May 2017 Vol. 72 No. 5
Features
The Evolution Of Grouting Solutions
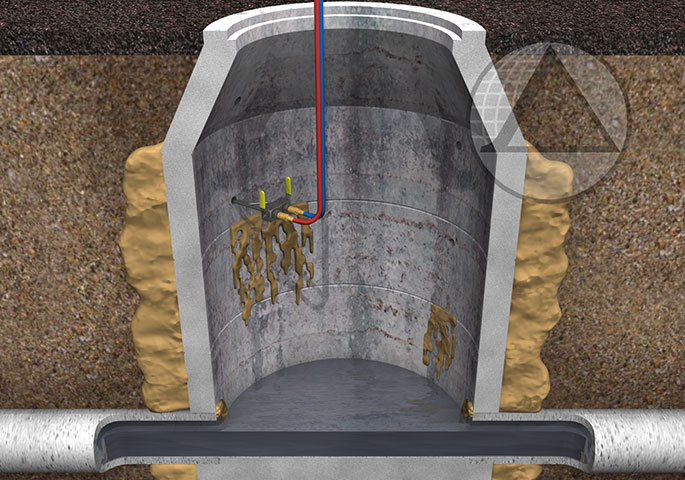
Injection grouting is described by its proponents as the first trenchless technology to repair leaks in underground pipes.
First used for municipal applications more than 50 years ago, injection grouting has advanced to become the most economical and reliable method for controlling infiltration in both sanitary and storm sewer systems, said Don Rigby, vice president of marketing and education at Avanti International.
Using remote packer technology aided by closed-circuit television (CCTV), the grouting process occurs from within the pipe by injecting a two-component resin with a predetermined gel-time through the pipe joint or defect and into the surrounding soil, creating an impermeable seal and stabilizing surrounding soil.
According to the U.S. Environmental Protection Agency, infiltration and inflow (I&I) of clean groundwater into a sewer system accounts for nearly 50 percent of the flow of wastewater into treatment plants.
“In addition,” said Rigby, “consequences of I&I go beyond excessive treatment costs. I&I contributes directly to sanitary sewer overflows (SSOs), including residential backups, and is a pre-cursor to structural failure, making the choice of rehab methods limited and far more expensive. I&I is responsible for reducing the lifecycle of the collection system and higher energy costs for pumping stations. Finally, I&I reduces pipe capacity by allowing soil fines into pipes, thereby requiring excessive cleaning and jetting of the system.”
Injection grouting is the only method specifically engineered to stop I&I by sealing a collection system at all entry points: mainlines, laterals, lateral connections and manholes. It also seals the annular space between a host pipe and pipe liner.
The most common municipal grouting technique uses an inflatable packer to isolate the joint or defect, perform an air test, inject resin if needed and, within a minute, conduct a second air test to validate that the joint has been sealed.
Mainline grout
Rigby said the process for grouting a mainline pipe from manhole to manhole includes:
- Cleaning and inspecting the pipe.
- Air testing all joints and circumferential defects that are not visibly leaking.
- Injecting resin/grout through the defective joint into the surrounding soil.
- Air testing the joint to ensure that it does not leak after the grout cures (typically 20 – 40 seconds in an 8-inch pipe).
- If it passes the air test, the packer deflates and moves to the next joint/defect.
- If the validation test fails, a technique called step-grouting is performed to ensure the proper amount of material is injected to seal the defect long-term.
Similarly, lateral and service line connection grouting follows a test, seal and validate process capable of sealing the service connection from the mainline and up the lateral pipe 30 feet – typically to the private property right of way.
Because every manhole is unique, techniques and technologies for stopping I&I vary, but acrylamide grout is often used for curtain grouting (creating an impermeable barrier on the positive/soil side). Urethane grouts may be optimum for sealing joints in a precast structure or point repairs for defects in the chimney, bench or pipe inserts. Most structural manhole rehab technologies require the manhole to be infiltration-free prior to applying cementitious coating or epoxy lining. Stopping the leaks can be accomplished from inside the manhole via “curtain grouting” or “crack injection” techniques; or from outside the manhole via “probe grouting” at street level.
“To date, the only proven method of stopping infiltration is the application of chemical grout,” said Dr. Vipulanandan, Ph.D., P.E., director of the Center for Innovative Grouting Materials and Technology (CIGMAT) and professor at the Department of Civil and Environmental Engineering at the University of Houston. “Based on its cost-effectiveness, durability and method of leak repair for sewer pipe joints, manholes and laterals, chemical grouting has proven to be the least expensive remediation alternative for stopping leaks and infiltration.”
