April 2018 Vol. 73 No. 4
Rehabilitation
Next-generation Technology Achieves Firsts for SIPP, Rehab Industries
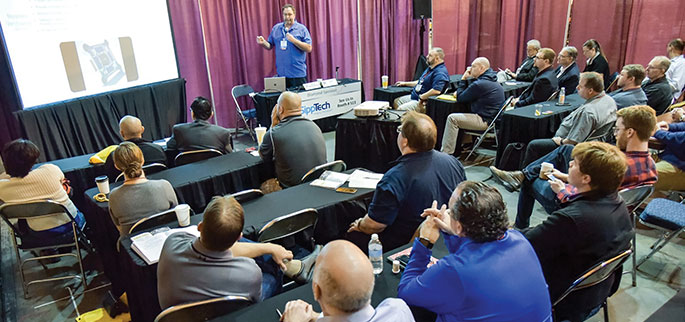
Due to their reduced environmental and community impact, trenchless technologies are increasingly preferred by municipal engineers and project owners – even required, in some cases – for rehabilitating and renewing the aging underground water infrastructure.
One trenchless method, Sprayed in Place Pipe (SIPP), involves applying one or more layers of polymeric material directly to the inside a pipe, in a single pass or multiple passes, via a hand-held spray for man-entry pipe, or a spin-cast-spray device in small-diameter pipe. It’s been used over the past 20 years to rehabilitate both gravity and pressure pipe systems non-structurally.
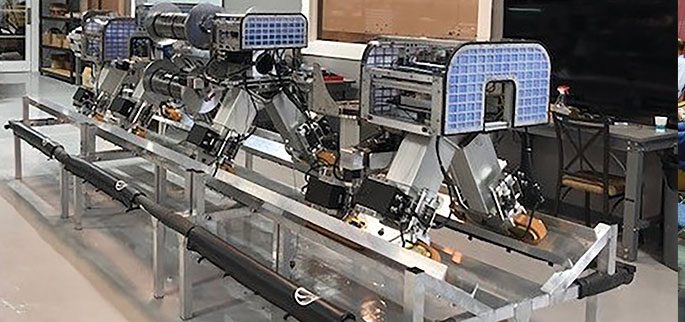
Specific SIPP uses include stopping and preventing internal corrosion, restoring hydraulic capacity, and eliminating water-quality deterioration caused by iron or steel corrosion and associated scaling. In the process, it’s been recognized for providing easier and faster (including, same-day) return to service, more versatility and cost effectiveness, and less environmental and community impact, compared to other trenchless methods.
Despite these advantages, SIPP application has been limited in pressure pipe rehabilitation, largely because its unreinforced composition cannot meet the “structurally independent” classification.
“As the term implies, this class of lining-structure is self-sufficient,” said Kent Weisenberg, CEO and chief technology officer of SippTech. “It’s designed to stand alone, spanning perforations, cracks and other discontinuities of the host pipe, and resisting all external load and internal pressure. Essentially, the host pipe is irrelevant, serving as a mold, or form, for the composite lining, which becomes a replacement, or ‘new,’ pipe.”

Such independence gives the lining-structure a useful life of at least 50 years, and a valuable edge over other rehabilitation options. In most cases, structurally independent is the most cost-effective method.
“Those funding the projects understandably want to get the most for their money, especially in today’s budget-cutting and -restrictive environment,” added Weisenberg.
Codependency issues
Rather than independent, traditional SIPP technologies are classified as “structurally interactive.”
“The lining and host pipe coexist, and share all external loads, pressures and resistance to failure events – generally not in good ways,” said Weisenberg. “Basically, they are considered a ‘Band-Aid’ solution.”
These not-so-good issues are not conducive to extending the design life of the pipe system.
“Current SIPP materials – polymeric or, more specifically, thermosetting plastics – have high resistance to bending and breaking, and the required rigidity, but are relatively brittle,” said Lin Li, Ph.D., chief mechanical engineer at SippTech. “Unless they are applied at considerable thickness, they can’t withstand internal working fluid pressure, transverse shear and overburden.”
