May 2016, Vol. 71 No. 5
Features
5,000 Linear Feet Of Overhead Power Lines Go Underground In Arizona
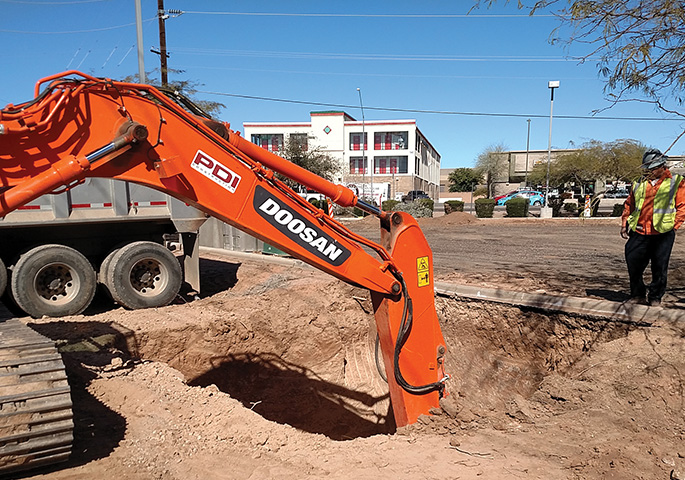
Millions of miles of overhead utilities are strung across the United States, but the unreliability of overhead utility lines as well as increasing maintenance and operating costs have led more municipalities, particularly in urban areas, to convert their overhead distribution lines to underground.
According to the Edison Electric Institute, almost 70 percent of the nation’s electric distribution system is built with overhead power lines; however, in the last 15 years, approximately half the capital expenditures by U.S. investor-owned utilities have been for underground wires.
In addition, there are many communities, such as the city of Mesa, AZ, that are converting overhead utilities to underground to improve the aesthetics of their neighborhoods and roadways.
Last summer, a local utility company hired PDI Construction – a division of Paramount Designs Inc. based out of Phoenix – to remove the existing 12 kilovolt (kV) overhead lines and bury approximately 5,000 linear feet of new 12 kV power lines as part of an aesthetics project.
PDI Construction is a full-service dry utility company that has extensive experience working in a variety of underground construction services. The company specializes in both horizontal directional drilling (HDD) and open-cut excavating/trenching; however, project manager Noel May chose the open-cut trenching method for this particular project. May knew he needed a machine that would complete the project in an efficient manner, so he selected a DX140LCR-3 reduced-tail-swing crawler excavator, which PDI Construction previously purchased from the local Doosan equipment dealer – Ditch Witch of Arizona.
“Instead of using a tractor loader-backhoe to install the conduit and cables, we used a DX140LCR-3 because of its reduced machine width, 19-foot dig depth and added maneuverability, helping our operators work in tight quarters,” May said. “We needed a machine that could safely turn 360 degrees and load material into a haul truck without interfering with oncoming traffic in adjacent lanes, May added.
The tail-swing radius on the DX140LCR-3 is just five feet, with a tail swing overhang of nine-inches over the side of the machine, which made it ideal for working in front of Dobson High School, which is a heavily congested area along West Guadalupe Road.
In addition, May’s operators needed a machine with good front and side visibility, as well as to efficiently see behind the machine when trenching. The machine’s selectable power and work modes also were beneficial, allowing operators to gain maximum efficiency and fuel economy at the jobsite.
Some excavator operators gravitate toward using a standard size bucket for applications, but this may negatively impact productivity. During the project, the DX140LCR-3 was paired with a 30-inch or 48-inch heavy-duty bucket to easily dig through a variety of soil conditions like clay and hardpan. May added teeth to the buckets to deflect the amount of bucket wear, helping the crew get more work done. In addition, the excavator was equipped with an optional quick coupler which helped expand PDI Construction’s attachment versatility on the jobsite.
“The quick coupler made it easier and faster for our operators to change buckets without exiting the cab,” May says.
Open-cut trenching
For the overhead-to-underground project, deciding between HDD and the open-cut trenching method primarily depended on the jobsite and soil conditions. At times, HDD can be the only option available to best navigate the underground congestion of cables, lines and pipes, according to May. However, for this particular project, the open-cut trenching method was the best suited for the job.
PDI Construction officials worked with local authorities to identify underground utilities before the Doosan excavator started digging. To make sure no utility lines were hit using open-cut trenching, the crew paralleled within four feet of water and gas lines and would check crossings every 20 to 50 feet.
After excavating the trench, the crew built a duct bank to help protect and consolidate the cables. Most duct banks use a protective concrete casing that surrounds the PVC conduits. For this project, the electrical cables were bundled together in a 2.5- and 3-inch PVC conduit using guide wires inside the bank. PVC allows for easier repairs on existing duct banks and require minimal digging. After the conduits were bundled, they were surrounded with an encasement, which is designed to prevent damage from water or physical stress.
“We put a clevis – a U-shaped or forked metal connector that can be fastened by a bolt or pin- on our DX140LCR-3 and placed the 200-foot conduit duct bank into the trench,” May said.
Once the conduit duct bank was installed, the DX140LCR-3 was used to backfill the trench. According to May, the project went smoothly and was completed in only a few months.
For more information:
PDI Construction,
(602) 258-7544, pdiconstruction.com
Doosan Equipment,
(877) 613-7970, www.doosanequipment.com
Comments