February 2016, Vol. 71 No. 2
Rehabilitation
Cured-in-Place Liner Research Demonstrates Long-Term Viability
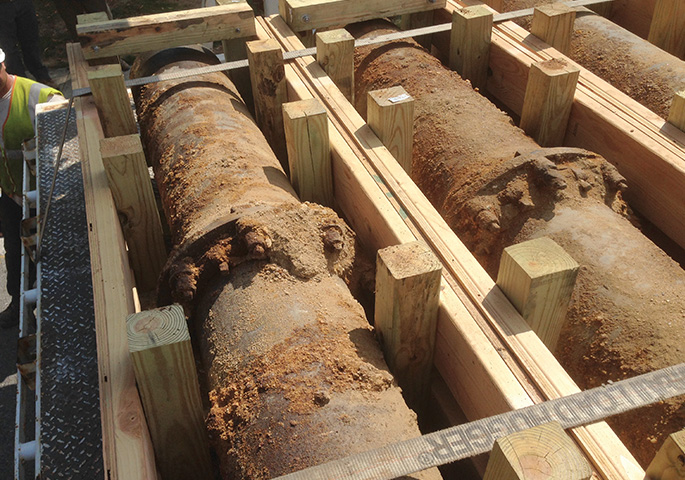
U-TECH: Underground Technology Cutting Edge Technical Information For Utility Construction & Rehabilitation
By David W. Merte Senior Project Manager, NYSEARCH/Northeast Gas Association
Cured-in-place liners (CIPL) have been installed on cast-iron and steel pipelines in natural gas distribution systems in Europe, Japan and North America over the last few decades.
CIPL have been used because of their rehabilitative and renewal qualities in contrast to the higher costs, construction risks and public inconvenience associated with conventional pipeline replacement methods, particularly in congested and difficult to access areas such as river and road crossings or urban areas.
Natural gas industry operators have demonstrated significant economic benefits with CIPL installations, compared to conventional replacement, in addition to reliable and safe operating histories. As an example, Public Service Electric and Gas (PSE&G) has realized over $10 million in savings on 40,000 feet of installed CIPL, as compared to conventional pipe replacement, with no history of leakage since beginning CIPL field installations in 1993.¹
CIPL is a three-component system, referred to as an elastomer‐fabric‐adhesive structure. The synthetic fabric jacket provides the strength characteristics for resistance to internal and external pressure, soil movement, and radial expansion. The elastomer skin provides the impermeable barrier that prevents the escape of gas.
The adhesive is a two‐part resin that bonds to form the composite and adheres to the fabric jacket to the pipe wall. Tubes of woven polyester fabric, similar to a hose, saturated with thermosetting resin are inserted, pressurized to expand them and allowed to cure in existing pipelines.
Laboratory testing of CIPL was completed in 2003 by NYSEARCH/Northeast Gas Association’s predecessor organization, New York Gas Group, in collaboration with Cornell University experts.
The Starline 2000 system liners demonstrated the in-service equivalent of up to (50) years of safe and reliable leak-free service from combined expansion, contraction, vertical displacement and rotational distortions that could be expected in the field, even under unusually severe conditions such as heavy traffic loading and encroaching excavations.
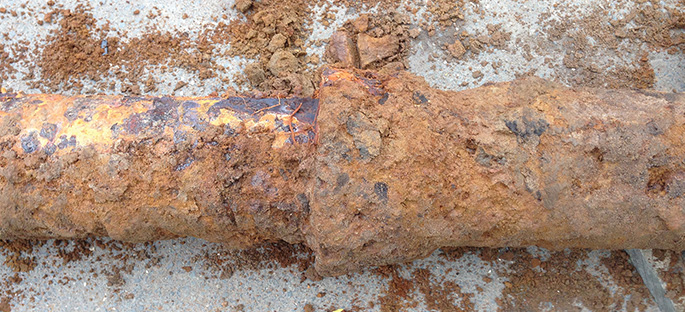
This testing further demonstrated that, when properly installed, the bond strength of the adhesive is high enough to ensure that the liner adheres to the host pipe but low enough to allow the liner to locally de-bond from the host pipe without causing leakage in the event that a mechanical coupling separates. In a similar manner, in the event of a cast-iron circumferential line break from differential soil movement or soil subsidence, the liner will separate from the host pipe wall without ripping or releasing gas.
