March 2016, Vol. 71, No. 3
Features
Mud Recycling Becoming Common For Mid-Sized HDD Rigs

Recycling and reusing drilling fluids is becoming increasingly common on jobs with mid-size horizontal directional drill (HDD) projects where previously that practice was uncommon.
Recycling isn’t for every job – it would not be practical on jobs with small machines making short bores – but contractors who are recycling on larger projects with 30,000 to 60,000 pound pullback equipment are reporting surprising cost savings resulting in overall lower project costs.
Savings come from using less water and drilling additives, less time in mixing fluids, reduced clean-up requirements and significant reduction in costs of hauling water to make the fluid and dispose of it after a job is complete.
Mud recycling is standard procedure on HDD projects with big drill rigs – to not recycle fluids on a long, deep bore with a big machine using a mud motor would make the logistics of handling fluids unmanageable and cost prohibitive, and the physical size of recyclers used on these projects would not permit their use on work sites of the mid-size drill rigs that do utility work.
Six equipment manufacturers answer questions about this industry development (note that not every source responded to each question):
Do you perceive a trend toward use of recycling on projects using HDD models with 30,000 to under 100,000 pounds of pullback?
American Augers, Richard Levings, director of product management: Yes, the cost of disposing drilling fluid has become too expensive and often is very difficult to access an approved disposal location. Higher levels of cleaning equipment and new technology will be employed to decrease disposal costs and reduce fluid system wear. Just having a fluid cleaning system is not enough, making it a priority and a focus is necessary to be successful.

Ditch Witch, Seth Matthesen, senior HDD product manager: Yes, in certain areas and certain types of jobs. HDD projects in adverse, rocky soil conditions use much more mud per foot, making it necessary for operators to either spend more time disposing of drill fluid or obtain fluid recyclers that can handle drills with more pullback range. This trend is more likely in urban areas where operators must drive much further to a dump site. Some cities are also implementing tighter restrictions for dumping liquids, making disposal even more costly.
Elgin Separation Solutions, Raymond Pietramale, marketing manager: Packaged mud recycling systems feature an all-in-one unit design, and the use of mud recycling has proven beneficial when used with mid to large size directional drilling rigs. The ability to continuously recycle drilling fluid and decrease the solids slurry waste saves costs associated with new fluid use and less waste for contractors to pay to haul off. The cost savings and environmental friendly impact is a significant trend being seen across the industry.
Mud Technology International (MTI), John Miller, chief executive officer: In this age of environmental consciousness for global sustainability, it is imperative that we look at every HDD job to determine how we can minimize the impact of our operations. Recycling, even with the smaller rigs, reduces the amount of water used, Bentonite needed and fluid haul off; saving time, money and making a contribution to the protection of our planet.
Thunder Products, Dan Sharpe, president: Yes.
Vermeer, Tod Michael, underground product
manager: Due to the difficulty and cost of disposing of drilling fluids in many locations across North America and Europe, we expect to see more contractors using reclaimers with smaller horizontal directional drills. The decision really depends on overall job-site mud volume, soil type and the kind of mud mixture. For recycling with smaller rigs, the decision whether to use a reclaimer will be driven by return on investment. It could be more cost-effective to just vacuum excavate the returns and pay disposal fees than purchasing a reclaimer and hauling it to job sites.
What are the benefits?
American Augers: Depending on the fluid system, a bore can be started with a given amount of fluid, and run the entire bore with that volume of fluid. The soil will consume some fluid so fresh water must be added as needed, but it will not be necessary to continuously run vacuum units to clean up and haul away fluid to be disposed.
Ditch Witch: Recycling fluid reduces water volume and removes the need for multiple trucks to haul and process water for the job site providing significant fuel cost savings. In addition to cost savings, HDD operators also see improvements in rig uptime by removing the need to mix drilling mud during the time the rig remains inactive.
Drilling-fluid recyclers also benefit the environment. With less fluid to clean up, transportation of fluid is reduced lessoning the carbon footprint by decreasing the overall emissions.
