January 2016 Vol. 71 No. 1
Features
Contractor Bore Salvages Water Line
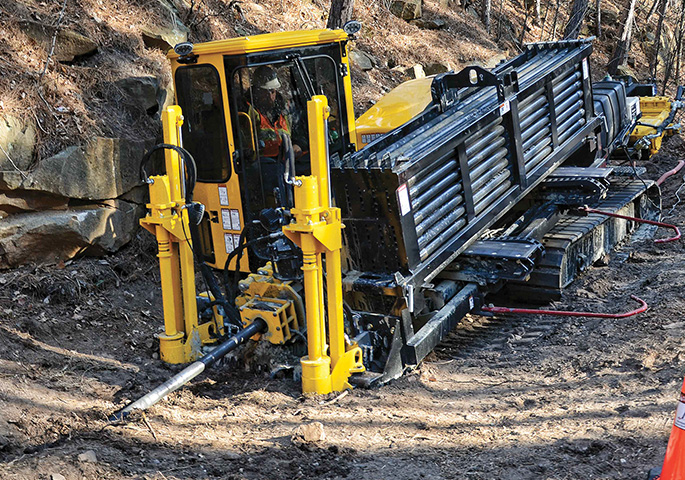
Pending Loss Of Community Water Supply Prompts Missouri Contractor’s Fast Action
Construction in Lathrop, MO, specializes in water main projects and contracts. In fact, about one-third of the company’s business is dedicated to maintaining more than 20 different municipal water systems across northwest Missouri, which means Decker Construction handles the installation and repairs for each system.
Last May, the company got an urgent call from Caldwell County Public Water Supply District (PWSD) 3, a municipal customer in Braymer, MO. Weeks of heavy rain near Kingston had caused Shoal Creek to flood several times and had finally scoured out the embankments, washing out the existing 6-inch water main under the creek. More than 2,500 residents would be without water if the situation was not resolved within 48 hours, when the reserves in the water towers would be depleted.
“We’re on call 24/7, 365 days a year for leaks and other emergencies associated with water works systems,” says Decker Construction owner Tom Decker. “We pride ourselves in having as quick of a response time as we can, and usually respond to anything within a couple of hours.”
Decker Construction had to wait several hours for the Missouri One Call System to mark where they could dig, which gave the crew time to mobilize people, equipment and materials.
The crew worked all day, through a torrential downpour, to install a 3-inch HDPE aerial crossing to get water across the creek, creating a temporary water supply line for the district. Decker Construction ordered an 8-inch-diameter HDPE pipe to replace the failed 6-inch class 200 PVC line, but the creek flooded again three days later, washing out the aerial crossing before the new pipe arrived.
Fortunately, Decker Construction was able to complete a simple horizontal directional bore to install a 3-inch line under the creek and a few days later, permanently replace it with 600 linear feet of 8-inch HDPE DR-11 as originally planned. The new 8-inch water main was installed about 10-feet away from the temporary 3-inch water line and took two full days to complete.
But the job was far from easy. The ground conditions were wet and varied. The soil went from silty loam to sticky clay to shale, making it challenging to steer and backream. The flooding kept the crews from getting close enough to the terrain to push a probe and analyze the ground conditions.
“Normally, if you were going to do a creek bore in low water conditions, you’d have the ability to get down and push a probe and investigate what conditions exist,” says Rick Bogart, superintendent for Decker Construction. “This one was just a blind shot. We just had to figure out what we were encountering as we bored.”
Flood changes parameters
The crew bored 12 feet under the creek, which was normally 70-feet wide and 20-feet deep, but at the time was about 140-feet wide due to flooding.
“With water more than 15-feet deep, there was no way we could get out there and physically see what we had. But I could tell when we shot through – we actually found a scour hole – and our steering head came out in the creek. We had to pull back up and bore deeper,” Bogart says. “That’s where we deemed how deep we needed to be to stay out of that scour hole. We also, ultimately, moved our directional drill to take a different angle in order to avoid the scour hole.”
Decker Construction used a Vermeer D36x50 Series II Navigator horizontal directional drill (HDD) to complete the job. Next, the crew backreamed with a 16-inch fly cutter twice – once before pulling pipe and again when pulling the pipe.
The drill’s auto pullback features were extremely useful on this job, as they helped the crew keep the backream operation at a smooth, constant speed and reduced operator fatigue. The crew also used the drill’s target mode to track the bore under and across the creek.
The biggest challenges of the job were heavy rain, mud and getting supplies and materials to the site.
“The side we set our drill up on was probably a quarter of a mile off the road, and on the opposite side of the creek. We had to bring material about a half-mile down a slope and a cleared right-of-way on an ATV trail,” Bogart says. “You almost had to see the site because we had water running down ditches and the slope, and it was not a straight shot – not a road or anything. It was just an open slope.”
There was a levee the crew had to go down to get in and complete the bore, and they only had a dry area of about 200 square feet in which to set up the drill. The rest of the surrounding area was covered in water.
“Within 30-feet of where our drill was stationed, and where the pipe was going into the ground, was a swift-flowing river,” says Decker Construction Safety Director Jason Southern. “We positioned the drill and the exit hole for the bore far enough away that we didn’t have to be right against the creek.”
The crew used a skid loader and an ATV to transport materials to the drill site using the ATV trail, through trees and ditches, and in the rain on very slick terrain.
“We fused the HDPE pipe together on top of the hill, where we could access it close to the road, and then we actually pulled all 600-feet down to the site with a trackhoe,” Bogart says. “It was quite an ordeal to get it all done.”
Looming deadline
The 48-hour deadline, varying soil types and persistent rainfall – on top of the constantly flooding creek – all presented Decker
Construction with unique challenges. To overcome them, the crew also adjusted the fluid mixture, which was a combination of bore gel base mixed with Baroid’s EZ-Mud Gold and dishwasher detergent.
“Once we encountered what we thought was the clay – going by the feel of the machine and the cuttings – we switched and added the EZ-Mud and detergent to help us counteract the clay,” Bogart says. “Both products also helped with the shale, to keep it suspended.”
Despite the difficult conditions, Decker Construction accomplished the project in a timely manner, and got the customer’s water system back in operation before the residents ran out of water.
“This was one of the most challenging jobs we’ve done,” Decker says. “I think most all of us enjoy a good challenge, and we had one
obstacle after another, but we just overcame.”
Decker says the job could not have been done without the use of a horizontal directional bore because, due to the flooding and forecast, it would have been impossible to perform an open cut.
But Decker says his company has found that directional boring is often the company’s preferred method of installation, even in less demanding situations, because it helps eliminate site restoration work, road closures and property damage.
In congested areas where new pipe must be installed, an experienced bore crew can install the same amount of pipe in a day’s time versus an open cut and with no site restoration, he says. This is a definite savings in labor and enhances the overall project performance.
What is the crew’s advice to other contractors facing similar challenges?
“Don’t get in a hurry. Take your time and don’t take shortcuts,” Southern says. “Shortcuts can cause problems, safety concerns –
and cost time and money. As our superintendent says, ‘You have to slow down in order to speed up.’ ”
Decker began Decker Construction in 1988 with one employee and one backhoe. Today the company has 22 employees and runs four crews.
“I think the success of a small business hinges on the employees and their harmony and teamwork,” Decker says. “Also, a properly sized directional drill with an experienced, dedicated crew is a tough combination to beat.”
FOR MORE INFORMATION:
Decker Construction
(816) 740-7000, http://deckerconstructionservicesinc.com
Vermeer Corp.
(888) 837-6337, www.vermeer.com
Baroid Industrial Drilling Products
(877) 379-7412, www.baroididp.com
Comments