But increased lining thickness also has consequences, Li explained. It leads to notably reduced pipe diameter and, therefore, decreased flow capacities and greater pressure drop. When applied in one pass, the thicker materials often tend to crack, primarily due to increased heat and localized stress, and significant loss of the polymer’s mechanical properties.
When a rigid polymeric material is adhered directly to the inside of the host pipe, shrinkage during curing can cause cracking or delamination. Direct application also prevents the rigid liner from surviving pipe failure events. Once fractures or remarkable deformations occur in the host pipe where the liner is adhered, the strains nearly become infinite on the liner system, causing it to crack, fracture or tear.
Another issue is material fatigue over time, or low creep resistance.
“In pressure pipe systems, which are under long-term, continuous stress, the strength and rigidity of polymeric/thermoset materials initially decrease rapidly, and then gradually further decrease with time during their service life,” said Weisenberg. “Managing the lining thickness doesn’t improve the creep resistance, either, due to the nature of the materials being used.”
In addition, the polymeric materials yield to radial and longitudinal shrinkage during the curing process.
“This will create a space (or annulus) between the liner and the host pipe,” said Li. “When pressurized fluid infiltrates behind the liner system at service connections, terminations and other discontinuities, the annulus renders the liner completely inconsequential, as the host pipe once again needs to resist all internal fluid pressures.”
All of this interactive, or codependent, behavior precludes traditional SIPP technologies from being a favored choice for the rehabilitation of pressure pipe systems.
Until now.
Novel approach
SippTech has pioneered a patent-pending approach, SippSteel, that overcomes the structurally independent deficits.
SippSteel is a three-component lining system comprising two, polymeric materials – one flexible and the other rigid – with encapsulated, carbon-fiber, filament-reinforcement between them. All these elements achieve intermolecular adhesion during installation, creating a three-layered structure inside pipe.
“The composite lining structure absolutely solves the inherent SIPP problems and affords the structural integrity to meet the industry’s structurally independent classification,” said Li.
This is accomplished through the use of materials that are highly resistant to fatigue, buckling forces and creep. In addition, innovative methods prevent failures caused by adhesion, and enable the SippSteel system to withstand all operating pressure and applied loads.
The flexible, or closed cell porous (CCP), layer is virtually impermeable to pressurized fluids and is applied directly to the inside of a cleaned host pipe. The rigid layer is bonded to the CCP – not to the host pipe, as in current SIPP technologies. In this structure, the flexible lining can stretch and yield to absorb strains, and reduce the reaction forces between the rigid liner and host pipe, when pipe movement or failure events occur.
“Essentially, the rigid liner is suspended in the host pipe, so external forces or strains are not fully transferred onto the rigid liner. Instead, they are dissipated throughout the CCP layer,” explained Weisenberg. “The CCP layer’s low Poisson’s ratio, and ability to expand and contract, continually fill and seal any annular space created by radial shrinkage of the rigid layer during the curing process.
“And since it’s impermeable, the flexible material can prevent fluid infiltration into any annulus at all discontinuities, such as service connections in the liner, therefore avoiding the potential for hydraulic failures that often occur with traditional SIPP and other trenchless technologies.”
Also unique to SippSteel is a filament reinforcement layer that further increases lining strength and stiffness, compared to today’s unreinforced, rigid SIPP materials.
“This extreme reinforcement effect allows for a thinner rigid layer – about 40 to 50 percent less – and no reduction in diameter, versus thermosetting linings without reinforcement,” said Li. “Additionally, the filaments resist a majority of the strain, thus appreciably reducing stress on the rigid liner caused by internal pressure or exterior buckling forces. Lower stress on the lining material significantly extends the working life of the liner against fatigue and creep failure.”