Elgin: Decreased costs on drilling fluid use; decreased costs on waste disposal; environmentally friendly; and increased profits for drilling contractors.

Thunder Products: Cost savings. A drill stays productive instead of having down time waiting on a vac. Far less drilling fluid is used. It is the most effective way to increase margins.
Vermeer: The main factor is reduced mud costs – not only water and additives but travel time to dispose of the used drilling mud, travel time to get additional water, the labor that goes into mixing mud and reducing idle time of the drill. If a reclaimer is used, it helps maintain the operation and allows contractors to use mud volumes needed for the job. There are many other factors playing into the decision to use a reclaimer,
including the type and size of a project.
Regarding savings, is it possible to estimate the cost savings from recycling on a typical project using a 40,000-pound pullback drill unit?
American Augers: Savings are very project and location dependent. The variable costs range from state to state and often from city to city. Disposal costs alone can vary immensely. An estimate would be on average of 50 percent or more savings when you consider disposal cost, equipment cost, consumables cost, labor, wear on equipment, mileage and work stoppage due to traffic delays.
Ditch Witch: An HDD rig with 30,000 pounds of pullback can pump approximately 20,000 gallons of fluid during the course of a project (this can vary depending on job-site conditions). Using the Ditch Witch MR90 specifically, the same volume could be pumped using only 1,500 gallons of drilling mud, saving 18,500 gal of water and as much as $1,500 spent for additives.
Elgin: Our experience is that when faced with the combined cost of disposal and new raw material costs, the installation of a recycling system can reduce total expenses by as much as 50 percent, depending on the sophistication of the recycling system deployed and the level of fluid reuse deployed. With that said, median savings will range from 15 to 30 percent. Drillers that manage a minimum of six jobs with a 40,000-pound rig will experience a tangible return on investment.
MTI: Using 50 to 70 gallons per minute as a base and a 1,000-gallon mixing system, not recycling requires mixing a new tank of mud every 14 to 20 minutes. Recycling provides the ability to reuse the mud, and only add water and chemicals as needed. This can result in great cost savings.
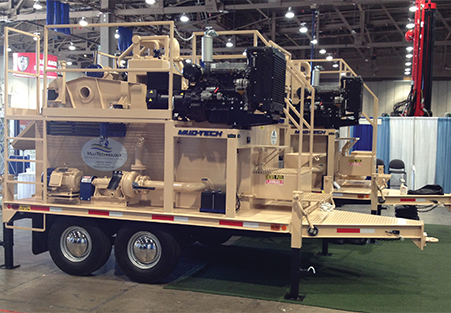
Thunder: Anywhere from $1,000 to $2,000 per day. There are savings on the dump fees of the vac or several vacs), savings on the driver and fuel hauling the vac, and savings on the amount of drilling fluids used. The productivity of the drill goes up.
Vermeer: Savings vary by job depending on the distance and difficulty of getting water, labor costs to get water to the job site and cost of hauling mud. Other variables are the type of soil, additive costs and whether mud can be processed at required rates. Disposing of high-cost additives instead of reusing fluids is a big factor in the overall cost of a project.
Can you provide brief examples of one or two recent projects with this size equipment that documented the cost savings and other benefits of recycling?
American Augers: On a recent 8-inch pipeline project, the right-of-way was very tight and the number of equipment on site needed to be reduced. The fluid cleaner being compact and productive, allowed the contractor to run continuously without having units in and out hauling fluid away.
Another pipeline project installing 16-inch steel pipe was in an environmentally sensitive area. Both mud motor and reaming passes required approximately 200 gpm flow rates. Once again, it was not feasible to operate any other way than recycling the drilling fluid.
Ditch Witch: Sonoma Underground Services switched to our recycler to reduce its mud-related costs. By recycling drilling fluid, the company reduced the amount of water and mud needed on the job site and eliminated daily vacuuming. On the most water-consuming day, the operators began with 2,000 gallons of mud and ended with 1,750, gaining three hours of drilling time by eliminating disposal runs and saving close to $2,000 for the day.
On another project, MasTec used recycling on a FTTH project. The company saved up to $100,000 per month throughout the length of the project from increased production and savings of drill fluid and disposal.