A more recent study performed by Cornell University further validated the ability of the liner to withstand external loading in areas where the host pipe had completely deteriorated. The study demonstrated the ability of CIPL to support external loads representative of soil and traffic loading for holes up to 6 inches diameter and circumferential gaps of up to 3 inches in diameter.
NYSEARCH/Northeast Gas Association (NGA) recently completed a two-year CIPL research and development project with support from National Grid, PECO Energy, Public Service Electric and Gas and Con Edison that included funding support from PHMSA.
The project was conducted and recently completed in collaboration with Cornell’s independent pipeline infrastructure experts. The project’s work scope included:
- The compilation of prior CIPL research conducted in the United States, Europe and Japan;
- A live demonstration following state-of-the-art liner field installation procedures on selected field segments of cast iron and steel distribution pipelines; and
- Extracted field-aged CIPL segments of cast-iron pipe tested for an additional 100 years of simulated in-service equivalent mechanical (traffic loading and ground deformation) and thermal aging (push/pull) cycles at Cornell’s Bovay Laboratory. The extracted test segments were field-lined between 10-16 years ago with the Starline®2000 composite liner system.
The project’s simulated tests, conducted in accordance with Cornell’s protocols established over two decades of CIPL and cast-iron pipe testing, were designed to ascertain liner residual tensile strength and adhesion properties at concentrated stress joint areas of extracted CIPL field-aged, cast-iron pipe test segments.
Field extractions
PSE&G crews extracted two segments of in-service, low-pressure 6-inch cast-iron lined in 1998 with Starline 2000 from Elmwood Park, NJ. Two 8-foot segments with a joint and one 6-foot straight segment were cut and removed from a residential street and transported in protected cradles to Cornell for testing.
National Grid crews extracted in-service 60-psig, MAOP 12-inch CI segments from Garden City, NY that were installed in 1951 and lined in 2004 with the Starline®2000 composite liner system. Two 8-foot segments with mechanical joints and one 10-foot straight segment without a joint were cut and removed from a residential area and transported in protected cradles to Cornell for testing.
Simulating century of performance
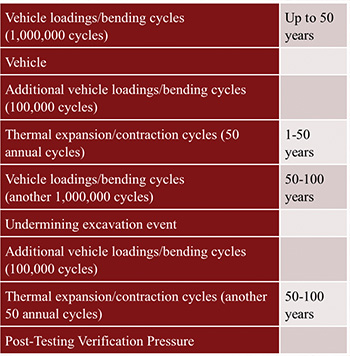
Mechanical aging tests conducted included vehicular traffic, undermining/backfilling events and thermal cycling, representative of the actual field service that gas distribution pipeline segments would experience. Thermal aging tests simulated the annual cycles of expansion and contraction for a circumferential round crack (or very weak joint) in a cast-iron pipe segment at typical pipeline depths.
Data for the state of New York and other parts of the Northeast show ground temperatures generally fluctuate between 70°F and 30°F. This ∆T=40° F change in ground temperature was simulated in the thermal cyclic tests. Vehicle traffic simulations were equivalent to 2 million cycles (equivalent to 100 years) of a repetitive 40-kip tandem axle load with an impact factor.
Deformations imposed by vehicular loading were determined from analytical models validated by full-scale field tests, assuming soil and flexible pavement conditions typically found in gas distribution systems. The test program sequence consisted of 1 million four-point bending (flexure) cycles (representing 50 years) for traffic loading, followed by an undermine event with an additional 100,000 cycles of traffic loading, and finally (representing 50) thermal-aging (push/pull) annual cycles.
The entire test program sequence would then be repeated, such that after the second set of (an additional 50 years) thermal aging (push/pull) annual cycles, over 100 years of equivalent field service life were imposed on each test segment. A post-testing verification pressure test was then completed for each test segment.
Vehicular traffic, thermal cycles
All four test segments completed the 100 years of four-point bending cyclic tests simulating vehicular traffic loading and two undermining events with additional traffic loading without leakage.
The amount of rotation that a pipe joint experiences in the field is a function of the joint stiffness. Both 6-inch cast-iron-lined extracted jointed segments included stiff cement bell and spigot joints that were resistant to bending deformations. Eliminating this joint stiffness prior to testing by cement removal would represent the weakest possible condition for the bell and spigot joints and thus this is the type of joint in greatest need of reinforcement by a CIPL.
