March 2017 Vol. 72 No. 3
Features
Pipelines And Earthquakes - Bracing For "The Big One" In Oregon
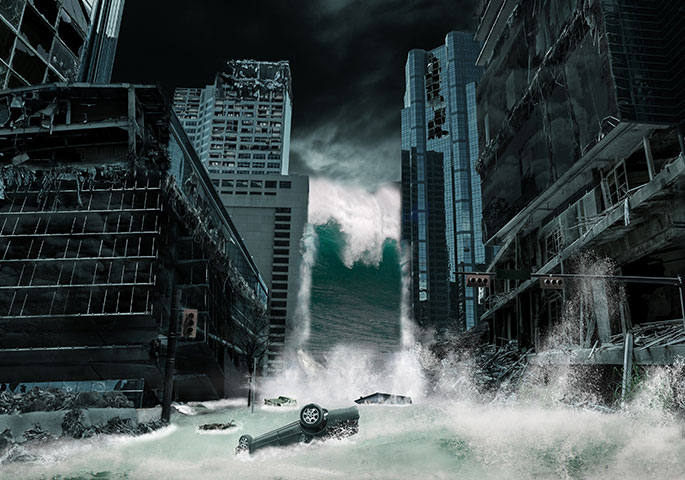
By Aaron Eder, P.E
Right after people started to feel safe enough to walk away from a recent summer blockbuster earthquake movie, “San Andreas,” New Yorker writer Kathryn Schulz had to go and scare the skinny pants off of Portland’s hipster crowd. Seismologists have long warned that a subduction zone earthquake off the Oregon coast is anticipated to cause far greater damage than a crustal quake along the movie’s namesake fault line. In other words, if California is expecting “The Big One,” the Pacific Northwest should brace for “The Really Big One,” according to Schulz.
The Cascadia Subduction Zone (CSZ) is the primary regional fault system in the Pacific Northwest and was created by the oceanic “Juan de Fuca Plate” subducting beneath the continental “North American Plate.” The subduction is occurring in the coastal region between Vancouver Island, British Columbia, Canada and the Mendocino Triple Junction in northern California. The CSZ earthquake events have the potential to generate seismic magnitudes up to 9.0, which translates into a duration of four minutes. Scientists estimate the odds of an abrupt release of CSZ forces in our lifetime to be roughly one in three over the next 50 years. The odds of “The Really Big One” are roughly one in 10.
In the Pacific Northwest, the area of impact is estimated to cover 140,000 square miles, including Seattle, Tacoma, Olympia, Vancouver, Portland, Salem, Eugene, and an estimated 7 million people. When the next full-margin rupture happens, the region will suffer the worst natural disaster in the history of North America. In colorful layman terms, Schulz has conveyed to us what scientists have been attempting to tell us for some time; by the time the shaking stops and the tsunami recedes, the area will be unrecognizable.
According to Oregon State University seismologist Chris Goldfinger, the gap between what we know and what we should do about it is getting bigger and bigger. He’s experienced firsthand a massive earthquake in the most seismically prepared nation in the world – the 2011 earthquake and tsunami in Tohoku, Japan. By many metrics, it will be as bad or worse after a major earthquake, with impacts spanning months, or even years, without electricity, drinking water, sewage systems, hospitals, etc. according to the State of Oregon’s map of impact zones (Figure 1) and estimated to time to restore service (Table 1).