Elgin: Due to confidentiality we provide our customers, it would not be appropriate to comment on the specific savings achieved. However, Elgin can safely indicate that it has sold more than two dozen mud systems in the last two years to customers that were utilizing 40,000-pound pullback drills. Each of these customers identified a need to reduce operating expenses and lower their disposal costs.
Thunder: In Ohio, a contractor was not using a mud recycler and he was running three vacs to keep his 36,000-pound rig drilling. At some point during the day his rig would be down waiting on water or a vac, and every day his drill crew was idle 30 percent of the time. He introduced our recycler and began saving $2,000 per day. The rig went from 70 percent utilization to 95 percent utilization. Plus, mud pumps last longer.
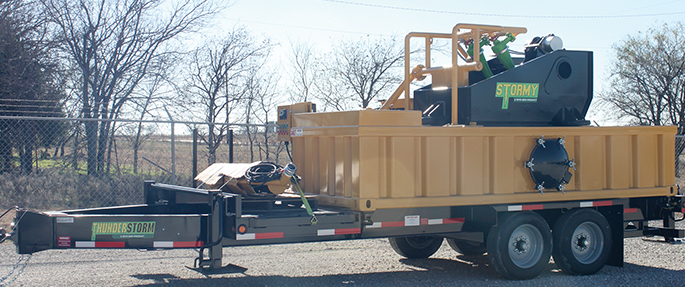
Can we expect to see more mud systems on urban job sites?
American Augers: Yes, current margins in the industry will force contractors to employ fluid recycling. Fluid containment and reducing risk of frac outs is paramount. Increasing annular flow to increase velocities to better clean the hole is necessary, and that is made possible by utilizing a fluid cleaning system.
Ditch Witch: Yes. As city restrictions on waste disposal get tighter, contractors will be forced to find other solutions, such as recycling, for HDD job sites.
Elgin: In today’s urban areas, environmental concerns regarding ground contamination of mud pits plays a major factor. Communities and businesses are taking on an increased role in maintaining the environment around them. The use of a mud reclaimer promotes a leave-no-trace ideal when drilling operations are complete.
MTI: Yes, due to changing regulations, education and more efficient drilling operations this equipment will become a standard fixture on job sites.
Thunder: In time it will become the norm. Mud recyclers pay for themselves rather quickly and it goes a long way on increasing margins. In the HDD market now we are seeing it work its way down into the smaller rigs. Five years from now they will become the norm, not just to increase contractor margins but environmental regulations will also drive it.
Vermeer: We expect to see an increased demand for reclaimers. It still is unclear if contractors will use individual reclaimers to support each drill or, if they will purchase a larger reclaimer and position it in a centrally located area to support multiple job sites. We’ve seen a few customers testing this business model.
Do you expect more companies to develop compact mud systems for this market?
American Augers: Yes, there are many options available today, but higher quality and more consistent performance systems will be developed.
Ditch Witch: This already is gradually happening. It will be a natural progression for companies to develop a product line to fit all drilling units in the marketplace. The market always is adapting to meet customer demands. We take customer feedback seriously and look for ways to improve their production times, ROI and save costs long term.
Elgin: Over the past several years, there have been new companies enter the reclaimers market. With the projected increase in HDD drilling activities, we expect to see more companies enter the market. In addition, there are companies which manufacture similar equipment for the oil and gas industry entering the HDD arena due to the current drop in that market.
MTI: I believe the equipment is already developed and available to the contractor.
Vermeer: The customer demand is there, so I think we’ll see more companies develop compact reclaimers.
FOR MORE INFORMATION:
American Augers
(800) 324-4930, www.americanaugers.com
Ditch Witch
(800) 654-6481, www.ditchwitch.com
Elgin Separation Solutions
(281) 261-5778, http://www.elginseparationsolutions.com
Mud Technology International
(903) 675-3240, www.mud-tech.com
Thunder Products
(940) 479-2200, http://thunder-products.com/
Vermeer Corp.
(888) 837-6337, www.vermeer.com
Comments