In the case of the 6-inch, cast-iron test segment No. 1, all cement was removed from the joint after the first 50 years of mechanical aging tests. In the case of segment No. 2, all cement was removed from the joint prior to all simulated vehicular traffic loading, undermining events and thermal-aging cyclic tests. The cement removal made these joints flexible to simulate the maximum deformation at these weak test segment joints.
A set of cyclic load-unload curves for the initial thermal cycle and the second 50 years of thermal aging for 6-inch, cast-iron test segment No. 2 was used. The curves have the same shape for the additional 50 cycles, indicating no major changes in cyclic degradation beyond the first few cycles of thermal aging.
All segments tested showed a dramatic change in axial pull-push stiffness after the very first thermal cycle. The first thermal cycle, performed over six hours for the first tension (pull) portion, and four hours for the completion of the compression (push) cycle, caused substantial de-bonding of the liner from the pipe. This rate of temperature drop is much faster than the decrease normally taking place over about 120 days, which is the typical duration of soil temperature cooling at typical gas pipeline depths in the northeastern U.S.
The 6-inch joint test segment lined with the Starline®2000 CIPL showed de-bonding of the composite liner from the pipe wall in the area adjacent to the bell/spigot connection after all thermal-cyclic testing. However, this de-bonding allowed the liner to stretch without experiencing excessive strain, which could cause damage to the fibers in the liner. As a result, there was no damage to the composite liner.
The 12-inch, field-aged cast-iron test segments each included a stiff mechanical joint tested as it had been removed from the field. The first thermal cycle on the 12-inch, cast-iron test segments (six hours for the tension and four hours for the compression) caused de-bonding of the liner from the pipe and potential tearing of some of the liner fibers.
This was not of concern because in actual field conditions, the elastic properties of the polyester fibers and the polyurethane membrane liner would release stress during natural slow cooling. Slow natural cooling, consistent with the actual seasonal rates of temperature change, would likely allow local de-bonding to relieve strain concentration in the liner.
Despite the dramatically accelerated thermal-cyclic testing, all four test segments passed 100 years of thermal-cyclic, push-pull tests simulating annual contraction and expansion cycles without leakage.
Initial, post-test pressurization
Internal pressures of 15 psig (nitrogen) and 15 inches of water column (nitrogen) were initiated prior to testing on both test segments, respectively. Following 100 years of mechanical aging, each test specimen was tested to a pressure equivalent or greater than that required prior to placing a new pipeline segment in service. The pressure tests were conducted to a maximum pressure of 150 psig (water) and 90 psig (nitrogen) for the 6-inch and 12-inch cast-iron test segments, respectively. All four pipe segments maintained integrity and passed final pressure tests without leakage.
Material properties of the test segment liners were assessed after field removal and prior to initiation of mechanical aging tests. Material properties of the test segment liners were also assessed after the 100-year mechanical aging tests at both de-bonded stress concentrated joint areas and areas that remained bonded to the pipe.
The liner material testing demonstrated that the test segment liner strengths were comparable for the 6-inch cast-iron segments for both field-aged and field/mechanically aged-liner specimens taken from bonded and un-bonded (joint) sections of the liners. Subsequent to aging, there was no significant effect on either the longitudinal or hoop tensile strengths of the 6-inch composite pipe liners.
For the 12-inch composite test segment liners, tensile strength reduction was measured in the immediate vicinity of damaged fibers in the de-bonded sections of the lining in the joint area. Considerable tensile strength was still present in test segment liner specimens with damaged fibers because the polyurethane membrane remained intact and provided resistance to tensile test forces.
Thus, liner specimens that were removed from 12-inch, cast-iron test segment de-bonded joint areas demonstrated tensile strengths that were comparable to field-aged and field/mechanically aged liner specimens taken from bonded sections of the liners.
An evaluation of whether the lap shear strength of the field-aged and field/mechanically aged test segment liner specimens were comparable to those of laboratory-aged specimens was also conducted. The lap shear strength of field-aged and field/mechanically aged specimens from the test segment liners and the lap shear strengths of laboratory-aged specimens of Starline®2000 liner tested previously at Cornell demonstrated no significant difference in the results.
