September 2017 Vol. 72 No. 9
Features
Cross Bore Analysis Review of Best Practices And Changing Trenchless Market
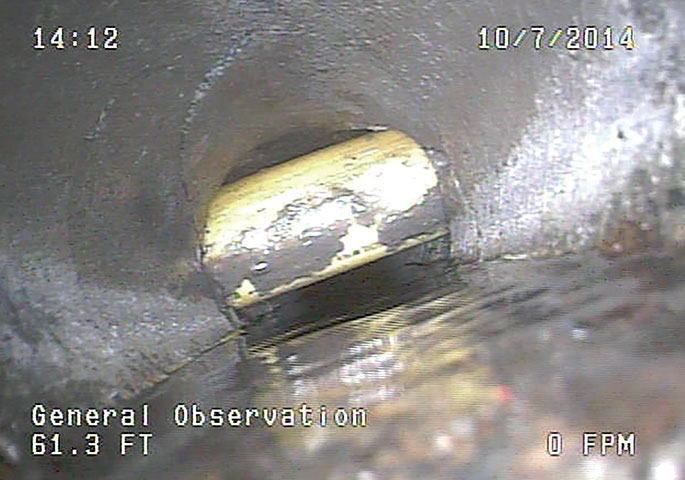
Since the first cross bore discovery in Kenosha, WI, in 1976, investor-owned utilities and municipalities have completed substantial research and discovery into cross bore prevention, trenchless construction innovation and safety awareness. As trenchless technology has improved, the ability of the contractor to avoid hazards has substantially increased. However, because of challenges with the One-Call system, lack of record-keeping, new equipment operators and other risk factors, the cross bore remains a primary topic of conversation due to the risk of hurting people or destroying property.
FMI completed substantial research and assessment of the current prevention programs by local distribution companies (LDCs), a review of the budding technologies and an assessment of the record-keeping that will influence the way we approach underground construction in the future. One of the most interesting findings was the array of approaches used by LDCs to address trenchless technologies.
For example, National Grid has regions within its system that require 100 percent open-trench construction in the replacement of natural gas mains and services. National Grid prefers to incur the extra expense required for identifying all potential lines in an area and the restoration of that property, rather than the potential liability of a cross bore. In a forward-thinking approach, National Grid builds in unit prices to contracts so contractors are not incentivized to cut any corners in their construction. In addition, National Grid regularly performs inspections and will even open closed holes to verify that the work was completed as promised. The attention to detail significantly reduces the risk of an accident that could cause loss of life or damage to property.
Conversely, a company like Piedmont Natural Gas, now a part of Duke Energy, assisted in completing the Operations Technology Development best practices for cross bore prevention and uses trenchless technology for many good reasons across its natural gas system. Trenchless construction limits interruption of traffic and impacts on local business, significantly reduces restoration costs and can install pipe with extreme accuracy in urban settings. It is typically less expensive and has fewer man-hour requirements in an environment where labor is one of the prime concerns. Many drillers have implemented best practices and are successful across the Piedmont system.
Challenges in approach
Some of the discrepancy between the approaches an LDC may take is simply when the sewer system was built. There are better records for construction that occurred more recently, so it is easier to identify sewer lines and design new gas installations to avoid conflict. The lack of information for construction that occurred in the late 1800s in some parts of the country makes cross bore prevention very difficult without performing an inspection of the area. GPR, sound probes and potholing can be solutions; however, some LDCs simply prefer to visually inspect all the lines that could potentially be encountered.
There are also significant challenges in accurately determining whether a cross bore has occurred. In the San Bruno accident inspection, the company contracted to complete the sewer inspections prior to construction was required to inspect and identify any potential cross bores and flag major defects in sewer mains. The company completed less than 50 percent of those investigations, had duplicate and faulty reporting, and encountered obstructed lines or unanticipated field conditions that prevented camera inspection of the sewer mains. The attempt to prevent an accident related to a cross bore failed due to the work of the inspection company and the inability of the city to provide proper oversight.
In addition to the record-keeping challenge, there are some macro factors that place the sewer and gas pipelines in much closer proximity to one another, and can contribute to a cross bore. Some of these include geographies that have high water tables, surrounding bodies of water or deeply buried gas lines. In specific locales, significant elevation changes, homes with no basements, private sewer systems or sewer laterals that exit somewhere other than the basement, create situations that provide a much higher risk of cross bore. These are particularly challenging for the contractor because if sewer system depth is not a defined, each home passed when installing a main or service line can create its own individual challenge and create significant expense in inspection.
Sewer lateral inspections are particularly challenging for a host of reasons – the first of which is expense. Most sewer systems are managed by municipalities that have limited budgets for inspection and mapping of their sewer systems. In addition, many states do not require that those municipalities participate in the One-Call system, despite being a pivotal player in underground construction. Because of this discrepancy, the onus for safe construction falls on the LDC and its gas distribution contractor. The contractor then must be concerned with difficult customers and property owners, sewer contractor resources, access to municipal sewer mains and hydrants, sewer blockages and sewer lateral piping configurations. In addition, the original construction can have differences between the code and actual because of the low-bid nature of municipal sewer construction.
Addressing hazards
Through our research, three different methods have arisen as means to address the potential hazard a cross bore presents: inspection, prevention and identification. The inspection opportunity occurs in the engineering and design phase of current projects and in understanding the infrastructure requirements at both the federal and state level. This can entail a full-scale review of a city’s sewer system, and a comparison to the current gas main and service lines for identification of potential areas where the lines are in close proximity in the underground. The inspection company then goes into the field to provide inspections of the municipality or the LDCs current pipelines, and recommends corrective action where there are blockages.
The best-in-class inspection then provides a digital map of the underground with specific three-axis mapping that is not dissimilar to the BIM models used in commercial construction. There are many LDCs that are at the forefront of this technology. The pipe that is placed in the ground is scanned and immediately uploaded into a digital copy of the LDCs infrastructure. Not only does the LDC know where its pipe is, but also when it was installed, who installed the pipeline and who manufactured the equipment, if there is ever a recall or product fault.
The prevention opportunity lies in the underground contractor working with the LDC to include cross bore prevention best practices in the costing of any job. Some of these practices include potholing to verify depth of a trenchless bore and to ensure there are no unknown pipelines in the area. Other common methods are open trench digging in areas that have a high potential for conflict, utilizing radio sonde methods, video-imaging or HDD “look-ahead” sensors. These activities can prevent future cross bores in installation or replacement of gas distribution mains and services. If priorities are aligned contractually, the contractor is incentivized to do careful assessment for the LDC in new pipe placement with trenchless technology.
Lastly, identification of legacy cross bores is imperative to prevent the accidents that cause significant harm and can create liability for either the contractor or LDC. Identification is a joint effort that requires coordination with the inspection companies mentioned previously and plumbers that are performing work on sewer line blockages. Common methods of clearing sewer lines with mechanical tools can destroy gas pipelines and create an immediate hazard for owners. With improved visual identifications or mechanical tools that identify a potential gas main or service, plumbers can work alongside the gas pipeline industry to ensure that homeowners are safe from devastating accidents.
Editor’s Note: FMI Corporation is a leading provider of management consulting and investment banking services to engineering and construction, infrastructure and the built environment. The company is active in researching industry trends and issues.
Comments