January 2018 Vol. 73 No. 1
Features
Making Pipe Dream A Reality
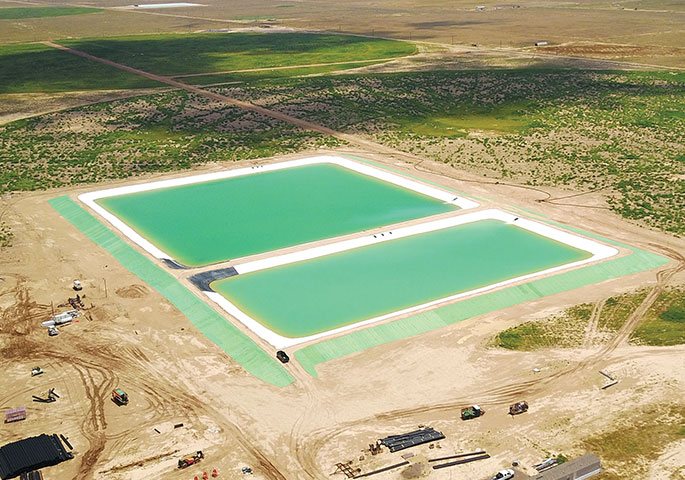
Hydraulic fracturing, or fracking – the process of cracking rock deep underground to release oil and gas – has revolutionized the oil and gas industry and helped reduce U.S. reliance on foreign oil. Industry estimates show U.S. crude oil production is up more than 85 percent, or some 4.5 million barrels per day, since 2008, and natural gas production rose more than 25 percent in that time.
One of the biggest components for fracking is the availability of a precious resource: water. It takes millions of gallons of water – in some cases, enough to fill nine Olympic-size swimming pools – to frack a single well. Much of the water for fracking is currently transported primarily via trucks or temporary lay flat hose.
Oil and gas companies are thirsty for water, especially in the arid Permian Basin, an oil-rich region spanning 59 Texas counties. To keep up with this voracious demand, in late 2016, Layne Christensen Company – a global water management, construction and drilling company headquartered in The Woodlands, TX – decided to invest in a new way to serve energy producers by:
Tapping non-potable brackish aquifers to reduce oil and gas companies’ reliance on potable water.
Building a high-capacity water pipeline and infrastructure system to deliver water to energy producers in the Delaware Basin.
To implement such a system, in November 2016 Layne contracted Lockwood, Andrews & Newnam Inc. (LAN), a planning, engineering and program management firm headquartered in Houston. To start selling water as soon as possible to its customers, Layne requested the system be operational by end of July 2017.
In addition to a feasibility study and hydraulic model analysis of Layne’s systems, LAN’s scope of work included the design of approximately 107,000 linear feet of 22-inch high density polyethylene (HDPE) pipe; 15,000 LF of 12-inch and 16-inch HDPE pipe; one 250,000-barrel storage reservoir; one 500,000-barrel storage reservoir and a 4,500 gallon-per-minute pump station.
Six existing groundwater wells, developed or rehabbed by Layne, supply water to the storage reservoirs. From these reservoirs, the well pumps convey water along the 22-inch transmission line to an existing storage reservoir on the north end of the waterline. The non-potable water supplied to the customer at the north end is used for fracking operations. Additional above-grade risers are also strategically placed along the pipeline to allow for connections to future customers. The system currently delivers up to 100,000 barrels per day (bpd) of non-potable water to one of the most active oil and gas drilling areas in the U.S. Additional capacity of up to 175,000 bpd will be used as needed via booster pump stations along the pipeline.
Engineered reservoir
One of the biggest components of the project, the storage reservoir, is unlike many others seen in the Permian Basin. Often, storage reservoirs are built as quickly as possible to satisfy an immediate need, without much thought to long-term durability. Many of these reservoirs are not often “engineered” structures. However, Layne and LAN knew the storage reservoirs built as part of this project would be used to deliver water to customers for several years and, as such, designed a number of elements to enable operational flexibility and long-term usage.
Traditionally, water is pumped over the berm using a series of above-grade suction hoses and a self-priming diesel pump. Although this setup is widely used, it creates above-grade obstructions around the reservoir and the constant need for refueling. As a result, the project team selected vertical turbine electric pumps and motors in lieu of a less-permanent diesel option. Furthermore, one of the reservoir’s primary features was burying all piping within the fence line to allow easier access and minimize obstructions around the facility.
To this end, LAN designed an 8-foot by 8-foot by 5-foot concrete sump to house the suction line and drum screen feeding the pump station exterior to the reservoirs. The sump included HDPE polylock and stud liner insert embedded in the concrete to allow the liner to be fused to the sump and create a watertight barrier. The concrete sump not only ensured the piping, hose and valves would be below ground, but also provided more than 13 feet of pressure head to aid in pumping operations, thereby reducing the project’s operational and maintenance costs.
Also, LAN designed the reservoir with a white HDPE liner, instead of the standard black liner often used in such reservoirs, to combat the effects of evaporation resulting from the extreme heat in the Delaware Basin. With every barrel of water in high demand, saving as much as possible during storage was critical to Layne. Other elements included overflow piping to control spillage during heavy rains, designing the reservoir’s berm with a 3:1 slope, use of a Recyclex Erosion Fabric to prevent erosion, and specifying 95-percent compaction requirements to protect the berm’s integrity.
