July 2017 Vol. 72 No. 7
Features
Pipe Slitting Brings Cost, Time, Life-Saving Benefits To Airport
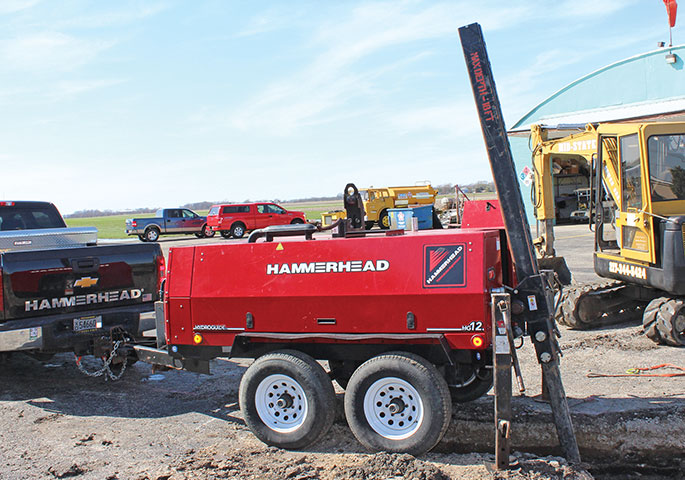
Pilots shout out “clear” to warn anyone they might not be able to see around their plane and to stay away from the propeller. While some pilots starting up their planes at Frasca Field, a privately owned, public-use airport located at the northern edge of Urbana, IL, might have seen men and equipment working the ground between two hangars, they were all well clear of flight line activities.
Unless the pilots had stopped to ask, they could not know water pipe spanning the breadth of the paved surface was being replaced right beneath their aircraft’s wheels. That’s because the Mid-State Sewer Services crew was using a technique called “pipe slitting.” While widely used to replace or decommission gas line services, the technique is being successfully used by Mid-State to expand the options it offers customers for noninvasive, trenchless water service replacement.
Mid-State’s owner, Steve Johnson, had performed spot repairs on this line in the past, so he was familiar with its deteriorating condition. He advised Tom Frasca, owner of Frasca Air Service, the airfield’s fixed-base operator (FBO), that it was time to consider replacing the water line completely.
“Otherwise,” Johnson told Frasca, “you’re at a point where you’re just going to find yourself making these little 10-foot repairs more and more often.”
Best course of action
Replacing the line between the two hangars was no problem, as it lay in open ground. Johnson could access the pipe with a simple narrow trench. However, a 340-foot run of 1½-inch HDPE pipe feeding the line from the FBO building was problematic. Lying perpendicular to the hangars’ shared water pipe, it joined the pipe at a tee fixture midway between the hangars. Except for that short bit of open ground at the tee, the pipe ran below the airfield’s tarmac, a portion of the field’s paved surface where planes park and transition between its hangars and runways. The trench for the original installation can be seen in pilot photos from the early 1960s. It was well past its useful life.
Traditional open-cut replacement of the water supply line with 1¼-inch CTS (copper tubing size) HDPE would mean opening a 2-foot-wide trench across the entire paved surface. While it wouldn’t shut down the airport completely, it would cause a significant disruption to routine activities for many days. Urbana’s municipal field, University of Illinois-Willard Airport, lies just on the other side of the metropolitan area from Frasca Field, is larger. Private pilots and corporations prefer Frasca for its lower traffic volume. Trenchless replacement was highly preferable for this job.
Even though his mid-Illinois service area doesn’t often require trenchless techniques, Johnson has a great deal of experience in them. About 13 years ago he added a Hammerhead PortaBurst PB30 to his equipment fleet to expand capabilities.
“Every once in a while,” Johnson said, “we would have to upgrade a line that ran under a road or patio or foundation. It sure comes in handy on jobs like that.” The portable 30-ton puller might sit unused for a couple of months, Johnson added, “but then I might have a streak where I need it twice a week for a while.”
