August 2018 Vol. 73 No. 8
Features
Challenges of Leak Detection on Produced Water, Crude Gathering Networks
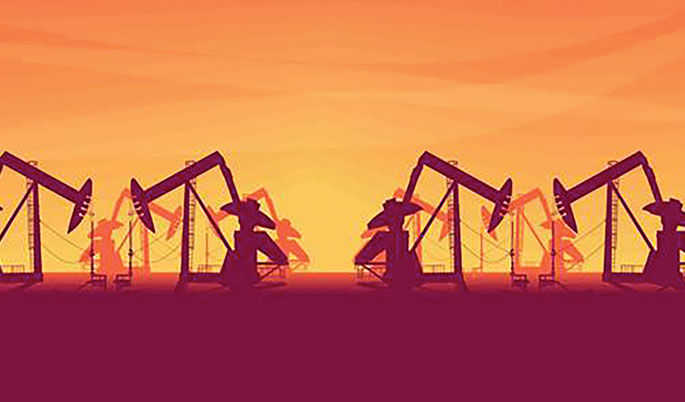
Oil producers laid hundreds of miles of gathering pipelines to keep pace with the shale boom across North America from 2009 to 2017. As a result, produced water production has increased exponentially with oil and gas production. Produced water is a byproduct along with the oil and gas. Oil and gas reservoirs often have water as well as hydrocarbons, sometimes in a zone that lies under the hydrocarbons, and sometimes in the same zone with the oil and gas.
U.S. oil and gas wells alone now produce over one trillion gallons per year of produced water, the inadvertent byproduct that must be contained and transported to disposal or reclamation sites.1 The everyday use of trucks to carry this dirty water creates challenges such as cost, safety and traffic congestion. A Barclays report stated, “Reducing transportation costs will inevitably drive investment in pipeline infrastructure for both produced water and freshwater. Although building pipeline infrastructure carries a high upfront capital expenditure, it reduces operating expenses down the line.”2
Produced water, like crude oil, is considered hazardous to the environment. It is prudent to consider cost-effective options for leak detection on these pipelines, as well as on the crude gathering networks.
According to the December 2016 leak detection study, Pipeline Leak Detection – Field Evaluation of Multiple Approaches For Liquids Gathering Pipelines, commissioned by the state of North Dakota and written by the University of North Dakota’s Energy & Environmental Research Center.3 “Field evaluation results suggest that the addition of CPM to an unpressurized gathering system could provide a 96 percent reduction in total spill volume when compared to daily flow accounting and would reduce the time to detect to less than two hours.”
The produced water pipeline infrastructure gathers produced water from temporary storage available at production sites and typically uses automatic pumping to transport the produced water to temporary storage, a disposal site or a reclamation facility. The crude gathering network collects crude from the wells and carries it to temporary storage or delivers it directly into a transportation pipeline.
Crude gathering networks and the produced water networks typically share some unique challenges for leak detection:
- Product composition is variable, depending on the specific well, production field and region, and density measurements are usually not available to the SCADA from each well.
- Gathering networks can have many injections and deliveries.
- Well-pads can be added weekly as new production comes online
- Dynamic nature of injecting from numerous wells at different flow rates
- Access is limited to the right-of-ways for adding instrumentation at the branch connections, so typically there is only flow and pressure data available from the LACT units at the wells and at the outlet.
- Constrained communications bandwidth limits the SCADA update rate to minutes, at best.
- Draining can cause slack in the network pipelines filling as injection pumps operate intermittently.
- Such challenges explain why many leak detection methods that work on transmission pipelines may be unsuitable for a gathering system or produced water system.
Factors that influence the performance of leak detection technology for these upstream systems include:
- Number and quality of sensors on the pipeline
- Availability and quality of the telecommunications system
- Pipeline operating scenarios, such as transient events from continuous start and stop of injections and deliveries, and slack flow conditions
Pumps on the wells at inlets of a gathering system frequently start and stop and flow rates change often; there is seldom a steady state, as normal operating conditions tend to always be transient. Some technologies are hard-pressed to cope with transient behavior and must desensitize to avoid frequent false leak alarms, sometimes to the level where they even mask leaks normally detected during steady state.
This paper explores the ability of the four main leak detection methods to overcome the unique challenges of crude oil gathering networks and produced water pipelines. Fiber optic leak detection was not considered because its high cost is unattractive in this price-sensitive industry. This is due to the risks in deploying it on existing pipelines and such systems cannot provide the size of a spill.
