May 2017 Vol. 72 No. 5
Features
Irrigation Project Testing Ground For Large HDPE Pipe Installation
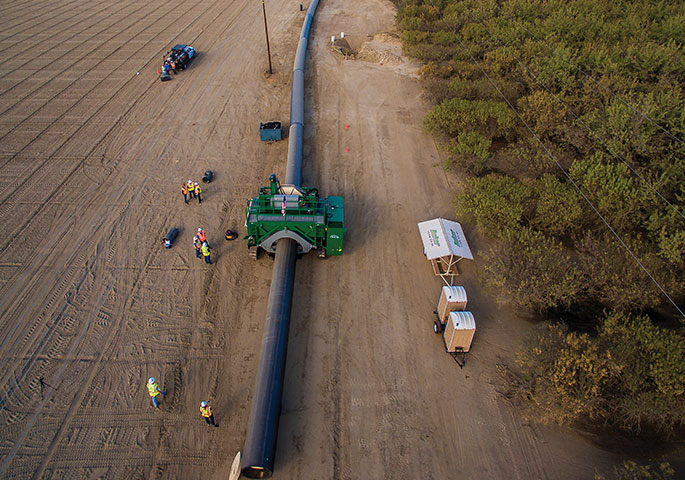
In February 2014, a news photographer snapped a picture of almond trees being ripped from dry soil in Firebaugh, CA. Baker Farming uprooted 20 percent, about 1,000 acres, of almond trees that day because adequate access to water was lacking, as the California drought continued into yet another year.
California agriculture relies heavily on irrigation, transporting water sometimes hundreds of miles. In order to keep the remaining trees living and producing almonds, Baker Farming needed an irrigation system upgrade.
For years, the farm’s irrigation was fed by a 48-inch steel pipe in the ground. “That pipeline is about 17 years old,” explained Rain for Rent Industrial Sales Rep Mike Bronze. “It has already developed leaks due to corrosion from being in the ground.” Baker Farming hired Rain for Rent in Fresno to replace the pipeline with a more reliable, longer-lasting, leak-free system.
When considering material for the project, Bronze said the priority was eliminating leaks while protecting against corrosion. High-density polyethylene (HDPE) pipe was selected because of its proven durability and corrosion resistance. “HDPE gives us the opportunity to install a piping system that will last more than twice as long as the original steel pipes,” he explained.
Saving water
“We’re preventing water from leaking and that’s a very important resource. Any time you can reduce loss of water, especially here in California, that’s a very big thing,” said Bronze.
Rain for Rent turned to long-time partner ISCO Industries to supply 13,000 feet of 54-inch DR17 pipe and various 8- to 18-inch sidewall connections.
The job came with another massive opportunity, as well. The design called for the pipe to be laid out in a straight line for about 2.5 miles. “The pipeline ties into the pump stations that are, in turn, tied into the California Aqueduct,” Bronze said.
This layout made this project ideal to use a first-of-its-kind fusion machine by McElroy. ISCO presented the idea of using the Talon 2000, a self-propelled, tracked vehicle designed for pipelining – an innovative approach to fusing large-diameter pipe.
The Talon 2000 has the unique ability to lift pipe from the ground with its powerful jaws, align it within the machine, fuse it and move from joint to joint down the pipeline, from one end of the job to the other.
“We had the option of being able to string the pipe out in one straight line and just have it drive over the top. We knew that was going to be the way to go,” Bronze said.
Winston West, in ISCO operations, worked with the machine and said the unit’s self-loading feature was one of the most striking differences. That made it much easier for operators working with large pipe, since the pipe stays close to the ground and is not hanging overhead, as can happen when pipe is loaded with equipment into traditional machines.
By using the Talon 2000, less heavy equipment and manpower were needed. On a job fusing large pipe with a fuse-in-place machine, a bulldozer is needed to pull the pipe, and a massive excavator or crane is needed to lift it and load it over the top of the machine. This requires at least two operators and two laborers. With the Talon, only an off-road forklift was used, requiring only one fusion operator and one forklift driver.
The ability to fuse two and a half miles of pipe without having to do a single tie-in – which takes a considerable amount of time and equipment – was another benefit. Fuse-in-place machines typically fuse several sticks of pipe together, then are moved down the pipeline to repeat the process. Once complete, at least three pieces of heavy equipment are brought in to help tie-in the fused pipe strings. The Talon simply moved on its own from fusion to fusion, without the assistance of heavy equipment. The pipelining method worked out perfectly throughout the project as it was able to keep up with the pace of delivery from the pipe manufacturer.
Different approach
“It’s a great machine, it definitely is. I think once people start seeing the capabilities of the machine itself, it will really fly. When you get on to larger projects − one mile, two miles and greater − that’s where you’ll really see the difference,” West said.
While the method of pipe handling is completely different with the Talon, its touchscreen interface is similar to McElroy’s other hydraulic machines. Users especially like the Talon’s feature that sequences the heater removal process and completes the fusion with a single input from the operator. It also includes a built-in data logging feature to record joint fusion data to ensure proper fusion procedures were followed.
McElroy conducted extensive fusion operator training on the new machine last year, and also sent its engineers and technical support personnel to consult throughout much of the job.
Site crew members were also pleased that easiness of the setup and deployment of the Talon allowed them to setup and perform a test fusion the first day. They were planning on doing five fusions a day, but found they were quite capable of fusing six joints in each 10-hour shift.
This job also featured a unique approach to saddle fusion developed by ISCO. The method eliminated the need for costly flanged tee fittings. It simplified the plan and reduced the overall cost of the project even more. To connect growing plot feeder lines, ISCO technician Steve Holpp used a branch saddle setup. The setup allowed him to make a saddle fusion onto the 54-inch main, butt fuse a flange adapter and backup ring to the saddle, blind off and perform a hydro test. As a final step, a special cutting tool was used to bore the mainline.
Multiple 8- to 16-inch connections were made using this setup, greatly improving efficiency on the job and allowing the technician to test his work before cutting the coupon out of the main. Typically, this process would be completed in four separate steps.
Not only did this project provide a reliable pipeline for a farm desperately in need of relief, it was an opportunity to provide the Talon 2000 for the first time, along with the specialized saddle fusion equipment, with remarkable results, revolutionizing the way large-diameter HDPE pipelines can be installed successfully and cost-effectively.
FOR MORE INFORMATION:
McElroy Manufacturing, (918) 836-8611, mcelroy.com
Rain-For-Rent, 800-742-7246, rainforrent.com
ISCO Industries, (800) 345-4726, isco-pipe.com
Comments