In summary, no loss of lap-shear strength could be seen over the 10-16 years of service life in the field or subsequent to the 100 years of mechanical aging imposed on the lined test segments. These findings are important because the strength of the CIPL system depends strongly on the liner lap-shear strength, especially for resistance to thermally induced contraction/expansion stress at round cracks or bell/spigot separation in a weak, deteriorated pipe segment joint.
A comparison of the peel strengths of field-aged and field/mechanically aged segments from the 6-inch pipe with the peel strengths of laboratory-aged specimens of 6-inch, cast-iron pipe with Starline 2000 composite liner system specimens tested previously at Cornell demonstrated no significant difference in the results.
Peel strengths for the 12-inch test segment liners could not be directly compared to those of the 6-inch test segment liners because the original installation of the 12-inch liner in the field involved curing the composite liner with an internal pressure substantially less than that for 6-inch pipe. This reduced-curing pressure would result in lower peel strength relative to that for the 6-inch pipe which was confirmed by the test results.
Live demonstration
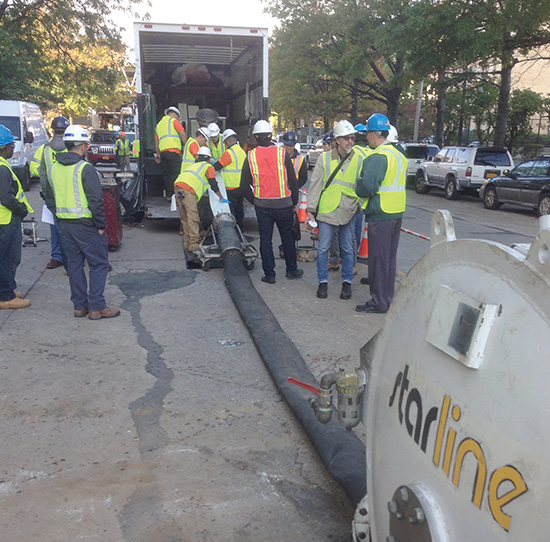
A live CIPL project demonstration was conducted last fall with Con Edison field support in the Mt. Vernon, NY-area using the Starline®2000 composite liner system and in accordance with state-of-the-art lining procedures. The area selected is an urban environment with heavy traffic and dense residential and commercial above- and below-grade infrastructure.
Among demonstration attendees were regulatory and utility officials who witnessed the lining process and current installation procedures, including liner adhesive mixing and application, liner inversion, installation, initial curing, and post-lining inspection.
An 8-inch, low-pressure cast-iron main on East Sidney Avenue and a 6-inch steel main on William Street were lined prior to the demonstration and inspected with a high-resolution camera showing second-day lining procedures to attendees.
Conclusions
All four CIPL field-aged, cast-iron test segments completed 100 years of four-point bending cyclic tests simulating vehicular traffic loading, without leakage. In addition, each of two undermining events was conducted for each of the four CIPL field-aged, cast-iron segments for additional years of simulated traffic loading without leakage.
Despite the dramatically accelerated thermal-cyclic testing, all four test segments also passed 100 years of thermal-cyclic, push-pull tests simulating annual contraction and expansion cycles without leakage. An important result from the material testing found no evidence of significant reduction in composite liner adhesion properties of lap shear or peel strength due to field aging after over a decade and subsequent to 100 years of additional field-simulated mechanical aging cyclic testing.
All four CIPL test segments, subsequent to all field and mechanical aging tests, maintained integrity and passed final pressure tests equivalent or greater than that required before placing a pipeline in-service.
The body of CIPL installations, research and performance history, when examined and compared to traditional pipeline replacement methods, demonstrate that CIPL can provide substantial pipeline renewal and is a viable option to conventional replacement methods for cast-iron and steel distribution pipelines.
References
¹ CIPL Project Workshop Presentation Cured-In-Place Liners (CIPL). August 2015.
Acknowledgements:
The author wishes to thank Con Edison, National Grid, PSE&G, PECO and PHMSA for providing support for this project. He also wishes to acknowledge the efforts of Progressive Pipeline Management (PPM) and recognize the significant contributions of Cornell University’s School of Civil and Environmental Engineering.
About The Author:
David Merte is an engineer and senior project manager with NYSEARCH/Northeast Gas Association and is responsible for several program areas including pipeline integrity, pipeline repair and rehabilitation, and real-time sensing.
FOR MORE INFORMATION:
Starliner (Progressive Pipeline Management),
(856) 579-4525, www.progressivepipe.com
Comments