Only two systems with the ability to successfully detect leaks during transient conditions are Statistical Corrected Volume Balance (SCVB) and, to a lesser extent, Real-Time Transient Model (RTTM). The SCVB system can detect leaks under all operating scenarios: shut-in, running and transient operation. RTTM, on the other hand, must raise the minimum detectable leak size threshold during transient operations (virtually all the time in gathering lines) to reduce false leak alarms and may require additional, costly instrumentation.
Performance of leak detection systems
Volume balance can detect leaks on upstream systems if the detection time windows are sufficiently long. However, the North Dakota study found that the speed of detection appeared to be a function of pipeline conditions over the past day, pump operations and leak size.3 The transient nature of a gathering system and the constant packing and unpacking within the pipeline system make line balance systems unreliable. Simple line balance systems have far longer detection times for leaks when used with extended scan rates, resulting in significantly larger spills before detection.
Negative pressure wave (NPW) based leak detection
Although negative pressure wave systems only require pressure transmitters, they typically require high data bandwidth to provide readings every few milliseconds. The high data rate allows for better location accuracy, but additional data acquisition units and high bandwidth communications are required. In these remote areas, high bandwidth data can be difficult and costly to achieve.
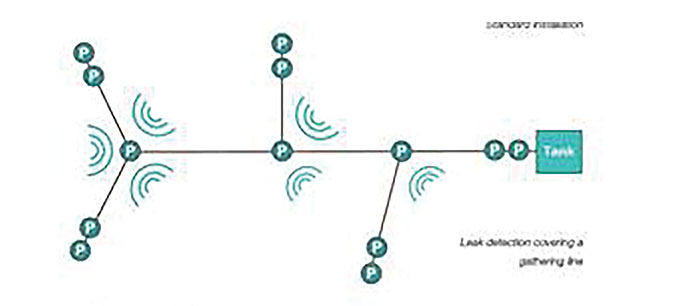
NPW systems only need pressure transmitters, but a pressure sensor should bound each branch. Adding this intermediate instrumentation can be difficult, as landowners often oppose access to install the additional pressure sensors and hardware. When there is access to install this hardware, the NPW option can provide very sensitive leak detection, detecting leaks faster than the other three systems under review.
Recent advances in non-intrusive sensor technology make it easy and cost-effective to add non-intrusive pressure sensors and even flow sensors anywhere along a pipeline (if the landowner permits access), even in locations that lack power or communications. There is no longer a need to drill or cut a pipeline at any intermediate position to add instrumentation. High-speed data collection and transmission devices can collect flow, pressure and temperature data, and perform the leak analysis locally, so the devices need only transmit the leak alarm and location back to the control room in cases with limited communication bandwidth.
Real-time transient model based leak detection
A well-maintained RTTM that accurately models the real-life behavior of a pipeline can provide good leak detection on transportation pipelines. However, as explained above, the nature of produced water and crude oil gathering networks makes them impossible to model with reasonable certainty. RTTMs cannot accurately model the transient behaviors caused by pumps frequently stopping and starting across the network, and must degrade leak detection at such times to avoid frequent false leak alarms.
An RTTM cannot accurately model the continually shifting composition and viscosity of the crude or produced water rising from the well-pads. The product compositions frequently change in each well-pad, change from well-pad to well-pad, and from oilfield to oilfield. The time taken to model additional pipeline sections as new wells come online makes it difficult to have an effective RTTM-based leak detection system. Furthermore, an RTTM requires accurate product temperature and density readings from the field, and these are seldom available.
Statistical corrected volume balance
The SCVB leak detection system has been successfully deployed on numerous crude gathering systems and produced water pipelines, and is the prevalent method used in the new shale boom pipelines. This is because it has demonstrated significant advantages over the other methods in real-life applications and through rigorous testing in the field. For example, the RTTM and volume balance methods rely on accuracy, whereas SCVB relies more on the repeatability of the measurements, making it the better choice regarding instrumentation requirement and scan rate.
SCVB can achieve good reliability and sensitivity, even with existing instrumentation of limited accuracy if the meters are repeatable, avoiding the high capital investment to upgrade instrumentation accurate enough to support an RTTM.
The Energy & Environmental Research Center tested the SCVB system alongside volume balance systems in the North Dakota study. The report concluded, “Ultimately, Company B2’s product identified all withdrawals without an erroneous false positive indication. Progress to detection was consistent during all tests despite pump cycling and slack variation, and detection occurred under steady-state, static, and transient conditions – all within a single CPM LDS package.
Additionally, Company B2’s LDS was the only LDS evaluated that provided leak
location estimates.”3 Company B2 used SCVB.