A few years ago, Johnson invested in gas line pipe slitting tooling, giving him a similarly noninvasive, trenchless alterative for non-frangible pipe materials like HDPE or copper. These pipe materials deform rather than fracture, making them poor candidates for basic pipe bursting. Pipe slitting tools feature blades that sever pipes laterally, as well as expanders that press the old pipe away from the pipe path to make room for new pipe drawn in place by the tooling assembly as it progresses.
Johnson believed the pipe slitting technique would be ideal for the thin-walled HDPE of Frasca’s water line. However, he needed more than twice the length of his PB30 cable to slit from the hangar’s tee to the FBO.
He contacted HammerHead Trenchless representative Nate Hrabosky to get a longer cable, but Hrabosky counseled against using a PB30 unit for a run of that length. It would certainly have more than enough power, but the compact PB30 has no cable handling system.
“Can you imagine the weight of 350 feet of ¾-inch cable? It would be difficult to move, let alone manhandle during the pull, with all that cable having nowhere to go. For longer pipe slitting and pipe bursting runs, a winch-like device is a much better option,” explained Hrabosky.
The HammerHead HydroGuide HG12 comes with its own 2,080 feet of 5/8-inch cable and a pulling capability rated to 12 tons. Hrabosky also brought Johnson a lower slitting unit and two pipe slitting heads with replaceable hardened-steel blades from HammerHead Trenchless’ Same Path pipe slitting system.
Pipe slitting
Hrabosky stayed onsite to help Johnson, who used a mini-excavator to dig up and remove the 300 feet of water line that ran between the hangars. Where the tee had been, Johnson widened his 4-foot-deep, 2-foot-wide trench to accommodate the self-deploying downrigger of the winch. This 5-foot long, 4-foot-wide pit provided sufficient room for backing to support the pull against the trench’s soil wall.
Once the downrigger was deployed and set against the backing, Johnson threaded the winch’s cable through a slitting head pointed toward the FBO. According to Hrabosky, slick plastic pipe can have a tendency to slide in the ground toward the downrigger during a pull. Placing a second slitter backward on the cable in the working pit slits pipe before it gets to the downrigger.
Then Johnson paid out the cable completely through the water line to attach it to the Same Path assembly in the FBO’s basement. The new 1¼-inch HDPE pipe was attached behind the slitting assembly. The FBO basement gave Johnson plenty of room to work with the stiff coil of new HDPE as it was drawn through the hole in the foundation wall, following the pipe slitter assembly it was attached to. Johnson took the precaution of taping a copper tracer wire to the new HDPE, which would be pulled in with it. Should something go wrong, Johnson would be able to locate the wire. Plastic pipe itself cannot be located.
The pipe slitting process itself was quick and simple. “The pull is always the easy part,” said Johnson. “We finished the run in about 35 minutes.”
911
Johnson knew that trenchless alternatives to open-cut pipe replacement added greatly to the service he could offer his customers. It would save them demolition and restoration costs. It would allow pipe replacement without marring surface attractions. However, he probably was not thinking of it as potentially lifesaving until this job.
“An ambulance drove past us where we were working to meet a medevac plane that had landed,” Johnson explained. “I could see a little girl on the stretcher as they rushed her from the plane to the ambulance. She probably couldn’t have been more than four years old. Had we cut a 4-foot-deep trench across that tarmac, I don’t know … I suppose they would have still made it work out somehow … maybe found a way to drive around. But they didn’t have to. Nothing we were doing was in their way.”
Mid-State’s use of trenchless techniques to replace sewer pipe and water lines did save Frasca Field the cost of cutting up its tarmac. Its greater value, however, was that it permitted routine airport operations to carry on unabated, including emergency services.
FOR MORE INFORMATION:
Mid-State Sewer Services
(217) 344-5424
HammerHead
(800) 331-6653, hammerheadmole.com
Comments