situations
Representatives of DCA’s Horizontal Directional Drilling (HDD) Committee described an increasing problem in the gas distribution construction industry. While HDD is widely considered a safe and environmentally sound method of installing distribution pipelines, “inadvertent returns” (IRs) are gaining attention and need to be addressed.
IRs are the unintended transfer of drilling mud to the surface during boring operations by way of fractures or fissures that can occur naturally, not necessarily as a result of boring operations. There is no shortage of confusion about what HDD is, IRs and the fluids that are used, and how IR situations can be prevented and mitigated. DCA is planning to discuss and resolve this confusion with a range of stakeholders, including federal agencies and even environmental groups.
In what turned out to be the largest panel of this year’s workshop, a panel of contractors, operators, plastic pipe manufacturers, service providers and experts in drilling fluids discussed the many intricacies related to today’s electrofusion process used in HDD operations. Recent questions about whether ingredients in drilling mud lead to ineffective bonding of electrofusion joints have led to extended public discussions on the subject.
The panel spent time to describe the electrofusion process, including the fittings and components that are involved. The importance of all related activities (wiping, scraping, pre-cleaning, etc.) was made clear. Greases, oils, soil and HDD fluids could potentially compromise an electrofused joint.
While the panel generally agreed that those involved in electrofusion must ensure correct installation through strict adherence to manufacturers’ standards, the process must be consistent and well-documented. Conflicting electrofusion guidelines can exacerbate this problem, and a new best practice is being developed by several industry stakeholders.
Gold Shovel Standard update
In the final panel of the workshop, the audience was updated on the Gold Shovel Standard (GSS), which continues attempting to establish performance metrics from damage prevention for excavators, operators and locators. While it seems that some operators involved in GSS are backing off the coercive approach of mandating contractor participation as a condition of doing business, most on the contractor side still believe GSS is a slap in the face of “shared responsibility” in damage prevention as promoted by the Common Ground Alliance.
Contractors in the audience weighed in during this conversation, stating that they have seen no benefit in participating in the program and that GSS communications appear to be “little more than a marketing ploy.” A final question raised from the contractor perspective was about the significant revenue that has been provided
to GSS from the contractor community, and where it’s being spent.
Comments