The SCVB system proved itself again when installed on a produced water network with multiple injections in Canadian winter conditions. It detected a leak at a well-pad in the first quarter of 2018 and located the leak with sufficient accuracy to allow the producer to quickly minimize the damage. It would have been difficult to detect this produced water leak visually because of snow cover and the produced water freezing soon after spilling out.
Based on the instrumentation requirements, infrastructure needed to support the CPM scan rate, transient functionality and high tolerance of composition change, the SCVB technology is the most suitable for gathering systems. Cases 1 and 2 below are two of many examples of its successful application on upstream pipeline networks.
Case 1: A crude gathering network
Early in the shale boom, the Atmos Pipe SCVB detection system was successfully implemented on several complex gathering systems; some collected crude and others collected produced water.
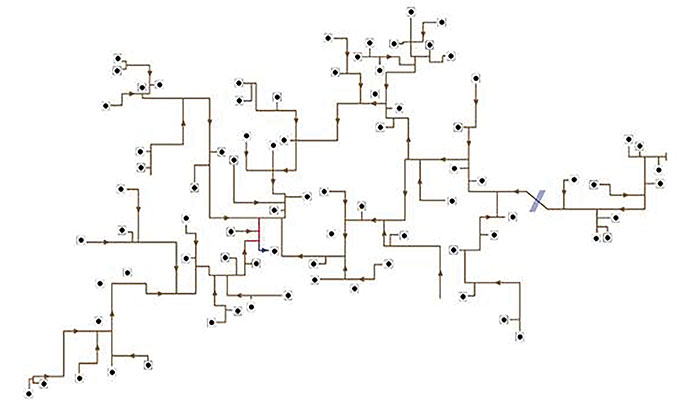
The first case shows a crude oil gathering system in Texas, which has maintained the SCVB LDS successfully for several years. First implemented onto the gathering system with 20 inlet stations, it has since been expanded to over 80 wells.
The initial SCVB LDS was installed with a 1 percent minimum detectable leak size sensitivity, and maintained that level as the network grew with complexity. The operators regularly test the system with physical product withdrawals and simulated leak tests to verify performance on the continually expanding gathering network.
Case 2: Produced water gathering system
The second case is an example of the SCVB leak detection system installed on a large produced water gathering system in Texas and shows only a section of the entire system. With multiple sectionalizing flow meters segmenting the network into separate hydraulic sections, it allows the client to optimize the performance of the leak detection system in each segment and maintain sensitivity as the produced water network expands unceasingly.
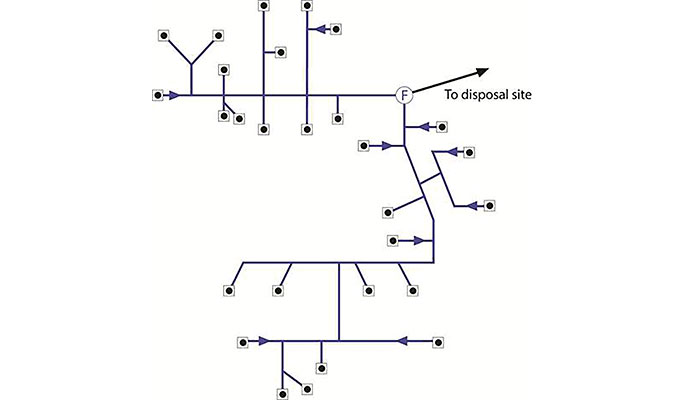
The system can detect a minimum leak of 1 percent of the nominal flow in 60 minutes in some sections, and a minimum leak of 2 percent of the nominal flow in 60 minutes in the remaining sections. These thresholds are set to assure high reliability to minimize disruption to operations from false leak alarms.
Conclusions
Oil and gas producers continue to add crude gathering and produced water pipelines in this shale-driven renaissance of North American energy production. With rising demand for nimble, efficient and cost-effective pipeline leak detection, SCVB technology has proven to be the most suitable and reliable for gathering systems. Field deployments show the SCVB LDS functions well with minimum instrumentation and slow data scan rates. Independent, third-party trials have proven that this cost-effective system detects and locates leaks during transient operations, and easily tolerates changes in product composition. This system continues to prove itself in the production fields, detecting real leaks quickly.
- References
- Reed, B. (2017, February 25). These Facts Suggest That Water “Commoditization” and a Water Price Index Is The Future Of Upstream Energy Water Management Cost Reduction. Retrieved from http://www.buzzle.comhttps://www.sourcewater.com/blog/water-commoditization/
- Barclays, Impact Series – 02, “Water and oil and gas, finding the right mix”
- Energy & Environmental Research Center, University of North Dakota. Pipeline Leak Detection – Field Evaluation Of Multiple Approaches For Liquids Gathering Pipelines. December 2016.
Comments