In addition, the project team implemented novel construction techniques. Charger Services LLC of Midland, TX, was awarded the contract to construct the storage reservoirs. As the project involved a large amount of dirt work and mass excavation, Charger Services employed its sizeable fleet of scrapers and mass excavation equipment, and relied on an innovative technique for forming the reservoir’s surfaces. Charger was able to take LAN’s computer-drawn images of the reservoir’s surfaces and plug the data into the GPS unit on its surface equipment. This way, Charger was able to fine-tune the reservoir’s shape to meet specifications. Taken together, the storage reservoir is truly an “engineered” product offering long-term durability and ease of maintenance.
Project benefits
By delivering water via pipelines, oil and gas companies can drastically reduce water management costs, which typically run into 10s of millions of dollars. Transportation is by far the costliest element of water management for fracking. Traditionally, water is transferred via trucks or a series of transfer pumps and flexible hose installed above grade. The use of transfer pumps and hoses often requires extensive around-the-clock supervision, creates above-grade obstructions and is costlier to the end user when compared with below-grade permanent pipelines.
Furthermore, trucking can cost three times more than transporting water via pipeline systems. As the demand for water creeps up, truck delivery grows less practical. Not only are trucks more time-consuming supply options, they create safety hazards and contribute to road deterioration. Additionally, these big trucks emit huge amounts of carbon every year. By taking trucks off the road, this project provides a safer and more sustainable alternative.
Also, using non-potable brackish water lessens the fracking industry’s reliance on potable water. Much of west Texas is still very dry and some water systems remain under stress. Demand for fresh water is rising as the state’s population grows. A 2017 report by the Texas Water Development Board projects this growth will be more than 70 percent between 2020 and 2070 – from 29.5 million to 51.0 million. A virtual ocean of brackish water lies under much of Texas. Projects such as the Layne pipeline that tap into this resource will enable the state to conserve and use its potable water for drinking or agriculture purposes.
Complex challenges
The tight deadline presented several complex challenges. One of the biggest was the frequent change the project team had to make in the pipeline alignment due to issues with land acquisition. Even though pipeline construction was scheduled to start on May 1, land acquisition negotiations continued until April 2017. In a few instances, Layne couldn’t reach an agreement with land owners and, as a result, had to change the pipeline route alignment. This added five miles of additional pipeline to the project during the middle of the design. It required LAN to go back and rerun the hydraulic models, change the pipeline design, as well as coordinate numerous times with various contractors to ensure the project stayed on schedule.
Material availability was another challenge. After evaluating different pipe materials, sizes and pressure classes to determine the most economical pipe for delivering 100,000 bpd of water to the north end of the line, LAN chose a 22-inch HDPE pipe for its reliability, durability and cost effectiveness. With HDPE being one of the primary pipe materials used in the oil and gas industry, demand was very high. To ensure the tight turnaround for construction, Layne ordered the materials in February 2017 to allow the manufacturer enough time to produce the 22 miles of pipe. All told, the manufacturer stockpiled a large portion of the 22-inch DR-17 pipe well before the contractor was selected.
Furthermore, LAN split the project into multiple contracts to save additional time and money, with procurement done through a design-bid-build process. For the construction of the pipeline, the bid was split in half (53,500 LF per section) to allow contractors the flexibility to bid one or both sections depending on their manpower and equipment, and the option to work on the project simultaneously. Ultimately, Layne ended up awarding both the waterline section and pump station to a single contractor, C&C Oil Field Construction of Marshall, TX, which had the resources to finish the project in the tight timeframe.
Another tool that sped up the project significantly was a fast-fusion machine C&C used. This was noteworthy because there are only a handful of fast fusers in the country capable of fusing 22-inch pipe. By using fast fusers, C&C was able to double its production rates when compared to a standard fuser. At its high point, C&C was working 24 hours a day and installing pipe at a rate of 3,000 feet per day. Furthermore, C&C used a chain wheel trencher in lieu of a paddle wheel trencher to minimize the number of potential shutdowns if rock or other dense materials were encountered along the right-of-way.
Conclusion
The project team efficiently designed and constructed the project leading to a final project cost of $18 million, including land acquisition. More significantly, LAN’s design and construction management expertise resulted in the completion of 22 miles of pipeline in less than 90 days. As a result, Layne started delivering water to its customers on July 15, 15 days ahead of schedule.
While the initial contract is expected to ensure adequate cash flow, Layne is also planning to expand. The pipeline, which goes through the heart of the Delaware Basin and passes several oil and gas operators, has the capacity to support additional water sources and delivery points. It features 13 riser stations that customers can connect to. By just opening a valve, Layne can deliver water to a new customer.
About the authors:
Alex Kajdan, P.E., is a water conveyance engineer at LAN. He can be reached at takajdan@lan-inc.com. Manny De Pau, P.E., is a senior project manager at LAN. He can be reached at edepau@lan-inc.com
For more information:
Layne Christensen Company,
(281) 475-2600, layne.com
Lockwood, Andrews & Newnam (LAN) Inc., (713) 266-6900, lan-inc.com
Charger Services LLC,
(432)218-7674, chargerservices.com
Pipeline Plastics,
(817)-693-4100, pipe.us
Accel Fusion,
(701)260-6489, accelfusion.com
Comments