May 2016, Vol. 71 No. 5
Features
Cradle Boring Makes A Comeback
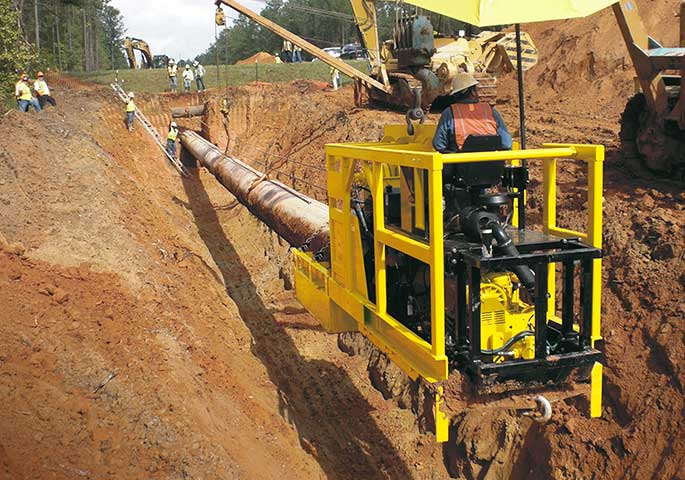
Installing pipeline across the United States, once a booming business in the 1960s, slowed in the late 80s and 90s. Today, thanks to the discovery of shale oil and gas, it’s back – and so is the cradle boring machine.
In fact, there has been a dramatic increase in pipeline projects worldwide in recent years due to the new finds of domestic oil and gas. Why? Because pipelines are a more cost effective and efficient way to transport oil than using trains or trucks. While the latest round of political plays have created a surplus, most experts predict this slowdown will be short lived and gas pipeline work continues regardless.
These long-distance jobs often call for about 50 bores stretched over more than 50 miles, which must be fast tracked so the owner can receive payback on the large investment in infrastructure as quickly as possible. As a result, cradle boring machines (CBMs), once popular during the heyday of cross-country pipeline installation more than 50 years ago, are making a comeback.
But today’s CBMs look and act different than they did in the old days. Modern units are designed with new safety features and the capacity to install hundreds of feet of pipe in a single day.
CBMs are designed for open-trench, cross-country pipeline road crossings and can efficiently install large steel casings up to 48 inches in diameter, or even 56 inches, with modifications. They can also install casing sections of up to 140 feet in one pass – a task that would typically be much more time consuming and labor intensive when using traditional pit-launched auger boring, especially given that it typically takes at least a half day to set up an auger boring machine.
CBMs operate like auger boring machines, by using an on-board engine and gear box to drive an auger that bores a pipe into the earth. But they are vastly different in terms of design, application and productivity. By using the cradle boring method, pipeline contractors can save time and increase productivity since they do not need to excavate and level large excavations for the boring machines.
While standard auger boring requires a launch and exit pit, a CBM is simply suspended from a pipe-laying, side-boom tractor. Then, instead of using cylinders for thrust, a CBM moves forward via a winch and a block and tackle that is attached to an anchor pipe — which is typically a large piece of pipe that lies perpendicular above the casing at the bore entrance.
By devoting less time and energy to digging, leveling and shoring trenches, and setting up a tracked auger boring unit, contractors can complete more bores per day. For example, contractors have been able to complete seven, 120-foot bores in one day – a 700 percent increase in production.
“When we initially came out with the CBM, we had a couple of pipeline contractors who were setting and leveling 120 feet of track using an auger boring machine. They were putting 100 feet of casing on it, and then drilling it in. These guys were getting in one bore every three days,” said Dave Gasmovic, president of McLaughlin, a leading CBM manufacturer. “When they switched to a CBM, they started getting in six bores per day.”
Cradle boring method
The first step in cradle boring is to excavate the dirt at the point of entry to obtain the cover required on the project. At the surface, auger flighting is inserted into each section of a dummy steel casing, and the casings are welded together to form a continuous string.
Next, an anchor pipe is buried crossway over the top of the bore entrance to provide reaction force for a winch, which is used to pull the assembly forward into the bore. Then, the dummy steel casing is attached to the cradle boring machine by placing the casing string into a cradle on the front of the machine. The auger flighting is then attached to the machine and the casing string is secured to the cradle boring machine.
The CBM then begins to turn the auger and advance the pipe into the ground. The entire string of casing to complete the road crossing is installed. If the road bore does not require an installed casing, the machine and casing are withdrawn and product pipe installed. In situations where the job involves a state highway and requires the pipeline to be housed in a steel casing, the pipeline contractor will leave the steel casing in the ground and just remove the auger.
Once the casing is installed, the cradle boring machine is disconnected and the auger flighting is pulled back through the installed casing to remove any remaining spoil from the dummy pipe. The dummy pipe is extracted, and the permanent pipe is installed using the side boom tractor.
Modern cradle boring machines have been re-engineered with improved capabilities that include state-of-the-art safety, productivity and control features.
In new CBMs, a casing is mounted in line with the driveline, instead of underneath the machine, eliminating rotating parts and exposed chains. Also, load-sensing circuits on the latches ensure the CBM pump senses when chains are loose, signaling the machine to automatically tighten them.
“You don’t have to worry about the pipe coming loose from the machine anymore,” Gasmovic said.
New CBMs also include technologically advanced features for operators, such as centrally mounted, fully adjustable seats that provide a clear view of the boring process and easy access to the control console. All new models from McLaughlin include hydraulic clutches that ensure quick driveline shutdown.
Additional considerations
When using a CBM, it is important to consider whether the operation has the correct size of side-boom tractors to support the cradle machine and casing when lifting pipe into the trench.
Also, side booms should be properly sized for the weight of the CBM and the casing being installed, and contractors must ensure the ground is solid enough to support both the side booms and pipe. Operators should only single part their winch line (never double or triple block it, which increases the force put on the cable and could cause the winch to break) and ensure the anchor plate is secure.
Finally, pipeline contractors should always secure the open trench right-of-way, make sure all existing utilities are marked and cleared by the relevant local authorities, and ensure that the trench is deep enough to catch the spoil – the cuttings coming out of the auger – as CBMs do not have paddles to discharge the spoil like track machines do, so it just drops straight below the machine.
CBMs are arguably the most efficient way to tackle this resurgence in cross-country pipeline jobs, when contractors are boring less than 140 feet.
“Every piece of equipment is designed for a specific application,” said Gasmovic. “If contractors are installing long water or sewer lines that have to be on-grade, they may be better off using a track auger boring machine. Contractors should work with their dealers to make sure they are using the right machine for their project.”
FOR MORE INFO:
McLaughlin,
(800) 435-9340, www.mclaughlinunderground.com
Comments