Table 1: Estimated Time to Restore Services to Oregon Seismic Zones
Critical Service | Zone | Estimated Time to Restore Service |
Electricity | Valley | 1 to 3 Months |
Electricity | Coast | 3 to 6 Months |
Police and Fire Stations | Valley | 2 to 4 Months |
Drinking Water and Sewer | Valley | 1 Month to 1 Year |
Drinking Water and Sewer | Coast | 1 to 3 Years |
Top-Priority Highways (Partial Restoration) | Valley | 6 to 12 Months |
Healthcare Facilities | Valley | 18 Months |
Healthcare Facilities | Coast | 3 Years |
Source: Oregon Resilience Plan Executive Summary, February 2013
Fig 1: Oregon’s Map of Seismic Impact Zones
Photo courtesy Oregon Seismic Safety Policy Advisory Commission (OSSPAC)
Pipelines and earthquakes
Damage to pipelines is historically the primary reason for water system failures after an earthquake has occurred. The resulting water shortage for firefighting and extinguishing earthquake-caused fire ignitions has resulted in excessive, life-threatening fires. Extended durations of water shortages have an adverse effect on business operations, and having drinking water readily available is critical following seismic events for emergency operations facilities, hospitals, etc.
Water pipelines have historically been susceptible to earthquakes – in particular, shaking and permanent ground deformation (PGD) caused by liquefaction, and related settlement and lateral spreading. Liquefaction is the process in which seemingly solid ground begins to behave like a liquid, to the detriment of anything on top of it. Lateral displacement results when a soil layer liquefies, with the soil layer above it sliding downhill. Lateral spreading can result in soil movement as little as one inch to 10s of feet. Older pipes were installed using weak pipe materials and welds or unrestrained bell-and-spigot pipe, which contributed to damage or failure. Since the times when weaker or unrestrained pipes were prevalent, the pipeline industry has welcomed the use of materials that are more resilient to PGDs, including welded steel and restrained ductile iron.
Lake Oswego-Tigard Water Partnership
In 2008, the cities of Lake Oswego and Tigard, OR, (Program Sponsors) executed an Intergovernmental Agreement (IGA) to form the Lake Oswego-Tigard Water Partnership. Lake Oswego’s water supply was near capacity, and major facilities were in need of expansion and improvement. The city of Tigard was in need of a secure, dependable supply of water. Together, the program sponsors have expanded and upgraded Lake Oswego’s water pumping, conveyance and treatment capacity to allow for delivery of finished water to both cities’ customers. The major elements of the improvements, presented consist of:
- A new river intake pump station (RIPS) on the Clackamas River in the city of Gladstone capable of pumping 38 million gallons per day (mgd).
- 14,000 feet of 48-inch through 36-inch raw water pipe (RWP) from the RIPS through the Gladstone, under the Willamette River and in the city of West Linn to the new water treatment plant (WTP).
- Water treatment plant (WTP) in West Linn capable of treating and pumping 38 mgd.
- 42,000 feet of 48-inch through 24-inch finished water pipe (FWP) from the new WTP to the new Waluga Reservoir.
- 5 mgd Waluga Reservoir No. 2 in Waluga Park in the city of Lake Oswego.
- 20 mgd Bonita Pump Station and 3,000 feet of 30-inch and 24-inch FWP in the city of Tigard.
Pipe material selection
Selection of pipe materials is often governed by cost, preferences of operation and maintenance staff (due to familiarity with pipe types and having spare pipe parts readily available in stock yards), availability and jurisdictional requirements in design standards. For this reason, smaller distribution systems in America often require ductile iron pipe (DIP) or polyvinyl chloride (PVC) with bell and spigot joints as their standard. DIP is often preferred because of the perception that it is more reliable, has a longer design life, and is easier to tap for domestic services. In other jurisdictions, PVC is used because it is less expensive and corrosion resistant.
Large transmission mains, generally 24 inches and larger, are typically installed with DIP, welded steel pipe (WSP), or concrete cylinder pipe (CCP), with cost and operator familiarity, again, being typical selection factors. For this project, WSP and DIP were the materials initially selected for consideration. The evaluations focused on the following criteria:
- Pressure
- Layout
- Connections and Appurtenances
- Corrosion Control
- Constructability
- Linings and Coatings
- Availability
- Cost
This evaluation resulted in the selection of double-lap welded steel pipe with cement mortar lining and tape-wrapped coating for the RWP and FWP. It was later decided to allow polyurethane coating for both. During design, it was determined that the use of welded steel pipe with a ¼-inch wall thickness, 36 ksi yield strength would be appropriate for use on the project.