Early days
“The forerunner of municipal grouting dates back to 1951 when researchers from the chemical giant, American Cyanamid, discovered that a combination of organic materials polymerized would have a setting time directly related to the catalyst used,” said John Manijak, business development manager/estimator for Michels Pipe Services, a division of Michels Corporation.
In 1955, American Cyanamid established a field services group to further test and develop a low-viscosity, fast-gel-time product used as a soil stabilizing system for dam cutoffs and sewer infiltration control.
In 1959, Penetryn Systems Inc. (later renamed Cues), filed a U.S. patent application for a mechanism sleeve packer for the internal sealing of pipe leaks. The mechanism consisted of the same basic components of today’s equipment, but far less sophisticated.
“Over the next 10 years,” Manijak continued, “early adopters of this trenchless technology continued to develop and perfect the delivery of acrylamide grout to leaking sewer joints. In its infancy, the grouting industry was led by installers such as Video Pipe Grouting, Chicago, IL; Gelco, Portland, OR; New England Pipe Cleaning Company (now part of Michels), Watertown, CT, and manufacturer Penetryn Systems (Cues), Orlando, FL.”
Rigby characterizes the 1970s, ’80s and ’90s as “Wild West Days” for municipal grouting.
“There were no rules or standards for grouting of sewer systems, and the work that was done was largely contractor driven,” he said. “Outcomes were inconsistent, often little more than temporary.”
During this period, grouting of sewer systems faced several challenges, including an effort to ban chemical grouting. That failed, and injection grouting continued its path to become an essential method for rehabilitating the nation’s sewer infrastructure.
Formal ASTM performance standards were introduced in the early 2000s. The Infiltration Control Grouting Association (ICGA), a division of NASSCO (National Association of Sewer Service Companies), released its first Operating Standards in 2012 with the collaboration of engineers, contractors, suppliers and municipalities.
Prepared for the future
The past 50 years prepared the grouting industry for the next 50 years, believes Rigby.
“Over those years, we’ve learned the single biggest impact to the long-term value of injection grouting is not the grout – it’s the quality of installation,” he said. “When the grout is mixed and injected properly, it will last a long time.
“The U.S. Department of Energy, after studying seven different grout formulations, determined that acrylamide grout, the most commonly used grout in the municipal sewer market, has a 362-year half-life in the soil.”
In place are ASTM standard practices for mainline pipes, laterals and manhole structures, and a suggested Standard Specification from NASSCO/ICGA. These standards have aligned engineers, contractors, and public and private property owners with well-defined procedures yielding predictable outcomes.
“Through education and dedicated grout schools, municipal contractors now know the importance of injection pressures, gel times, temperature effects and volume of material,” Rigby said.
Grout rig and remote packer manufacturers have optimized equipment for a more uniform conveyance of material. Material suppliers teach the importance of injection techniques, grout additives and gel times for long-term performance.
Different perspective
The grouting community today is much different than in the past – more science, less art – providing more predictable results.
Public works officials, consulting engineers, municipal contractors and technology players are far more unified behind these operating and performance standards. Engineers are able to write specifications around in-situ conditions, which vary based on soil type, groundwater tables and condition of the collection system.
The bidding process has changed – cost and volume of grout is now a separate bid item to encourage the use of more grout to stabilize the pipe, encapsulate the joint and stop infiltration for the long term.
“Injection grouting is not a competing alternative to CIPP lining,” Rigby said. “It is clearly complimentary and becoming a prerequisite prior to installing a pipe within a pipe. Most importantly, municipal stakeholders are more confident in its long-term value as the cost-effective method for controlling infiltration.”
Initiatives already in place will further the growth of municipal grouting and provide a level of confidence for engineers and owners that grouting is both a proactive maintenance practice and engineered construction project. Such initiatives include:
Release of an Inspector Training Certification Program for Grouting from NASSCO/ICGA.
- On-site inspection will be required on more grouting projects.
- Operating guidelines will continue to evolve.
“The grouting industry acknowledges the early pioneers of trenchless injection grouting 50 years ago,” Rigby concluded. “We salute those visionaries who paved the way for generations to come as we look to the future.
“It is an exciting time.”
FOR MORE INFORMATION:
NASSCO’s Infiltration Control Grouting Association (ICGA), sewergrouting.com
Avanti International, (800) 877 2570, avantigrout.com
Center for Innovative Grouting Materials and Technology (CIGMAT), cigmat.cive.uh.edu
Michels Corporation, (920) 924-4300, michels.us
Comments