Beyond structurally independent
SippSteel is more than just the first structurally independent SIPP lining system. It addresses other customer needs and resolves systemic problems in trenchless technology, in ways that optimize cost-effectiveness and efficacy of the rehabilitation method.
As a thinner and more precise liner system, for example, it uses less materials, reducing the costs and time to install a much stronger lining. Not only does the thinner liner prevent reduced cross-sectional diameter, it actually increases flow capacity.
Robotic installation of the lining, in one pass through the host pipe, also saves time and costs, and corrects limitations and inconsistencies of traditional SIPP.
“The SippSteel system employs both individually specific and a synergistic combination of computer vision, LIDAR, ultrasound, RF, Wi-Fi, gyroscope, accelerometer and machine learning technologies,” said Julie Lee, Ph.D., SippTech’s chief electrical engineer.
“Further assuring precise application, the robotic apparatus is self-propelled, and all its mechanical functions are controlled autonomously by internal sensors and computer vision,” Lee added. “Continuous, real-time control and monitoring of thickness and fiber pitch (the distance between individual filaments) certify the lining meets all design requirements.”
The robotic system enables versatility that hasn’t been possible with traditional SIPP technologies. It can navigate pipe bends and valves, for example. And it can be operated by umbilical or autonomously, providing lining lengths of more than a mile from one access point.
The composite lining structure design is based on the pipe diameter, working condition, and optimal combination of lining thickness and dimensional filament pitch applied inside the lining.
“Adjusted according to the liner’s structural requirements, the pitch is typically reduced to apply more filament and increase the lining’s resistance to internal pressure, commonly referred to as hoop strength,” said Weisenberg.
In large-diameter pipe applications for exceedingly high internal pressure and/or overburden, additional, modular, robotic segments may be attached that enable the rigid lining material to be applied in multiple layers in one pass. This allows the filament to be repetitively applied within the rigid material matrix to create multiple reinforcement layers.
Also, when pipe will be subjected to a high potential of bending and/or shear forces, such as in elevated systems, longitudinal fiber reinforcement is incorporated in the robotic process.
In all these ways, SippSteel elevates SIPP to a new level of pipe rehabilitation that is smarter, faster, more precise and consistent, safer, lower-cost and versatile, as well as fulfilling the structurally independent liner requirements.
Monumental moments
Getting there has involved innovative and painstaking research and development. The multidimensional, composite lining system represents the company’s interconnected process of conceptualizing, designing, engineering and manufacturing proprietary polymeric materials, and robotics for their installation. Now, in the final analysis phase, SippTech is also benefitting from strong, strategic partnerships.
The Trenchless Technology Center (TTC), at Louisiana Tech University, has provided ongoing support and collaboration on the advancement of SIPP, and was awarded a contract for final verification of the scientific testing and empirical data on SippSteel.
“This new SIPP technology has high potential to drive the pressure pipe rehabilitation industry forward in the very near future,” said John Matthews, Ph.D., director of the TTC and principal investigator on the SippSteel project. “It is also a monumental moment for the TTC, as this is the largest contract ever awarded to us from a private company.”
In another agreement, SAK Construction is the sole national installation contractor for SippSteel. The O’Fallon, Mo., company, which serves the municipal, energy and industrial markets, “has delivered the most-advanced, field-proven products to rehabilitate
pipes globally for years,” said Weisenberg.
SippTech is currently in the final stages of assembly and testing of its LD 48/144 robotic system, and will officially launch this technology with SAK in late June. Its first real-world implementation will be structurally independent rehabilitation of both 60- and 72-inch, high-pressure, water transmission lines in early July.
“I am extremely proud of our SippTech team, as well as sincerely appreciative of all the support provided by SAK in expediting this launch,” said Weisenberg. “Since our prelaunch presentation on SippSteel at the UCT show this past February, the sincere requests for potential implementation of our technology, from both the municipal and industrial sectors, have been rewarding and inspiring, to say the least.”
FOR MORE INFORMATION
SippTech,
(844) 378-7477, sipptech.com
Comments