DIP and PVC are installed with bell-and-spigot push-on joints, mechanical joints or flanged joints. To prevent the separation of pipe segments due to unbalanced hydrostatic forces, joints are often restrained using wedges embedded in the gaskets.
Steel and CCP both use bell-and-spigot joints as well, but they are typically welded to convey thrust loads across joints. As such, welded joints are inherently restrained. Welding methods include butt welding, double-lap welding and single-lap welding.
Butt welding consists of two flush pipe segments being welded together end-to-end. Because of the integrity of this welded configuration, it is currently the strongest welded joint in the pipeline industry. However, this type takes the longest to weld and reduces production by as much as 70 percent. As such, butt welds are typically more expensive than lap-welded joints, and installation crews cost up to $25,000 per day.
Double-lap welding consists of welding two pipe segments together where the spigot is inserted into the bell. Welds are made on the outside and inside, resulting in symmetrical loading across the joint. Single-lap welds are similar, but only the inside or the outside is welded. Pipes 24 inches and smaller typically use single-lap with an exterior weld, due to the difficulty of welders fitting into pipes that small.
Joints are the weakest point in a pipeline alignment. Single-lap welded pipes with welds only on the outside or inside generate approximately one-third of the strength of the pipe barrel. Double-lap welded pipes with welds on both the outside and inside generate approximately two-thirds of the pipe barrel strength. Butt-welded pipes generate approximately full strength of the pipe barrel.
Seismic design
The International Building Code’s (IBC’s) approach to generating a seismic design event begins with the anticipated ground movement from an event with a 2 percent probability of being equaled or exceeded once in 50 years, which corresponds to a 2,475-year return period. This ground motion is then multiplied by a factor of 2/3 for the base design load.
For “important structures,” such as schools, jails and public assembly areas with more than 300 occupants, the ground motion is then increased by 25 percent. For “very important structures,” such as hospitals, emergency shelters, and police and fire stations, the design event is increased by a factor of 50 percent. When the base design load is increased by a factor of 50 percent, the subsequent ground motion becomes the original 2 percent in 50-year design event.
Water systems, including pipelines, are routinely defined as being “very important structures,” due to the need for drinking water and firefighting capabilities after earthquakes. As such, the design ground motion chosen for the RWP and FWP were the 2 percent in 50-year event, consistent with other elements of the Partnership’s program. This seismic event is also consistent with the highest design standard accepted around the world.
This design earthquake translates to peak ground acceleration (PGA) of 0.55 times gravity, a spectral acceleration of 0.70 times gravity, and a peak ground velocity (PGV) of 37.7 inches per second, which is used to identify the possible occurrence of assorted geotechnical hazards.
There is no universal code or standard for seismic design of water mains. However, WSP is the most commonly used material for large-diameter transmission mains in seismically vulnerable areas. WSP, selected for this project’s RWP and FWP, is one of the most seismically resilient pipe materials and is anticipated to provide adequate protection for the region’s seismic location.
Conclusion
Damage to pipelines is historically the primary reason for water system failure after an earthquake, but their continuous operation is essential for fire suppression and drinking water supply following natural disasters. Steel pipe with double-lap welded joints and ¼-inch wall thickness will be able to accommodate this project’s design seismic event and associated potential liquefaction and settlement, minimizing the risk of citizens and firefighters having an inadequate supply of water following an earthquake.
About the Author: Aaron Eder, P.E., served as the Raw Water Pipeline Lead and the Finished Water Schedule 6 Lead for this project. Eder is the Conveyance Lead for the Portland office of MWH (now part of Stantec), an international leader in the planning, design, and construction services for water and wastewater system and conveyance facilities. As the Conveyance Lead, Eder leads the business development and technical execution of conveyance pursuits and projects in Oregon and southwest Washington. He is a licensed professional Civil Engineer in Oregon and Washington.
Comments